WACKER’s research and development follows three goals. Firstly, we search for solutions that meet our customers’ needs and contribute to their market success. Secondly, we optimize our processes in order to be the technology leader and to operate sustainably. Thirdly, we concentrate on creating innovative products and applications for new markets and on serving future trends – such as higher energy requirements, urbanization, digitization and growing prosperity.
WACKER ranks among the world’s most research-intensive chemical companies. R&D expenditures in 2012 came in at €174.5 million (2011: €172.9 million). The R&D rate – research and development spending as a percentage of Group sales – was 3.8 percent, slightly above last year’s figure.
New Products’ Share of Sales Rises Slightly
The new-product rate (the percentage of sales accounted for by products launched in the last five years) rose slightly to 24.1 percent (2011: 24.0 percent). This was due to stronger sales for wafers of the new design rule generation, as well as for novel carpet-market dispersions.
New-Product Rate (NPR)1
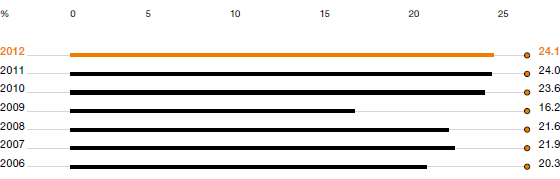
1 Percentage of sales accounted for by products launched in the last five years
We received about €7.1 million from licensing agreements in 2012 (2011: €6.7 million). WACKER’s innovative strength is reflected in the number of patents held and patent applications submitted. In 2012, we filed 119 patent applications (2011: 138). Our portfolio contains about 5,400 active patents worldwide, as well as 2,900 patent applications currently pending.
Licensing Income
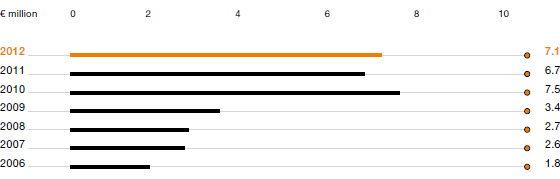
In 2012, WACKER invested €8.9 million in R&D facilities (2011: €17.3 million). At 0.8 percent of our total Group investments, R&D funding was lower than a year earlier due to long-term investment projects that had already been accounted for in 2011. Staff at our Munich-based corporate research facility (the “Consortium für elektrochemische Industrie”) moved into a new laboratory building there. And at the Burghausen site, WACKER SILICONES opened a new laboratory building for applications technology, R&D and quality assurance. Our Analytics unit is now working in this building, as well.
Additional R&D investment activity included the development of high-throughput screening for efficient protein production with ESETEC®, and the creation of simulation software that can predict the effects of process changes. We invested in laboratory facilities and pilot plants to enable process optimization in the production of VAE (vinyl acetate-ethylene copolymer) dispersions and vinyl acetate monomer (VAM), for instance, as well as in research on lithium-ion batteries. We opened a laboratory at Burghausen in which we develop test formulations from our raw materials for the food industry, to name one example.
Investment in R&D Facilities
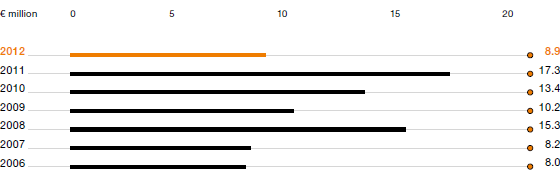
Breakdown of R&D Expenditures
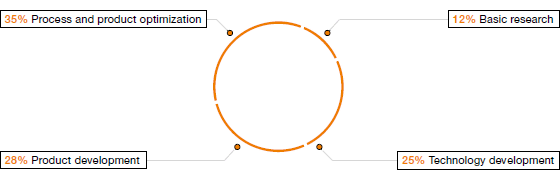
R&D Costs
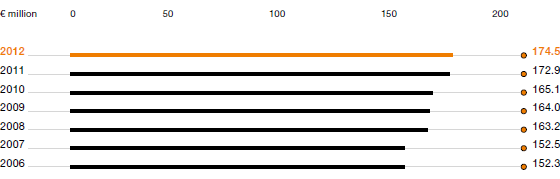
Most of the €174.5 million in R&D costs was spent on the development of new products and production processes. We acquired only a small amount of R&D expertise from third parties in 2012, spending some €250,000. This amount went to a total of six licensors, with four-fifths being used to acquire two particular know-how licenses, for which we paid €120,000 and €80,000 respectively.
Some of our research projects in 2012 were subsidized by government grants. Here are a few examples:
- Our participation in the National Platform for Electric Mobility (NPE, a joint initiative run by the German government and industry) has resulted in a number of collaborative projects involving our Central R&D facility (Consortium). Some of these projects are publicly funded, one example being the SafeBatt project to develop lithium-ion batteries that are fireproof and protected from explosion (making them intrinsically safe), which is supported by the Federal Ministry of Education and Research (BMBF). Another example is the alpha-Laion project funded by the Federal Ministry of Economics and Technology (BMWi), in which we conduct research on high-energy lithium batteries for electric vehicles.
- In a project funded by the Federal Ministry of Education and Research (BMBF), WACKER SILICONES is developing electrically-active silicone-based polymers for use in energy production.
Our business divisions and Central R&D have also applied for government research grants for further projects that are still in the approval phase. Our externally-funded research projects are coordinated though our Grant Management office, which evaluates candidate programs, submits our project proposals and manages contacts with funders.