Geared for Efficiency
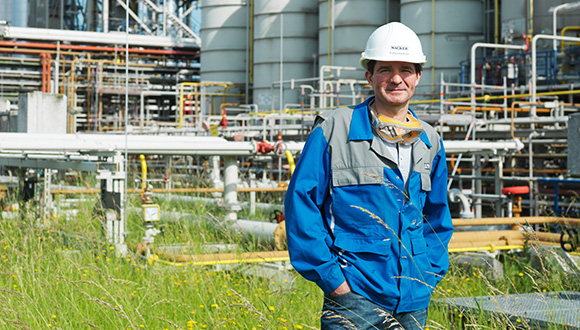
Christian Kaltenmarkner considerably reduced his plant’s energy consumption and intends to achieve a great deal more.
WACKER’s comprehensive energy management has brought about a 22-percent reduction in its specific energy consumption in Germany over the last five years. The Group has defined concrete energy targets for the years ahead.
Being cautious by nature, Christian Kaltenmarkner had been worrying about the matter for some time. The chemical engineer was aware that certain improvements to his silane distillation facility needed to be made. The rising energy costs were cause for concern. Modification work would improve the situation, yet Kaltenmarkner hesitated. Given the fact that corrosive hydrogen chloride is formed when chlorosilane comes into contact with atmospheric humidity, this had to be prevented at all costs. So, numerous tests had been conducted to practically eliminate technical risks. But was it possible to carry out the numerous modifications on the columns within the tight schedule of just two weeks? “I was acutely aware that we had to have a 100-percent success rate,” recalled Kaltenmarkner. Otherwise, the raw-material supply for Burghausen’s entire silicone production would have been jeopardized.
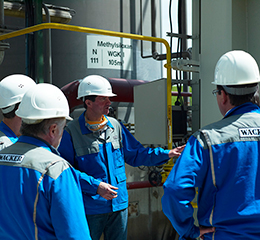
To save energy, the facility heads and energy managers work together closely.
Today, he is so pleased that, despite misgivings, he went ahead with the modifications. By means of a heat-integration system, he is able to utilize the unused heat from one plant as a power supply for other facilities. “The result proved even more successful than we had hoped,” said the 41-year-old, looking out of his office at the distillation columns, steel cylinders rising up to an imposing height of 60 meters.
The raw materials for producing silicones in pure form are extracted in the 14 columns. The distillation process separates a liquid silane mixture into individual components. Yet distillation requires a great deal of energy, which pushes up running costs considerably. The modification work now saves Kaltenmarkner over €2 million in energy costs annually.
Such energy-saving projects are immensely important at WACKER. As the main plant, Burghausen’s daily energy requirements equal those of a town with roughly 230,000 inhabitants. Due to rising oil and gas prices, energy costs account for an ever-increasing portion of the manufacturing costs, and currently amount to around 12 percent.
Specific Energy Targets
Consequently, not only is energy efficiency important for climate protection, it is also essential to a competitive position on the world market. “Naturally, we want to conserve energy and raw materials,” says Dr. Jutta Matreux, responsible for sustainability throughout the Group. “Commercial acumen plays a key role in any sustainability policy.”
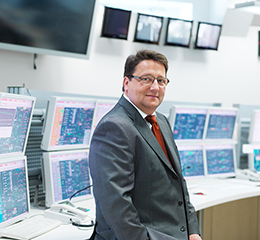
It’s Jochen Lediger’s job to implement the energy targets.
This is why WACKER has reduced specific energy consumption in Germany by 22 percent over the last five years. WACKER has defined concrete energy targets for the years ahead: annual specific-energy savings of 1.5 percent are to be achieved in Germany by 2022. In total, resource consumption per production output is to be reduced by a third. “This is very ambitious,” says Jochen Lediger. “But we know exactly where to start.”
Lediger is one of the people at WACKER responsible for implementing these energy targets. The Burghausen site’s integrated heat-utilization system already provides 44 percent of the total heat requirements. The energy manager has an overview of the entire system consisting of energy consumers and energy flows. He also ensures that energy saving is maximized during production at the Burghausen site. Over the last seven years, he and his colleagues have closely examined all energy-intensive plants. “We went through the facilities and worked out improvements with the people on site,” explains Lediger. To date, his team has implemented 150 energy-saving projects, most of which have already paid themselves off.
One of these was the modification work to Christian Kaltenmarkner’s distillation columns. The idea was to complement the heat-integration system by means of new inner mechanisms designed to raise plant efficiency. A 50-strong crew worked around the clock to cut several kilometers of old support rings out from the columns. The schedule was so tight that acceptance of the welded joints by the German technical inspectorate (“TÜV”) took place at 4 a.m. Yet production resumed as planned after two weeks of modification work.
In order to gauge the success of such measures, Jochen Lediger and his team have made a concerted effort to collect energy data over the past few years. They have installed new measuring devices and automated others. Previously, consumption measurements were carried out once a month, but now, hourly readings are possible, enabling Lediger to track precisely when, where and how much energy is consumed.
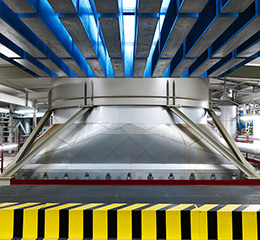
Heat-recovery steam generator above the turbine inside the Burghausen site’s combined-cycle gas turbine power station.
In 2012, WACKER had its German sites’ energy management system certified to ISO 50001. The audits resulted in good ratings for Lediger and his team. The aim of certification is to make energy consumption even more efficient.
Using new software which supports the recording of energy data, invoicing, planning and forecasting, Lediger can ascertain how much energy will be required for production the following day and how much electricity and heat WACKER will produce. For example, his calculations will depend on whether all the turbines in the power station are operating. Another determining factor is the weather: on a rainy day, more water drives the turbines in the hydroelectric plant than is normally the case. The precise forecasts make it easier to calculate how much energy to procure. If necessary, electricity for an extra hour or two can be purchased to cover demand at night or on weekends.
In any case, WACKER itself produces 45 percent of the electricity needed by its German sites. Most of it is produced in a combined-cycle gas turbine power station at the center of the site grounds in Burghausen: an unimposing structure, remarkable only in terms of its size, while inside, massive turbines and steam generators convert natural gas into steam and electricity. Stefan Seidel, in charge of the power plant, enjoys viewing the Burghausen site from the vantage point of the power-station roof at an elevation of 52 meters. At this height, the site, with its innumerable production facilities, pipelines and offices, resembles the motherboard of a PC. “It is rather impressive,” he says, “considering that we supply the energy for all the production plants.”
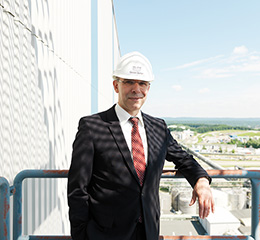
Power plant head Stefan Seidel supplies energy for WACKER’s largest site.
Generating Hydropower Since 1922
Seidel knows that energy generation exerts a profound influence on production costs and, consequently, on the success of the company. State-of-the art plants are essential. The generating station works as a combined heat and power plant. It produces electricity and process steam simultaneously. At over 80 percent, the level of fuel efficiency is twice that of conventional power plants.
Plus, the Burghausen site uses environmentally compatible hydropower. From the roof of the power plant, Stefan Seidel points to the Alz canal, a greenish-brown ribbon meandering through the site, culminating directly above the Salzach river at the power-station surge tank. This WACKER subsidiary has been supplying electricity for production since the days of Dr. Alexander Wacker, the company’s founder, back in 1922, when it went into operation as the largest industrial hydroelectric plant in Germany. Today, it is still capable of supplying electricity for 90,000 households with zero carbon dioxide emissions, says Stefan Seidel.
However, Seidel cannot rest on these laurels. His task involves continuously optimizing the Burghausen site’s energy supply, for which an integrated production system such as WACKER’s provides conducive conditions. “Many innovations come from employees,” he remarks. For example, two engineers recently suggested that the process water, which needs to be pre-heated prior to desalination, could first be run over the power-plant turbines as cooling water. A small change costing little, but achieving much: Seidel calculates annual savings of several hundred thousand euros.
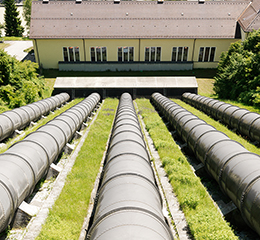
Alzwerke power station: generating environmentally compatible hydroelectricity for over 90 years.
Christian Kaltenmarkner, too, has become an efficiency expert with his silane distillation facility. He has an excellent view of his plant from his third-floor office. He points at the new condensate line: “It saves up to €200,000 per year.” He adds that new, more accurate detectors measuring permitted impurities in the siloxane yield up to €100,000 a year.
His key energy figures have never been this good, Kaltenmarkner relates proudly. Nevertheless, both he and Stefan Seidel are buzzing with ideas for the future as to how they can make their plants even more efficient. “That’s the exciting thing about my job: I can operate my own energy-saving lever like a small-scale entrepreneur,” says Kaltenmarkner. He is one of the people the energy managers can depend on.
Tracking Down Energy Loss
The newest tool available to energy managers is the energy cascade. Using computer models, experts compare a theoretical optimum value with the actual energy consumed by large, energy-intensive plants. The model identifies the sources of energy losses. The simulation enables production managers to determine even more accurately where potential electricity and heat savings are to be achieved and when optimization would pay off. In 2012, the energy cascade was implemented in three Burghausen-based plants, and 2013 will see the powder dryer in Nanjing, China, profiting from this energy-saving system.