Logistics and Transport
We constantly strive to improve our processes in order to optimize logistics chains and minimize shipment journeys or avoid unnecessary ones. Since 2010, our Logistics department has been using a simulation system to help us analyze the flow of goods. We can also use this system to calculate carbon dioxide emissions and determine the potential for optimizing transport routes and vehicle capacity utilization. We use electronic systems to organize in-plant transportation such that routes are short and wasted empty space is avoided. As well as checking carbon dioxide levels, we monitor noise emissions from the vehicles we use for our shipments.
In 2012, we transferred 740,000 metric tons of finished products from our Burghausen logistics hub to our customers (2011: 715,000 metric tons). The number of journeys rose about 15 percent to just under 43,000. More than 38,000 truckloads (2011: 35,000) and 11,540 overseas containers (2011: 10,500) were required to transport our products. 70 percent of our shipments are by road and 30 percent by rail (22 percent of which are then transferred to ship).
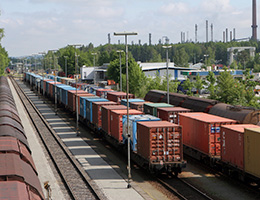
Most of the freight containers leaving our German sites reach northern ports via rail.
From our Nünchritz site, some 5,000 containers are transported to German seaports by rail and inland waterways from Riesa every year. When we procure raw materials, they are primarily transported by rail, too. Over shorter distances, however, truck transport is still more cost-effective and thus indispensable.
Reducing Shipment Routes
In integrated production, we transport products and byproducts from one plant to neighboring facilities by pipeline. For large quantities, the transport of products by pipeline is cost-effective, safe and emission-free. Ethylene, one of our most important raw materials, is piped to our Burghausen site from the adjacent OMV Deutschland site.
Our Nünchritz plant obtains cartridges for silicones from a packaging manufacturer in nearby Grossenhain. Burghausen procures reusable IBCs (intermediate bulk containers), drums and pallets from regional suppliers. Take the following example from Burghausen, where we have replaced 250-liter drums for shipping silicone fluids and emulsions with 1,000-liter IBCs. WACKER fills over 100,000 of these reusable containers annually, and then sends them to a service provider a short distance away, where they are recycled.
Short distances to service providers and maximum avoidance of empty space in the containers help to minimize emissions and waste. We are implementing similar measures at our sites in China, Japan and the USA. As an alternative to tank containers and IBCs, we also use flexitanks to transport liquids to Brazil, China, India and the Middle East, for example. WACKER mounts the flexitanks in containers in such a way that, once the flexitank has been emptied, the container can be used for another cargo straight away, without having to be cleaned first.
Piston tanks are an environmentally sound alternative to transport drums for viscous products such as our silicone sealants. A moving internal piston pushes 25 metric tons of silicone sealant – equivalent to 125 steel drums – into the tank semitrailer during loading. Customers can connect the tank directly to their filling equipment and the piston pushes the product out of the tank. Several thousand metric tons of silicone sealant currently leave our Burghausen site in this way.
WACKER’s sites outside Germany, too, procure mainly from regional suppliers to shorten transport distances. During the period under review, we opened further facilities in China and have managed to avoid transporting raw materials to them from Germany and the USA thanks to our integrated production system. With these plants, our products are close to our Chinese customers, allowing us to reduce intercontinental transportation routes.
We exchange electronic data with our shipping agents so that they can plan their trips as efficiently as possible and ensure their vehicles are always fully loaded. Plus, we launched a strategy back in 1996 to help avoid empty runs by focusing on regional shipping agents. It enables the agents responsible for a particular postal code area to plan return journeys in their region so that trucks are almost never partially laden. Our annual assessment of shipping agents extends to their environmental performance. For example, we ask how their vehicles are rated in European emission standards (such as the Euro 5 exhaust emission standard). The number of Euro 5 compliant vehicles used by our logistics providers has increased from just under 8 percent in 2006 to over 77 percent in 2012 (equivalent to around 15,000 trucks).
Improved Transportation Infrastructure at Our Sites
WACKER has grown significantly in recent years. This is particularly true of production operations at our Burghausen and Nünchritz sites. They rely on good logistics, not least to minimize the impact on the general public. In 2011, we finished a 2.6-km bypass at our Nünchritz site to relieve congestion for residents in the nearby village of Roda. At the new US polysilicon-production site in Tennessee, which is set for commissioning in 2015, we have built a bridge over “Mouse Creek” to shorten traffic time to the site.
At our Burghausen site, we are currently building a public freight terminal, set to start up in early 2014. This terminal will allow us to transfer more freight transport from road to rail. For example, one extra goods train a week on top of the five trains currently traveling from Burghausen to North Sea ports is all it would take to transfer around 2,500 truckloads to rail. A new gate at the site’s northern end will provide the connection to the terminal. It will be built in 2013 specifically for this purpose.
Wherever possible, we are switching from road to rail transport. Today, the majority of the freight containers leaving our German sites are transported by rail to North Sea ports, in particular. Since 1999, WACKER’s 600-meter long container train has traveled every day from Burghausen to the ports in Bremerhaven and Hamburg. In Burghausen, we now transport more than 95 percent of container shipments by rail, which means that over 11,000 freight containers a year no longer travel to ports by road. Running at virtually 100-percent capacity utilization, it is one of the most efficiently used container trains in the industry.
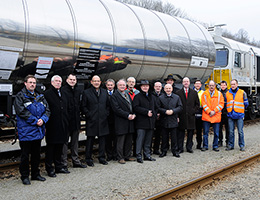
By deploying new rail tankers, we further lowered noise emissions at our Burghausen site. They have composite brakes, also known as whisper brakes. This reduces the noise emissions of trains by around ten decibels.
The national rail carrier Deutsche Bahn AG replaced its diesel locomotives with a new class during the period under review. These new locomotives comply with current emissions standards and are so powerful that one alone is sufficient to pull the entire container train (two were required previously). We implemented further measures to optimize logistics and minimize disturbance to residents. For example, we significantly reduced the amount of shunting required by our locomotives.
To monitor our journeys, we follow the “guidelines for determining the carbon dioxide emissions associated with logistics operations” (German language only) issued by the German Chemical Industry Association (VCI). Our container trains between Burghausen/Nünchritz and the ports of Bremerhaven and Hamburg replace around 18,000 road journeys a year. This saves around 1,600 metric tons of carbon dioxide annually.
Expansion of Transport Routes to ChemDelta Bavaria
Expansion of the A 94 Munich to Passau autobahn – supported by the ChemDelta Bavaria association of companies – is progressing. In December 2012, the 4.3-km Ampfing-to-Heldenstein section was officially opened. The only stretches between Munich and ChemDelta Bavaria that still need to be built run from Pastetten to Dorfen (17.4 km) and Dorfen to Heldenstein (14.9 km). Here, some parts are under construction and some still lack funding. A continuous autobahn from Munich to Marktl can be expected for 2018 at the earliest. Completion of the A 94 would not only improve the transport infrastructure of ChemDelta Bavaria, but also relieve congestion in villages and towns along the B12 highway and thus reduce the risk of accidents on this stretch of road. We actively support the “Ja zur A 94 e.V.” (Yes to A 94) association (German-language link only).
The ChemDelta Bavaria’s second major infrastructure project is the electrification of the rail route to Munich and its expansion to two tracks. This project has recently been making progress, too. Previously, the rail line to Burghausen had been in the same condition as in 1897, with the exception of a few enhancements over recent years. The section between Altmühldorf and Tüssling, where three rail lines meet, is a bottleneck; around 1 percent of German freight traffic passes through here. This bottleneck is scheduled to be removed by 2017.
We support the “Magistrale für Europa” (Major Rail Route for Europe) initiative (German-language link only), which has been committed to the expansion of the rail connection between Paris and Budapest under the slogan “from patchwork to network” for the past 20 years. The Munich-Mühldorf-Freilassing section is on this route.
Ethylene Pipeline South
The Ethylene Pipeline South (EPS) provides the infrastructure needed for safely and economically transporting ethylene between major southern German chemical sites and helps to maintain ChemDelta Bavaria’s competitive advantage and to safeguard jobs.
For the EPS, a 370-km long pipeline runs west from Münchsmünster in Bavaria across Baden-Württemberg to Ludwigshafen in Rhineland-Palatinate. Construction began in 2007. During 2012, the final section was installed, the EPS pipeline filled and continuous operation tested. Official opening and start-up took place in summer 2013.
The pipeline enables ethylene to be transported without emissions and at very low energy costs. Once the construction work has been completed, the EPS will be virtually invisible and will have no adverse effect on the landscape. Pipelines were not laid in protected areas where drinking water is abstracted or mineral springs are located, and were only installed in significant water management areas if special safety precautions were put in place.