Product Safety
WACKER provides information on the safe use of its products and is continually working to prevent or reduce the use of product ingredients that are harmful to human health or the environment. We pursue this aim in a number of ways:
- We try to replace harmful ingredients with alternative substances.
- In the absence of an alternative, we restrict the sale of products containing harmful substances to commercial and industrial customers wherever possible.
- We develop innovative alternatives to conventional products containing harmful substances.
As a guide for our product developers, we maintain a list of about 550 substances that WACKER products may no longer contain. In addition to prohibited and restricted chemicals (such as materials listed in REACH Appendices XIV and XVII), these also include substances that are the subject of heated public debate or undesired by individual companies. We avoid substances that are on the European Chemicals Agency’s List of Substances of Very High Concern (SVHC).
Product Information
WACKER ensures that, if used correctly, no risk to health or the environment is posed by any of its products. We continually update our product information and constantly revise our risk assessments – which relate, for example, to safety aspects and environmental impacts – to promptly take account of new findings. When there are new findings that have to be included in the substance safety report to comply with REACH requirements, we adapt our risk assessments accordingly.
When advertising our products and services, we make sure that our brochures, for example, contain verifiable data and precise, legally-compliant terminology and wording that reflect current scientific knowledge. The following are a few examples of how our advertising provides product sustainability information:
- We provide an information sheet for dispersions in which we outline our position on biostability and product safety as per EU Directive 286/2011, which went into effect June 1, 2015.
- In an additional information sheet, we describe our plant hygiene initiatives for the entire product life cycle of our dispersions.
- We present our silicone solutions for high-performance LEDs in a brochure on LED technologies.
- We also produce another brochure in which we explain how SILPURAN® Film, an ultrathin precision silicone film, is used in medical applications.
- In WWW – our corporate magazine – we report on how ELASTOSIL® silicone film helps convert wave power into electricity.
Material Safety Data Sheets
A material safety data sheet (MSDS) is only required by law for some 40 percent of WACKER products. We go beyond these requirements and compile these sheets for all our sales products – not just for those classified as hazardous substances. WACKER publishes over 75,000 material safety data sheets in up to 35 languages.
WACKER publishes a wide range of information in its material safety data sheets to ensure that substances and mixtures are handled correctly:
- Designations of substances and mixtures
- Potential risks
- Composition and information about ingredients
- First-aid measures
- Fire-fighting measures
- Response in the event of accidental release
- Handling and storage
- Restriction and monitoring of exposure; personal protective equipment
- Physical and chemical properties
- Stability and reactivity
- Toxicological data
- Environmental data
- Notes on disposal
- Transportation guidelines
- Legislation and other information
Nanomaterials
There is no standard definition to date for the term “nanomaterial” as far as regulatory issues are concerned, and there are no standardized specifications for the analysis methods used for classifying nanomaterials. WACKER identifies nanomaterials on the basis of the EU recommendation for defining these materials (2011/696/EU); this recommendation, in turn, is based on ISO TC 229 “Nanotechnologies.”
Nanomaterials can possess innovative properties that significantly enhance products and processes. What is true of all chemical substances applies to nanomaterials: the possible risks of inhalation, and dermal or oral exposure to production staff and users must be taken into account. In addition, there are deliberations about the effects on health that can result from the uptake of particulate, fibrous or plate-like nanomaterials. (Source: a recommendation entitled “Empfehlung für die Gefährdungsbeurteilung bei Tätigkeiten mit Nanomaterialien am Arbeitsplatz,” which was issued jointly by the BAuA [German Federal Institute for Occupational Safety and Health] and the VCI [German Chemical Industry Association] for analyzing hazards during activities involving nanomaterials at the workplace.)
All the nanomaterials that we produce or use have been recorded and their risks assessed. Most of these are nanostructured – a classification that includes materials whose internal structures are nanoscale (between 1 and 100 nanometers), but whose external dimensions are greater than the nano-range. These nanostructured products include HDK® pyrogenic silica, a powder that we have sold as a thickening agent, filler and flow enhancer for over 40 years. The physicochemical properties of the HDK® product group have been examined in detail in collaboration with external scientific institutes, and extensive toxicological, eco-toxicological and epidemiological data are available.
In collaboration with the Technical University of Dresden, we validated analytical techniques to measure nanoparticles. We investigated the potential release of nanoparticles at our labs and, in 2010, at our HDK® production facility, finding no evidence of relevant HDK® nanoparticle release. During the period under review, we continued exploring the issue of nanomaterials, working in national an international committees and task forces. As part of these efforts, we pay particular attention to nano-specific regulatory requirements (such as national nanoproduct registers and specific REACH requirements), which we implement accordingly. We inform our customers of how our products are classified and of issues related to regulatory compliance.
REACH
REACH legislation, which came into force in 2007, governs the registration, evaluation, authorization and restriction of chemicals within the European Union. Comprehensive data are gathered through REACH, which imposes high requirements on the manufacturers, importers and users of chemical products. All substances on the European market that are used or imported in annual quantities exceeding one metric ton must be registered and evaluated. The scope of evaluation work is largely determined by the quantity produced or imported and the expected risks. Particularly high-risk substances are subject to regulatory approval. The cost of REACH compliance for WACKER comes to a total of €30 million.
WACKER Submits 171 Registration Dossiers for REACH
By late 2014, WACKER had submitted 171 registration dossiers to the European Chemicals Agency (ECHA). For some of the phase-one and phase-two dossiers, submitted in 2010 and 2013, ECHA required additional information, which we provided in 2014. By the end of 2014, ECHA and the regulatory agencies of EU member states had identified 161 materials of potential concern in terms of human health and environmental safety. Of these materials, 31 already require approval. WACKER has been only marginally affected to date, with only a few purchased substances, and none of its own. As part of the EU Commission’s GHS (Globally Harmonized System of Classification and Labeling of Chemicals), all mixtures will have been reclassified pursuant to EU-GHS (roughly 7,000 mixtures) by mid-2015. A central register for hazardous substances has been set up at the ECHA, and we have registered all relevant substances since 2011.
Since 2007, WACKER has been in close contact with its suppliers about their preregistrations for REACH, their already completed registrations and those planned for the coming years. To obtain authoritative information, we systematically ask our suppliers about their current status and will continue with these inquiries beyond the final REACH registration deadline in 2018.
REACH demands extensive information about the properties of chemical products – which necessitates an increase in mandatory animal testing. WACKER makes every effort to avoid animal testing and only performs ECHA-required tests. Whenever possible, we use recognized alternative methods, such as in-vitro tests. We classify substances with similar properties into groups for testing and work within REACH consortia to exchange scientific data with other companies.
European Chemicals Agency’s REACH Schedule: Deadlines for Submitting Dossiers

1 New substances > 1 metric ton / year
2 Phase-in substances > 1 metric ton / year
3 R50 / 53 substances: “highly toxic to aquatic organisms” and “may have long-term harmful effects in bodies of water”
4 CMR substances: carcinogenic, mutagenic or toxic to reproduction
5 Phase-in substances: predominantly old substances listed on the EINECS inventory (European Inventory of Existing Commercial Chemical Substances on the market before 1981)
GPS
The ICCA (International Council of Chemical Associations) has developed the Global Product Strategy (GPS), which governs how to assess the properties of chemicals and how to provide information on their safe use. In Europe, most GPS requirements are satisfied by REACH and by the CLP Regulation (Classification, Labeling and Packaging of Substances and Mixtures). Manufacturers are required to publish descriptions written in layman’s terms on the safe and environmentally sound use of chemicals (Safety Summaries). By the end of 2014, we had published 75 Safety Summaries on the ICCA chemicals website for the substances we registered under REACH.
GHS
GHS (Globally Harmonized System of Classification and Labeling of Chemicals) is a United Nations initiative for harmonizing the classification and labeling of hazardous substances. It is up to individual countries to decide whether to adopt the system, and, if so, which modules to accept, and when. GHS was introduced to Europe in January 2009 with the European Regulation on the Classification, Labeling and Packaging of Substances and Mixtures (the CLP Regulation). More information on this regulation is available online from the European Commission.
Overview of Hazard Symbols in the EU
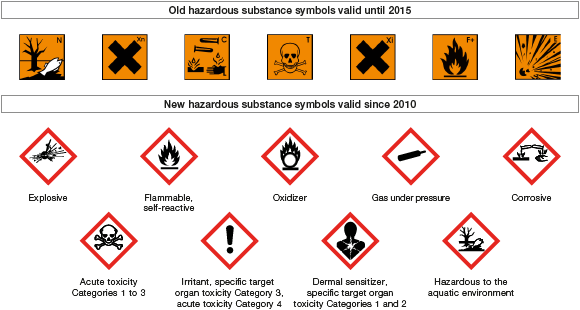
The GHS Regulation on the Classification and Labeling of Chemicals has already replaced the previous orange hazard symbols for pure substances in Europe with new symbols consisting of a white diamond in a red frame.
By 2015, we will have reclassified all of our mixtures pursuant to EU GHS (7,000 mixtures). The ECHA has set up a central classification and labeling register for hazardous substances. We have been registering all relevant substances here since 2011.
The cost to WACKER of changing to GHS comes to around €4 million. For us, this system switchover means that every product must be checked, reclassified and relabeled. Within just a few years, we have to reclassify tens of thousands of substances and mixtures, change all material safety data sheets and redesign hazardous substance labels to accommodate the new symbols and hazard information.
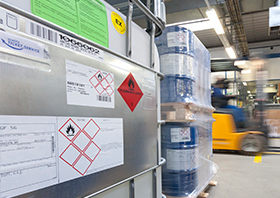
Because GHS affects any employee whose work involves hazardous substances, it impacts not only production and laboratory workers (who handle GHS-labeled chemicals on a daily basis), but also safety officers (who prepare SOPs). Furthermore, employees who label vessels, piping and equipment have to know and internalize the new hazard symbols.
WACKER provides its employees with online training and a wide range of informative literature on GHS. In Germany, the online GHS training course is currently mandatory for all employees working with chemical substances. In 2013, we set up a non-EU-specific, English version of the online GHS training for employees, which we use at our US sites in particular.