Integrated Production
WACKER’s integrated production system is its greatest strength. Compared with its competitors, WACKER has the key competitive advantage of highly integrated material loops at its major production sites in Burghausen, Nünchritz and Zhangjiagang. Basically, integrated production involves using the byproducts from one stage as starting materials for making other products. Auxiliaries required for this process, such as silanes, are recycled in a closed loop and we utilize waste heat from one process in other chemical processes. The result is lower specific production costs per net production volume compared with open production processes. Integrated production allows us to lower energy and resource consumption, use raw materials more efficiently and, at the same time, integrate environmental protection measures into production processes. Through our integrated production sites, we create synergies in the supply of raw materials and energy.
Our integrated production system is primarily based on salt, silicon and ethylene as starting materials. In our integrated processes, we optimize material efficiency by purifying byproducts and reusing them or making them available for external use. Examples:
- In our integrated ethylene production system, we use ethylene to obtain organic intermediates, which we then turn into polymer dispersions and dispersible polymer powders.
- Our integrated silicon production system operates along similar lines. Although comprising only a small number of raw materials – silicon, methanol and salt (sodium chloride) – this system enables us to manufacture over 2,800 different silicone products, as well as pyrogenic silica and polysilicon.
A further focus of our integrated production is to minimize hydrogen chloride consumption. Hydrogen chloride is an essential auxiliary deployed in the production of reactive intermediates from energy-poor natural materials. We then use these intermediates to make our end products. Hydrogen chloride production requires a lot of energy. In our integrated material loop, we recover both hydrogen chloride and some of the energy in the form of heating steam during the conversion of the chlorine-containing intermediates to chlorine-free end products (such as hyperpure silicon or pyrogenic silica). We then return the recovered hydrogen chloride to the production loop and reuse it. This closed material loop reduces emissions and, due to lower raw-material consumption, shipment journeys.
Integrated Hydrogen Chloride System
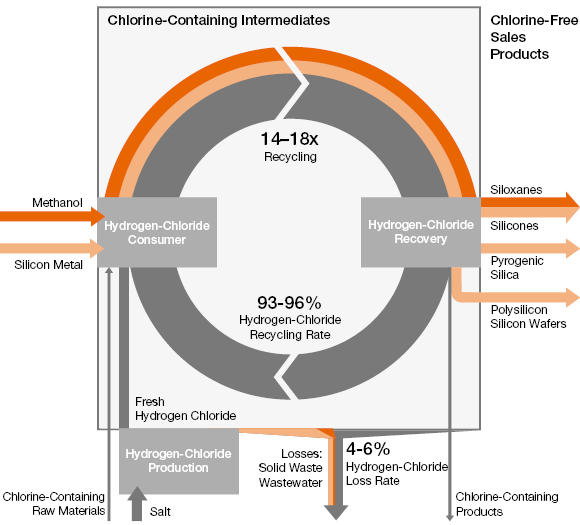
We use a chlor-alkali membrane process to supply chlorine, hydrogen, caustic soda and hydrogen chloride as starting materials to our Burghausen site. This membrane electrolysis has enabled us to stop using mercury-based chlorine electrolysis and simultaneously cut energy consumption by around 25 percent per year. Thus, WACKER has fulfilled the chemical industry’s voluntary commitment to phase out mercury-based processes by 2020 well ahead of schedule.
Examples of savings potential for resources through our integrated production system:
- We recycle 93 to 96 percent of the hydrogen chloride that we use in the production loops at our Burghausen and Nünchritz sites. During the reporting period, we reduced the HCl loss rate by means of further optimization projects. To achieve this, we put an additional waste-gas recycling facility into operation in the integrated chlorosilane system and optimized waste-gas recycling in the production of pyrogenic silica. The reduction in HCl losses can also be seen in the decline in chloride loading of the Burghausen site’s wastewater by some 1,300 metric tons.
- In 2016, our integrated production system in Burghausen prevented the emission of 961,243 metric tons of CO2 equivalents (CO2e) (2015: 917,608 metric tons). Due to this high reutilization rate, less fresh hydrogen chloride needs to be generated and, consequently, there are savings in the transportation of raw materials and in energy consumption.
- 50 percent of the heat used by Burghausen during the reporting period stems from the site’s integrated heat-utilization system.
- We optimized the hydrogen loops in our integrated polysilicon production system and thus significantly lowered the consumption of hydrogen extracted from natural gas. This has led to a reduction in carbon dioxide emissions of 9,300 metric tons per year compared with 2014.
Zhangjiagang in China – alongside Burghausen (Bavaria) and Nünchritz (Saxony) in Germany – is our third major integrated production site. We employ state-of-the-art environmental technology in China, too, where we operate facilities according to stringent national and WACKER EH&S standards. This also applies to our new site in Charleston in the USA, where we will further optimize our system of integrated polysilicon production.