Material Loop Creates Value
WACKER SILICONES produces approximately 3,000 different silicone products, a task made possible in large part by the unique integrated production system at the Burghausen site. The processes involved have been harmonized and optimized over decades, greatly reducing raw-material, transport, energy and disposal costs. This has made the sophisticated material-recycling system one of the most important factors helping the Group’s largest site worldwide to thrive amid international competition.
The best way to gain an impression of integrated production is to start at the silicon grinder, right in the middle of the Burghausen site. About 80 percent of Group sales are based on silicon, while the other key raw material for integrated production – chlorine – is produced only a few steps away, in the chlorinealkali electrolysis plant. The unit for manufacturing pyrogenic silica (HDK®) is within view, and you only have to cross the Alz canal to reach the siloxane plant, which manufactures the most important intermediate for silicones. “The integrated production system here at Burghausen is the only one of its kind in the world,” says Dr. Thomas Frey. “The distances are short and our material loops are closely interconnected – and that allows us to reduce our use of raw materials and the transport of our intermediates to a minimum.”
A process engineer, Frey is the production manager for Basics & Intermediates at WACKER SILICONES, and is responsible for manufacturing about 250 intermediates that are subsequently converted into about 3,000 different silicone products. Thanks to silicones, cars run properly, aircraft fly, or people recover faster from an illness. Potential applications are almost unlimited.
A Competitive Edge
WACKER generates roughly 60 percent of its sales outside of Europe, yet manufactures over 80 percent of its products in Germany – this is not quite the contradiction that it seems to be, however. “What ultimately makes a chemical manufacturer competitive is its ability to maximize the quality of its products while keeping production costs to a minimum,” points out Dr. Rudolf Braun, who heads WACKER SILICONES’ Basics & Intermediates business unit. “Our sophisticated integrated production system at Burghausen gives us a competitive edge, even though our energy and personnel costs are high compared to those of other international players.”
During his tour, Frey walks under some of the site’s 21 kilometers of pipe bridges. Winding through the site some five meters above ground, these bridges carry thick bundles of pipes and tubing that form the arteries of the plant, connecting its various systems. Some of these lines supply raw materials and process fluids, while others carry away the finished products. The pipe bridge system offers significant cost and safety benefits. Why? “For example because, to produce one metric ton of siloxane, our most important intermediate, we must move about five metric tons of corrosive chlorinated liquids and gases, which must undergo several production steps and therefore pass through several plants,” says Frey. “That would not be possible without this pipe system.”
Tangible Results
Silicone products have been manufactured here in eastern Bavaria since the 1950s. Besides continuously improving the chemical processes involved, the company’s engineers and chemists have also increasingly integrated these processes – with tangible results for manufacturing output, energy costs and yields. For example, specific energy required for siloxane production has been reduced by about a third in the past five years.
Raw-material yields represent another area where integrated production receives top grades. In addition to silicones, WACKER produces crystalline silicon for subsequent use in solar cells and computer chips at the Burghausen plant. Because the starting material for both production lines is silicon metal, the material is pulverized at the silicon grinder upon delivery to produce different grain sizes for different needs. “That way we can utilize virtually 100 percent of the raw material,” says Frey. “It would be extremely difficult, if not impossible, to achieve that with only one product line.”
Hydrogen chloride (HCl) produced from chlorine is also circulated within a largely closed material loop. Because HCl molecules are little more than auxiliaries in silicone and polysilicon production, the material can, with a certain extra effort, be fed back into the production process without compromising quality. By now, this recycling process has been optimized to the point that, statistically speaking, each chlorine atom passes through the material loop eight times before it leaves the plant as a by-product or – chemically bound up as common salt (NaCl) – as a residue. As a result, the site now needs only a quarter of the fresh HCl that it needed just a few years ago. In the same period, the divisions significantly increased their manufacturing output.
The pyrogenic silica (HDK®) plant plays a key role in the integrated production system. “Large amounts of tetrachlorosilane are produced as a by-product of polysilicon manufacturing. It can either be returned directly to the production process, or processed further to produce pyrogenic silica. So now, instead of disposing of the by-products from silicone manufacturing, we can use them as raw materials in HDK® production. The HCl that is liberated during this process returns to the integrated production loop,” explains Frey. Producing HDK® is more than just a way of upgrading the company’s silicones – WACKER also sells the material to external customers, who use it as a filler in insulation panels or in adhesives. With HDK®, WACKER thus achieves three objectives at once: creating added value for the site, while also reducing waste and helping to recycle HCl.
WACKER’s integrated production system forms the basis of the highly cost-efficient deployment of energy and resources
By-products and waste heat are fed back into production via highly complex material and energy loops and go on to create more value.
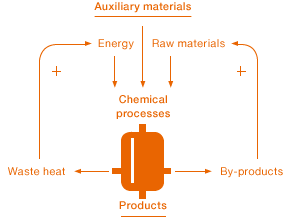
Sharing Integrated-Production Expertise
The Burghausen plant exports its integrated production expertise to other sites as well. For example, since the purchase of the Nünchritz plant in 1998, siloxane production has been expanded to about 130,000 metric tons, seven times higher than originally. That even exceeds the current production in Burghausen. WACKER has also opened a major silicone production site in China, giving the company a presence there as well. Additional plants are to follow. “Our goal is to create a worldwide integrated network,” says Braun, looking ahead.
Capacity will also be increasing in Europe, however. Silicone market volume is growing by roughly 6 percent annually, and the Burghausen and Nünchritz sites have to keep pace with that growth by systematically subjecting their chemical, process-engineering and logistics processes to scrutiny and eliminating any production bottlenecks. According to Braun, “the aim is to increase our siloxane production over the next five years by 10,000 metric tons per year.” Braun, a chemist, is certain of one thing: opportunities for optimizing the integrated production system in Europe have by no means been exhausted.