WACKER’s total procurement volume is broken down into raw materials, other services, and investments. The volume of raw materials and other services was €1.89 billion in 2008. The level of investments procured amounted to €767 million. The procurement rate – the procurement volume for raw materials, other services and investments in relation to sales – was 61.8% (2007: 60.6%). Some 1,300 different raw materials and numerous technical goods and services were purchased last year for plant-engineering and maintenance-related purposes.
download table |
|
|
|
Procurement Volume | ||
|
|
|
€ million |
2008 |
2007 |
|
|
|
Procurement volume |
2,660 |
2,291 |
To boost efficiency and effectiveness, WACKER reorganized its procurement processes in 2008. The measure was prompted by two developments. On the one hand, raw materials procurement was becoming increasingly important, given the huge volumes and widely fluctuating prices. On the other hand, WACKER’s large-scale investment projects in Germany and abroad necessitate an even greater emphasis on what we procure. That is why we made raw materials procurement into a separate corporate department and increased staff numbers there. Our existing Technical Procurement & Logistics department is responsible for the purchasing of technical goods and services and the related logistical aspects.
New Procurement Organization Improves Purchasing Processes
We globally coordinate the procurement of our eight key raw materials (e.g. silicon, methanol and ethylene), while decentralizing operational responsibility, devolving it to WACKER’s subsidiaries. By reorganizing raw materials procurement, we aim to bolster procurement reliability, optimize our terms of purchase, improve supplier relations and further intensify our activities on raw materials markets.
As for technical procurement, we set up our own project procurement unit to prepare ourselves for new challenges. Centers of expertise tackle such fields as contract management and electronic procurement/processes. Together with logistics, as well as the purchasing of materials and services, these fields are the responsibility of our Technical Procurement & Logistics department.
WACKER centrally manages supplier contracts, quality assurance, procurement-process enhancement, support of global suppliers and all procurement-related processes for technical goods and services. Materials-delivery scheduling and dispatch are handled regionally or locally. This boosts the reliability of local supplies and optimizes local deliveries. With capital expenditures up in 2008, there were more procurement transactions for the construction of new plants. The handling of such large-scale projects hinges not only on price/quantity negotiations, but also on fixing deadlines with contractors. The whole process occurs in close collaboration with Corporate Engineering.
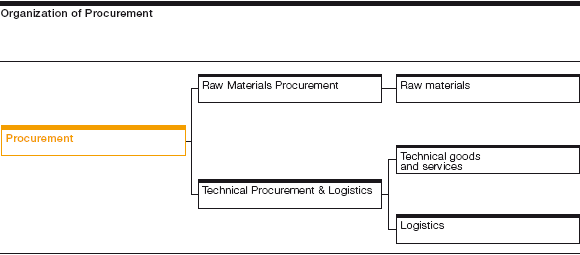
Our integrated procurement system’s aim is to ensure worldwide product availability for customers. We run all procurement processes via our Group’s SAP IT system – supplemented by our custom data-processing programs, preferably linked to SAP. Our homogeneous IT infrastructure benefits transparency. At all times, our procurement management system provides detailed data on each purchasing transaction. APP’s integration into WACKER in 2008 means that SAP now covers APP procurement processes, too.
To supply customers even faster and more reliably worldwide, we expanded Burghausen’s Container and Logistics Center. WACKER invested a total of €18 million in this expansion project. A second fully automated high-bay warehouse increased the center’s overall capacity from 11,000 to 19,000 pallets. The clear separation between incoming products (from production plants) and outgoing ones to be shipped to customers make warehousing processes much more efficient. Expansion of Burghausen’s logistics hub was rounded out when Loxxess opened an external warehouse there. As a result, ten external, previously separate warehouses could be concentrated at a single site.
WACKER has signed long-term agreements with many logistics providers and regularly puts most of its services out to tender. Where appropriate and necessary, we negotiate multi-year contracts. Contracts for sea/air freight, couriers and road/rail transport are awarded and managed globally. Their day-to-day operations are global, too, except in the case of road and rail transport, which is handled decentrally. To reduce road-transport and environmental impact, most of the containers leaving WACKER’s German sites are exported via rail – totaling over 20,000 freight containers per year.
In 2008, the importance of electronic order processing continued to grow, accounting for some 60% of our orders (2007: 55%). For some major raw material suppliers, we use channels such as ELEMICA (the chemical industry’s e-commerce platform) and SAP’s Supplier Self-Services feature. What’s more, we currently use over 80 different e-catalogs.
Procurement uses its own e-auctionhouse platform to handle online auctions and requests for bids. E-business solutions streamline our supplier transactions. In Germany alone, we process around 19,000 order items electronically every month. This frees up more time for large-scale and complex procurement transactions. Standardized and automated data transfer has many other advantages. It saves costs, enhances data quality and thus reduces error sources. Plus, transactions are faster, more accurate and reliable.
Electronic Orders Continue to Grow