Managing Sustainability
We take our responsibility to society and the environmental seriously, as our long-term commercial success is based on it. Sustainability has thus been firmly rooted in our business processes for many years.
WACKER is a member of two global initiatives, which underpin our sustainability activities: Responsible Care® (the chemical-industry initiative) and the UN’s Global Compact. Through this voluntary commitment, WACKER undertakes to protect the environment, employees and society above and beyond legal requirements. We also expect our suppliers to respect the principles of the Global Compact and we evaluate them on this point in our risk assessments.
Sustainability Department Established
Our company has been growing worldwide for years. We acquire and set up new sites and expand existing ones. We adjust our sustainability management activities accordingly. In 2011, we established an internal Corporate Sustainability department. It guides the implementation of WACKER’s voluntary commitments under Responsible Care® and the Global Compact and coordinates our sustainability activities worldwide.
Our integrated management system (IMS) remains the most important instrument for our operational processes. The IMS regulates workflows and responsibilities, attaching equal importance to productivity, quality, environment, health and safety. In the future, we wish to control additional sustainability-related activities more closely, for example, life cycle analyses for our products.
WACKER has been pursuing several strategic projects in the field of sustainability management:
- One focus has been the inclusion of all our sites in our ISO 9001 (quality) and ISO 14001 (environment) Group certification by 2012. Certification ensures that customer-driven specifications and our corporate standards are implemented at all WACKER sites. In addition, this has roughly halved the company’s previous annual expense for external audits.
- We are developing an energy management system that meets ISO 50001 requirements. We expect this system to stimulate further reductions in our energy consumption and costs. Certification of our German sites is planned for 2012.
- The occupational health and safety management system at all WACKER sites is to be certified under the globally recognized OHSAS 18001 standard by 2015. Our Siltronic subsidiary and our new site in Jincheon (South Korea) are already certified under this standard.
- WACKER will be preparing a Corporate Carbon Footprint report. This report is an important tool for improving climate protection.
- We will convert our various sustainability-reporting IT systems to a uniform Group system.
Substantial progress was made on these projects in 2011:
- We had our Jena plant certified under ISO 14001 and the new polysilicon facilities in Nünchritz under ISO 9001 and ISO 14001, as part of Group certification. Almost all our production sites are now included in the Group certificate. Measured against the number of employees, 94 percent of the Group is already included in it. Not yet included are the sites in Brazil and India and our new acquisitions in Holla (Norway) and Jincheon (South Korea), which have corresponding individual certificates, however.
- We gave the sites checklists in 2011 for them to measure their degree of compliance with OHSAS and to identify shortfalls.
- To prepare a Corporate Carbon Footprint report, we collected our first data on indirect greenhouse-gas emissions from the acquisition of energy.
- We have examined programs developed for sustainability reporting and chosen a system, which is to be implemented groupwide as of 2012.
New Efficient Policy for Issuing Regulations
WACKER revised the hierarchy of its management documents in 2011 and prepared a new policy for issuing Group regulations. Twenty-one regulations now govern topics of overall material significance for the company. They concern management, organization and collaboration, law and compliance, strategy and business processes as well as financing, controlling, accounting and taxes.
In 2011, WACKER Greater China continued work on having its key, majority-owned production facilities certified as national environmentally-friendly enterprises by the Chinese Environmental Protection Bureau. The production subsidiaries meet certification requirements (e.g. final acceptance by the local environmental bureau and ISO 14001 certification). One production subsidiary has already passed the final audit. The authorities are still conducting their review at the other two.
In 2011, WACKER published its new Sustainability Report for 2009/2010. The report adheres completely to the guidelines set by the Global Reporting Initiative (GRI). GRI evaluated the report and accorded it an A, their highest report grade. With its new Sustainability Report, WACKER provides a full and transparent account of its sustainability efforts to customers, business partners, employees, shareholders, analysts, non-governmental organizations, regulatory bodies and the neighbors of its various sites.
Increased Compliance Training at Non-German Sites
WACKER’s ethical and legal principles of corporate management exceed legal requirements. Employees in Germany, the USA, China, Japan, India, South Korea, Brazil and Singapore now have access to compliance officers. If employees notice any violations, they have been instructed to inform their supervisors, the employee council, their designated HR contacts or the compliance officers. One focus of our compliance management in 2011 was on non-German sites. More overseas employees were included in both online and classroom-based training.
Environmental Protection
All WACKER’s processes focus on the need to protect the environment and to manufacture safely. We attach particular importance to integrated environmental protection. This commences with product development and plant planning. In 2011, WACKER spent €7.9 million on environmental investments (2010: €11.8 million). Environmental operating costs amounted to €73.3 million (2010: €65.2 million).
In 2011, we continued working on our groundwater remediation strategy at Nünchritz. We conducted a field test to determine whether contaminants (solvent residues) in the groundwater there can be degraded using naturally occurring microorganisms. The test results show that effective and economical groundwater remediation is not possible via this route. Therefore, in 2012, we will be conducting hydraulic remediation by pumping the groundwater into a treatment system and returning it after cleaning. We expanded our wastewater treatment plants in the course of building our Nünchritz polysilicon facilities.
For the first time, our environmental indicators reflect the Holla, Norway silicon-metal plant acquired in 2010. The environmental impact of metallurgical production differs greatly from that of WACKER’s typical chemical operations. For this reason, the environmental indicators, particularly regarding airborne emissions, rose. Without the consolidation of the Holla site, the environmental indicators for air, water and waste in 2011 are slightly above the prior-year level. The rise in nitrogen oxide emissions is due to the integration of the Holla site, the start-up of polysilicon facilities in Nünchritz, and a further rise in emissions at Burghausen following a maintenance-related shutdown of the gas turbine in 2010. The atmospheric emission of non-methane volatile organic compounds (NMVOCs) fell as a result of process improvements in Burghausen. WACKER continuously strives to close its material loops and recycle byproducts from other areas back to production and thus to prevent or reduce waste.
download table |
Emissions into the Air in 2011, Business Divisions/Metallurgy | ||||||||||||
|
2011 |
2011 |
2011 | |||||||||
| ||||||||||||
|
|
|
| |||||||||
Air |
|
|
| |||||||||
CO2 emissions (t) |
1,347,000 |
1,026,000 |
321,000 | |||||||||
Nitrogen oxides (NOX) (t) |
2,221 |
1,052 |
1,169 | |||||||||
Non-methane volatile organic compounds (NMVOCs) (t) |
396 |
389 |
7 |
In 2011, we conducted the first survey of our indirect greenhouse gas emissions from bought-in energy (as per Greenhouse Gas Protocol Scope 2).
download table |
Environmental Indicators from 2008 to 20111 | ||||||||||||||||||||||||
|
|
2011 |
2010 |
2009 |
2008 | |||||||||||||||||||
| ||||||||||||||||||||||||
|
|
|
|
|
| |||||||||||||||||||
Air |
CO2 emissions (t) |
1,347,000 |
986,000 |
969,000 |
976,041 | |||||||||||||||||||
|
Nitrogen oxides (NOX) (t) |
2,221 |
926 |
963 |
997 | |||||||||||||||||||
|
Non-methane volatile organic compounds (NMVOCs) (t) |
396 |
415 |
383 |
501 | |||||||||||||||||||
|
Greenhouse gases |
|
|
|
| |||||||||||||||||||
|
Direct2 (t CO2) |
1,347,000 |
– |
– |
– | |||||||||||||||||||
|
Indirect3 (t CO2) |
1,072,171 |
– |
– |
– | |||||||||||||||||||
|
|
|
|
|
| |||||||||||||||||||
Water |
Water consumption (1,000 m3) |
268,657 |
252,151 |
264,532 |
241,286 | |||||||||||||||||||
|
Chemical oxygen demand (COD) (t) |
1,680 |
1,820 |
2,730 |
4,782 | |||||||||||||||||||
|
Halogenated organic hydrocarbons (AOX) (t) |
5 |
6 |
6 |
7 | |||||||||||||||||||
|
|
|
|
|
| |||||||||||||||||||
Waste |
Disposed of (t) |
47,410 |
48,520 |
80,860 |
87,293 | |||||||||||||||||||
|
Recycled (t) |
80,290 |
77,030 |
63,430 |
74,327 | |||||||||||||||||||
|
Hazardous4 (t) |
68,230 |
69,320 |
100,860 |
108,458 | |||||||||||||||||||
|
Non-hazardous (t) |
59,470 |
56,230 |
43,430 |
53,161 | |||||||||||||||||||
|
|
|
|
|
| |||||||||||||||||||
Energy |
Electricity consumption (TWh) |
4.4 |
3.8 |
2.7 |
2.4 | |||||||||||||||||||
|
Primary energy |
|
|
|
| |||||||||||||||||||
|
Natural gas (TWh) |
5.8 |
5.5 |
5.4 |
5.4 | |||||||||||||||||||
|
Solid fuels5 (coal, charcoal, wood) (TWh) |
0.9 |
0.4 |
– |
– | |||||||||||||||||||
|
Heat6 (supplied by third parties) (TWh) |
0.2 |
0.2 |
0.2 |
0.2 | |||||||||||||||||||
|
Heating oil (TWh) |
0.02 |
0.01 |
0.01 |
0.01 |
The Bavarian State Ministry of the Environment and Public Health honored WACKER as a founding member of the Bavarian Environmental Pact. The joint public-private initiative was founded in 1995 with the goal of promoting environmental protection beyond that required by laws and regulations.
Product Stewardship
Our life cycle assessments (LCAs) look at the environmental impact caused by a specific product family throughout its life cycle – a “cradle-to-gate” assessment extending from manufacturing to the factory gate. The analyses allow us to assess the sustainability of our products and production processes, and improve them accordingly. During 2011, we introduced life cycle assessments, which we launched at WACKER POLYMERS in 2010, to additional business divisions. We want to establish this tool throughout the Group.
Energy Management
The chemical industry is an extremely energy-intensive sector. WACKER is a one of Germany’s major energy consumers. For this reason, globally competitive energy prices are of considerable significance to us. WACKER is constantly improving the energy efficiency of its processes. This enables us to remain globally competitive and to support climate protection. At Burghausen, for example, we generate hydroelectric power and our production facility in Holla obtains electricity mainly from hydroelectric power. Our primary source of energy, though, is climate-friendly natural gas. At WACKER’s large Burghausen and Nünchritz sites, steam and electricity are produced in cogeneration systems. These combined heat and power (CHP) plants have more than 80 percent fuel efficiency, twice that of conventional power-generation plants.
In 2011, WACKER’s electricity consumption rose to 4.4 million MWh (2010: 3.8 million MWh). This was caused by the high capacity utilization of our production operations and the launch of polysilicon production at Nünchritz. In addition, a full year’s consumption of our silicon-metal production plant in Holla, Norway, which was acquired in June 2010, was included for the first time.
The Group’s captive power plants – the hydroelectric and CHP (gas and steam turbine) generating stations in Burghausen and the CHP in Nünchritz – produced around 1.5 million MWh in 2011. This means that WACKER covered about a third of its total electricity needs itself. Groupwide, CO2 emissions totaled 1.3 million metric tons, of which 64 percent resulted from captive power plants that are subject to emissions trading rules.
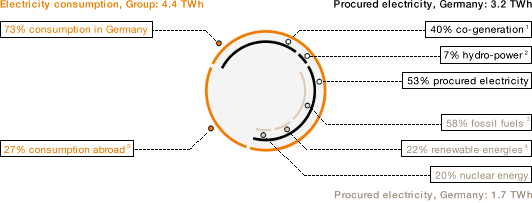
1 Burghausen and Nünchritz
2 Burghausen
3 Coal, lignite, oil, gas
4 Hydro, wind, solar power
5 Outside Germany, we purchase electricity from third parties based on the local
standard energy mix
WACKER’s German production sites account for 73 percent of its electricity needs. In Germany, we purchased enough electricity from utilities to cover 53 percent of our electricity requirements there. In line with the utilities’ primary energy sources, 58 percent of this electricity was generated from fossil fuels. 20 percent came from nuclear energy, and 22 percent from renewable energy sources. Heat consumption, which includes the use of solid carbon-based fuels (coal, charcoal, wood) in silicon-metal production, rose across the Group to 3.9 TWh (2010: 3.4 TWh). This increase is due to our new Holla site.
download table |
Energy consumption | ||||||||||||||||
TWh |
2011 |
2010 |
2009 |
2008 | ||||||||||||
| ||||||||||||||||
|
|
|
|
| ||||||||||||
Energy consumption |
4.4 |
3.8 |
2.7 |
2.4 | ||||||||||||
Heat consumption1 |
3.9 |
3.4 |
2.8 |
2.8 | ||||||||||||
Primary energy |
|
|
|
| ||||||||||||
Natural Gas |
5.8 |
5.5 |
5.4 |
5.4 | ||||||||||||
Solid fuels2 (coal, charcoal, wood) |
0.9 |
0.4 |
– |
– | ||||||||||||
Heat3 (supplied by third parties) |
0.2 |
0.2 |
0.2 |
0.2 | ||||||||||||
Fuel oil |
0.02 |
0.01 |
0.01 |
0.01 |
Workplace, Plant and Transport Safety
WACKER’s aim when it designs plants and processes is to ensure that they pose no risk to people or the environment. We consequently make safety management a comprehensive, groupwide undertaking that includes workplace safety and the safety of our plants.
In order to ensure the safety of our plants, we ascertain risks in a systematic way, analyze them, and set forth appropriate safety measures using two primary methods. In a plausibility check, we review a plant’s safety plan with regard to how well we control the energy (pressure, heat) existing in the process. In addition, we consider scenarios that could trigger undesirable events (such as blowouts of pipelines). The WACKER analysis starts with possible individual deficiencies and investigates the entire chain of events on to the breakdown or accident.
In the year under review, we completed the “ANSIKO 2010” project launched in 2010. In this project, we reviewed all the Group’s safety plans for facilities with a dust-explosion risk. In addition to protection against dust explosions, we examined plants that do not require monitoring. Improvements are now being made and are expected to be completed in 2013.
WACKER attaches particular importance to providing ongoing training to its safety experts. We hold regular training sessions, for example, on plant safety and explosion protection. Group experts organize safety training at WACKER’s non-German sites. In 2011, experts from all Asian production sites met to exchange information and attend training sessions in China. We also conducted safety audits at our sites in South Korea and China. WACKER organized its first Safety Day for all its sites in China. During the event, three-fourths of the targeted employees participated in training sessions, presentations and plant inspections.
At Nünchritz, firefighting capacity was broadened to encompass the Poly 9 facility’s expansion stages. 2011 saw the fire department being reinforced with additional full-time fire fighters and technical equipment (including a new, ultramodern turbo-extinguisher).
In 2011, there were 3.9 workplace accidents groupwide (2010: 4.3) per 1 million hours worked. Most accidents are not of a chemical nature. The most common causes are tripping, slipping and falling or inattentiveness during manual activities. At WACKER, the accident rate is fueling our efforts to further enhance occupational safety. We are implementing our new safety program step by step. Called WACKER Safety Plus, it adopts safety elements that Group companies and sites with particularly low accident rates have successfully employed. These include safety patrols, group discussions with the workforce and emergency drills.
download table |
Reportable Accidents per 1 Million Hours Worked1 | ||||||||||||||
Accident Rate |
2011 |
2010 |
2009 |
2008 |
2007 | |||||||||
| ||||||||||||||
|
|
|
|
|
| |||||||||
Reportable accidents involving Group employees |
3.9 |
4.3 |
4.0 |
3.7 |
3.8 |
The WACKER plant in Kentucky (USA) was recognized for its commitment to safety in 2011. The Governor’s Safety and Health Award, and the Safety Award of the American Coatings Association (ACA) recognize companies for high safety standards and a long-term absence of reportable accidents.
WACKER ensures that its products are safely stored and transported. Before loading vehicles, we carry out stringent checks on them. This applies especially to hazardous materials. If a vehicle fails inspection, we continue sending it back until it passes. The defect rate has been at a low level for years. In 2011, it was 3.6 percent for transporting hazardous goods (2010: 3.0 percent). WACKER audits hazardous goods shippers at least every two years.
We regularly review aspects of transport safety with our logistics providers, e.g. during the annual Logistics Day. If deficiencies are found, we agree on specific improvements and then follow up on their implementation. WACKER uses in-house criteria and internationally recognized systems, such as the Safety and Quality Assessment System (SQAS) operated by the European Chemical Industry Council (CEFIC), to select logistics service providers and evaluate their performance. Our evaluation criteria include driver qualifications and training, vehicle equipment and accident response. Through the use of standards and specifications, WACKER ensures that even the subcontractors working for our logistics providers meet the same requirements.
In 2011, we recorded eight transport accidents (2010: five). This number includes not only accidents involving the distribution of our intermediates and products where we commissioned the transport, but also incidents that do not involve hazardous goods, as well as those that do not adversely impact people or the environment. Such incidents are likewise listed in shipper evaluations.
download table |
Transport Accidents | ||||||||
Number of Accidents |
2011 |
2010 |
2009 |
2008 | ||||
|
|
|
|
| ||||
Road |
6 |
4 |
5 |
11 | ||||
Rail |
1 |
1 |
– |
4 | ||||
Sea |
1 |
– |
– |
2 | ||||
Inland waterways |
– |
– |
– |
– | ||||
Air |
– |
– |
– |
– |
Education Partnerships Founded
We take our social responsibilities seriously, especially toward communities near our sites. We are aware that companies can only be successful if they have society’s trust. One emphasis of our social commitment is young people’s scientific and technical education. We will need committed scientists and engineers in the future if we are to remain competitive.
We entered into two education partnerships in 2011 near our future US polysilicon site in Charleston, Tennessee. WACKER and Chattanooga State Community College have established a training program for future employees. Graduates of this course will fill a variety of production jobs at the new facility from 2013. The Group is supporting the newly established WACKER INSTITUTE at Chattanooga State University with a donation of $3 million. WACKER is also supporting the nearby Cleveland State Community College by donating $150,000 to its Excellence in Education program. The five-year program is intended to advance the development of curricula in the natural sciences, mathematics and technical faculties. We also again sponsored the Dresden/East Saxony regional heat of the “Young Scientist” competition.
For the 14th time, we presented the WACKER Silicone Award, one of the world’s most significant honors in the field of silicon chemistry. The €10,000 prize went to Prof. Matthias Drieß, from the Technical University of Berlin. The scientist was honored for his pioneering work on low-valent silicon compounds, which – owing to their isolability and reactivity properties – now constitute promising building blocks in organosilicon chemistry and make it possible, for example, to produce catalysts which do not contain precious metals.
Dedicated to Young People and Society
Additionally, projects to help children and young people are a special concern. Since 2007, WACKER has supported a German religious charity, “Die Arche” (The Ark), which aids children and young people from socially disadvantaged families in several German cities. It provides the children with hot meals and extra tutoring, organizes leisure activities and offers counseling. WACKER again donated €100,000 to mark the five-year anniversary of the charity’s Munich branch.
WACKER and its Wacker Asahikasei Silicone (AWS) joint venture together donated 7.5 million yen (about €65,000) to the Japanese city of Chikusei. The money was for the repair of the municipal hospital that was heavily damaged by the earthquake on March 11.
WACKER participated in the open house held by the VCI (German Chemical Industry Association) in 2011. Around 20,000 people availed themselves of the opportunity to take a look behind the scenes at WACKER’s sites in Burghausen, Freiberg and Cologne on September 24.
WACKER set up a liaison office in Berlin in 2011 to better represent the company’s political interests.