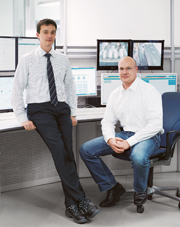
Process Innovation
Jochen Groß knows “his” plant on the WACKER site in Burghausen like the back of his hand. The 3,000-square-meter complex has been the focus of his working life for over 15 years. “Up there,” says the production manager pointing to the walkways at a dizzying height, “you can feel the eddies inside the reactors. Standing there, I can sense whether the reactor is running properly.” Each year, the facility produces several hundred kilotons of methyl chlorosilanes. These serve as feedstock for producing silicones – fluids, rubbers and resins with applications in such industries as construction, automotive, plastics, electrical and textiles.
A Fluid Contact Mass
The principle behind the process is anything but new. It was discovered back in 1940 by Eugene Rochow, an American, and Richard Müller, a German. It starts from solid silicon and gaseous methyl chloride. Copper is also required as a catalyst, to increase the reaction rate and make the process economical.
A radically new insight into two key processes used in the chemical industry will boost the efficiency of silicone and hyperpure silicon production while reducing raw material consumption.
The silicon and copper, along with co-catalysts, are finely ground and then mixed to make the contact mass. In the Müller-Rochow reactors at WACKER, the methyl chloride flows up through a bed of contact mass particles at high speed. “This causes the particles in the contact mass to behave like a boiling liquid. In this fluidized bed, bubbles are created and the particles constantly rise and sink,” explains Groß.
There is another key production process, well-established at WACKER, that is performed in fluidized-bed reactors, namely the industrial-scale production of trichlorosilane – the precursor of hyperpure silicon in solar cells and semiconductors. Trichlorosilane (TCS) synthesis, too, is the first stage of a value-creation chain but distinct from that of the Müller-Rochow process. TCS synthesis is therefore the responsibility of a different WACKER business division. Yet the two processes are in fact very similar. In TCS synthesis, too, a gas is forced through solid metallurgical grade silicon, where it reacts to form the product.
WACKER performs both of these processes in fluidized-bed reactors because these systems offer optimum thermal and mass transfer. The yield is higher, i.e. more product. And local hotspots are avoided, which could otherwise compromise the product’s composition.
“Up until now, Müller-Rochow and TCS synthesis have been studied empirically,” says Dr. Thomas Frey, WACKER’s head of Process Development and Productivity at Corporate Engineering. This means that records are kept of how changes in the conditions within the reactor affect the quantity and composition of the product. The information and experience accumulated over the years have helped WACKER to make continuous improvements to its processes. “However, there’s limited scope left for making further empirical optimizations ,” admits Frey.
The problem is that there are too many variables. Hundreds of them, he says: starting with desirable and undesirable impurities in the silicon and catalytic additives, then the crystal structures of the solids, and their particle sizes, and finally process engineering variables such as pressure, temperature and flow rate. “Looked at on this scale, the Müller-Rochow and TCS syntheses constitute a black box – very complex systems that can only be examined in terms of their external behavior,” explains Frey. Consequently, attempts to elucidate the process in recent years were limited to the use of computers and ingenious algorithms to explain the interplay of the various factors.
The Reactor Is No Longer a Black Box
“Now, though, a new and highly promising approach has been developed that enables us to simulate the processes inside the reactor realistically using a computer,” adds Frey. Meanwhile, in production, Jochen Groß is also testing the new findings, which could prove to be a milestone in making production more versatile, cheaper and more economical on resources. What has made the two so optimistic is the outcome of some truly cutting edge research. A team led by Dr. Anne Alber from Corporate R&D has refined a special analytical technique to the point where it can now be used to view individual, fundamental processes occurring on the surface of the solid particles. The graduate chemist was honored with the Alexander Wacker Innovation Prize 2011 for her work.
The Particles Can Now Remain in the Reactor for Analysis
“What makes the technique so special is that we can use it to analyze the solids at the molecular level minute by minute in realistic conditions as the reaction is happening,” explains Alber. In the past, analysis entailed removing solid particles from the reactor for examination. The time delay allowed the particles to cool down and also to react with oxygen in the air. As a result, this analysis gave little information about what was really happening inside the reactor. Thanks to this new, innovative technique, WACKER researchers have already gained a very detailed idea of what Alber calls the reaction network of the Müller-Rochow process. The formation of methylchlorosilanes on the surface of the contact mass particles actually proceeds via a complicated process involving scores of intricately interlinked intermediate steps. The catalyst, too, plays a number of active roles, even though it ultimately emerges from the process virtually unchanged.
An innovative analytical method improves production processes.
As Anne Alber has only recently begun to apply her special analytical technique to trichlorosilane synthesis as well, concrete results are not yet available. “Much of what we learned from our pioneering work on the Müller-Rochow process is transferable to the trichlorosilane synthesis. So, progress will be swift,” assures Alber.
Armed with the fresh knowledge of the fundamental processes occurring in the Müller-Rochow direct synthesis, the WACKER process engineers have identified ways to further improve it. They are now assessing which of the possible recipes will be particularly effective at lowering silicon consumption in practice and at boosting productivity. For now, they are conducting model trials in fluidized-bed reactors the size of a glass beaker. Then, they will scale this up to reactors capable of converting several kilograms of raw materials. “Many of the new optimization methods have already gone to factory trials at the ton scale and will be phased into regular production,” adds Frey, visibly pleased.
Characteristics
Process Innovation for Silane Production
80%WACKER’s group sales are mainly derived from products whose precursors are produced in fluidizedbed reactors. Here, the fluidized bed of solid particles comes into intimate contact with the fluidizing material (gas or liquid), resulting in a dynamic exchange in all directions. This leads to good thermal transfer within the reactor, which is ideal for an efficient, energetically favorable process. |
![]() 85mis the height of the distillation columns used to synthesize chlorosilanes at WACKER. Such columns are in use at the Burghausen and Nünchritz sites. |
Müller-Rochow Direct Synthesis
The U.S. American Eugene Rochow and the German Richard Müller independently discovered the basic principle for manufacturing silanes – Mülller-Rochow direct synthesis – in 1940. It starts from solid silicon and gaseous methyl chloride. Copper, as a catalyst, speeds up the reaction. In the Müller-Rochow reactors at WACKER, the methyl chloride flows up through a bed of contact mass particles. Then the methylchlorosilanes that are produced are separated from unspent methyl chloride in a condenser.
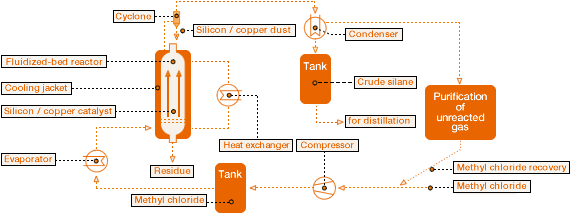
2,500 Silicone Products
WACKER manufactures silicone products using Müller-Rochow direct synthesis. As feedstocks for producing silicones, methylchlorosilanes make possible many products that are essential to modern life. They can be found, for example, in cars, electrical equipment, plastic products, textiles and buildings.
Process Innovation for Polysilicon Production
1839 was the year that Alexandre Becquerel discovered the photovoltaic effect. The French physicist immersed two platinum electrodes in an acid bath to create a battery. Then he separated the electrodes optically and exposed one to light while shading the other. He found that more current can be obtained from the battery when the electrode is exposed to sunlight.
1904 was when the German physicist Phillipp Lenard discovered that certain metals release electrons from their surface when irradiated with light. He thereby gave the first explanation of the photoelectric effect, obtaining the 1905 Nobel Prize for Physics for his work.
1905 was the year that Albert Einstein, using quantum theory, explained that light can exist either as a wave or a particle. He realized that the energy of a light particle (photon) depends on the wavelength. He, too, proved that bombarding a metal with light beams releases electrons. Using two electrodes, he was able to utilize the electrons as electric current. Einstein was awarded the 1921 Nobel Prize for Physics for these discoveries.
200 megatons of carbon dioxide can be prevented by the amount of silicon that WACKER produced in 2011 for use in photovoltaic modules. In 2014, the potential saving is estimated at 380 million metric tons. |
6 monthsis the energy payback time for a photovoltaic cell in the Sahara. This is how long it must operate in order to generate the amount of energy used in its manufacture. In Northern Germany, the energy payback time is 18 months. |
30 yearsis the lifetime of crystalline solar cells. After 25 years, manufacturers still offer a performance warranty of 80 percent. ![]() |