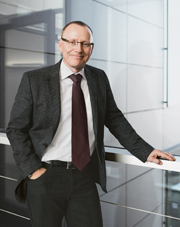
Focus Innovation
Mumbai never stands still. Especially not at noon, when the “dabbawalas” in their pristine white caps are swarming around the center of the 35-million metropolis. They deliver lunch in small boxes direct to the offices that make up the Indian commercial center. Barely 20 years ago, this would have been a hazardous undertaking, sprinting in sandals between honking taxis, overcrowded buses and clattering mopeds. Back then, in 2011, the city had a population of 20 million, and was permanently shrouded in a grimy, acrid smog. But now, in 2030, the noise and stench have disappeared. Electromobility dominates the city center as exhaust-free urban vehicles guided by smart vehicle telematics drive silently around the congestion-free city. Hopelessly utopian, perhaps?
In 2011, chemists, solid state chemists and physicists based in WACKER’s Corporate R&D facility in Munich were all working intensively on energy-storage technologies that will pave the way for viable, sustainable electromobility. For a year now, Dr. Jürgen Pfeiffer, a chemist, has been in charge of Technology Management in the Energy Storage and Conversion section. He is consolidating the company’s expertise in silicon, silicone, silane and polymer chemistry and channeling it into lithium-ion cell research. “You won’t find this combination anywhere else in the world,” he says, proudly. “That holds big opportunities for WACKER.”
Unity amongst Different Industries
Back in 2010, the German government launched the “National Platform for Electromobility” (NPE) aimed at bringing a million electric vehicles onto the streets by 2020 and at making Germany the lead market for electromobility. “WACKER is positioning itself here as an expert manufacturer of active materials,” says Pfeiffer, who, along with his colleagues, represents WACKER on the NPE working groups. “Never before have companies and industrial sectors shown such solidarity. From raw-material suppliers to automotive companies, the response has been fantastic, with representatives even getting involved in laying down definitions of requirements and specifications. That has accelerated the pace and efficiency of developments.”
Silicon is the key to improving the energy density of lithium-ion batteries. WACKER researchers are investigating ways of increasing the range of future electric vehicles up to fourfold.
The energy storage systems currently employed in electric vehicles cannot match the 600-km range of combustion engines. The average battery pack is only good for 60 to 100 kilometers at the moment. That may not sound like a lot, but “in Europe, more than 70 percent of car trips are shorter than 40 kilometers a day,” says Pfeiffer. “If these were made on purely regenerative electric power alone, the bulk of the carbon dioxide emitted by private transport today could be avoided.”
It is an opportune moment for WACKER to become involved in car-battery development. “Electricity storage technology is set to become the technology carrier in the electrification of powertrains,” says Prof. Ferdinand Dudenhöffer, Director of CAR (the Center for Automotive Research) at the University of Duisburg-Essen. Dudenhöffer expects sales of high-performance vehicle batteries to hit €130 billion by 2025.
Asia has set a blistering pace on the path to realizing these “turbo” batteries. At the forefront are Japan, Korea and China, the most important makers of small electronic devices, who have played a central role in advancing lithium-ion battery technology. The principle is simple: during charging, positively charged lithium ions migrate from the cathode to the anode. During discharging, the process is reversed. The more lithium ions that the anode and cathode can store, the greater is a battery’s capacity.
Silicon Greatly Enhances Battery Efficiency.
While the cathode usually comprises transition metal oxides, e.g. of cobalt or manganese, or iron phosphate, the anode nowadays is predominantly graphite. The researchers aim to progressively replace it with silicon. This is because silicon can theoretically absorb up to 10 times as many lithium ions as can carbon. The problem is graphite swells by roughly 10 percent when it absorbs lithium ions, compared with up to 300 percent for silicon. “Our work here is focused on designing silicon-based active materials that are firmly attached to the anode, but are still inherently flexible. The goal is to substantially reduce the absolute volume swell accompanying lithium-ion absorption and so significantly extend the lifetime of such materials,” explains Pfeiffer.
But irrespective of what optimization work is performed, the weight must be right: automakers nowadays factor 200 kg for the battery into every 1,000 kg that a vehicle weighs. “Consequently, we have to pack much more energy into those 200 kg.” The electrolytes employed at the moment consist of low-boiling organic compounds that are highly flammable. This means that the casings for protecting the system must be made of a substantial material. “The use of silicon-containing electrolytes, which are more flame resistant, or even form a harmless ash, could make a sizable contribution toward increasing the safety of lithium-ion batteries. They could help reduce weight by eliminating the safety measures that would otherwise be necessary.
Innovations Shift Focus onto What Is Feasible
To help them resolve such complex chemical and physical issues, the developers at WACKER have devised a clearly structured innovation schedule called the Stage Gate Process, which spans the range from initial idea to market launch. “Stage Gate requires a strict focus on what is feasible,” stresses Pfeiffer. But there must also be scope left for independent research. The 44-year-old has only praise for the many creative spirits within the various participating teams. “Being innovative requires not only outstanding expertise, but also enthusiasm, targeted action and the ability to think outside the box.” To this end, information exchanges are held at all working group levels. They ensure that communication lines remain open across product and process innovations. These are backed up by a constant exchange of ideas with companies, universities and scientific institutes.
“Step by step gets you to the top,” says Pfeiffer, who is an avid rock climber in his leisure time. He thinks that it will be 2025 or 2030 before the post-lithium-ion technologies of the future, based on lithium-sulfur or lithium-air, come onto the market.
These technologies could possibly quadruple the range of today’s electric vehicles. He is convinced that, here too, WACKER will still be in the vanguard of developments, thanks to its expertise in active materials.
If high-performance energy-storage devices help electromobility to make further inroads around the world, then, during rush hour in 2030, it might well be the dabbawalas who enchant downtown Mumbai with the aroma of steaming curry.
Characteristics
66%of 14 to 29-year-olds in Germany believe that electric vehicles will supersede conventional combustion engines. Younger people are even more certain. Among the over fifties, 55 percent believe that the future lies with the electric car. |
Charging Stationsfor car batteries have been available in all German cities since 2011. ![]() |
Li Lithiumnamed from the Ancient Greek “lithos” (stone) is a chemical element with the symbol Li and the atomic number 3. The element was called “lithium” because, unlike sodium and potassium, it was discovered in stone. It is the alkali metal in the second period of the periodic table of elements. Lithium is a light metal with the lowest density of all solid elements under standard conditions. |
Goals for the application of silicon-based lithium-ion batteries and the potential for increasing their power.
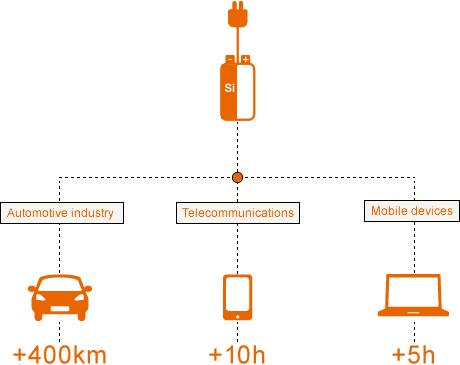
60–160kmis the current range of battery powered cars. Over 70 percent of all journeys in Europe are less than 40 kilometers.
1899was the year that, on April 29, the Belgian racing driver Camille Jenatzy became the first person to drive a car at over 100 kilometers per hour. His vehicle was called “La Jamais Contente” (The never satisfied), and was electrically driven.
1 Millionelectric vehicles, at least, should be running on Germany’s roads by 2020. That is the goal of the National Platform for Electromobility. It is estimated there will be 5 million electric vehicles on China’s roads by 2020. |
70%was the share of world oil reserves consumed by transport in 2011. At the current consumption rate, oil reserves would only last another 40 years. ![]() |