WACKER products are intended for the manufacturing industry rather than for end users. Our products are intermediates in our customers’ production processes, where they are given further added value. Our customers want us to produce these intermediates in a sustainable way. Plus, they expect their products to pose no risks to health or the environment. WACKER’s principle is to provide high-quality products that can be transported, used and disposed of safely and with minimum environmental impact. Here are a few examples from the period under review:
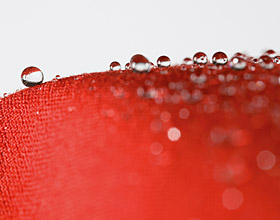
With our WACKER® HC 303 silicone microemulsion, textiles can be impregnated efficiently at low temperatures in a washing machine – without energy-intensive post-treatment in the dryer.
- UV-active silicones for potting and encapsulation: ever more electronic components, such as microprocessors, are being produced for the automotive, power-electronics and sensor sectors. Components are sealed to protect them against heat, contamination and moisture. Until now, the elastomers used for sealing electronics had to be cured for an hour in an oven at 150 °C. We have partnered with our customers to develop a new, UV-active silicone elastomer, SEMICOSIL® UV. It cures by UV radiation at room temperature in just five minutes. This saves energy and greatly reduces cycle times. As a result, throughput can rise tenfold.
- Aqueous silicone emulsions for textile impregnation: outdoor and work apparel is often given a water-repellent finish. Wearing and washing such clothing impairs the finish’s efficacy, so it has to be re-applied regularly. However, aerosol impregnation sprays usually contain organic solvents. Water-based laundry impregnation agents – which are better for the environment – have so far largely been inferior to solvent-based systems. WACKER has developed an aqueous silicone microemulsion, WACKER® HC 303, which can be used to efficiently impregnate textiles at low temperatures in a washing machine. Unlike conventional water-based agents, clothing can be washed and impregnated in a single machine cycle. Clothes no longer require post-treatment by ironing or in the dryer. This saves consumers time, energy and money.
- Solar-grade polysilicon: climate protection and the depletion of fossil fuels are putting the spotlight on renewable resources. At the moment, photovoltaics accounts for just 0.1% of the world’s energy consumption. All the same, the demand for technology to convert the sun’s energy into electricity has been rising for years. Our WACKER POLYSILICON division provides the key starting material for solar modules, namely hyperpure polycrystalline silicon. Each metric ton of polysilicon used in solar modules prevents the emission of some 6,000 tons of carbon dioxide.
In the reporting period, WACKER expanded polysilicon production facilities at our Burghausen site. Capacity rose to 11,900 tons in 2008 – up 40% from 2007’s 8,100 tons. WACKER’s expanded facilities, too, are now a part of our integrated material loop. The planned expansion program at our Nünchritz site is set to see our total annual polysilicon production capacity exceed 35,000 tons by the end of 2011.
Technological advances in silicon-wafer manufacture and solar-module design have increased solar-cell efficiency. Experts predict that grid parity will have been achieved in many parts of the world by 2015: solar power will cost just as much as grid power and its generation will be increasingly unaffected by the political framework. Additionally, the technological progress of recent years has greatly reduced energy payback times. In Germany, it takes about two years for a photovoltaic cell to fully recoup the energy expended on its production. In California, it only takes about a year.
- Binders for exterior insulation and finish systems (EIFS): the sustainable use of energy resources means saving energy, too. By supplying VINNAPAS® polymer powders, our WACKER POLYMERS division helps lower end-user heating costs, while cutting greenhouse-gas emissions. In hot regions, climate change makes it necessary to insulate against heat.
Heating or air-conditioning accounts for half of a building’s energy demand. A house that is inadequately insulated loses a large part of its energy via the exterior walls and roof. EIFS can reduce heating energy losses by 60% and cut the energy lost by air-conditioners by as much as 72%.
VINNAPAS® polymer powders added to the mortar ensure that the EIFS layers bond together firmly. The insulation systems are therefore much more stable, durable and weather-resistant. They permit the use of insulation boards comprising different materials, including renewable substances, such as cork and wood-wool. VINNAPAS® polymer powders can be used to make construction chemicals that meet the strict EMICODE® emissions standards set by Germany’s GEV (Association for the Control of Emissions in Products for Flooring Installation).
There is enormous potential for using EIFS to sustainably reduce greenhouse-gas emissions. According to the German Energy Agency (dena), only a third of all German homes are adequately insulated. Giving a building effective insulation based on EIFS could save 80 million metric tons of carbon dioxide emissions a year – that’s 10% of Germany’s total emissions.
- Saving energy with silicone resin emulsion paints (SREP): some buildings, such as historic and half-timbered houses, cannot be insulated with EIFS. In such cases, a coat of SREP is one of the few ways to improve the building’s energy balance. WACKER SILICONES is a leading manufacturer of silicone resin emulsions for SREP.
A coat of high-quality SREP can cut the heat lost by a facade by as much as 40% (published in a 2007 study by the Fraunhofer Institute of Building Physics). Silicone resins protect masonry against moisture. Damp walls lose heat faster. A SREP coating reduces heat consumption by an average of 4.6%. What’s more, SREPs improve the indoor climate by transmitting water vapor.
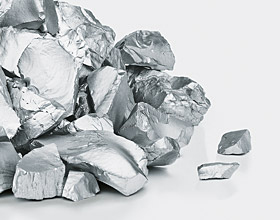
Polycrystalline silicon is the key raw material for solar cells, which transform sunlight directly into electricity. In this way, the sun’s energy is converted into an environmentally-compatible and economical power source.