Microinjection
Precisely Pumped Dosages
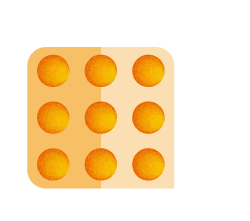
The Right Packaging for Medicine
Our resins help ensure that drugs reach patients safely and intact. When used in tablet blister packs, these resins make sure that the aluminum foil and plastic adhere firmly to each other, yet make it easy to open the pack. Germs and air humidity, which might adversely affect the medicine, don’t stand a chance.
Handy medical devices make life easier for people with chronic conditions. Automated dosing systems are gradually replacing regular injections of essential medication. At the heart of such devices is a microinjection pump made with a housing of the kind developed by Trelleborg, a polymer processor. This required a new silicone elastomer with very special properties.
Morning, noon and night – no matter the hour, people with chronic illnesses always need to monitor their bodies. Diabetics have to check their insulin level. People suffering from Parkinson’s need to adjust their apomorphine dosage. Incorrect dosage of medication can be life-threatening. Some of the diseases mentioned can be managed well with drugs that must be injected subcutaneously: small jabs that perform a vital function. Portable medical devices such as insulin pens are especially convenient, enabling the fast and safe injection of liquid medication in everyday situations. They fit in every purse and can be used without attracting attention. The patient, however, still needs to remember the dosage and timing precisely.
Automated dosing systems now go one step further. These palm-sized medical devices can be attached directly to the skin with adhesive plasters, for example. Located on the surface in contact with the patient is an extremely fine needle that extends automatically to inject a preprogrammed quantity of medicine subcutaneously – without the patient having to make a single move. Precise control regulates even delivery of as little as a few microliters of active ingredient over a period of minutes, hours or even several days. This improves the quality of life of those affected, granting them more flexibility and making their lives worry-free.
“The pump’s ability to administer extremely precise doses of drugs was crucial to the success of the entire device.”
Felix Schädler, Project Manager for Innovation and Technology at Trelleborg
The centerpiece of these medical devices is a tiny microinjection pump that reliably delivers precise doses of the essential medication. Trelleborg was commissioned by one of the world’s leading suppliers of pharmaceutical and medical products to help develop a pump housing made of plastic and silicone. Deep inside this part, a unique, innovative material from WACKER ensures smooth operation. Felix Schädler, who is project manager for innovation and technology at Trelleborg and played a key role in the development, reports that “the pump’s extremely precise dosage of drugs was crucial to the success of the entire device.”
Tiny Parts in Mass Production
The delicate microinjection pump consists of a cylindrical hollow body in which a plunger is moved up and down electrically. It draws the drug from a supply vessel and conveys it to the injection needle. The pump housing comes in different versions that can deliver 2 µl or 10 µl of liquid medication. With a length of 15 mm, the smaller pump is not much bigger than a fingernail. Friction, sealing and the bonding of two different materials in a very tight space posed a challenge to the developers from the start. In addition to wanting a compact design, the customer also attached importance to the lowest possible cost, as the injection pump in the final medical device is a single-use product. For safety reasons, all those elements of the dosing system that come into contact with the medication or the patient must be disposed of after use. That also includes the injection pump. But other components, like the housing, motor and battery, can be reused.
“Due to the compact dimensions and low tolerances involved, the part could only be manufactured using two-component injection molding with seals made of liquid silicone rubber,” Schädler says. Diameters the size of a pin make it impossible to insert localized seals subsequently. The special two-component processing method efficiently bonds two different materials in a single step. The idea was that an almost complete inner lining of the pump cylinder with elastomer should seal the moving plunger and lubricate it at the same time.
Processing liquid silicone rubber (LSR) is the field of expertise at Trelleborg’s Stein am Rhein site in Switzerland, where one- and multicomponent injection-molded LSR parts are manufactured in a fully automated process. In addition to products for the automotive and industrial sectors, Stein am Rhein has a comprehensive cleanroom production facility for medical technology applications. The facility, whose capacity is set to expand, currently has four cleanrooms, where production takes place under strictly controlled and monitored conditions. “The capacity created by the most recent cleanroom expansion five years ago is already being fully utilized, so we are currently expanding again,” Schädler reveals. Two-component injection molding was already common for automotive parts but was less in demand for medical applications. Citing increased pressure on the sector in terms of risk and cost reduction, Schädler explained that that was beginning to change. “What’s more, self-adhesive LSR grades have now become available for food-contact and medical applications,” he adds, “making two-component injection molding possible for these applications for the first time.” Dr. Ulrich Frenzel and Dr. Florian Liesener, who both work in technical marketing at WACKER, couldn’t agree more. They collaborate closely with Trelleborg and, looking back, they consider their microinjection pump to be a very special achievement in materials development.
When thermoplastic elastomer (TPE) proved unsuitable for this specific application, Schädler and his team initially turned to SILPURAN® 6700 self-adhesive liquid silicone rubber. WACKER has marketed specially developed silicones for medical technology under the SILPURAN® brand for a little over 10 years. Frenzel, a trained chemist, explains: “In this LSR line for sensitive applications, we use special formulations that can satisfy particularly demanding purity requirements, setting them apart from our silicones for engineering products.”
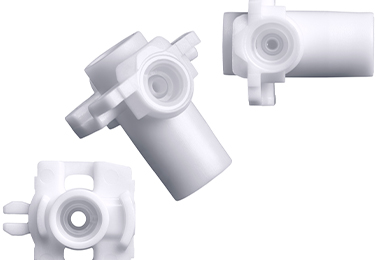
An inconspicuous, albeit technically perfect part: the plastic pump cylinder is lined with a fine, yet multifunctional, layer of silicone elastomer.
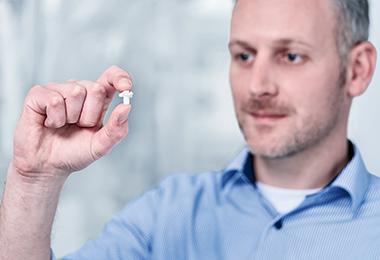
The microinjection pump developed by Felix Schädler and his team at Trelleborg is not much bigger than a fingernail.
Specialty Line Enables Efficient Production
When it launched in 2008, SILPURAN® 6700 was WACKER’S first self-adhesive LSR line marketed specifically for applications in medical technology. Their exceptional adhesion to any number of thermoplastic materials makes these LSR grades ideal for two-component injection molding. Functional parts that have been directly injection-molded and firmly bonded can now also be mass-produced inexpensively, quickly and reliably for medical technology.
Tests conducted with the medical-device manufacturer and Trelleborg’s elastomer laboratory in Stuttgart demonstrated, among other things, that SILPURAN® 6700 can withstand long-term storage with the medication. Since the drugs come into direct contact with the seals, interactions of any kind had to be ruled out. When the pump’s functionality was put to the test, however, it turned out that the friction between the plunger and the cylinder surfaces made of SILPURAN® 6700 was too high. Even the slightest over- or under-dosage of medication can lead to life-threatening situations for the patient; it is therefore essential for the pump to operate smoothly. If friction between the plunger and cylinder were high, more force would have been required for the pumping action, which in turn would have necessitated a different drive and thus a larger device overall. Alternatively, the customer could have used lubricants. Those, however, would inevitably come into contact with the drug being delivered and possibly impair or, in the worst case, contaminate it. For the same reason, the use of oil-bleeding silicones such as those offered by WACKER for automotive applications was ruled out. While these automotive grades do have very low friction values, they cannot be used for medical applications. It is imperative to prevent oil from mixing with the drug and inadvertently being injected into the patient. WACKER’S materials specialists found a solution that works without oil.
“In view of our strong, longstanding partnership with WACKER’S materials developers, we presented them with this challenge,” Schädler says. They very quickly came up with some initial ideas for an innovation that might work. A wholly new materials technology was developed and ready for marketing within just one year.
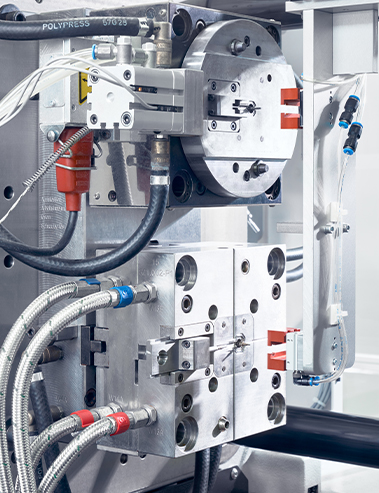
View of the two-component injection-molding tool. In one production cycle, the plastic part is first manufactured on the two mold halves, and the silicone elastomer is injected immediately afterwards.
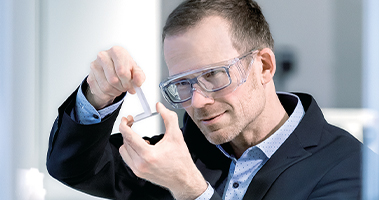
Dr. Florian Liesener is an expert in silicones. Here, he is testing a two-component compound. The self-adhesive silicone bonds reliably with the thermoplastic base part.
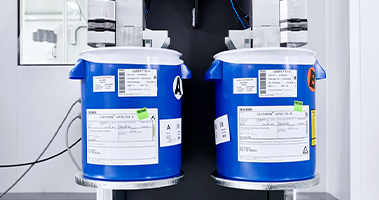
An innovative material consisting of a silicone resin and a crosslinker component, SILPURAN® 6760/50 enables sealing and high friction in the smallest of spaces.
Opposing Properties
“We already had liquid silicone rubbers with self-adhesive properties in our portfolio, as well as products with low coefficients of friction, but none for sensitive applications that offer both together,” Liesener recalls. “The micropump was thus the perfect opportunity for us to combine both properties in one silicone.” The resulting LSR would have to have properties that appear physically incompatible: high adhesion and low sliding friction – in other words, holding on and letting go at the same time. Impossible, one might think, “and yet WACKER demonstrably solved this chemical conundrum, without any problems,” Schädler says with admiration.
The materials specialists want to reveal only this much about the technology: an additional formulation component modifies the self-adhesive silicone in such a way as to significantly reduce the friction with the surface of the other material. This creates a permanently friction-modified surface even without the addition of exuding oil. “That is the key requirement for this application,” Liesener says.
The material developed made its public debut under the name SILPURAN® 6760/50 in 2016. To this day, it is the only market-ready, self-adhesive, friction-modified liquid silicone rubber with biocompatibility certificates.
“The micropump was a good opportunity to combine different material properties.”
Dr. Florian Liesener, Technical Marketing, WACKER
Complementing their successful collaboration in developing the material, Liesener, himself a silicones expert, found that the Trelleborg specialists possessed extensive know-how and experience in the production process. The fixed pump cylinder consists of a glass-fiber-reinforced engineering plastic. It is initially manufactured in an injection mold. In a second step, the inner wall of the cylinder is then lined with an extremely thin layer of SILPURAN® 6760/50. “We had to adhere to manufacturing tolerances of two hundredths of a millimeter,” Schädler remembers, “with the materials themselves already shrinking by as much as 35 percent.” To solve this and other critical production problems, Trelleborg worked with its customer to improve the part’s design in a way that would make it technically feasible. “That compelled us to refine our manufacturing technology,” Schädler says. The injection pump is manufactured in a cleanroom and is currently one of the smallest two-component parts that Trelleborg manufactures on site. The experts involved agree that, given the current state of the art in manufacturing, it could not be made any smaller. SILPURAN® 6760/50 plays an important, and reliable, dual function in the compact drug-delivery device. It may be invisible to its users, but it gives them completely new freedoms.