A TV in Your Pocket
Seoul, South Korea: in the new “Center of Electronics Excellence,” a team of WACKER experts is working on silicones for the high-tech applications of the future. For example, the chemists are developing silicones for flexible displays that will allow screens to be folded up, or even rolled up.
“Not Really Very Practical, Is It?”
Dr. Kyuha Chung reaches into his pocket and pulls out his cellphone, a thick smartphone with a screen the size of a postcard. Every second passenger in the Seoul metro is whiling away their time with a similar device. “Not really very practical, is it?” says the slender Korean with a smile. Then he places his ballpoint pen next to the phone. “What if we could roll up the display to the size of this pen?”
Innovations for Technology Leaders
Kyuha Chung, vice president of Wacker Chemicals Korea Inc., was personally involved in the rise of the South Korean electronics industry. The chemist worked for Samsung Electronics for many years, helping to develop the first 40-inch OLED displays. “Back in the nineties, Korean products were considered run of the mill,” he says. Now, Korean electronics companies are among the world’s technology leaders, continually looking for innovations. “They make excellent end products, but need outstanding raw materials from other companies,” explains Chung. That is where WACKER’s Center of Electronics Excellence (COEE) comes in, which Chung heads.
In 2012, COEE started work on high-tech silicones for the electronics industry. The new lab is located in Pangyo, South Korea’s silicone valley. This area, in the south of Seoul, has become a magnet for high-tech startups, research institutes and software companies. Engineers are testing their robots on the campus under the midday sun. Behind the shimmering green of the South Korean headquarters’ glass facade, WACKER, too, is busy working on many innovations for LEDs, displays, automotive electronics and semiconductors.
Speed Is of the Essence
COEE provides new products and tailored solutions to customers from the region, since demand for high-tech materials is growing in both South Korea and its neighbors, such as China and Japan. “Speed is of the essence,” explains Kyuha Chung, who has excellent contacts within the industry.
“Either you are there on the spot, or you are out of the picture.”
Dr. Kyuha Chung, vice president of Wacker Chemicals Korea Inc.
“We can be in daily contact with customers here. The customers we see are very demanding, and aren’t prepared to wait weeks for a sample. “Either you are there on the spot, or you are out of the picture.” Even when his staff is groaning from long nights in the lab, the short gray-haired man still presses them on: “The electronics market runs at its own pace.”
In the lab, employees test UV-activated silicone gels for optical lamination.
The First WACKER Site in Asia
Wacker Chemicals East Asia Ltd. in Tokyo, Japan, was found ed on January 8, 1983, as a sales office for Wacker-Chemitronic GmbH’s products in Japan, Hong Kong, Taiwan, South Korea and the People’s Republic of China.
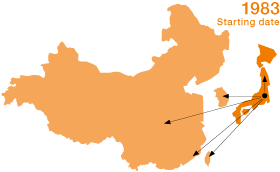
The LED Market Takes Top Priority
Fortunately, says Chung, his team can rely on WACKER’s extensive know-how. “If we had to do everything on our own, I would never have taken on the job in the first place,” he says, laughing. “We get the building blocks from our colleagues in Germany and use them to build new products.” Han-Hyung Cho, head of the Wacker Chemicals Korea subsidiary, has a clear idea of what WACKER can achieve with silicones for the electronics sector when the small R&D team puts its mind to it. “We are only just starting out, but we want to be number one in certain segments,” he says. “We can’t afford to fritter away our energy.”
Sales of silicones for the electronics sector are forecast to rise tenfold between 2010 and 2020. The LED market has first priority. COEE mainly concentrates on materials for lenses and for encapsulating chips. Because of the long lifetime of the LEDs, silicones are the material of choice here, since they also maintain their special properties in the long term: they are thermally stable and provide protection against UV radiation, moisture and vibrations.
“We are seeing a global turnaround, a revolution toward LEDs,” says Dr. Christian Hartel, head of the WACKER SILICONES division: the fate of the incandescent bulb is already sealed in much of the world. According to a study by management consultants McKinsey, the LED will command a 65-percent share of the global market in 2020. The transformation is taking place particularly fast in Asia, which is also the biggest market. In 2020, Asia is expected to have a share of 45 percent of the global lighting market.
“We are only just starting out, but we want to be number one in certain segments.”
Han-Hyung Cho,
president of Wacker Chemicals Korea Inc.
Kyuha Chung knows there is fierce competition on the LED market. “We will have to achieve success very soon,” he says. The first innovations from COEE are already being manufactured in the Jincheon plant, 100 kilometers southeast of Seoul. To meet the electronic industry’s strict demands, WACKER has set up a cleanroom there, to produce high-tech silicones under dust-free and ultra-clean conditions.
Dr. Chung and his team are optimistic that other new developments will follow soon. One customer is currently testing an innovative silicone gel for airtight bonding of cellphone displays and PC monitors to the protective screen. “It will cut out reflections altogether,” explains Dr. Chung, showing the difference between two displays in the lab. “Optical lamination” as it is called is a new, strongly growing market.
Another new market is that for flexible displays. Here, WACKER is working in a research cluster financed by the South Korean government. That is potentially a billion-dollar market for silicones, says Chung, though at this stage it isn’t clear which technology will prevail. “That’s why we’re not putting all our eggs in one basket,” he adds. But Dr. Chung is sure about one thing: “Flexible displays are on their way.”
Kyuha Chung shows one of the samples that could one day become a display, a composite film of glass fiber and silicone. A South Korean electronics manufacturer will launch the first foldable displays in late 2015, which will double their size. The next step would be displays you can roll up. And one day, who knows? You might actually be able to carry a 20-inch TV in your pocket.