Energy Supply
An Energy Mix in Changing Times
WACKER has set itself the goal of halving its specific energy consumption by 2030 compared with 2007 – which is a challenge. Stefan Henn, in charge of Energy and Utility Supply at the Burghausen Plant, is working with his team on ways to turn this vision into reality.
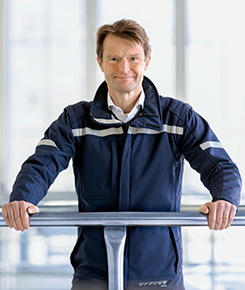
The heart of the WACKER Group is a 2.6 km2 production site in Burghausen, a small town in southeast Germany. Located near the Austrian border, this site has been manufacturing a large part of the Group’s products for over 100 years. The size of the site is vast, with production facilities as far as the eye can see. Industrial plants and pipelines cover an area larger than the Principality of Monaco. The energy required at the Group’s largest production site is correspondingly high. The demand for electricity alone accounts for about 0.5 percent of German electricity consumption, with electricity, alongside process steam, being the most important source of energy for production.
Broadly speaking, Stefan Henn and his team have taken on the mammoth task of determining the makeup of the energy mix of the future and of making it as climate-friendly as possible. As head of Energy and Utility Supply in Burghausen, he is working on one of the greatest challenges facing the German chemical industry at present: the transition to supplying as much climate-friendly energy as possible.
This kind of task requires tremendous commitment as well as mental agility and sheer hard work. “At present, we are focusing intensely on our energy strategy for 2030,” says Henn, who has been working at the chemical group for 26 years. When he was appointed head of the Energy and Utility Supply department at Burghausen just over a year ago, he started working flat out on the company’s future energy strategy. “We must start right now to get an overview of the situation in order to have solutions at hand very soon,” he says.
The energy project began in July 2021. According to the targets now set by the Group, greenhouse gas emissions are to be halved by 2030, compared with emissions in 2020. The same applies to specific energy consumption, which is to be cut in half, compared with 2007. Henn and his colleagues are in charge of finding ways to achieve not only these two goals, but even more targets in the future. They form a 20-strong project team of energy experts, planning engineers, purchasers of raw materials, and Controlling staff, who are all involved in devising a broad range of strategies. “We are looking at all the possible ways of reducing carbon emissions produced by our site’s energy supply.”
Green Electricity from Hydroelectric Power
A trip back in time shows that a sustainable energy supply has played an important role since the early days of the plant. The deciding factor for the choice of location more than one hundred years ago was hydroelectric power. That was the only way of obtaining the enormous amount of electricity needed for energy-intensive electrochemical processes.
The company’s founder had a 16-kilometer canal dug in order to transport water from the Alz river to one of Germany’s largest privately run industrial hydroelectric plants, known as the Alzwerke. Since it came into operation in 1922, WACKER’s own hydroelectric plant has provided production with green hydroelectric power. “Renewable power was a crucial location factor for WACKER,” Henn explains. “Initially, the Alzwerke hydroelectric plant was able to cover 100 percent of the company’s power needs as well as supplying households in the surrounding area with electricity.”
On average, the hydroelectric plant produces 265 million kilowatt-hours of electric power a year, enough to supply 90,000 households with electricity. However, the Alz canal has another added benefit for the site: the canal runs through the site from east to west and provides it with cooling water. “Historically, there are many facilities operated here with continuous-flow cooling,” says Henn. “The Alz canal also feeds our emergency power supply, which is in constant operation, so we don’t need any large diesel generators that have to be started up in an emergency before they can provide electricity.”
An Energy Mix in Changing Times
The hydroelectric plant supplies an enormous amount of energy but its capacity is limited. We cannot simply increase the amount of water taken from the Alz river, nor can we change the transport volume of the canal. However, what has changed is the energy required by the plant. Back in the 1940s, power generation and consumption were virtually the same. Modernization work and more powerful turbines brought short-term relief in the 1950s. But even back then it was quite obvious that the power station would not be able to meet the plant’s energy needs in the long term.
Today, the amount of energy which the hydroelectric plant supplies to Burghausen is roughly 10 percent. WACKER buys in around 55 percent of its power from external electricity suppliers. The remaining 35 percent is produced in a combined heat and power plant on site, where natural gas is converted into electricity and process steam. The steam, in turn, provides the energy for the chemical processes in production.
The combined-cycle gas turbine power station in Burghausen is one of the most advanced of its kind, with 90-percent fuel efficiency. This means that as much as 90 percent of the energy contained in natural gas is converted into usable electricity and heat. How much is produced depends on the steam required by the plants. “In general, the facilities in Burghausen are heat-driven,” Henn explains. “That means that the amount of process steam required in the plant defines the amount of electricity produced.”
Steam obtained from heat recovery at the Burghausen site Share of total demand is rising constantly
Optimized use of heat and process steam in production are crucial for Burghausen’s energy strategy. WACKER has therefore invested a great deal in heat recovery – with successful results.
Take polysilicon production, for example. The deposition of hyperpure silicon for the solar and semiconductor industries is particularly energy-intensive. The process takes place in bell-shaped reactors which are heated to 1,000 degrees Celsius. Thanks to an ingenious system, a large portion of the heat can be recovered and fed back into the site network as steam.
60-Percent Steam Recovery
This and other measures mean that every year the site has been able to feed more energy from production back into the heat-integration system. In 2011, approximately 40 percent of the steam needed came from heat recovery, while today that amount has risen to 60 percent. And that’s not all: in Henn’s opinion, the plant may well produce a mere 20 percent of the required steam in 2050. The much larger amount – 80 percent or more – will be provided by heat recovery.
“For every kilogram of steam saved by heat integration, we reduce the amount of natural gas needed to generate steam, thereby cutting climate-damaging CO2 emissions too,” says Henn, adding that WACKER had its roots in energy-intensive electrochemistry and that looking for and raising optimization potential had always been important. “Dealing efficiently with energy, whether it be electricity or heat, is basically in WACKER’s DNA.”
Alternative Sources of Energy
Henn is convinced that emissions will continue to fall drastically in the future. “If we are striving for carbon-neutral production in Burghausen as a vision for the future, we have to sound out all the options right now.” Henn’s team is testing, for example, whether the heat supply can be changed over to heat pumps. It is also examining whether the CO2 that forms during steam generation can be separated and used as a material. Procuring solely green electricity from external energy suppliers in the future is another option that WACKER’s energy experts are looking into. “Nothing is off limits,” says Henn, “we have CO2 in our sights and are really assessing every possibility we have to reduce emissions.”
What is technologically feasible, what is economically viable? Which energy sources can be used sustainably? And what do we have to invest in to achieve net-zero production? Stefan Henn and his team are currently focusing on these issues and drawing up sustainable scenarios for the future. They are getting plenty of encouragement and backing from management: “You can just tell that energy is becoming a topic of increasing importance to us as a chemical company,” he explains.
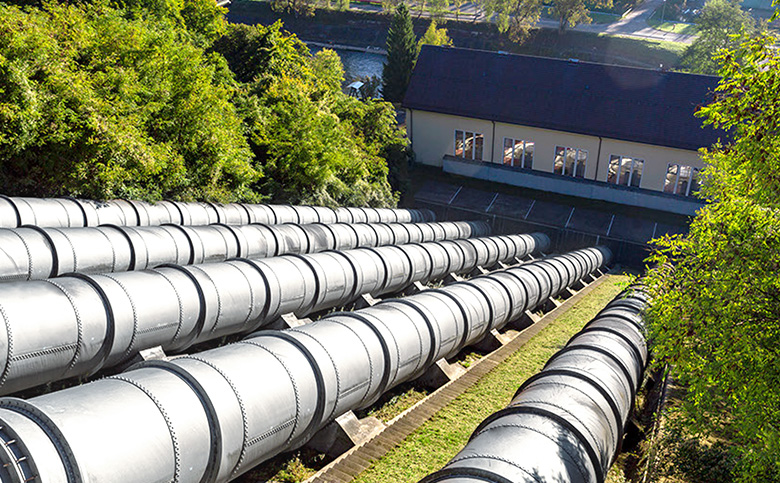
The challenges are enormous, however, not only for Burghausen. Energy suppliers and companies in the region are also working on net-zero solutions. WACKER is therefore taking an active role in industrial and research projects which are developing scenarios on how to cope with the demand for green electricity in the region.
The recently initiated project entitled “Trans4In – Energy Transformation in ChemDelta Bavaria,” an initiative launched by the Research Institute for Energy in Munich (FfE), is focusing, for example, on possible ways of achieving carbon neutrality in the region. These ideas were prompted by the predicted energy consumption in the industrial sector and by the kind of impact the demand for green electricity would have on energy generation and energy transport in the region.
Many things still need to be clarified – alongside technological issues, the basic political parameters for such a transformation. One thing is certain, Stefan Henn says emphatically, “as one of the largest electricity consumers in ChemDelta Bavaria, WACKER’s Burghausen site will do its bit toward developing sustainable regional solutions on the road to climate neutrality.”