Integrated Production
Waste Nothing, Use Everything
A tangle of buildings crossed by countless pipelines: at first sight, WACKER’s site in Nünchritz is difficult to fathom. And yet this complex, integrated setup is the key to low-waste and energy-efficient production. It’s worth taking a closer look, as the best is gotten out of every atom and every kilowatt-hour of electricity here, sometimes even several times over.
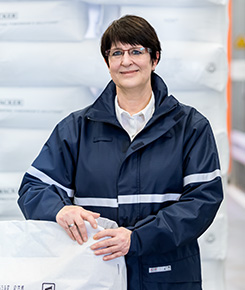
The site’s highest platform is right at its center. This is the roof of the pyrogenic-silica production facility and Dr. Jutta Matreux’s favorite spot. Only the long, thin reaction columns nearby are taller than the site manager here. She likes having a look around from these lofty heights. “From here, I don’t just get the best view of our Nünchritz site,” says Matreux, “I can also see how it is nestled into the surrounding landscape.” To the west, the Elbe river slowly flows by. At the northern fringe, the nearest residential housing can be seen – looking tiny from up high. Opposite, there is a local recreational area and nature reserve. The mountains of the Saxon Wine Route can be made out in the distance and the Elbe Sandstone Mountains rise majestically on the far horizon. “We have a particular responsibility here,” continues the site manager, “For our products, people and the surrounding environment.” It is all interconnected, on both a large and a small scale.
Production at the WACKER site in Nünchritz is particularly low in waste and highly energy-efficient. This is confirmed by the latest environmental-performance indicators: in the period since WACKER took over the site 20 years ago, solid waste, wastewater volumes, exhaust air load, effluent burden and carbon dioxide emissions have each been reduced by more than 90 percent per metric ton of gross production. “An impressive achievement, considering the site was greatly expanded during this time,” adds Matreux, not without pride. Total gross production has increased by a factor of 26 over these last 20 years. From the roof, the recipe for success is visible directly below her: processing plants with hundreds of thousands of individual components that together make up a highly integrated system. Here, everything is recycled. Waste products and byproducts from one production stage are fed back into production elsewhere – as raw materials or in the form of energy, for instance. Almost everything procured by the site is converted into salable products.
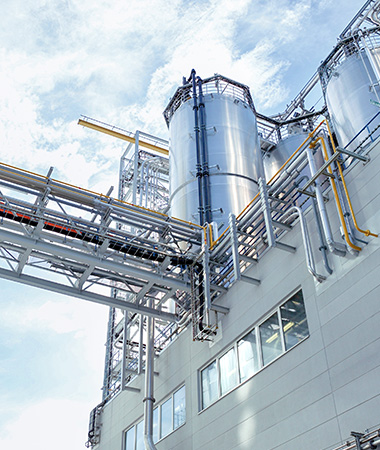
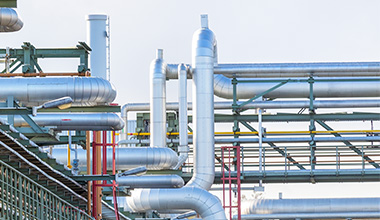
Efficiency Is More Than the Sum of Individual Parts
A bird’s eye view of the Nünchritz site looked quite different in 1998. On an aerial photograph from back then, Matreux shows that not only was the total area much smaller than it is today – a closer look reveals that the few plants were also rather cut off from one another. Fewer pipelines connected them with each other. In short, it was not yet a closed integrated production system. Capital expenditures of €1.7 billion have since greatly altered the appearance of the site. Plants along the chemical reaction pathways for synthesizing silicones and polysilicon were expanded or rebuilt. A highly integrated structure was always the focal point here. Matreux is confident when she says, “A chemical site like this one can only be operated economically with closed material and energy loops.” This holds true to this day. The considerable expansion since WACKER took over has allowed the integrated loops to be aligned and optimized. The history of the WACKER site in Saxony shows that sustainability and profitability do not just belong together, they depend on each other.
“A chemical site like this one can only be operated economically with closed material and energy loops.”
The heart of the integrated materials system – the hydrogen chloride plants – is located in the northeast of the site. Hydrogen chloride, a colorless gas, is used in two loops – one for silicone, one for polysilicon. It is the real champion of the integrated production system here. At various stages of production, hydrogen chloride gets the inherently inert starting materials silicon and methanol to react again and again. It combines with methanol to form chloromethane, for example. Chloromethane, in turn, reacts with metallurgical-grade silicon in a fluidized-bed reactor to yield a mixture of different methylchlorosilanes (Müller-Rochow process). Distillation of the silanes and subsequent hydrolysis, or alcoholysis, produce siloxane, pyrogenic silica and various silane byproducts. The latter are processed into silicone fluids or specialty silicones, for instance, and sold. Hydrogen chloride itself is recovered, purified and used again.
The integrated hydrogen chloride system is also the key to polysilicon production with added value. Ground metallurgical-grade silicon reacts with gaseous hydrogen chloride to form trichlorosilane. Rods of pure polycrystalline silicon – polysilicon – are then obtained from this ultrapure liquid. The hydrogen chloride released here is also fed back into the loop.
“We try to circulate every single molecule of hydrogen chloride and reuse it several times,” underscores Matreux. Statistically speaking, a single chlorine atom can therefore be reused up to eight times in comparable integrated production systems. The idea is to waste nothing and make use of everything. Hydrogen chloride is nevertheless inconspicuous, because, except for very small, salable residual amounts, it is not contained in any of WACKER’s subsequent sales products.
HDK® Links the Loops
Recycling of hydrogen chloride is not the only distinguishing feature of the integrated production system, however. There is also the clever combination of byproducts to create new sales products. The best example of this is pyrogenic silica. The plant where it is produced has the roof with the beautiful view mentioned earlier. So, let’s leave the roof and enter the building.
This is where you’ll encounter pyrogenic silica, which WACKER markets as HDK®, in the form of a fine white powder. As a kind of Swiss army knife of auxiliaries and additives, it finds use in a wide range of applications – from easy-flow ketchup to finely pressed tablets to optimized automotive paint. HDK® is marketed directly as a sales product. Additionally, in the integrated production system, it links the polysilicon loop with the silicone loop like no other product. The manufacture of ultrapure polysilicon generates chlorosilanes among other things, which can be converted into pyrogenic silica in the HDK® facility. This HDK® is, in turn, used elsewhere: in the modification of silicones, for instance, to increase their strength or flowability.
Integrated Production in Nünchritz
Currency of the Future: Energy and CO2
The energy loop is less obvious, but equally important for a highly integrated production system. The Nünchritz site needs around one terawatt-hour of electricity per year for its energy-intensive production setup. The majority of this is sourced from the public grid. “Every watt that is not consumed doesn’t cost us anything either,” says Matreux. Given the recent record electricity prices, this is a big lever. Beside electricity, steam is the site’s main energy source. WACKER generates steam from natural gas in an environmentally friendly manner at its own thermal power plant. Where possible, waste heat and steam from chemical energies are directed to other plants and used there. The site’s own residue incinerator extracts the last little bit of energy even from materials that can neither be processed further nor sold. “We don’t just attach great importance to conserving resources, we also strive to make the best possible use of our production-plant media such as energy, steam, electricity and water,” she explains. The association of northeast German chemical companies (Nordostchemie) recently honored our success in this regard. It bestowed its Responsible Care® Award 2021 on the Nünchritz site for particularly high CO2 savings in its production processes. Measures to improve heat recovery, together with options to reuse energy, have led to a reduction in the use of primary energy (natural gas) at the Nünchritz cogeneration plant and a cut in the site’s annual CO2 emissions by 30,000 metric tons. What is more, the site now covers around 70 percent of its overall steam needs through heat recovery.
Its highly integrated production system is WACKER’s major strength. The best possible use is made of energy and materials – making, for example, ultrapure-polysilicon production with added value feasible in the first place. Purpose-designed production pathways, reuse and recycling of raw materials, and energy efficiency are key to sustainable and economical production. These kinds of measures are in demand more than ever going forward in order to achieve global climate goals. At the Nünchritz site, employees are already working on new projects. As part of a groupwide decarbonization roadmap, they are testing further technologies that could be used in Nünchritz. They are doing this to ensure that the integrated production system will remain true to its history over coming years and will keep getting better.
The WACKER Group’s Integrated Production Sites
Nünchritz (Saxony, Germany) isn’t WACKER’s only integrated production site. Burghausen (Bavaria, Germany) and Zhangjiagang (China) are too. They are likewise characterized by predominantly closed production loops, in which, for example, 93 to 96 percent of hydrogen chloride is reused. By supporting each other, these sites also form a groupwide integrated system. Nünchritz, for instance, is the global hub for siloxanes, which are held there in large volumes and then shipped to the other sites. This ensures that the continuously producing integrated system can keep going even during planned shutdowns or maintenance. WACKER employs state-of-the-art environmental technology and adheres to stringent EHS standards at all three integrated production sites.