Biomass Balance Approach
Renewable Raw Materials Have a Future
WACKER already offers organic polymer and silicone products that are manufactured with significantly fewer fossil raw materials. Instead, byproducts of the wood industry or raw materials derived from biomass are used. A certified method is used to provide end-to-end verification that renewable raw materials are used in production through to the end product.
For a long time, attitudes to chemical products could still be summed up in a quotation from the ancient statesman Pericles; “Don’t judge them by their provenance but by their performance.” Of course, the 5th century BC politician was talking about people. But end consumers and industrialists no longer view chemical substances solely according to what they can do in day-to-day use, and with good reason. In view of increasing raw materials scarcity and global warming, customers are asking more and more about the origins of such products and what ingredients they contain.
This is also confirmed by a recent survey of industrial customers of the WACKER POLYMERS business division. 75 percent of customers in the Europe, Middle East and Africa region report that sustainability is an important or even very important issue for them. The use of bio-based raw materials is also top of the priority list for many of the respondents.
But how can this desire to employ renewable raw materials be realized in practice? The apparently simple recipe for processing renewable raw materials instead of fossil-based ones in existing production facilities is full of pitfalls: it presupposes that every raw material has a bio-based counterpart that is available in sufficient amounts and in comparable quality. Such an approach would make production considerably more expensive. A bio-based raw material usually costs more than its petrochemical counterpart. Since the properties of the product are not otherwise improved, only a few customers would probably be prepared to pay a surcharge for sustainability.
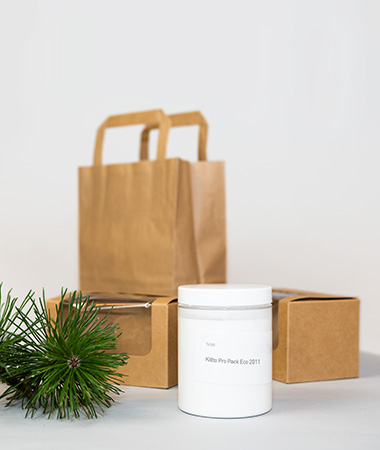
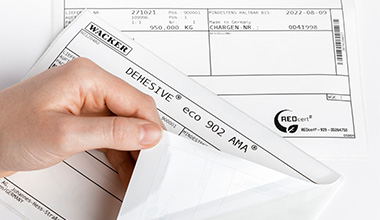
WACKER therefore proposes taking a different route and processes plant-based alternatives alongside petrochemical raw materials. One example is acetic acid – an important chemical building block for the manufacture of polymeric binders based on vinyl acetate-ethylene copolymer. The acetic acid for such products has been derived from petrochemicals until now. But there are alternatives. Acetic acid, which occurs as a byproduct of wood processing, can be used in just the same way.
Bio-Based Methanol Replaces Fossil Counterpart
The same applies to methanol. Along with silicon, it is a key raw material in silane and silicone synthesis. While WACKER used to take the methanol it required from fossil sources, it now increasingly uses plant-based methanol. The products have exactly the same properties and can be processed in the same way. Chemically and physically, the eco and standard products are absolutely identical.
The amount of bio-based raw material determines what products may be labeled as resource-efficient ones. “The biomass balance method thus guarantees that the amount of eco products corresponds to the ratio of the renewable raw materials used,” explains Dr. Peter Gigler, who is responsible for sustainability at Group level. “If you buy an eco product from us, you can be sure that a corresponding amount of the renewable raw material is also used in production. Our calculations are scrutinized annually by external auditors.”
Biomass Balance Approach
The biomass balance approach is now used for 68 products. For example, WACKER POLYMERS offers over 20 VINNAPAS® grades in an eco version: vinyl acetate-ethylene copolymer binders are used, for example, for enhancing mortars, as tile adhesives or for formulating adhesives, wall paints and self-leveling flooring compounds.
Such VAE copolymers are manufactured mainly from vinyl acetate and ethylene. For VINNAPAS® eco products, the business division uses vinyl acetate from acetic acid derived from wood processing and pulp production. The wood comes entirely from forests certified as sustainably managed. WACKER POLYMERS is also looking for alternatives to ethylene, the second key raw material in VAE. “We are continually looking for further bio-based raw materials and are making every effort to expand our raw-materials base for the biomass balance,” says Linn Mehnert, head of sustainability, environment, health and workplace safety at WACKER POLYMERS.
The eco campaign is attracting great interest from customers. “Demand for VINNAPAS® eco is growing steadily,” says Dr. Christine Wagner, who is responsible at WACKER POLYMERS for marketing in the EMEA region: The traditional Finnish company Kiilto, a purchaser of VINNAPAS® eco since its launch, offers, e.g., its own adhesives range under the name Kiilto Pro Pack eco for customers in the packaging and paper industries. Kiilto’s Business Area Director Tomi Takala is confident about the eco approach: “A hallmark of our activities is our especially strong commitment to developing environmentally friendly solutions. VINNAPAS® eco helps us to live up to our claim to be a pioneer in matters of sustainability.”
Eco Products Are in Demand
The WACKER SILICONES business division, too, is experiencing growing business in its eco products. Its traditional brands, such as BELSIL® and ELASTOSIL®, have long been available as “eco” versions. “Well-known cosmetics manufacturers are already using BELSIL® eco. We already offer 13 eco products, which, for example, makes lipstick kissproof and ensures silky easy-to-comb hair,” says Dr. Claudius Schwarzwälder, global segment manager for consumer care products.
Axel Schmidt, too, is noticing strong interest by key account customers. He is responsible for Sealants & Adhesives, and is thus responsible for ELASTOSIL® eco joint sealants. Though WACKER SILICONES produces joint sealants and also fills them into ready-to-use cartridges, they are marketed by the customers. “We already have the first consumers who have integrated the ELASTOSIL® eco label in their cartridge design,” says the manager with a touch of pride. Homeowners and professional users throughout Europe would now be able to use sustainably manufactured silicone sealants for any conceivable construction and renovation project.
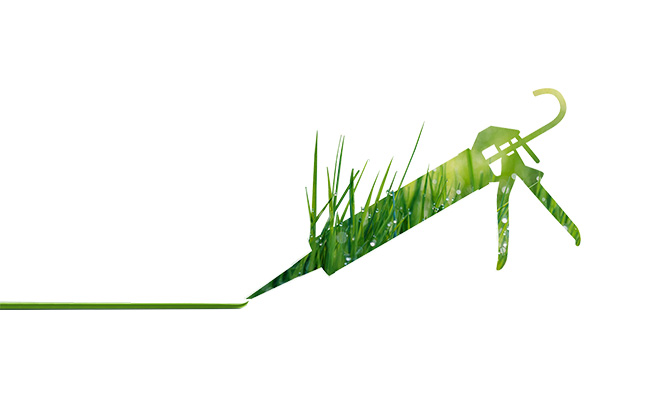
Demand for eco silicones is increasing in other industries, too. And it is therefore only fitting that the business division continually expands its product portfolio. Silicone-based polishes and care agents (LIOSIL®), foam-control agents (PULPSIL®, SILFOAM®), release coatings (DEHESIVE®, CRA®) and textile softeners (WETSOFT®) are now available in fossil-free versions. “To manufacture one kilogram of BELSIL® eco DM 350 silicone fluid, up to 0.89 kilograms of biomethanol is used as replacement for the fossil methanol and other fossil-based raw materials,” calculates Erich Schaffer, responsible for sustainability at WACKER SILICONES.
The highest sustainability standards apply here, too: only certified biomethanol from straw, grass cuttings or sugar beet residues is used – i.e. from biomass that cannot be used for food production. The grass cuttings, for example, come from the green verges alongside freeways and may not be fed to animals.
WACKER’s eco initiative shows that high-performance products based on renewable raw materials are no pipe dream. “The time is right. We sense that many customers and end consumers are more than ready to switch to sustainably manufactured products,” says Peter Gigler. It is still early days, but the trend is clear. “With our mass balance approach, we are starting a transformation toward the use of bio-based raw materials. We will take our customers with us and constantly adjust our portfolio according to the growing demand,” says the sustainability expert. “And one day, we will even build and operate plants that only process alternative raw materials.”