Sustainability
Managing Sustainability
Companies can be profitable in the long term only if they take their responsibility toward the environment and society seriously. That is why sustainability has been firmly rooted in our business processes for many years. The importance of sustainability to us is demonstrated by the fact that we have made it one of our five strategic goals and have compiled our own Code of Sustainability. Sustainable development means balancing economic, ecological and social factors in everything we do.
Two voluntary global initiatives form the basis for sustainable corporate management at WACKER: Responsible Care® (the chemical-industry initiative) and the UN’s Global Compact. Through this voluntary commitment, WACKER undertakes to protect the environment, employees and society above and beyond legal requirements. We expect our suppliers to observe the principles of the UN’s Global Compact and the Responsible Care® initiative, and have included this in our general terms of procurement. Together with some 40 other chemical companies, WACKER Greater China renewed its commitment to the Chinese Responsible Care® program in 2014. The WACKER region had joined this initiative of the Association of International Chemical Manufacturers in China in 2008.
Substantial progress was made on strategic sustainability-management projects in 2014:
- Group Certificate
Our Group certification ensures that customer-driven specifications and our corporate standards are implemented at all WACKER sites. In the reporting year, we included the technical competence center in Mumbai, India, in the Group certification for ISO 9001 and ISO 14001. Almost all WACKER production sites are now included in the Group certificate. Not yet included are the sites in Brazil, the Kolkata plant of Wacker Metroark Chemicals Pvt. Ltd., India, and the Halle (Germany) site acquired from Scil Proteins Production GmbH in 2014. All these sites, however, have corresponding individual certificates.
- Greenhouse Gas Emissions
In 2012, we began calculating our indirect greenhouse-gas emissions in accordance with Greenhouse Gas Protocol Scope 3. These emissions include all those generated along the supply chain, e.g. by suppliers or through waste disposal and the transportation of products. In 2014, we added further Scope 3 categories and adapted our calculation methodology to the GHG Protocol guidance for the chemical industry. The Group’s carbon footprint is an important tool for improving climate protection.
oekom research AG, a German sustainability rating agency, gave WACKER a good overall rating of B–. According to oekom’s rating methodology, our company is classified as “Prime.” The status makes WACKER’s publicly traded securities eligible for investment from an environmental and social perspective. oekom’s clients include financial service providers with over € 600 billion in assets invested on the basis of the rating agency’s sustainability research. oekom has been assessing WACKER since 2008.
- Sustainability Platform
In 2013, our new IT system for sustainability reporting (SPIRIT) was implemented groupwide, replacing various individual systems. We use the new software to collect and manage environmental and energy data, environment- and safety-related incidents and Integrated Management System (IMS) audits. The tool went live at all of our major production sites during the reporting year, replacing over 70 percent of our existing systems.
Compliance Management Takes Aim at Cybercrime
WACKER’s ethical principles of corporate management exceed legal requirements. Employees can direct their questions to 22 compliance officers worldwide, who are based in Germany, the USA, China, Taiwan, Japan, India, South Korea, Brazil, Mexico, Singapore, Russia and the United Arab Emirates. Compliance issues in countries other than those listed are handled in Germany by the Group Compliance Officer.
Employees are instructed to inform their supervisors, the compliance officers, the employee council or their designated HR contacts of any violations they notice. In 2014, Compliance Management consulted with the international sites to ensure that globally applicable measures comply with local requirements. Emphasis was also placed on preventing cybercrime. Accordingly, employees in at-risk areas such as accounting and finance were informed about effective strategies against cyber attacks.
Workplace and Plant Safety – Global Focus on Machinery Safety
Managing plants and processes in a way that poses no risk to people or the environment is an important objective at WACKER. We therefore operate a groupwide safety management system that covers both workplace safety and plant safety. We will align our processes and workplace safety standards with the international OHSAS 18001 standard by 2015.
Systematic workplace safety includes the regular evaluation of hazards and work-area monitoring. The first step in ensuring plant safety is to identify the risks systematically and then assess them. This includes analyzing how well we control the energy (e.g. pressure, heat) present in a process and determining what influence an individual error might have on a chain of events that could lead to the escape of a substance or to an accident. On completion of this comprehensive analysis, we specify safety measures to prevent undesirable incidents.
In 2013, we had placed the focus of the ANSIKO project for machinery safety on the German production sites. In 2014, we inspected machinery at all our international sites, identifying equipment that poses a risk of injury. We then critically reviewed this machinery to make it even safer for employees.
WACKER attaches particular importance to providing its safety experts with ongoing training. We hold regular training sessions, for example, on plant safety and explosion damage protection. In Adrian (USA) and Zhangjiagang (China), we trained our specialists on machinery safety, in particular, during the year under review. We also conducted safety assessments of our sites in Ulsan (South Korea), Nanjing and Zhangjiagang (China), and Kolkata (India).
Our goal for occupational safety is to reduce our groupwide accident rate (the number of workplace accidents per million hours worked) to below 2.0 in 2015. Working toward this overall goal, we set an interim target for 2014 of bringing the number of workplace accidents per million hours worked to below 3.0 at our German sites. This target was almost achieved: we had 3.3 workplace accidents with missed workdays per 1 million hours worked in Germany in the reporting year. The groupwide rate was 2.8, 26 percent lower than the previous year (2013: 3.8 accidents). In terms of reportable accidents (accidents with more than three days of absence), WACKER’s numbers are far better than the German chemical industry average. The reportable accident rate in 2014 was 1.2 per 1 million hours worked (2013: 1.4), whereas in 2013, Germany’s BG RCI (the statutory employer liability insurance carrier of the basic materials and chemical industries) registered 9.3 reportable accidents per 1 million hours worked in chemical companies.
Very few of the accidents at our sites are chemical in nature. The most common causes are tripping, slipping, falling, and inattentiveness during manual activities. Not satisfied with our accident rate, we are stepping up our occupational-safety efforts. We are systematically implementing our new WACKER Safety Plus (WSP) program, which incorporates successful safety elements from sites with particularly low accident rates. Such elements include safety patrols, discussions with the workforce and emergency drills. The goal of WACKER Safety Plus is to recognize and avoid unsafe behavior – on the way to and from work, in the office, at the plant, when operating machinery, or when handling chemicals.
At its German sites, WACKER placed particular emphasis in 2014 on reviewing and updating hazard assessments. As a consequence, we improved protective concepts and safety measures in many areas. The program will be continued at all German sites until 2016.
Workplace Accidents Involving Permanent Staff and Temporary Workers
Download XLS |
|
|
|
||||||||||||||||
Number |
2014 |
2013 |
2012 |
2011 |
2010 |
2009 |
2008 |
|||||||||||
|
|
|
|
|
|
|
|
|||||||||||
|
||||||||||||||||||
Accident rate for Group employees: accidents1 per 1 million hours worked |
2.8 |
3.8 |
4.7 |
3.9 |
4.3 |
4.0 |
3.7 |
|||||||||||
Accident rate for Group employees: reportable accidents2 per 1 million hours worked |
1.2 |
1.4 |
2.1 |
1.4 |
1.2 |
1.2 |
1.0 |
|||||||||||
|
|
|
|
|
|
|
|
Minor Deficiencies in Hazardous Goods Transportation
WACKER ensures that its products are transported and stored safely worldwide. Before loading vehicles, we carry out stringent checks on them, especially if they are carrying hazardous goods. In 2014, nearly 7,800 trucks were inspected on our behalf. If a vehicle fails an inspection, we continue sending it back until it passes. Failure rates have been low for years now. The 2014 failure rate for shipments of hazardous goods in Germany dropped further to 0.3 percent (2013: 1.2 percent). WACKER normally audits hazardous-goods shippers every two years.
We rely on well-trained personnel for transport safety. In 2014, we instructed some 1,200 employees in Germany alone in classroom seminars on how to transport hazardous goods safely. Another 1,000 employees completed an online training program focused mainly on securing freight. At our international production sites, comparable training courses are in place.
We regularly review aspects of transport safety with our logistics providers, e.g. during the annual Logistics Day. If deficiencies are found, we agree on improvements and then follow up on their implementation. WACKER uses in-house criteria and internationally recognized systems, such as the Safety and Quality Assessment System (SQAS) operated by the European Chemical Industry Council (Cefic), to select logistics service providers and evaluate their performance. Our evaluation criteria include drivers’ qualifications and training, vehicle equipment and accident response. Through the use of standards and specifications, WACKER ensures that even the subcontractors working for our logistics providers meet our stringent safety requirements.
In 2014, we recorded 8 transport incidents (2013: 8). This number includes not only accidents involving the distribution of our intermediates and products where we commissioned the transport, but also incidents not involving hazardous goods, whether or not they adversely impact people or the environment. These incidents, too, form part of our shipper assessments.
For products with elevated hazard potential, we use packaging and tanks that meet the highest quality standards, which in some cases go beyond legal requirements. Wherever possible, we evaluate the routing of planned road shipments.
Transport Accidents
Download XLS |
|
|
|
||||||||||||
Number of Accidents |
2014 |
2013 |
2012 |
2011 |
2010 |
2009 |
2008 |
|||||||
|
|
|
|
|
|
|
|
|||||||
Road |
5 |
4 |
8 |
6 |
4 |
5 |
11 |
|||||||
Rail |
2 |
1 |
2 |
1 |
1 |
– |
4 |
|||||||
Sea |
1 |
2 |
– |
1 |
– |
– |
2 |
|||||||
Inland waterways |
– |
1 |
– |
– |
– |
– |
– |
|||||||
Air |
– |
– |
– |
– |
– |
– |
– |
|||||||
|
|
|
|
|
|
|
|
Social Responsibility: Supporting Science Education and Social Projects
To be commercially successful, businesses must also have society’s trust, which is why we take our social responsibilities seriously, especially in communities near our sites. The scientific and technical education of young people is important to us, as we will need committed chemists, engineers and laboratory assistants in the future if we are to remain competitive.
2014 was the ninth time that we had taken the helm as statewide sponsor and organizer of the “Young Scientists” competition in Bavaria. We also once again sponsored the Dresden/East Saxony regional heat of “Young Scientists.”
We attach particular importance to projects that help children and young people. Since 2007, WACKER has supported “Die Arche” (The Ark), a Christian charity that aids children and adolescents from socially disadvantaged families in several German cities. In the reporting year, WACKER presented its eighth annual donation of € 100,000 to the charity’s Munich branch. The government of Upper Bavaria presented WACKER with its honorary award for outstanding integration work, recognizing the company’s sustained support of the charity.
WACKER’s own Burghausen Vocational Training Center (BBiW) accommodated eight unaccompanied adolescent refugees from West and Central Africa in its guest house. The young refugees are taking intensive German lessons to help them in their new life in Germany. They are also taking an integration class at the Mühldorf vocational school with the goal of obtaining the necessary educational qualification for a vocational-training place.
Sites Participate in Open House Day
WACKER participated in the Open House Day organized by the VCI (German Chemical Industry Association) in 2014. On September 20, some 27,000 employees, family members, neighbors and other guests took the opportunity to go behind the scenes at WACKER’s sites in Burghausen, Freiberg, Cologne and Nünchritz – and join in the company’s centennial celebrations.
The VCI honored three companies nationwide for outstanding site communications projects. WACKER’s Burghausen site took second place with its “Get to Know and Trust WACKER” project. The site runs a systematic communications program that reaches out to neighbors, regional political bodies and non-governmental organizations.
Environmental Protection
All WACKER’s processes focus on the need to protect the environment and to manufacture products safely. We attach particular importance to integrated environmental protection, which commences with product development and plant planning. In accordance with the core ideas of the Responsible Care® initiative, our environmental protection measures often go beyond what is legally required. In 2014, WACKER invested € 5.1 million in environmental protection (2013: € 5.4 million). In the same period, environmental operating costs amounted to € 88.2 million (2013: € 89.4 million). WACKER continuously works on improving its production processes to conserve resources. One of our main tasks is to close material loops and recycle byproducts from other areas back into production, enabling us to reduce or prevent emissions and waste.
Since 2011, our key environmental indicators have included our silicon-metal plant in Holla (Norway), acquired in 2010. The environmental impact of metallurgical production there differs greatly from that of WACKER’s typical chemical operations. Airborne emissions, in particular, have risen as a result of the acquisition. 2014 was the first year when the accounting of key environmental indicators included consolidated reporting on 300 mm wafer production in Singapore.
In 2013, we had optimized the Burghausen site’s gas turbine during a scheduled shutdown. In 2014, the longer availability of this facility – and increased electricity production at the Burghausen power plant – resulted in higher direct emissions of carbon dioxide. At Nünchritz, we improved steam-generation processes within the integrated production system, thereby reducing direct emissions of carbon dioxide. Total direct carbon-dioxide emissions in 2014 were at the prior-year level. As for total emissions of non-methane volatile organic compounds (NMVOCs), we amended our accounting methodology in 2014. The prior-year data were adjusted to reflect the new methodology. The rise of the figures during 2014 was due to production increases. Higher production volumes raised Burghausen’s demand for cooling water, which climbed back up to the 2012 level. Groupwide, emissions to wastewater (chemical oxygen demand – COD) fell. Optimized wastewater treatment at the Nünchritz site reduced the COD load. The Group’s total waste volume rose slightly. The increase stemmed from various factors, including consolidated reporting of the Singapore site and the expansion of the Calvert City site, where considerable amounts of rubble had been produced.
In 2014, our indirect CO2 emissions from procured energy (pursuant to Greenhouse Gas Protocol Scope 2) rose to 1,420 kt (2013: 1,241 kt). This was due to increased production volumes, particularly of polysilicon at the Burghausen and Nünchritz sites. We used energy-efficiency measures to reduce weighted specific energy consumption and the associated specific CO2 emissions – while maintaining a comparable product portfolio.
The Group’s carbon footprint is an important tool for improving climate protection. Having determined our indirect greenhouse gas emissions from procured energy (pursuant to Greenhouse Gas Protocol Scope 2) for the first time in 2011, we have also been measuring our Scope 3 emissions since 2012. These include all emissions generated along the supply chain, e.g. by suppliers or through waste disposal and the transport of products. In 2014, we once again forwarded these emissions data to the Carbon Disclosure Project (CDP), which WACKER joined in 2007. Founded in London in 2000, CDP is a not-for-profit organization working to achieve greater transparency in greenhouse gas emissions.
In 2014, WACKER was listed for the first time in the Carbon Disclosure Leadership Index (CDLI) for the German-speaking region (Germany, Austria, Switzerland and South Tyrol) having achieved a score of 95 B. We thus outperformed our peer group in the MDAX in this respect. Following our score of 86 B in 2013, we defined our CO2 reduction target and elaborated our reporting on opportunities and risks and on indirect emissions generated along the supply chain (Scope 3).
Since the fall of 2013, we have been participants in the “myccf” project of co2ncept plus – a German association of businesses with interests in emissions trading and climate protection issues. In this project, which is supported by the German Federal Environmental Foundation (DBU), we are further developing our corporate carbon footprint (CCF). We want to expand our reporting on indirect emissions generated along the supply chain (Scope 3).
Environmental Indicators from 2008 to 2014
Download XLS |
|
|
|
||||||||||||||||||
|
2014 |
2013 |
2012 |
2011 |
2010 |
2009 |
2008 |
|||||||||||||
|
|
|
|
|
|
|
|
|||||||||||||
|
||||||||||||||||||||
Air |
|
|
|
|
|
|
|
|||||||||||||
CO2 emissions1 |
|
|
|
|
|
|
|
|||||||||||||
Direct (kt) |
1,249 |
1,251 |
1,311 |
1,341 |
986 |
969 |
976 |
|||||||||||||
Indirect (kt) |
1,420 |
1,241 |
1,133 |
1,075 |
– |
– |
– |
|||||||||||||
NOX nitrogen oxides (t)2 |
1,960 |
2,010 |
2,225 |
2,221 |
926 |
963 |
997 |
|||||||||||||
Non-methane volatile organic compounds (NMVOCs) (t)3 |
830 |
750 |
720 |
670 |
620 |
530 |
560 |
|||||||||||||
|
|
|
|
|
|
|
|
|||||||||||||
Water |
|
|
|
|
|
|
|
|||||||||||||
Water consumption (thousand m3) |
241,973 |
220,908 |
242,072 |
268,657 |
252,151 |
264,532 |
241,286 |
|||||||||||||
Chemical oxygen demand (COD) (t) |
1,230 |
1,320 |
1,460 |
1,680 |
1,820 |
2,730 |
4,782 |
|||||||||||||
Halogenated organic hydrocarbons (AOX) (t) |
2 |
2 |
3 |
5 |
6 |
6 |
7 |
|||||||||||||
|
|
|
|
|
|
|
|
|||||||||||||
Waste |
|
|
|
|
|
|
|
|||||||||||||
Disposed of (t) |
49,260 |
31,560 |
39,920 |
47,410 |
48,520 |
80,860 |
87,293 |
|||||||||||||
Recycled (t) |
108,940 |
110,500 |
96,880 |
80,290 |
77,030 |
63,430 |
74,327 |
|||||||||||||
Hazardous (t) |
75,630 |
73,380 |
73,620 |
68,230 |
69,320 |
100,860 |
108,458 |
|||||||||||||
Non-hazardous (t) |
82,570 |
68,680 |
63,180 |
59,470 |
56,230 |
43,430 |
53,161 |
|||||||||||||
|
|
|
|
|
|
|
|
|||||||||||||
Energy |
|
|
|
|
|
|
|
|||||||||||||
Electricity consumption (GWh) |
4,927 |
4,526 |
4,559 |
4,372 |
3,759 |
2,702 |
2,405 |
|||||||||||||
Primary energy consumption Natural gas (GWh) |
4,978 |
5,051 |
5,927 |
5,771 |
5,463 |
5,378 |
5,372 |
|||||||||||||
Solid fuels (coal, charcoal, wood) (GWh) |
839 |
872 |
862 |
886 |
432 |
– |
– |
|||||||||||||
Heat supplied by third parties (steam and district heating) (GWh) |
244 |
236 |
223 |
218 |
228 |
209 |
195 |
|||||||||||||
Heating oil (GWh) |
20 |
17 |
18 |
16 |
13 |
8 |
9 |
|||||||||||||
|
|
|
|
|
|
|
|
Water Consumption Tested Using the Global Water Tool©
In many parts of the world, clean water is particularly scarce, and obtaining and purifying water is very expensive. As a global player, we take such conditions into account in our production processes and during transport. We use the Global Water Tool© (GWT) developed by the World Business Council for Sustainable Development (WBCSD) to analyze the annual relative water stress index of the countries where our main global production sites are located.
This analysis was conducted for the first time in 2012, based on analyses using the water stress index developed by the Water Systems Analysis Group of the University of New Hampshire, USA. This index provides information on the relationship between water consumption and the availability of renewable fresh water. The outcome of the analysis is that our most important production sites are located in regions with a low relative water stress index. These regions account for more than 97 percent of our annual water use and over 90 percent of our production volume. Production sites in countries for which no GWT-based water stress index information is available account for less than 0.5 percent of our water consumption.
A special Employee Suggestion Program initiative entitled “Save Wastewater and Make a Profit” was launched at the Nünchritz site in December 2014. The purpose of the initiative is to encourage employees to develop ideas for conserving and recycling water in production. The campaign runs through June 30, 2015. In 2014, a similar campaign took place at the Burghausen site: employees there made 72 improvement suggestions, nine of which have been implemented to date in areas such as wastewater treatment.
Product Stewardship
WACKER takes criteria for environmental and health protection as well as for safety into account at every stage of the product lifecycle. In research and development projects, we examine the sustainability aspects of our new products and processes, starting with the raw materials used. We try to minimize raw-material consumption while selecting materials that offer maximum ecological benefit.
Our products are generally supplied to business customers for further processing – not directly to end customers. Our lifecycle assessments (LCAs) look at the environmental impact caused by a specific product family throughout its lifecycle – a “cradle-to-gate” assessment extending from manufacturing to the factory gate. They allow us to gage the sustainability of our products and production processes, and to improve them accordingly.
Product Lifecycles
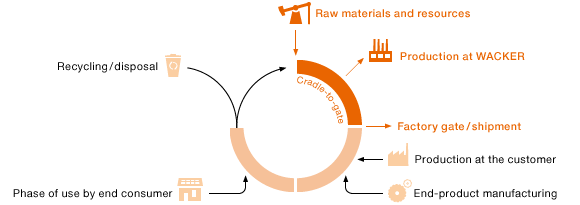
Since 2012, we have been using the WACKER® Eco Assessment Tool to systematically evaluate the opportunities and risks of our product line from an environmental perspective. The tool factors in the material, water and energy consumption of a product, as well as its ecotoxicity, over the entire lifecycle.
Energy Management
The chemical industry is one of the most energy-intensive sectors. In Germany alone, it uses around 20 percent of all the electricity consumed by industry. That is why WACKER, too, is continually improving the energy efficiency of its processes. This enables us to remain globally competitive and to support climate protection. Many chemical reactions generate heat that can be put to use in other production processes. We have been using integrated heat-recovery systems in Burghausen and Nünchritz for years and are continually improving them. In this way, we can reduce the amount of primary energy (as a rule, natural gas) that our power plants consume.
To enhance energy efficiency and reduce specific energy consumption (amount of energy per unit of net production output), the Executive Board has defined energy targets for WACKER Germany. The goal is to reduce weighted specific energy consumption by a third between 2007 and 2022.
Our energy goals ensure that we meet one of the requirements of the energy management system as per ISO 50001, which we have introduced and certified at all sites of Wacker Chemie AG, Siltronic AG and Alzwerke GmbH in Germany. We are thus already in full compliance with the legal obligation to have an energy management system in place by 2015.
In 2014, Wacker Chemie AG received the Bavarian state government’s Energy Award, which was conferred in recognition of the Group’s highly efficient polysilicon manufacturing operations. Thanks to patented technology advancements and process optimizations, we lowered our specific energy consumption for polysilicon production by 29 percent. Hyperpure polysilicon is the main raw material for making solar modules and, consequently, plays a vital role in generating solar power. The Bavarian Energy Award is conferred every two years for outstanding innovations in responsible energy management.
Generating Energy Efficiently
Burghausen uses hydroelectric power to generate electricity. Our Norwegian site, Holla, also generates its electricity mainly from water power. Our primary source of energy, though, is climate-friendly natural gas. At WACKER’s large Burghausen and Nünchritz sites, we produce steam and electricity in cogeneration systems. These combined heat and power (CHP) plants have more than 80-percent fuel efficiency, which is significantly higher than that of conventional plants, where electricity and heat are generated separately.
Electricity Supply
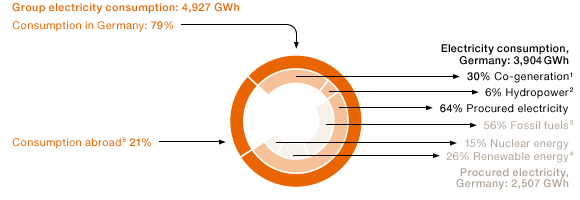
1 Burghausen and Nünchritz
2 Burghausen
3 Coal, lignite, oil, gas; modified calculation method: since 2014, data in line with Germany’s energy mix; source: BDEW (German Association of Energy and Water Industries)
4 Hydro, wind, solar power; modified calculation method: since 2014, data in line with Germany’s energy mix; source: BDEW (German Association of Energy and Water Industries)
5 Outside Germany, we purchase electricity from third parties based on the local standard energy mix
In 2014, absolute electricity consumption rose slightly to 4,927 GWh (2013: 4,526 GWh) although specific energy consumption was lowered by energy-efficiency measures. The rise stemmed from the high level of polysilicon-plant utilization throughout the year. The Group’s power plants – the hydroelectric and CHP (gas and steam turbine) generating stations in Burghausen and the CHP in Nünchritz – produced around 1,405 GWh in 2014 (2013: 1,457 GWh). This means that WACKER covered about 30 percent of its total electricity needs itself. Groupwide, carbon dioxide emissions from captive power plants subject to emissions trading rules and from silicon-metal production in Holla (Norway) totaled about 1.1 million metric tons in the reporting period (2013: 1.2 million metric tons).
WACKER’s German production sites accounted for 79 percent (2013: 78 percent) of its total electricity needs. In Germany, we purchased enough electricity from utilities to cover 64 percent (2013: 59 percent) of our electricity requirements there. In line with the German energy mix, 56 percent of this electricity was generated from fossil fuels (2013: 51 percent). 15 percent came from nuclear energy (2013: 18 percent) and 26 percent from renewable energy sources (2013: 31 percent). Heat consumption, which includes the use of solid carbon-based and biogenic fuels (coal, charcoal, wood) for silicon-metal production at Holla (Norway), fell marginally across the Group to 3,572 GWh (2013: 3,724 GWh). We have modified our calculation method for the electricity-generation mix: since 2014, our data are based on Germany’s energy mix as published by the BDEW.
Energy Consumption
Download XLS |
|
|
|
||||||||||||||||
GWh |
2014 |
2013 |
2012 |
2011 |
2010 |
2009 |
2008 |
|||||||||||
|
|
|
|
|
|
|
|
|||||||||||
|
||||||||||||||||||
Electricity consumption |
4,927 |
4,526 |
4,559 |
4,372 |
3,759 |
2,702 |
2,405 |
|||||||||||
Heat consumption1 |
3,572 |
3,724 |
3,755 |
3,862 |
3,374 |
2,794 |
2,782 |
|||||||||||
|
|
|
|
|
|
|
|
|||||||||||
Primary energy |
|
|
|
|
|
|
|
|||||||||||
Natural gas |
4,978 |
5,051 |
5,927 |
5,771 |
5,463 |
5,378 |
5,372 |
|||||||||||
Solid fuels2 (coal, charcoal, wood) |
839 |
872 |
862 |
886 |
432 |
– |
– |
|||||||||||
Heat supplied by third parties (steam and district heating) |
244 |
236 |
223 |
218 |
228 |
209 |
195 |
|||||||||||
Fuel oil |
20 |
17 |
18 |
16 |
13 |
8 |
9 |
|||||||||||
|
|
|
|
|
|
|
|