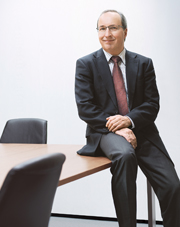
Product Innovation
Karl Kiermaier, facility manager at the WACKER site in Burghausen, has never bothered to count the many first-aid kits and safety glasses distributed around the site. They probably number in their thousands. As the company’s main production site grows, he and his colleagues have to continually anchor more and more plastic boxes to the wall – to hold safety glasses or gauze bandages. This can be troublesome – especially where a wall forms part of an explosion zone harboring, say, flammable solvents. Clearly, an electric drill is out of the question for safety reasons. Now, though, Kiermaier’s job has been made quite a bit easier thanks to a recent invention by Corporate R&D. Whenever he leaves his workshop these days, instead of his drill, he simply takes a tube of adhesive along: GENIOSIL® N70-HT. The HT stands for high tack. For Kiermaier that means “just press firmly in place for an instant bond.”
Innovation Award for a High Performance Adhesive
Banal though that might sound, it represents a crucial leap forward for modern industries and applications. Adhesives are a great way of joining things together. They eliminate the need for drilling holes, or inserting screws and rivets. Nor must the material be heated, as in the case of welding. Adhesives are unobtrusive and easy to use. Modern automobiles contain the equivalent of a 100-meters of adhesive seams, and shipbuilders and aircraft makers, too, are employing them more and more. Whatever the application, the adhesives and sealants must be easy to use, fast curing and ecologically sound.
GENIOSIL® Hybrid Polymers Are the Basis of Completely New Product Innovations.
GENIOSIL® high-performance adhesives fit the bill exactly, which is why, last September in London, WACKER chemist Dr. Rudolf Hager was presented with the New Product Innovation Award by the management consultant Frost & Sullivan. Hager heads the key Group project which forms the basis for the new product range and goes by the somewhat cumbersome name of “Silane-Curing Organic Polymers.” For him, the award is a milestone, “because it shows that market experts and analysts, too, are excited about our technology.”
Market experts? Analysts? Surely a chemist should be more interested in garnering praise from his peers and boosting his scientific status. Hager, though, prefers to seek out new solutions for new markets. Take adhesives, for example. Two thirds of the 1.7 million metric tons of adhesives consumed annually contain either silicone or polyurethane. The new hybrid adhesives combine the advantages of both. “We’re not re-inventing adhesive bonding, but making it easier to find new solutions,” explains Hager. And floorers could hardly fail to be delighted with a wood floor adhesive that does not take days to cure, is elastic, does not present a health or environmental risk and is still easy to use. In these new GENIOSIL® hybrid polymers, WACKER is supplying adhesives manufacturers with the component for an adhesive that is both technically and ecologically optimum.
2,000 metric tons of hybrid polymers are currently in production in Burghausen. It may still be a niche business for WACKER, but it is growing fast. The new polymers will not just wind up as binders in wood floor adhesives. They make prime candidates for all bonding, sealing, coating and foaming tasks. They can be used to customize a wide variety of products to specific tasks: such as all-round assembly adhesives, isocyanate-free construction foams, flexible sealing membranes and scratchproof top coats for the automotive industry.
Developing the hybrid polymers took ten years of intensive research. Yet, it was clear to the basic research scientists in the Consortium from the outset that they had to focus on the intended application. The objective was ambitious: the researchers wanted to create a wholly new class of product combining the advantages of organic polymers with those of silicones. The small team was left alone to focus exclusively on this topic.
Methodically Improving the Success of Innovations
So, it is no coincidence that a successful product is now on the market. WACKER’s strategy of innovation ensures that research is focused on market needs. To appreciate how revolutionary this approach is, it is necessary to delve a little into the history of the German chemical industry. It has always involved a lot of experimentation. But all too often, after years in the laboratory, the basic researchers came up with some wondrous inventions that were not really needed in the outside world. In recent years, WACKER has managed to systematically increase the success of its innovations. With global competition intensifying and production cycles becoming ever shorter, there is no such thing now as a business that is not innovation driven. Hybrid polymers are evidence that a Group like WACKER is not an immovable colossus. WACKER is the only company in the world with industrial-scale production capability for highly reactive alpha-silanes, the precursors for the new polymers.
WACKER is a leading producer of silicones and polymers. Drawing on their expertise in these two areas, its researchers have now created a totally new product class.
Back in 2001, the laboratory researchers expended tremendous time and effort on synthesizing the first few milliliters of these specialty silanes. “The amount we made wouldn’t have filled my coffee mug,” recalls Hager. At that time, nobody had a clue about how to set about producing large quantities. Alpha-silanes posed a challenge to all, because they are roughly one-hundred times as reactive as conventional silanes. “This reactivity is a huge advantage, but you must be able to control it,” explains Hager. The technical service managers and engineers had to draw on their experience and creativity to develop the production facilities in Burghausen; as a result, many processes in the complex production method are unique.
Versatile Hybrid Polymers
The first batches of the hybrid polymers to emerge from the pilot plant in 2005 were destined for established markets, primarily the construction industry. However, because the hybrid polymers are so versatile, new solutions are continually being devised in the laboratories in Burghausen. Trials are underway, for example, to seal damp walls with a membrane of hybrid polymers. The chemists are also working on a waterproof wood glue that meets the most stringent of the relevant standards, DIN D4. So far, only adhesives made from polyurethanes meet this standard, “but we’re close to achieving it without polyurethane,” says Hager.
Soon, innovative solutions for new, lucrative application areas will become available. WACKER sees itself as a provider of products for innovative solutions, which it creates by working closely together with customers . The rotor blades of wind turbines, for example, are growing larger and larger and must withstand enormous forces. Here, WACKER is developing the optimum adhesive for this purpose. For the automotive industry, WACKER is formulating new adhesives that will increase the economics of carbon fiber processing. And facility manager Karl Kiermaier might never need to use anchors and screws ever again.
Characteristics
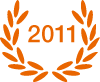
New Product Innovation Award
WACKER was awarded the New Product Innovation Award in 2011 by the management consultant Frost & Sullivan for its GENIOSIL® product class in the construction field.
1.7m Tonsof sealants and elastic adhesives are consumed per year. Two thirds of these are based on silicone or polyurethane. The new hybrid adhesives combine the advantages of both. |
Chemical formula for an alpha-silane![]() |
Everyday Applications of Silane-Crosslinking Hybrids
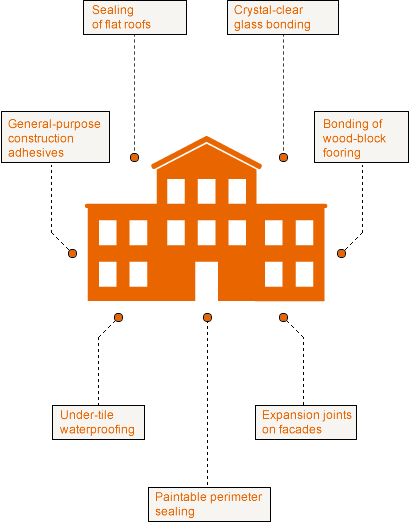
Reactive, moisture-curing adhesives and sealants have been an integral part of construction for decades. Silicones and polyurethanes are the best known, with hybrids increasing in popularity, too.
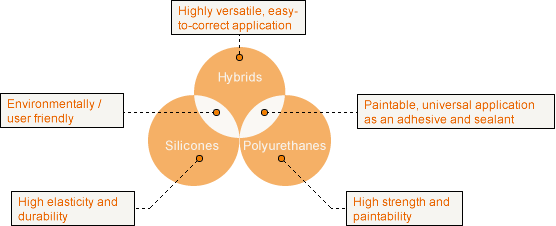