Managing Sustainability
Companies can only be profitable in the long term if they take their responsibility toward the environment and society seriously. That is why sustainability has been firmly rooted in our business processes for many years.
Our sustainability activities are underpinned by two global initiatives: Responsible Care® (the chemical-industry initiative) and the UN’s Global Compact. Through this voluntary commitment, WACKER undertakes to protect the environment, employees and society above and beyond legal requirements. We also expect our suppliers to respect the principles of the Global Compact.
New Vision and Goals Fully Integrated in the Group
We redefined our vision and goals at the beginning of 2012. This repositioning will enhance WACKER’s profile and establish a common set of values for the entire Group. During the year, our executives began introducing the vision and goals at moderated group discussions throughout the company.
Our Vision | ||||||||
| ||||||||
Vision | ||||||||
|
|
|
|
|
|
|
|
|
Customers |
|
Employees |
|
Innovations |
|
Company Value |
|
Sustainability |
|
|
|
|
|
|
|
|
|
Code of |
|
Code of |
|
Code of |
|
Code of Teamwork |
|
Code of |
| ||||||||
Regulations | ||||||||
| ||||||||
Directives |
Aside from our vision and goals, we have revised our business principles, which represent the third pillar of our corporate policy guidelines. These principles – laid down in five corporate codes – govern how the Group should achieve its objectives. The five codes are the Code of Safety, the Code of Conduct, the Code of Innovation, the Code of Teamwork & Leadership, and the Code of Sustainability. The codes are supplemented by a body of regulations and directives.
Energy Management Certified to ISO 50001
We control operational processes via our integrated management system (IMS). The system regulates workflows and responsibilities, and defines groupwide standards for quality, the environment, and health and safety. In the future, we intend to use the IMS to control additional sustainability-related activities more closely, for instance the effective use of resources such as energy in our production processes. We have our Group management system analyzed by an international certification organization in accordance with uniform standards based on ISO 9001 (quality) and ISO 14001 (environment). At Siltronic, every site is certified to ISO/TS 16949, to ISO 14001 and to OHSAS 18001 (occupational safety), due to this subsidiary’s specific processes and customer requirements.
Substantial progress was made on strategic sustainability-management projects in 2012:
- Group Certificate:
Our maintenance of the Group certificate ensures that customer-driven specifications and our corporate standards are implemented at all WACKER sites. In 2012, we expanded our Group certification to include our Norwegian site in Holla (certified to ISO 9001 and ISO 14001) and our sales regions (certified to ISO 9001). Almost all our production sites are now included in the Group certificate. Not yet included are the sites in Brazil and India, as well as Jincheon (South Korea), which have corresponding individual certificates, though. - Energy Management:
2012 saw WACKER acquire its first-ever certificate under the energy-management standard ISO 50001, covering its sites in Germany. Maintaining the certificate will stimulate further reductions in our energy consumption and costs. - Occupational Health and Safety Management:
In the years ahead, we intend to add another international standard – OHSAS 18001 – to our Group certification. OHSAS regulates occupational health and safety management processes and standards. Our Siltronic subsidiary and our site in Jincheon (South Korea) have an OHSAS certificate. - Greenhouse Gas Emissions:
Having conducted the first survey of our indirect greenhouse gas emissions from bought-in energy (as per Greenhouse Gas Protocol Scope 2) in 2011, the next phase, begun in the year under review, was to measure our Scope 3 emissions. These include all emissions generated along the supply chain, e.g. by suppliers or through waste disposal and the transportation of products. The Group’scarbon footprint is an important tool for improving climate protection. - Lifecycle Assessments:
We have developed an analytical tool that enables us to estimate, already in the R&D phase, the environmental impact of new products. Launched in 2012, the environmental analysis performed with the Eco Assessment Tool is gradually being established within the Group. This analysis allows us to assess and improve the sustainability of our products. - Sustainability Platform:
We are in the process of standardizing our various IT systems for groupwide sustainability reporting. Standardization includes not only the management of environmental metrics, energy data, and environmentally relevant and safety-related events, but also audit planning and follow-up measures within the integrated management system. In 2012, we defined software requirements and began implementing them.
Safety Goals now Part of Performance Target Agreements
Workplace and plant safety are of vital importance at WACKER. This is why, in 2012, we included safety goals in the annual performance reviews for Executive Personnel and management employees in Germany. As personal goals, their achievement is mandatory, especially for executives with responsibilities involving hazardous situations. They also influence the final performance evaluation.
Compliance Officers Available Worldwide
WACKER’s ethical principles of corporate management exceed legal requirements. Employees can direct their questions to 22 compliance officers worldwide. Alongside the existing officers in Germany, the USA, China, Japan, India, South Korea, Brazil and Singapore, additional compliance officers were appointed and trained in Mexico, Taiwan and the United Arab Emirates during 2012.
Employees are instructed to inform their supervisors, the compliance officers, the employee council or their designated HR contacts of any violations they notice. In 2012, Compliance Management focused on devising and implementing globally applicable measures (in response to the UK Bribery Act 2010, for example) in consultation with international sites to ensure compliance with local requirements.
Environmental Protection
All WACKER’s processes focus on the need to protect the environment and to manufacture products safely. We attach particular importance to integrated environmental protection. This commences with product development and plant planning. In 2012, WACKER spent €8.6 million on environmental investments (2011: €7.9 million). Environmental operating costs amounted to €79.3 million (2011: €73.3 million).
In the course of setting up the polysilicon facilities at our Nünchritz site, we expanded the wastewater treatment plants as well. We have been using a hydraulic groundwater remediation process since 2012. The process involves pumping the groundwater into a treatment system, and returning it to the ground after purification. By the end of 2012, we had cleaned a total of 65,000 cubic meters of groundwater there.
Since fiscal 2011, our environmental indicators include our silicon-metal plant in Holla (Norway), acquired in 2010. The environmental impact of metallurgical production there differs greatly from that of WACKER’s typical chemical operations. The environmental indicators, particularly regarding airborne emissions, have risen as a result of the acquisition. In the case of wastewater, chemical oxygen demand (COD) and halogenated organic compounds (AOX) were both down because we closed the Burghausen acetaldehyde plant in 2012. Disposable waste has been reduced, since the filter cake from wastewater treatment in Burghausen is now being recycled instead of disposed of as before.
WACKER continuously strives to close its material loops and recycle byproducts from other areas back to production and thus to prevent or reduce waste. We have only some benchmark figures on how the chemical industry recycles or disposes of hazardous chemical waste because of the industry’s product-mix variations and unique site infrastructures.
Download XLS |
Emissions into the Air: Business Divisions/Metallurgy | ||||||||||||||||||||
|
|
|
|
|
|
| ||||||||||||||
|
2012 |
2011 |
2012 |
2011 |
2012 |
2011 | ||||||||||||||
| ||||||||||||||||||||
|
|
|
|
|
|
| ||||||||||||||
Air |
|
|
|
|
|
| ||||||||||||||
CO2 emissions (t) |
1,294,000 |
1,341,0003 |
983,200 |
1,020,0003 |
310,800 |
321,000 | ||||||||||||||
Nitrogen oxides (NOX) (t) |
2,225 |
2,221 |
1,072 |
1,052 |
1,153 |
1,169 | ||||||||||||||
Non-methane volatile organic compounds (NMVOCs) (t) |
418 |
396 |
411 |
389 |
7 |
7 |
Our indirect greenhouse gas emissions from procured energy (as per Greenhouse Gas Protocol Scope 2) rose by 5.9 percent in 2012. The main reason is production-capacity expansion for polysilicon via commissioning of new facilities at the Nünchritz site.
Download XLS |
Environmental Indicators 2006–20121 | ||||||||||||||||||||||||||||||||||||
|
|
|
|
|
|
|
| |||||||||||||||||||||||||||||
|
2012 |
2011 |
2010 |
2009 |
2008 |
2007 |
2006 | |||||||||||||||||||||||||||||
| ||||||||||||||||||||||||||||||||||||
|
|
|
|
|
|
|
| |||||||||||||||||||||||||||||
Air |
|
|
|
|
|
|
| |||||||||||||||||||||||||||||
CO2 emissions2 (t) |
1,294,000 |
1,341,000 |
986,000 |
969,000 |
976,041 |
912,260 |
941,572 | |||||||||||||||||||||||||||||
NOx nitrogen oxides (t) |
2,225 |
2,221 |
926 |
963 |
997 |
838 |
804 | |||||||||||||||||||||||||||||
Non-methane volatile organic compounds3 (NMVOCs) (t) |
418 |
396 |
415 |
383 |
501 |
687 |
560 | |||||||||||||||||||||||||||||
Greenhouse gases |
|
|
|
|
|
|
| |||||||||||||||||||||||||||||
Direct4 (t CO2) |
1,294,000 |
1,347,000 |
– |
– |
– |
– |
– | |||||||||||||||||||||||||||||
Indirect5 (t CO2) |
1,150,071 |
1,086,192 |
– |
– |
– |
– |
– | |||||||||||||||||||||||||||||
|
|
|
|
|
|
|
| |||||||||||||||||||||||||||||
Water |
|
|
|
|
|
|
| |||||||||||||||||||||||||||||
Water consumption6 |
242,072 |
268,657 |
252,151 |
264,532 |
241,286 |
244,173 |
228,283 | |||||||||||||||||||||||||||||
COD chemical oxygen demand (t) |
1,460 |
1,680 |
1,820 |
2,730 |
4,782 |
2,162 |
1,993 | |||||||||||||||||||||||||||||
AOX halogenated organic hydrocarbons (t) |
3 |
5 |
6 |
6 |
7 |
6 |
5 | |||||||||||||||||||||||||||||
|
|
|
|
|
|
|
| |||||||||||||||||||||||||||||
Waste |
|
|
|
|
|
|
| |||||||||||||||||||||||||||||
Disposed of (t) |
39,920 |
47,410 |
48,520 |
80,860 |
87,293 |
43,100 |
42,250 | |||||||||||||||||||||||||||||
Recycled (t) |
96,880 |
80,290 |
77,030 |
63,430 |
74,327 |
74,676 |
73,774 | |||||||||||||||||||||||||||||
Hazardous7 (t) |
73,620 |
68,230 |
69,320 |
100,860 |
108,458 |
70,027 |
75,263 | |||||||||||||||||||||||||||||
Non-hazardous7 (t) |
63,180 |
59,470 |
56,230 |
43,430 |
53,161 |
47,538 |
41,049 | |||||||||||||||||||||||||||||
|
|
|
|
|
|
|
| |||||||||||||||||||||||||||||
Energy |
|
|
|
|
|
|
| |||||||||||||||||||||||||||||
Electricity consumption (TWh) |
4.6 |
4.4 |
3.8 |
2.7 |
2.4 |
2.1 |
1.9 | |||||||||||||||||||||||||||||
Primary energy8 |
|
|
|
|
|
|
| |||||||||||||||||||||||||||||
Natural gas (TWh) |
5.9 |
5.8 |
5.5 |
5.4 |
5.4 |
– |
– | |||||||||||||||||||||||||||||
Solid fuels9 (coal, charcoal, wood) (TWh) |
0.9 |
0.9 |
0.4 |
– |
– |
– |
– | |||||||||||||||||||||||||||||
Heat (supplied by third parties)10 (TWh) |
0.2 |
0.2 |
0.2 |
0.2 |
0.2 |
– |
– | |||||||||||||||||||||||||||||
Heating oil (TWh) |
0.02 |
0.02 |
0.01 |
0.01 |
0.01 |
– |
– |
Last year, we started measuring further indirect greenhouse-gas emissions, as per the Greenhouse Gas Protocol. These are greenhouse-gas emissions generated along the supply chain – for example, through production and transportation of raw materials or through waste disposal. We have forwarded these data to the Carbon Disclosure Project (CDP), which WACKER joined in 2007. Founded in London in 2000, CDP is a not-for-profit organization working to achieve greater transparency in greenhouse-gas emissions.
Product Stewardship
In 2012, we continued with our lifecycle assessments to determine the “cradle-to-gate” environmental impact of our products. WACKER was a participant in a study published by the European Silicones Center (CES) in 2012. This study comprises the entire product lifecycle of silicones and related products, such as silanes. The study assessed the CO2 emissions caused by producing the silicones compared with the resultant reduction of CO2 achieved by using the silicones. It found that the use of silicones and related products (such as siloxanes and silanes) reduces the carbon footprint of many significant products by a factor of 9. At 54 million metric tons of CO2 a year, this reduction is equivalent to the emissions generated to heat 10 million homes.
We have introduced a tool to evaluate systematically the risks and opportunities of our product line from an environmental perspective. In the Eco Assessment Tool, we take into account not only material, water and energy use, but also ecotoxicity over the entire product lifecycle. We have assessed initial products in this fashion and will expand our analysis.
Product Lifecycles
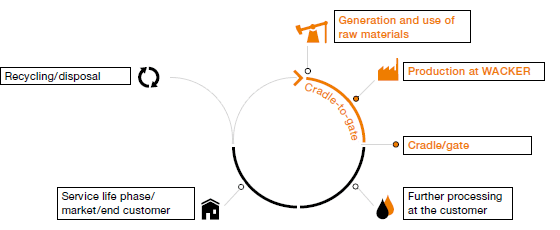
Energy Management
The chemical industry is an extremely energy-intensive sector. WACKER is one of Germany’s major energy consumers. For this reason, globally competitive energy prices are of considerable significance to us. WACKER is constantly improving the energy efficiency of its processes. This enables us to remain globally competitive and to support climate protection. In 2012, we had our energy management system for WACKER Germany certified to the ISO 50001 standard. Since 2007, we have reduced our average specific energy consumption (amount of energy per unit of net production output) by 22 percent, mainly due to our POWER PLUS energy-conservation program.
Hydroelectric power is used at the Burghausen site, while our production facility in Holla, Norway, generates electricity mainly from hydro-power. Our primary source of energy, though, is climate-friendly natural gas. At WACKER’s large Burghausen and Nünchritz sites, we produce steam and electricity in cogeneration systems. Our combined heat and power (CHP) plants have more than 80 percent fuel efficiency, twice that of conventional power-generation plants.
In 2012, WACKER’s electricity consumption rose to 4.6 million MWh (2011: 4.4 million MWh). This was due to higher polysilicon production in 2012. The Group’s power plants – the hydroelectric and CHP (gas and steam turbine) generating stations at Burghausen and the CHP at Nünchritz – produced around 1.6 million MWh in 2012 (2011: 1.5 million MWh). This means that WACKER covered about a third of its total electricity needs itself. Groupwide, CO2 emissions remained at the prior-year level of some 1.3 million metric tons, of which 60 percent resulted from captive power plants that are subject to emissions trading rules.
Electricity Supply
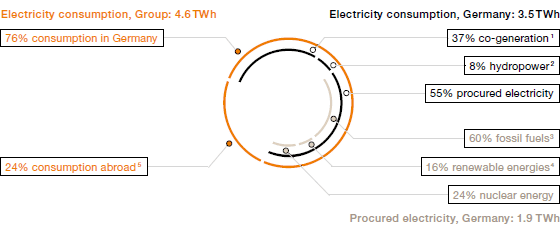
1 Burghausen / Nünchritz
2 Burghausen
3 Coal, lignite, oil, gas
4 Hydro, wind, solar power
5 Outside Germany, we purchase electricity from third parties based on the local standard energy mix.
WACKER’s German production sites account for 76 percent (2011: 73 percent) of its electricity needs. In Germany, we purchased enough electricity from utilities to cover 55 percent (2011: 53 percent) of our electricity requirements there. In line with the utilities’ primary energy sources, 60 percent (2011: 58 percent) of this electricity was generated from fossil fuels. 24 percent (2011: 20 percent) came from nuclear energy, and 16 percent (2011: 22 percent) from renewable energy sources. Heat consumption, which includes the use of solid carbon-based and biogenic fuels (coal, charcoal, wood) in silicon-metal production at Holla (Norway), fell slightly across the Group to 3.8 TWh (2011: 3.9 TWh).
Download XLS |
Energy Consumption | ||||||||||||||||||
|
|
|
|
|
| |||||||||||||
TWh |
2012 |
2011 |
2010 |
2009 |
2008 | |||||||||||||
| ||||||||||||||||||
|
|
|
|
|
| |||||||||||||
Energy consumption |
4.6 |
4.4 |
3.8 |
2.7 |
2.4 | |||||||||||||
Heat consumption1 |
3.8 |
3.9 |
3.4 |
2.8 |
2.8 | |||||||||||||
Primary energy |
|
|
|
|
| |||||||||||||
Natural gas |
5.9 |
5.8 |
5.5 |
5.4 |
5.4 | |||||||||||||
Solid fuels2 (coal, charcoal, wood) |
0.9 |
0.9 |
0.4 |
– |
– | |||||||||||||
Heat (supplied by third parties)3 |
0.2 |
0.2 |
0.2 |
0.2 |
0.2 | |||||||||||||
Heating oil |
0.02 |
0.02 |
0.01 |
0.01 |
0.01 |
Workplace and Plant-Safety Projects
Designing plants and processes in a way that poses no risk to people or the environment is an important objective at WACKER. We consequently make safety management a groupwide undertaking that includes workplace and plant safety.
To ensure the safety of our plants, we ascertain and evaluate risks in a systematic way. We not only analyze how well we control the energy (pressure, heat) existing in a process, but also determine what influence an individual fault might have on a chain of events leading up to a failure or accident. On completion of this comprehensive analysis, we specify safety measures to prevent the occurrence of undesirable incidents.
In the year under review, we initiated a new safety project. Our “ANSIKO 2012/2013” project identifies machinery that poses a risk of injury, reviews safety plans for such machinery critically and, where needed, specifies additional measures to protect employees. The project was launched at the German sites in 2012. The non-German production sites will be included from mid-2013.
The expansion of polysilicon production at Nünchritz involved a corresponding upgrade of the site’s emergency-response procedures. We now have gas detectors to quickly identify releases of hazardous substances, sirens for warning local residents, and signaling to divert traffic from all roads in the vicinity of the plant.
WACKER attaches particular importance to providing ongoing training to its safety experts. We hold regular training sessions, for example, on plant safety and explosion protection. Group experts organize safety training at WACKER sites outside Germany. In 2012, experts from all production sites met to share information and attend training sessions at Burghausen. We formed a committee (the “Expert Committee on Plant and Process Safety”) to organize advanced training in site and process safety issues. We conducted health and safety audits at sites in the USA during the year under review.
Groupwide, there were 4.7 workplace accidents with missed workdays per 1 million hours worked in 2012 (2011: 3.9 accidents). This result puts us behind those chemical companies that lead the way in occupational safety. Bayer, BASF, Dow, Evonik and Henkel collectively had an average of 1.5 workplace accidents with missed workdays per 1 million hours worked in 2011. WACKER’s figures for reportable accidents (accidents with more than three missed workdays) compare much more favorably with the average for the German chemical industry. The reportable accident rate in 2012 was 2.1 per 1 million hours worked, while, in 2011, Germany’s BG RCI (the statutory employer liability insurance carrier of the basic materials and chemical industries) registered 9.5 reportable accidents per 1 million hours worked in chemical companies.
Regrettably, a partner company had one fatal workplace accident during the reporting period. At our Charleston site (Tennessee, USA), two construction workers from a partner company laying concrete were caught by a loose molding and fell to their deaths. After a temporary closure of the building site, we worked with the construction company involved to improve safety precautions.
Most accidents at our sites are not chemical in nature. The most common causes are tripping, slipping and falling or inattentiveness during manual activities. Not satisfied with our accident rate, we will be increasing our occupational-safety efforts. We are systematically implementing our new safety program – WACKER Safety Plus (WSP), which incorporates successful safety elements from sites with particularly low accident rates. Such elements include safety patrols, discussions with the workforce and emergency drills. WACKER Safety Plus has the goal of recognizing and avoiding unsafe behavior – on the way to and from work, in the office, at the plant, when operating machinery, or when handling chemicals. We organized WSP seminars for executives at all of our production sites in 2012.
Download XLS |
Reportable Accidents per 1 Million Hours Worked | ||||||||||||||||||||
|
|
|
|
|
|
|
| |||||||||||||
Number |
2012 |
2011 |
2010 |
2009 |
2008 |
2007 |
2006 | |||||||||||||
| ||||||||||||||||||||
|
|
|
|
|
|
|
| |||||||||||||
Accidents1 involving Group employees |
4.7 |
3.9 |
4.3 |
4.0 |
3.7 |
3.8 |
4.1 | |||||||||||||
Reportable accidents2 involving Group employees |
2.1 |
1.4 |
1.2 |
1.2 |
1.0 |
1.4 |
1.2 |
Stringent Controls for Safe Transportation
WACKER ensures that its products are safely stored and transported. Before loading vehicles, we carry out stringent checks on them. This applies especially to hazardous materials. We inspected in excess of 6,600 trucks in 2012. If a vehicle fails inspection, we continue sending it back until it passes. Failure rates have been low for years now. In 2012, it was 2.2 percent for transporting hazardous goods (2011: 3.6 percent). WACKER audits hazardous goods shippers at least every two years.
We rely on well-trained personnel for transport safety as well. In 2012, we instructed over 1,000 employees throughout the Group in classroom seminars on the transport of hazardous goods. Another 1,500 completed an online training course.
We regularly review aspects of transport safety with our logistics providers, e.g. during the annual Logistics Day. If deficiencies are found, we agree on improvements to be made and follow up on their implementation. WACKER uses in-house criteria and internationally recognized systems, such as the Safety and Quality Assessment System (SQAS) operated by the European Chemical Industry Council (CEFIC), to select logistics service providers and evaluate their performance. Our evaluation criteria include drivers’ qualifications and training, vehicle equipment and accident response. Through the use of standards and specifications, WACKER ensures that even the subcontractors working for our logistics providers meet our strict safety requirements.
In 2012, we recorded ten transport incidents (2011: eight). This number includes not only accidents and incidents involving the distribution of our intermediates and products where we commissioned the transport, but also incidents that do not involve hazardous goods, as well as those that do not adversely impact people or the environment. Such incidents are likewise listed in shipper evaluations.
Download XLS |
Transport Accidents | ||||||||||||||||||
|
|
|
|
|
|
|
| |||||||||||
Number of Accidents |
2012 |
2011 |
2010 |
2009 |
2008 |
20071 |
20061 | |||||||||||
| ||||||||||||||||||
|
|
|
|
|
|
|
| |||||||||||
Road |
8 |
6 |
4 |
5 |
11 |
– |
– | |||||||||||
Rail |
2 |
1 |
1 |
– |
4 |
– |
– | |||||||||||
Sea |
– |
1 |
– |
– |
2 |
– |
– | |||||||||||
Inland waterways |
– |
– |
– |
– |
– |
– |
– | |||||||||||
Air |
– |
– |
– |
– |
– |
– |
– |
A New Kind of Experiment Kit for Schools
Companies can be commercially successful only if they have society’s trust, which is why WACKER takes its social responsibilities seriously, especially in communities near its sites. We attach considerable importance to giving young people training in the natural sciences and technology. After all, we will need committed chemists and engineers in the future if we are to remain competitive.
2012 was the eighth time that we had taken the helm as statewide sponsor and organizer of the “Young Scientists” competition in Bavaria. We also again sponsored the Dresden/East Saxony regional heat of “Young Scientists.” We have launched a new experiment kit called CHEM2DO. With it, students get the opportunity to experiment with modern silicones and cyclodextrins. It includes a lesson plan and can be used in various kinds of German secondary schools. The experiments and documentation have been completely revised, and we have now also developed a preparatory course for teachers across Germany. Run by the teacher-training centers of the Society of German Chemists and selected universities, the course is the perfect way to prepare chemistry teachers for the experiments.
WACKER has set up a scholarship program at Liangfeng Senior High School in Zhangjiagang (China). Awarded annually to 25 students and six teachers with outstanding academic performances, the WACKER Scholarship provides financial support that extends to students from disadvantaged families. In addition, WACKER experts share their know-how at the high school by giving specialized classroom instruction on industrial silicone applications.
Employees Donate to Sustainable Projects
As a true corporate citizen, we support projects to help children and young people in communities near our sites and elsewhere in the world. Since 2007, WACKER has supported a German religious charity, “Die Arche” (The Ark), which aids children and young people from socially disadvantaged families in several German cities. It provides the children with hot meals and extra tutoring, organizes leisure activities and offers counseling. In the reporting year, WACKER presented its sixth annual donation of €100,000 to the charity’s Munich branch.
In 2012, the company relief fund (WACKER HILFSFONDS), our foundation for disaster relief, gave employees the option to donate the cents from their monthly paychecks to the fund on a regular basis. About 4,300 people in Germany have responded to the call and are thus helping to sustain relief fund projects centered on the reconstruction and running of schools and training facilities. As in other fund campaigns, the WACKER Group is participating in the cent-donation program with a contribution that matches employee donations. With the help of the cent donations, the foundation can now support an entire school of about 200 students in Kosgoda (Sri Lanka) up to the tenth grade. WACKER HILFSFONDS also supported schools in Gressier (Haiti) and Murghazar (Pakistan). Destroyed in natural disasters, they now have their students back in class in new buildings dedicated in 2012.
In 2012, the WACKER site in Nanjing (China) opened its gates to the public. The open house was organized by the Association of International Chemical Manufacturers and the Nanjing Chemical Industry Park. Some 400 guests from municipal government and the surrounding communities – as well as students and journalists – came to take a closer look at the WACKER POLYMERS site.