“All of us in the company can learn a lot from one another in matters of safety.”
The visitor from China has some suggestions. Wouldn’t it be a good idea to fit chin straps to all the hard hats? Couldn’t the footpaths be better marked out? And the traffic density on site ... Kim Hu mentions everything that strikes him, and Stefan Henn, Group coordinator for safety, pays close attention. His colleague Kim’s visit to WACKER’s main plant in Burghausen is part of a “cross-site audit.” The aim of the mutual site inspections is to learn better from one another. Learn from the Chinese? Aren’t we always hearing that accidents are routine occurrences in China, and that human life doesn’t count for much? The very idea raises a smile from Kim Hu, safety coordinator at WACKER Greater China, and from Stefan Henn. “At our German plants, there are quite a few things that are not as strictly controlled as in China,” says Henn. “In China, we were able to give our employees and management proper training from the start on the appropriate conduct and necessary safety regulations.”
Perfect Accident Statistics
The statisticians count accidents that involve sick leave as a ratio of million hours worked. The resulting figure is important in the chemical industry. In 2010, this statistic was zero for WACKER Greater China. Unbeatable! It was 0.6 in 2012. WACKER Greater China is thus one of the world champions in questions of safety. Stefan Henn himself spent three years in China for WACKER. So he knows the reasons why such exemplary safety work is performed there. When he arrived in Zhangjiagang in 2006, production in the new factory was just starting up. Hundreds of employees were gradually starting work. “They were mostly people under 30, very young, very dynamic, but with little experience in the chemical industry,” he recalls.
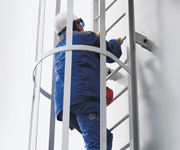
State-of-the-art technology is used to
protect employees and equipment.
So an intensive training program was developed for all employees to complete within their first few months. They deal with the requirements in three stages – on site, in the respective production facilities and at their own workplaces. Henn was delighted at how fast he was able to implement his safety plans. “If you want to lay down new rules at established sites, it can take a long time to reach the majority of the workforce. In Zhangjiagang, most of our 400 employees observed the conduct we expected right from the start,” says Stefan Henn.
Learning from the Competition
One reason why the Zhangjiagang plant, about two hours’ drive from Shanghai, works so well is that it combines WACKER’s safety expertise with that of one of its competitors. WACKER constructed the production facilities for the starting materials for manufacturing silicones together with the US Dow Corning group. The joint venture produces siloxane and pyrogenic silica. Nevertheless, from the works fire department through to the centralized safety regulations, many joint safety questions remained to be answered. Stefan Henn saw that as a huge opportunity: “We have combined the best safety plans from the two partners and tailored them so that they can be effectively implemented in Chinese day-to-day routine.” The Chinese safety team also provides creative incentives aimed at ensuring that employees are conscious of workplace safety on a daily basis.
Safety Bonuses
One of these ideas, which Kim Hu is particularly proud of, is the reporting system. “We have a special budget for rewarding people who report safety deficiencies and narrowly avoided accidents,” he explains. Each year, €10,000 is shared between particularly safety-conscious employees. And the incentive works. Over 200 reports are submitted each year. They show up weak points, such as inadequate barriers or careless fork lift truck drivers. The employees in China benefit, even if nothing happens. Their bonus increases if WACKER Greater China achieves its safety goals. The annual performance bonus is only paid if, among other things, the accident figures are at a low level.
Managers Must Set an Example
Because safety is a management responsibility, the managers at WACKER Greater China are given an additional incentive. Team leaders must specify their personal safety goals as part of their annual target setting. Management must set an example in matters of safety. Once a year, production is shut down for safety reasons. “We want all our colleagues to be completely familiar with EHS requirements,” says Kim Hu. That is why he organizes a “Safety Day” each year. This involves shutting down the production plants in Zhangjiagang, Nanjing and Wuxi for one afternoon. Last year, the employees met in the site canteen for a safety competition.
Keeping Safety at a High Level
The WACKER sites in China rely on standardized, readily verifiable rules. For example, regarding work approval. “In Zhangjiagang, a painter requires a work permit to climb a ladder,” explains Stefan Henn. In Germany, it is assumed that this activity is included in the painter’s professional training.
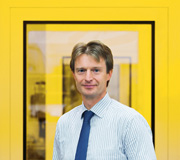
Stefan Henn
is Group coordinator for safety issues
and heads the safety department at
the Burghausen site.
Here, the Chinese mentality meets the approval of safety experts. In China, once a rule has been laid down, it is observed faithfully and is less likely to be questioned than in Germany. A good example of that is the use of protective glasses. “As a safety specialist, you can gain a good impression of the safety culture at a new site within half an hour,” explains Stefan Henn. The way cyclists ride around, for example, or the use of a handrail are telling signs. And, for Henn, it is absolutely essential to hold onto the handrail when using the stairs, even though some consider that overdoing it. “It shows that I take the subject seriously and accept responsibility for my own safety.”
Stepping up Dialogue
“We have to learn from one another,” says Stefan Henn. The sites in Germany still lead the way in some safety matters, such as plant safety and reaction safety. Similarly, other WACKER sites in the US, Europe or Asia have exemplary processes. “By improving dialogue, we will be able to make our company even safer in the future.”
Workplace Accidents
4.7 work-related accidents were recorded by the WACKER Group in 2012 per million hours worked. |
0.6 work-related accidents were recorded by WACKER Greater China in 2012 per million hours worked. |
![]() 5,797 trucks carrying hazardous materials were examined at WACKER’s Burghausen site in 2012. |
![]() 200 reports on possible safety risks were submitted by Chinese employees in 2012 as part of an incentive program intended to further improve the safety culture. |
Safety Training
850 managers from WACKER Germany took part in the Safety Plus training program in 2012. |
181 employees from WACKER Germany completed training for hazardous goods transportation in 2012. |
43 online training courses are offered by WACKER Germany on topics of workplace safety, for example on conduct at the plant or protective measures against explosions. |