Energy
Energy Targets: Lowering Specific Energy Consumption by 2022
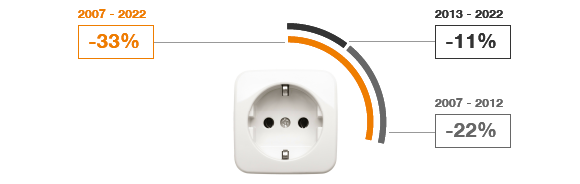
The chemical industry is one of the most energy-intensive sectors. In Germany alone, it uses around 20 percent of all the electricity consumed by industry. WACKER is therefore also continually improving the energy efficiency of its processes. This enables us to remain globally competitive and to support climate protection. Many chemical reactions generate heat that can be put to use in other production processes. We have been using integrated heat-recovery systems in Burghausen and Nünchritz for years and are continually improving them. In this way, we can reduce the amount of primary energy (as a rule, natural gas) that our power plants consume.
To further improve energy efficiency and reduce specific energy consumption (amount of energy per unit of net production output), the Executive Board has defined energy targets for WACKER Germany. The goal is to reduce weighted specific energy consumption by a third between 2007 and 2022.
Our energy goals ensure that we meet one of the requirements of the energy management system as per ISO 50001, which we have introduced and certified at all sites of Wacker Chemie AG, Siltronic AG and Alzwerke GmbH in Germany. Since 2014, we have thus already been in full compliance with the legal obligation to have an energy management system in place by 2015.
Bavarian Energy Award
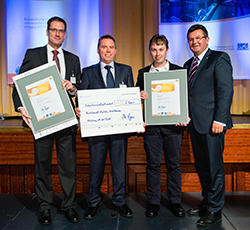
Bavaria’s state secretary for economic affairs Franz Josef Pschierer (right) handed over the 2014 Bavarian Energy Award to Ewald Schindlbeck, head of WACKER POLYSILICON (left), as well as to Werner Klenk and Claus Burkhardt of energy technology company Burkhardt GmbH (second and third from left). The Munich-based WACKER Group received the award for its highly efficient polysilicon production (photo: Bayern Innovativ).
In 2014, Wacker Chemie AG received the Bavarian government’s Energy Award, which was conferred in recognition of the Group’s highly efficient polysilicon manufacturing operations. Thanks to patented technology advancements and process optimizations, we lowered our specific energy consumption for polysilicon production by 29 percent.
Hyperpure polysilicon is the main raw material for making solar modules and, consequently, plays a vital role in generating solar power. The Bavarian Energy Award is conferred every two years for outstanding innovations in responsible energy management.
Generating Energy Efficiently
Burghausen uses hydroelectric power to generate electricity. Our Norwegian site, Holla, too, generates its electricity from water power. Our primary source of energy is climate-friendly natural gas.
At WACKER’s large Burghausen and Nünchritz sites, we produce steam and electricity in cogeneration systems. In Burghausen, we operate a highly efficient combined heat and power (CHP) plant to cover the site’s electricity and steam needs. It has a fuel efficiency of around 85 percent. The CHP plant represents a technology that bridges the gap to renewable energy systems, since it contributes to CO2 savings, unlike uncoupled electricity and steam generation. Its capacity makes it a so-called systemic facility that contributes to stabilizing the public grid.
These combined heat and power (CHP) plants have more than 80-percent fuel efficiency, which is significantly higher than that of conventional plants, where electricity and heat are generated separately.
Electricity Supply
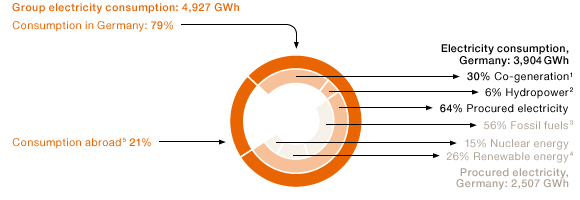
1 Burghausen and Nünchritz
2 Burghausen
3 Coal, lignite, oil, gas
4 Hydro, wind, solar power
5 Outside Germany, we purchase electricity from third parties based on the local standard energy mix.
In 2014, absolute electricity consumption rose slightly to 4,927 GWh (2013: 4,526 GWh), while energy efficiency measures served to lower specific energy consumption. This was due to the consistently high utilization of our polysilicon production capacity throughout the year. The Group’s power plants – the hydroelectric and CHP (gas and steam turbine) generating stations in Burghausen and the CHP plant in Nünchritz – produced around 1,405 GWh in 2014 (2013: 1,457 GWh). This means that WACKER covered almost 30 percent of its total electricity needs itself.
WACKER’s German production sites accounted for 79 percent (2013: 78 percent) of groupwide electricity needs. In Germany, we purchased enough electricity from utilities to cover 64 percent of our electricity requirements there (2013: 59 percent). In line with Germany’s energy mix, 56 percent of this electricity was generated from fossil fuels (2013: 51 percent). 15 percent came from nuclear energy (2013: 18 percent) and 26 percent from renewable energy sources (2013: 31 percent). Heat consumption, which includes the use of solid fossil and biogenic fuels (coal, charcoal and wood) in silicon-metal production in Holla, Norway, fell by 4 percent to 3,572 GWh (2013: 3,724 GWh). We changed the way we calculate the power-generation mix. Since 2014, our data is based on Germany’s energy mix as per the German Association of Energy and Water Industries (BDEW).
Consumption of natural gas decreased in 2013 due to the planned shutdown of a gas turbine at the Burghausen site. It sank further in 2014, in particular because of declining steam demand and lower hydrogen production compared with the previous year.
Download XLS |
|
|
|
|
|||||
|
|
|
||||||
GWh |
2014 |
2013 |
2012 |
|||||
|
||||||||
|
|
|
|
|||||
Electricity consumption |
4,927 |
4,526 |
4,559 |
|||||
Heat consumption |
3,572 |
3,724 |
3,755 |
|||||
|
|
|
|
|||||
Primary energy |
|
|
|
|||||
Total |
6,081 |
6,176 |
7,030 |
|||||
Of which |
|
|
|
|||||
Natural gas |
4,978 |
5,051 |
5,927 |
|||||
Solid fuels1 (coal, charcoal and wood) |
839 |
872 |
862 |
|||||
Heat supplied by third parties (steam and district heating) |
244 |
236 |
223 |
|||||
Fuel oil |
20 |
17 |
18 |
|||||
|
|
|
Hydroelectric Power
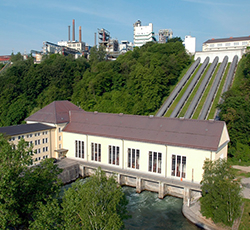
The Alzwerke power station has been supplying the Burghausen site with hydroelectric power since 1922.
The Burghausen site has been supplied with electricity from Wacker Chemie AG’s “Alzwerke” hydroelectric facility for over 90 years. From December 1922 to December 2014, this power station generated 22,782 GWh of electricity. Average annual production is currently at 266.1 GWh.
The Alz canal between Hirten on the Alz river and Burghausen on the Salzach river made it possible to harness the water – which plunges 63 meters into the turbines – for a hydroelectric power plant on the banks of the Salzach. The electricity generated by the Alzwerke plant was the key prerequisite for the chemical industry to settle in Burghausen. Over the past nine decades, the hydroelectric facility has continuously increased its energy yield and annual availability.
In 2014, our Nünchritz site specifically required around 91 percent less process steam from its CHP plant to manufacture one metric ton of product than it did in 1999, when WACKER acquired the site. Specific CO2 emissions developed accordingly.
Saving Energy with WOS
In 2014, we again improved our energy efficiency with the help of projects that form part of our WOS (Wacker Operating System) program. At our Burghausen site, for example, we feed cooling water that has been preheated in a compressor to the demineralization facility, saving steam and natural gas in the manufacture of deionized water. By reducing the pressure of the cooling water at our Nünchritz site, we have achieved electricity savings of over 15 percent.