Product Stewardship
Corporate Research & Development
WACKER’s research and development pursues three goals.
- Firstly, we search for solutions that meet our customers’ needs and contribute to their market success.
- Secondly, we optimize our processes in order to be the technology leader and to operate sustainably.
- Thirdly, we concentrate on creating innovative products and applications for new markets and on serving future trends, such as higher energy requirements, urbanization, digitalization and rising affluence.
Research along the Supply Chain
WACKER takes environmental, health and safety criteria into account at every stage of the product life cycle – every research and development project examines the sustainability aspects of our new products and processes, starting with the raw materials used. We try to minimize raw-material consumption, while selecting materials which offer maximum ecological benefit. Examples:
- Novel silicone resins are replacing organic binders in composites, and we are avoiding organic solvents in the manufacture of such resins.
- In the VINNEX® product family, WACKER has enhanced a binder system for bioplastics. This system now enables polymers based on renewable resources to be processed just like standard thermoplastics. The system improves the physical properties of the bioplastics and makes them compatible with each other. These polymer blends have higher impact strength, higher melt strength or better flexibility than conventional biopolymers. Blends formulated with VINNEX® can be processed into items such as food packaging materials, disposable flatware, parts for electronic appliances and self-degradable gardening and agricultural containers.
- One of the focal points of WACKER POLYMERS’ research is polymers that enable the formulation of low-emission downstream products, so that the latter can meet the requirements of the most stringent ecolabels. In the interests of sustainability, we have developed or enhanced products that are free of alkylphenol-based surfactants (APEOs), low in volatile organic compounds (VOCs) and largely free of formaldehyde. Examples include dispersible polymer powders using VAE (vinyl acetate-ethylene copolymers) for cement applications as well as products based on VAE dispersions, e.g. for coating carpets and for sealants.
Indeed, WACKER continually strives to optimize the efficiency, environmental impact, energy consumption and costs of its processes. Here is an example: to improve the energy balance of solar cells and lower costs, we have endeavored to make further reductions in energy consumption in polysilicon production. WACKER POLYSILICON has continued to optimize the processes in its closed production loop, enabling us to once again lower energy consumption during deposition and conversion. Using advanced, patented technology and process optimizations, we succeeded in lowering our specific energy consumption for polysilicon production by 29 percent between 2005 and 2013. For this achievement, Wacker Chemie AG received the Bavarian government’s 2014 Energy Award.
Environmental Assessments
Our products are generally supplied to business customers for further processing – not directly to end customers. Our life cycle assessments (LCAs) look at the environmental impact caused by a specific product family throughout its life cycle – a “cradle-to-gate” assessment extending from manufacturing to the factory gate. These analyses allow us to gage the sustainability of our products and production processes, and to improve them accordingly.
In the reporting period, WACKER POLYMERS, for example, updated the life cycle assessment data for homopolymer and copolymer dispersions as well as for dispersible polymer powders. The division continued to work on replacing APEO-based surfactants (alkylphenol ethoxylates) in its product range. By optimizing production processes, it succeeded in achieving further substantial reductions in the percentage of volatile organic compounds (VOCs) in numerous dispersions and polymer powders. Take the following example: VINNAPAS® 5111 L is a VOC-reduced polymer powder for the formulation of self-leveling flooring compounds and fillers that conform to eco-labeling requirements, such as EMICODE® EC1+ or Blue Angel.
Product Life Cycle
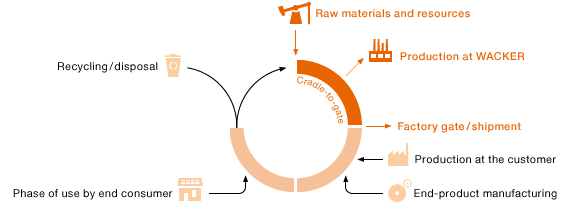
WACKER ECOWHEEL®
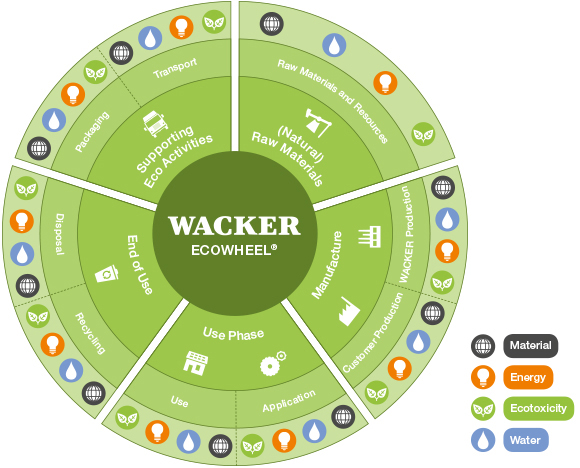
Since 2012, we have been using the WACKER® Eco Assessment Tool to evaluate systematically the risks and opportunities of our product line from an environmental perspective. We present these risks and opportunities in what is called an “ECOWHEEL®.” We take account of material, water and energy consumption, as well as ecotoxicity, over the entire product life cycle.
Research and Development at Two Levels
WACKER conducts R&D at two levels: centrally at our Corporate Research & Development department and locally at our business divisions. Corporate R&D coordinates activities on a company-wide basis and involves other departments, such as Corporate Engineering (during process development). We also use a management process to keep our R&D projects transparent throughout the Group. In 2014, we further optimized the Project System Innovation (PSI) program we use to manage our projects, focusing on making the compiled data more relevant in terms of actual benefits for projects and the portfolio.
We launched the New Solutions initiative in 2013. The goal is to develop technically and commercially advanced solutions for new applications. Expertise from various areas in the company is consolidated groupwide and applied to projects as needed. In 2014, we worked on ten projects in this program. The market and technology evaluations conducted under the initiative revealed potential additional sales worth hundreds of millions of euros. Initial solutions developed through the New Solutions initiative have been placed with customers for application testing.
Breakdown of R&D Expenditures
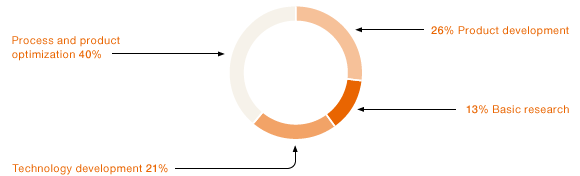
R&D expenditures in 2014 amounted to €183.1 million (2013: €173.8 million). At 3.8 percent (2013: 3.9 percent), the R&D rate – research and development spending as a percentage of Group sales – was down slightly year over year due to the positive sales trend. The bulk of R&D costs were incurred in the development of new products and production processes. In 2014, WACKER scientists worked on around 270 projects (2013: 260) based on more than 40 technology platforms. Over 20 percent of these projects were of a key strategic nature. The highly promising fields in which we work include energy, electronics, construction and automotive engineering as well as household and personal-care products, food and biotechnology.
Investments in R&D
Our investments in R&D included pilot plants that we use to scale up project results from the laboratory scale to full industrial-scale production, or to confirm results from simulations. Examples include polysilicon deposition and conversion, as well as a facility for producing electrically active silicone films. Corporate Research & Development has built laboratory facilities for the production of nanostructured silicon for lithium-ion batteries. Further investment spending funded laboratory equipment to investigate full cells of lithium-ion batteries, for example.
Strategic Collaboration with Customers and Research Institutes
Our business divisions conduct application-driven R&D. They focus on product and process innovations relating to semiconductor technology, silicone and polymer chemistry, and biotechnology, as well as on new processes for producing polycrystalline silicon. We collaborate with customers, scientific institutions and universities in order to achieve successful research results more quickly and efficiently. In the reporting period, WACKER worked on around 50 research projects with more than 40 international research institutes across three continents. Our collaborative efforts cover topics that include electricity storage, biotechnology, process simulation and process development. In the field of process development, we have established new partnerships with universities in Munich and Stuttgart.
Local Knowledge Transfer
WACKER has also created a worldwide network of 21 technical competence centers that liaise between sales offices and local production sites. Specialists in these centers customize products to regional requirements, taking account of climatic conditions, national standards and local raw materials, for example. They develop formulations for customers’ new products and optimize existing formulations.
Our WACKER ACADEMY locations serve as a collection of forums for industry-specific knowledge transfer between customers, distributors and WACKER experts. The focus is on industry-specific courses, which now cover silicone applications in addition to polymer chemistry, e.g. for cosmetics and paints. The training centers’ proximity to our development and test laboratories promotes the sharing of ideas and enables participants to conduct practical on-site tests. We work with company research facilities, universities and institutes to ensure our seminars remain state of the art.
Publicly Funded Research Projects
Some of our research projects were funded by the government in the reporting period. Examples:
- In the MAI Speed project, the German Federal Ministry of Education and Research (BMBF) is funding a subproject in which WACKER is involved. Working with partners from industry and science, we are doing research on new materials for use in fiber-reinforced lightweight construction in areas such as the automotive industry.
- In the Si-HTF project, the German Federal Ministry for the Environment, Nature Conservation, Building and Nuclear Safety (BMUB) is supporting the development of environmentally compatible high-temperature heat-transfer fluids for solar thermal facilities. In this project, WACKER is developing high-temperature silicon-based heat-transfer fluids for use in solar-thermal power plants with parabolic collectors. In contrast to those achievable with existing heat-transfer systems, these products should make higher operating temperatures possible in future systems, thus resulting in greater efficiency. This could lower the cost of electricity generation. One particularly beneficial feature of the new solution is its broad range of operating temperatures, which eliminates the need for expensive trace heating. We are also investigating their use in industrial heat-transfer applications.
- In the OPERA project, WACKER SILICONES is working on phosphorescent polymers for LED applications. This project is being supported at a European level by the European Nanoelectronics Initiative Advisory Council (ENIAC), and by the BMBF in Germany.
- In the MAINPAGE joint research undertaking, where WACKER was involved in two projects, the BMBF provided funds for the development of trailblazing new materials for industrial photovoltaic applications with enhanced energy efficiency. WACKER POLYSILICON had responsibility for a project aimed at producing granular polysilicon of the highest product quality. Siltronic led the research on a continuous, crucible-free pulling process for 200 mm monocrystals with granular silicon.
- In the Fusion Proteins project, the BMBF and the Bavarian Ministry of Economic Affairs, Infrastructure, Transport and Technology (STMWi) funded research on optimizing the industrial-scale production of proteins through the secretion of fusion proteins in specific E. coli K-12 bacterial strains.
- In the Olefinic Fatty Acids project, the German Federal Ministry of Food, Agriculture and Consumer Protection (BMELV) funded work on new methods for cleaving, transforming and functionalizing olefinic fatty acids. We developed a method by which specialty olefinic chemicals can be manufactured.
During 2014, our business divisions and Central R&D submitted applications for eight more projects (in the areas of lightweight construction, energy storage, biologics and electronics) to government sponsors, with approvals pending. Our externally-funded research projects are coordinated by our Public Funding office, which evaluates candidate programs, submits our project proposals and manages contacts with funders.
Our R&D Workforce
WACKER had 1,061 research and development staff in 2014 (2013: 987), which represents 6.4 percent (2013: 6.2 percent) of the Group’s workforce. Our scientists and engineers conduct basic research, develop new products and processes, and improve existing processes. The lab and technical staff at our R&D, applications-technology and production-support facilities work in our laboratories and in our production and pilot plants, or on-site at our customers’ plants. Our other R&D personnel construct research equipment in our workshops, or perform administrative functions in such fields as market research and trend analysis.
We recognize the dedication of our researchers by presenting them with awards. The 2014 Alexander Wacker Innovation Award went to a project team for its ground-breaking work on the ESETEC® 2.0 secretion system. The researchers were honored for their fundamental analysis of the E. coli-based production system for pharmaceutical proteins and for making enhancements which enable even highly complex molecules such as antibody fragments to be produced cost-effectively and efficiently. Named after the company’s founder, the Alexander Wacker Innovation Award has been presented every year since 2006 – alternating between the categories of product innovation, process innovation and basic research. In 2014, the €10,000 in prize money was awarded for innovation in basic research. In the previous year, the prize was awarded in the process innovation category and went to a project team at Siltronic that had developed a process for manufacturing silicon wafers for high-performance devices. This granular float-zone process opens up technological prospects for the custom high-performance wafer market.
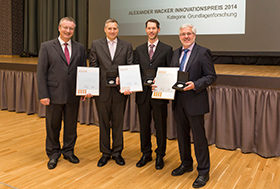
WACKER Executive Board member Auguste Willems (far left) with the winners of the 2014 Alexander Wacker Innovation Award (from left): Dr. Carsten Bornhövd, Dr. Tobias Daßler and Dr. Günter Wich. The researchers were honored for enhancing a system for manufacturing pharmaceutical proteins.
Siltronic AG confers its Inventor Award on employees who have delivered technological innovations. In 2014, eight employees received this award for their creative thinking and the systematic implementation of their projects to optimize wafer processing. With their CMP (chemical-mechanical polishing process) and wet-bench cleaning projects, the two winners in 2013 improved processes in the final wafer-treatment stages. The Siltronic Inventor Award is bestowed in two categories – “Most Important Invention” and “Best Inventor” – each offering €10,000 in prize money.
Research for Sustainable Development
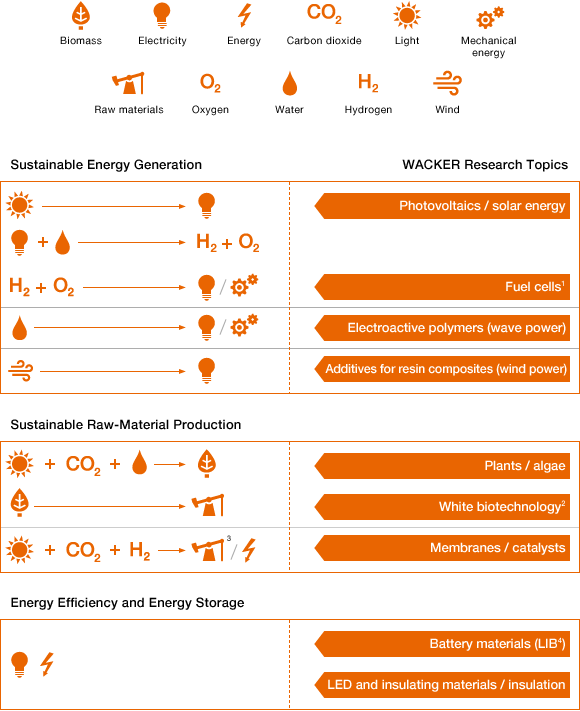
1 Fuel-cell project ended
2 Out-licensing
3 Methane
4 Lithium-ion batteries (LIB)
Selected Topics of Central R&D
In our research, we are devoting particular attention to energy storage and renewable energy generation. Further R&D priorities are the highly promising fields of consumer care, biotechnology and construction applications.
On the topic of energy, we continued our activities in electricity storage and conversion. We are working on materials used in lithium-ion batteries (LIB) in order to enhance this type of battery for automotive and consumer-product applications. We are also focusing on lightweight construction, as lighter materials can be used to conserve raw materials and energy, for instance in the automotive and aerospace industries. In these fields, we are developing building blocks for composites.
We have developed nanoscale silicon structures and binders for use in anodes of lithium-ion batteries. In tests conducted on batteries with these anodes, we have achieved good stability in charge-discharge cycles: compared with commercially available anodes, these have a much higher specific capacitance. We are also developing new additives in the SafeBatt project, also funded by the BMBF, to improve the safety of lithium-ion batteries.
Their good gas permeability makes silicones suitable as a membrane material for all kinds of applications. When combined with gas-selective materials, such membranes could be used for separating gases. The hydrophobic nature of silicone films combined with their high water-vapor permeability also makes them interesting as materials for textile applications and air-filtration systems. We are conducting tests in a development project to determine how such material systems might be used.
Sustainable Products
Over the last two years, WACKER has developed diverse products that promote sustainability. Examples are presented below for the highly promising fields of energy, urbanization, digitalization and rising affluence.
Energy
The energy sources of the future are the sun, wind, water, biomass and geothermal power. WACKER is making a significant contribution to their efficient use, and WACKER SILICONES has been driving forward research into electrically active silicone polymers. Very thin films of these polymers lend themselves to energy recovery, and are also used for actuators and sensors. In 2014, WACKER and one of its partners developed an innovative algae bioreactor with highly transparent silicone rubber tubing from WACKER at its heart.
Conversion of Wave Power into Electricity
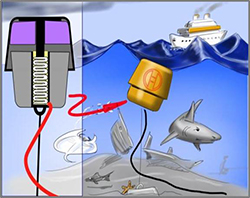
Low-maintenance generators based on electroactive polymers made of ELASTOSIL® Film can transform the power of ocean waves into energy. The idea behind this “sandwich” of silicone film and electrodes is simple yet ingenious: the action of the waves stretches a silicone film and then compresses it again; this movement generates electrical energy.
Silicone films can play a pivotal role in the conversion of wave power into electricity. As part of the EPoSil project sponsored by the German Federal Ministry of Education and Research (BMBF), an industrial/R&D consortium led by Robert Bosch GmbH is developing the basic principles underlying wave farms. As a member of the project, WACKER is responsible for developing and manufacturing ELASTOSIL® Film, a precision silicone film.
As silicone elastomers are electrically insulating, have good dielectric properties and endure long-term mechanical loads with hardly any signs of fatigue, ELASTOSIL® Film can be used as a dielectric precision layer in electroactive polymers (EAPs). EAPs alter their shape when a voltage is applied. Based on this principle, silicone films can be used to develop innovative sensors, actuators and generators. Potential applications range from intelligent pressure and strain sensors and electrical relays to valves and peristaltic pumps. As a component of “artificial muscles” in actuators, silicone films can contribute to replicating not only linear movements, but also natural forms of movement.
Biocompatible SILPURAN® Film is ideal for use in heart-lung machines or for the manufacture of atraumatic adhesive plasters. ELASTOSIL® Film and SILPURAN® Film are made without the use of solvents in cleanroom conditions.
We are developing silicone resins that modify the proppants used in modern oil and gas drilling technologies. WACKER® SG 3377, a silicone oil demulsifier, can break crude oil emulsions even when the oil-water mixture is not at the proper processing temperature – a problem that arises, for example, on offshore oil rigs. Even at temperatures below 40 °C, the product exhibits outstanding performance, reducing both the water content of crude oil to 1 percent and the concentration of oil in water to under 10 ppm.
WACKER actively supports climate-friendly mobility – whether in battery research or as a manufacturer of high-tech materials for electric vehicles. Specialty silicones can withstand the higher temperatures that arise in car engines which have been downsized to achieve better fuel efficiency. Carbon-fiber-reinforced plastics (CFRPs) with silicone-coated fibers are 80 percent lighter than steel. That makes them a key component in the automotive sector for extending the range of electric vehicles and reducing the fuel consumption of combustion engines.
We have refined our highly transparent liquid silicones for lighting applications and are supporting energy-efficient LED-based vehicle headlamp technologies by developing highly transparent silicone rubber compounds, which are used to make components for secondary optical devices. The tremendous increases in LED performance over the last few years has meant that organic materials are no longer capable of withstanding the heat and light flux. That is why high-performance LEDs are being produced using heat- and light-resistant silicone-based encapsulation and lens materials. LUMISIL® silicone elastomers make it possible to produce a moldless optical lens directly on an LED chip in a single production step. In this manner, LED components can now be manufactured in very large quantities with modest plant and process investment.
The generation of safe, clean power from wind plays a central role at WACKER, too. Wind turbine blades consist of half-shells of composite materials that are bonded together. Such bonding requires the use of special high-impact modifiers for wind turbines. With its VENTOTEC® impact modifiers, WACKER is able to supply a new generation of products for optimizing reactive resins. The powder-form additives combine in one product the two technologies for the production of silicones and organic polymers. The result is a hybrid product that makes adhesive layers stronger and more durable. The additives significantly enhance the impact strength of epoxy resins and other thermosets.
Polysilicon: Energy-Generating Solar Installations
WACKER is among the main suppliers worldwide of polysilicon for the production of solar modules. In the reporting period, WACKER continued to expand its production capacity for hyperpure polysilicon to meet increasing demand from the photovoltaic industry and to support the switch to renewable energy sources.
Polysilicon is a hyperpure material that is deposited from trichlorosilane in the form of rods and crushed into chunks for further processing. Our customers use it to produce monocrystalline or multicrystalline solar wafers, which are in turn utilized to make solar modules, e.g. for installation on roofs. In the reporting period, we continued to strengthen our technological lead in polysilicon production. Our aim is to improve our silicon deposition process and to enhance our closed production loop, which ranges from silicon metal, hyperpure solar-grade and electronic-grade silicon through to silicones and pyrogenic silica.
Technological progress in the development of solar modules continues to proceed in leaps and bounds. Wafer thickness has been reduced: from 450 µm in 1995 to 250 µm in 2005 and to under 200 µm in 2010. The standard thickness is currently around 180 µm. Cell efficiency has risen in parallel, and is now around 18 percent for multicrystalline standard cells and well over 19 percent for monocrystalline ones. High-efficiency monocrystalline cells have efficiency levels of between 20 and 25 percent.
The energy payback time – the time taken for a photovoltaic cell to generate the energy used in its production – has become even shorter. Depending on the geographical location of the solar cells, this payback time now ranges from 6 months (in the Sahara) to 18 months (in northern Europe). Each metric ton of polysilicon used in solar modules prevents the emission of 6,000 tons of CO2. (Source: study issued in 2011 by the Karlsruhe Institute of Technology.)
Dispersible Polymer Powder for Building Insulation: Energy-Efficient Construction
Saving energy – particularly in construction – has developed into a global trend. On top of that, there is climate change, which makes it necessary to insulate against heat as well as cold. VINNAPAS® dispersible polymer powder ensures that the adhesive mortar sticks to both the wall and the insulation material in exterior insulation and finish systems / external thermal insulation composite systems (EIFS/ETICS). The dispersible polymer powder boosts adhesion and impact resistance within the base coat. Hydrophobizing VINNAPAS® polymer powders, in particular, prevent moisture forming in the top coat.
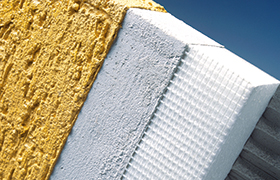
Modern ETICS/EIFS for building insulation consist of a multilayered material composite. But it takes the addition of a dispersible polymer powder to create a permanently stable insulation system.
There is enormous potential for using EIFS/ETICS to achieve a long-term reduction in greenhouse-gas emissions. Heating or air-conditioning accounts for more than half of a building’s energy demand. A house that is inadequately insulated loses a large part of its energy via the exterior walls. An ETICS/EIFS system can reduce a building’s heating costs by up to 50 percent.
The German Energy Agency (dena) has calculated the savings potential that can be achieved using insulation alone. While over 10,000 kilowatt hours of heating energy escape through the walls of an uninsulated single-family house each year, this can be reduced to just 2,200 kilowatt hours if the external walls are insulated.
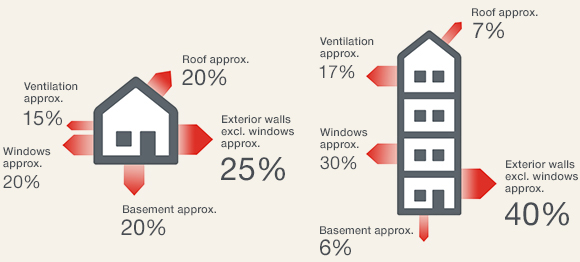
Almost 80 percent of the energy consumed by buildings is required for heating. Most of the heating energy that is lost escapes through the building envelope. For a single-family house this averages at 25 percent. In a ten-story apartment building, 40 percent of the heating energy is lost through exterior walls (Source; available in German only: Qualitätsgedämmt e.V.)
More than 80 percent of residential buildings in Germany were built prior to the introduction of the third thermal insulation ordinance of 1995. The energy rating of two out of three of these buildings needs to be improved. If all residential buildings were renovated to comply with the energy saving ordinance of 2009, 357 TWh heating energy could be saved annually. Here, building insulation alone has a savings potential of 177 TWh. This is 1.8 times as much energy as German nuclear power plants generate per year.
The biggest energy savings on houses built prior to 1993 can be achieved by improving the energy rating of the building envelope, especially the exterior walls. The climate footprint of the past 35 years for exterior insulation systems in Germany is impressive:
- 997 million m2 of exterior insulation
- Equivalent to savings of 92 billion liters of heating oil
- Equivalent to a reduction of 279 million metric tons of CO2 emissions
(Source; available in German only: Qualitätsgedämmt e.V.)
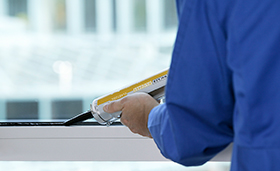
Around 20 to 30 percent of heating energy is lost through poorly insulated windows. ELASTOSIL® silicone rubber seals windows, is weather-resistant and withstands temperature fluctuations.
Urbanization and Construction
More than half of the world’s population now lives in cities. This creates new challenges for our communal life. We need infrastructure that conserves resources better, construction that is more intelligent, and materials that are lighter. As one of the world’s leading manufacturers of construction chemicals, WACKER is contributing to the development of better cities for the future. An example of this is particularly important for cities in emerging economies where water is scarce: sealing slurries using WACKER binders can seal leaky canals securely and economically, thus preventing water from being lost.
VINNAPAS® dispersions and dispersible polymer powders are used as polymer binders (e.g. in tile adhesives, self-leveling compounds and interior wall paints) in the construction sector. They make it possible to formulate construction chemicals with reduced VOC emissions, which meet stringent environmental standards such as the EMICODE® emissions standard set by Germany’s GEV (Association for the Control of Emissions in Products for Flooring Installation). In the reporting period, we launched a new polymer powder for the formulation of cost-efficient, low-emission self-leveling flooring compounds. VINNAPAS® 4220 L can be used to produce self-leveling compounds that result in smooth, uniform surfaces satisfying ecolabel requirements such as EMICODE® EC1+.
Dispersions for Environmentally Sound Paints
VINNAPAS® dispersions are used, among other things, as binders for interior-wall paints. Particularly ecofriendly dispersions are those made without substances that emit formaldehyde or APEO-based surfactants (alkylphenol ethoxylates), and containing just minute amounts of volatile organic compounds (VOCs). A VOC content of <1 g/l in interior-wall paints ensures a pleasant and healthy indoor climate. In the reporting period, we premiered the VINNAPAS® EF 3818 polymer dispersion for low-odor, low-VOC interior paint formulations. It is made without APEOs, plasticizers or solvents.
Dispersible Polymer Powders for Tile Adhesives, Flooring and Insulation Systems
Urban centers are booming worldwide. Wherever space gets tight, the buildings get higher. This puts new demands on materials. VINNAPAS® dispersible polymer powders make it possible to manufacture insulation boards comprising different materials, including renewable substances such as cork and wood-wool.
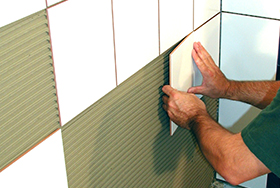
In the reporting period, we launched VINNAPAS® 8620 E, a polymer powder for the formulation of high-quality, low-emission tile adhesives, which can be used to reliably bond modern large-format or very thin tiles as well as porcelain or natural-stone materials. VINNAPAS® 8620 E is free of plasticizing additives.
Silicone Resin Emulsion Paints: Long-Lasting Facade Protection
SILRES® BS products based on quartz-like structures protect exterior paints and plasters. The facades stay attractive for longer and are better insulated, and energy efficiency is boosted as a result. Silicone resin emulsion paints (SREPs) are permeable to water vapor and so help to improve the climate indoors.
A coat of high-quality silicone resin emulsion paint reduces heat loss from external walls by as much as 40 percent. Heat is lost faster from damp walls – the role of the silicone resins is to help keep the walls dry. A SREP coating decreases heat demand by an average of 4.6 percent. Silicone resin emulsion paints and silicone resin plasters lengthen the intervals between renovations of facades by up to 25 years. Some listed buildings cannot be insulated with ETICS/EIFS. In such cases, a silicone resin emulsion paint is one of the few materials that will improve a building’s energy balance.
Gypsum dry-mix mortars formulated with SILRES® BS Powder S can be mixed very quickly without generating any dust. It can be used indoors, since it is environmentally compatible and releases neither alcohol nor other volatile organic compounds (VOCs).
Digitalization
Siltronic AG is a global leader in the market for hyperpure silicon wafers and a partner to many top-tier chip manufacturers. It develops and produces wafers with diameters up to 300 mm at sites in Europe, Asia and the USA. Wafers are cut from silicon ingots and then used to produce chips for electronic devices. Sensors, power devices, microcontrollers and other electronic chips make sure that modern electrical appliances and hybrid and electric vehicles are safe and economical.
The performance of semiconductor devices doubles about every two years. Among the key performance-boosting parameters are the design rules achieved on a silicon wafer. They determine how many transistors fit on a device per square centimeter. The semiconductor industry’s current standard design rules of 22 and 16 nanometers (nm) are increasingly being replaced by an 11 nm standard. In the coming years, the design rule will be reduced even further, to 8 nm, and Siltronic is currently developing processes to produce 300 mm wafers that can be used for this new design rule. In the reporting period, regular shipments of 11 nm wafers continued to increase and we further refined the technology for 8 nm wafers. We also worked on wafers for power and LED applications.
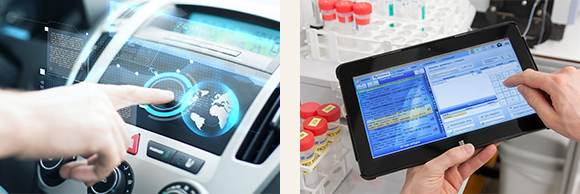
Our highly transparent silicone gels are deployed in energy-saving displays and the touchscreens of mobile electronic devices.
Rising Affluence
Affluence is on the rise almost all over the world, lifting expectations as regards living conditions, food, health and comfort as well. WACKER is driving innovations in all of these areas. We intend to keep pace with rising affluence, especially in emerging-market economies, by offering products manufactured using energy- and resource-efficient processes. Such products include polymers, e.g. for the paper and packaging industry, and cyclodextrins, e.g. for foodstuffs.
In the reporting period, we launched new products made with sustainable ingredients that target the highly promising field of rising affluence. Here is an example from medical engineering: surgeons have recently begun using silicones from WACKER to make tissue-mimicking “phantoms.” ELASTOSIL® RT 601 and ELASTOSIL® P 7676 are silicones of this kind, and have been deployed in experiments to distinguish tumors from healthy tissue. We have developed SILPURAN® 2112, a skin-compatible silicone adhesive for modern wound dressings, while SILPURAN® 2438 ADH silicone adhesive is suitable for bonding textiles and composites, e.g. of the kind used to make prosthetics. This product, too, is both biocompatible and skin compatible.
WACKER BIOSOLUTIONS has launched a nature-identical hydroxytyrosol branded HTEssence®, which is suitable for use in nutritional supplements and cosmetics. Hydroxytyrosol is an antioxidant with therapeutic effects on blood pressure, joints as well as the immune and cardiovascular systems. As a free-radical scavenger, it can mitigate the effects of skin aging and lighten the color of the skin.
We have developed products for nutritional supplements that enhance the bioavailability of active ingredients. With CAVAMAX® W8, a cyclodextrin, we can enhance the bioavailability of curcumin 40-fold. Curcumin, the active compound in turmeric, is a powerful antioxidant that exhibits anti-inflammatory, antibacterial and hypoallergenic properties. As curcumin is extremely hydrophobic, it is not readily absorbed in the human bloodstream.
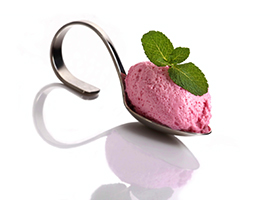
In addition to being an acknowledged of source dietary fiber, CAVAMAX® W6, an alpha-cyclodextrin, has stabilizing properties that make it suitable for other innovative food-contact applications. It is a low-cholesterol, purely vegan alternative to caseinate in coconut milk powders and enables cream desserts or fruit mousse to be made without the addition of fat or eggs.
In the reporting period, the EU Commission certified a health claim for the proven health-benefit effect of alpha-cyclodextrins. The EU expert opinion confirmed that alpha-cyclodextrins can reduce the increase in blood sugar after a starchy meal. It thus backs up a recommendation issued by the European Food Safety Authority (EFSA). Food manufacturers can now state on their labeling that alpha-cyclodextrin used as dietary fiber has a blood-sugar-lowering effect. Alpha-cyclodextrins are annular, plant-based molecules obtained from renewable raw materials, such as potatoes and corn. They are used to provide dietary fiber, e.g. in beverages, dairy products, muesli bars and breakfast cereals.
Our researchers at Wacker Biotech have enhanced the E. coli-based secretion technology used for the production of pharmaceutical proteins. With ESETEC® 2.0, we now have an efficient method for producing high yields of antibody fragments for medical therapies. The method was first applied for the US company MedImmune, a subsidiary of AstraZeneca. This technological development was honored with the 2014 Alexander Wacker Innovation Award in the category of basic research.
Wacker Biotech and XL-protein GmbH have shown that antibody fragments with substantially extended activity can be produced efficiently using WACKER’s ESETEC® secretion technology and XL-protein’s PASylation®. We custom-developed a bacterial cell line and obtained high yields of the PASylated antibody fragment, which is currently being tested for effectiveness against autoimmune diseases. Working with Metheresis Translational Research, Wacker Biotech developed a cell line based on ESETEC® for producing an antibody fragment for a cancer drug.
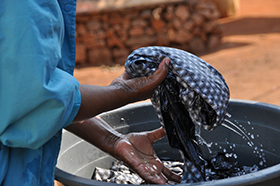
In Asia, especially in the key market of India, people often still wash their garments by hand. In the reporting period, we developed SILFOAM® single-rinse technology. Antifoam agents in the detergent mean only one rinse is required, thus saving water.
The new silicone impregnant WACKER® HC 321 facilitates the manufacture of cleaning agents that lend a remarkably water-repellent surface to textiles and other substrates. WACKER® HC 321 is an aqueous silicone emulsion designed for solvent-free household products.
GENIOPLAST® Pellet P plus has been approved as an additive for plastics in food-contact use, making it suitable for the manufacture of kitchen appliances or packaging. It enhances the effect of fire-retardant additives, and creates smooth surfaces, e.g. for refrigerator inserts, that are especially easy to clean. As a processing aid for compounders, the product lowers energy consumption, and makes for higher throughput and less waste.
GENIOSIL® XL 70 is an arylalkoxysilane monomer designed as a water scavenger for silane-curing adhesive and sealant formulations. It is ideal for products that must be free of unpleasant odors when used, e.g. adhesives for parquet flooring or liquid waterproofing systems applied over large areas. In the reporting period, we launched the VINNAPAS® EP6300 and VINNAPAS® EP7000 dispersions, which are binders for water-based adhesives and free of alkylphenol-based surfactants (APEOs).
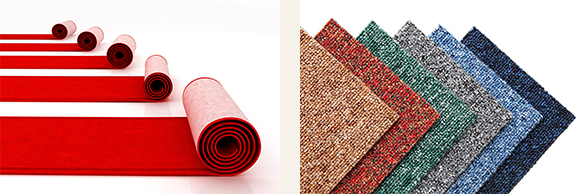
Since their surface area is large, floor coverings can emit volatile organic compounds (VOCs). Used as binders for carpet coatings, VINNAPAS® VAE dispersions emit hardly any VOCs, exhibit better flame retardance and are virtually odorless. With VINNAPAS® CA 55 as a binder, it is possible to formulate both precoats and secondary coats to bond the backings of carpets used, e.g., in residential settings. Floor coverings of this kind, which bear the “GUT” label of the German Association of Environmentally Friendly Carpets (GUT e.V.), must undergo extensive analysis for possible pollutants.