Water
Water is an extremely precious resource – not only as drinking water, but also as a raw material, solvent and coolant in many technical and chemical processes. At WACKER, we use water sparingly and protect natural water resources. We always purify our wastewater as effectively as possible and recycle the water through loops in our production. We make sure that this multiple use does not increase energy consumption or otherwise negatively impact the environment.
Water Consumption Tested Using the Global Water Tool©
In many parts of the world, clean water is particularly scarce, and obtaining and purifying water is very expensive. As a globally-active company, we take such conditions into account in our production processes and during transport. We use the Global Water Tool© (GWT) developed by the World Business Council for Sustainable Development (WBCSD) to analyze the annual relative water stress index of the countries in which our main global production sites are located.
This analysis was conducted for the first time in 2012, based on analyses using the water stress index developed by the Water Systems Analysis Group of the University of New Hampshire, USA. This index provides information on the relationship between water consumption and the availability of renewable fresh water. The outcome of the analysis is that our most important production sites are located in regions with a low relative water stress index. These regions account for more than 97 percent of our annual water use and over 90 percent of our production volume. Production sites in countries for which no GWT-based water stress index information is available account for less than 0.5 percent of our water consumption.
“Save Wastewater and Make a Profit” was the title of a special Employee Suggestion Program initiative launched in December 2014 at the Nünchritz site. The purpose of the initiative is to encourage employees to develop ideas for conserving and recycling water in production. The campaign ran until June 30, 2015 and is currently being evaluated. In 2014, a similar campaign took place at the Burghausen site, where employees submitted 72 improvement suggestions, e.g. for wastewater treatment.
The process water used at Nünchritz comes from on-site wells (2014: 4,230,971 m3; 2013: 4,123,612 m3). Drinking water accounts for less than 1 percent of our total water consumption at this site. In 2014, we reduced the water consumption at Nünchritz with the help of a project that forms part of our WOS (Wacker Operating System) program. We now use the water we need for waste-gas purification at the incinerator twice, allowing us to considerably reduce the amount of wastewater.
The town of Freiberg is connected to a highly branched, man-made water ditch system. Our Siltronic site there uses surface water, which is carried to the site by such a ditch, to cool the crystal pulling facilities. We also purify the surface water into hyperpure water for wafer production.
By modifying production processes and re-using materials, the Siltronic division has reduced its use of chemicals, e.g. in wafer cleaning tanks. We reuse water several times over, wherever the purity requirements for wafer manufacturing permit. This has allowed us to reduce specific consumption of demineralized (deionized) water by around 35 percent in Burghausen since 2005 and also around 35 percent in Portland since 1996 without compromising on quality. We monitor the use of ultrapure water in wafer production, where Siltronic achieves a water-recycling rate of up to 45 percent.
Lower exterior temperatures and plant-capacity utilization in 2013 resulted in reduced cooling-water use at Burghausen. In 2014, cooling-water use returned to the 2012 level, due to production increases at a Burghausen facility.
Groupwide, organic emissions to wastewater – specified as chemical oxygen demand (COD) – fell in 2014. We closed the Burghausen acetaldehyde plant in late 2012; this has significantly lowered the COD and emissions of halogenated organic compounds (AOX) to water. At the Nünchritz site, we implemented optimization measures for wastewater treatment in 2014, which reduced the COD load.
In 2014, WACKER POLYMERS’ VAE (vinyl acetate-ethylene dispersions) plant in Burghausen lowered its specific wastewater load by 5 percent by implementing new flushing options for filtration systems. This is equivalent to a COD-load reduction of some 126 metric tons and an AOX-load reduction of 10.2 metric tons. WACKER SILICONES started up a plant for decentrally pretreating wastewater in Burghausen in 2014. This plant uses the Fentox® process to remove highly diluted silicone constituents from the wastewater generated in the production of silicone emulsions.
Download XLS |
|
|
|
|
|||||
|
|
|
||||||
|
2014 |
2013 |
2012 |
|||||
|
||||||||
|
|
|
|
|||||
Water consumption (1,000 m3) |
241,973 |
220,908 |
242,072 |
|||||
Cooling water volume (1,000 m3) |
223,647 |
197,681 |
225,391 |
|||||
Wastewater volume (1,000 m3) |
21,140 |
18,995 |
19,569 |
|||||
COD (chemical oxygen demand) (t) |
1,230 |
1,320 |
1,460 |
|||||
AOx (adsorbable organic halides) (t) |
2 |
2 |
3 |
|||||
Heavy metals (t) |
1.3 |
1.1 |
1.2 |
|||||
Nitrogen (t)1 |
533 |
451 |
414 |
|||||
Phosphorus (t) |
7.8 |
6.0 |
7.0 |
|||||
|
|
|
Fewer Emissions to Water
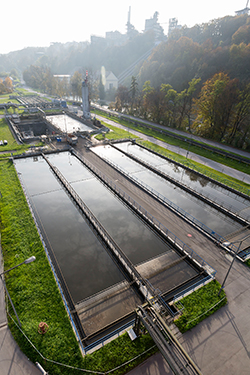
Organically polluted wastewater is purified in the first bio-stage of the wastewater treatment system at the Burghausen site.
At our Burghausen site, we have significantly reduced the amount of harmful emissions to the Salzach river over the past five years. In 2012, we our acetaldehyde and acetic acid production plant. The shutdown reduced organic pollution (COD, chemical oxygen demand) in the multistage biological wastewater treatment plant by 30 percent. The site’s wastewater volumes remained unchanged. In 2013, we switched the biological wastewater treatment plant’s first bio-stage from double-tank to single-tank mode on a trial basis. We made this successful mode of operation permanent in 2014.
Furthermore, in spring 2013, we put an intermediary wastewater storage tank into operation. We use it to collect peak pollutant loads from specific facilities so that they can be fed into the biological wastewater treatment system in a controlled manner during phases of low influent from production. This makes the supply more consistent and leads to more stable operation of the biological wastewater treatment plant. Compared to 2010, emissions of organic pollutants to the Salzach river have decreased by 39 percent.
Since the acetaldehyde plant’s shutdown, emissions of halogenated hydrocarbons (AOX) have fallen by 66 percent relative to 2010. The consistently low mass flows of readily degradable organic substances (BOD5, biological oxygen demand) o the past two years are the result of stable operation have decreased by 16 percent since 2010.
Thanks to these measures, we are also preventing sludge (biomass from the biological wastewater treatment plant) from overflowing into the Salzach river. Furthermore, several facilities were able to reduce their emissions of the heavy metals, iron, copper and zinc to the Salzach by around 50 percent.