Prevention
Workplace Accidents 1 Involving Permanent Staff and Temporary Workers
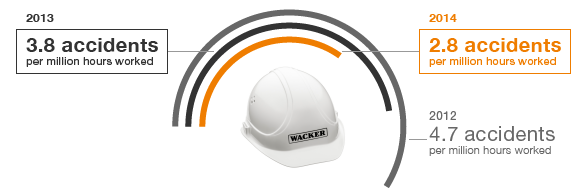
1 Accidents leading to at least one work day missed
Managing plants and processes in a way that poses no risk to people or the environment is an important objective at WACKER. We therefore operate a groupwide safety management system that covers both workplace safety and plant safety. Our processes and workplace safety standards will be aligned with international standard OHSAS 18001 by the end of 2015. Systematic workplace safety includes the regular evaluation of hazards and work-area monitoring.
Risk Management
The first step in ensuring plant safety is to identify the risks systematically and then assess them. This includes analyzing how well we control the energy (e.g. pressure, heat) existing in a process and determining what influence an individual fault might have on a chain of events leading up to a failure or accident. On completion of this comprehensive analysis, we specify safety measures that will prevent undesirable incidents.
In 2013, our ANSIKO project on machine safety targeted our production sites in Germany. In 2014, we turned our attention to all international sites, identified machinery that poses a risk of injury, subjected their safety plans to critical review and made them even safer to protect employees.
Safety Training & Employee Motivation
WACKER attaches particular importance to providing ongoing training to its safety experts. We hold regular training sessions, for example, on plant safety and explosion protection. Group experts organize safety training at WACKER sites, including those outside Germany. In the period under review, we trained our specialists in Adrian, USA, and Zhangjiagang, China, primarily in the field of machine safety. We carried out safety reviews at the following sites:
- Jandira, Brazil
- Holla, Norway
- Kolkata, India
- Nanjing and Zhangjiagang, China
- Ulsan, South Korea
- Nünchritz, Freiberg, Cologne and Jena, Germany
But it is not only our safety experts who regularly attend trainings. All our employees are given safety training specific to their individual workplace, e.g. in the form of e-learning courses. WACKER Germany, for example, offers 32 online training courses on workplace safety. Topics range from general safety guidelines for office and laboratory workers to instruction on safe behavior in ex areas and the classification of hazardous materials. Each instruction module contains tests that enable participants to assess their progress.
WACKER published a safety manual for partner companies in Germany in 2013. It lays down standard policies and procedures for working with partner companies. The manual is directed not only at the partner companies, but also at their customers, such as construction managers, project engineers and production supervisors. The goal of the manual is to ensure the same level of safety for employees of partner companies at our sites as for WACKER employees. Customers are requested to assess the safety aspects of their suppliers’ behavior transparently and unconditionally. The partner companies’ approach to safety flows into the supplier assessment.
WACKER Greater China has been supporting other chemical companies in establishing process-safety systems since 2013. WACKER organized appropriate training for more than 20 companies at the request of the Zhangjiagang free-trade zone, the Association of International Chemical Manufacturers in China (AICM) and the International Council of Chemical Associations (ICCA).
Our 2015 goal for occupational safety is to reduce our groupwide accident rate (the number of workplace accidents per million hours worked) to below 2.0. As part of our efforts toward this goal, we set ourselves an interim target for 2014 of fewer than 3.0 workplace accidents per million hours worked at German sites. We almost reached this target: in Germany, there were 3.4 workplace accidents with work days missed per million hours worked in 2014. Groupwide, the figure was 2.8. That was 26 percent down on the previous year (2013: 3.8 workplace accidents). Nonetheless, we are lagging behind the chemical companies that lead the way in occupational safety.
In terms of reportable accidents (accidents with more than three work days missed), WACKER’s numbers are far better than the German chemical industry average. The reportable accident rate in 2014 was 1.2 per million hours worked (2013: 1.4), while, in 2013, Germany’s BG RCI (the statutory employer liability insurance carrier of the basic materials and chemical industries) registered 9.3 reportable accidents per million hours worked in chemical companies. During the reporting period, again there was not a single fatal workplace accident among WACKER employees.
Since 2014, we have also been logging accidents involving employees of partner companies working on WACKER sites. Groupwide, there were 33 accidents with work days missed at our partner companies.
Very few of the accidents at our sites are chemical in nature. The most common causes are tripping, slipping and falling, and performing manual activities without due care. Not satisfied with our accident rate, we are increasing our occupational-safety efforts. We are systematically implementing our new safety program – WACKER Safety Plus (WSP), which incorporates successful safety elements from sites that have particularly low accident rates. Such elements include safety patrols, discussions with the workforce and emergency drills. WACKER Safety Plus has the goal of recognizing and avoiding unsafe behavior – on the way to and from work, in the office, at the plant, when operating machinery, or when handling chemicals.
In 2014, WACKER focused on reviewing and updating hazard assessments at our German sites. This yielded improved protection concepts and measures in many areas. The program will be continued across all German sites until 2016.
Download XLS |
|
|
|
|
|||||||
|
|
|
||||||||
|
2014 |
2013 |
2012 |
|||||||
|
||||||||||
|
|
|
|
|||||||
Accident rate across Group: accidents1 per 1 million hours worked |
2.8 |
3.8 |
4.7 |
|||||||
Europe |
3.5 |
4.5 |
5.3 |
|||||||
The Americas |
1.6 |
2.6 |
4.3 |
|||||||
Asia |
0.8 |
0.6 |
1.2 |
|||||||
Accident rate across Group: reportable accidents2 per 1 million hours worked |
1.2 |
1.4 |
2.1 |
|||||||
Fatal workplace accidents |
– |
– |
– |
|||||||
|
|
|
Decoys on Site
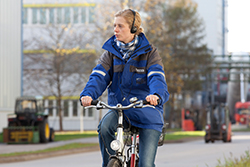
In 2013, WACKER’s main site in Burghausen conducted a campaign called “Take the Plunge.” Its goal was to encourage employees to approach colleagues and supervisors about careless behavior. Over a ten-month period, safety officers and foreman-level managers were deployed to simulate typical behavior with risk potential: they used their cell phones while cycling, climbed over fences, rode their bikes on the sidewalk and disregarded other familiar safety rules, without ever being exposed to real danger. Any employees who had the courage to confront the decoys were praised and rewarded with a raffle ticket.
“The focus was not only on employees behaving in accordance with safety rules themselves, but on communicating with others,” explains Stefan Henn, Group Safety Coordinator and initiator of the campaign. The goal was to bring about a change in culture. “We want employees to gradually lose their inhibitions and start talking to one another about unsafe conduct. The ‘Take the Plunge’ initiative certainly got us off to a great start.”
Practiced Safety
Low accident figures are a reflection of safety-conscious conduct. At WACKER, we give special recognition to facilities that operate for sustained periods of time without a reportable accident. Some of these have also been honored by institutions outside the company. Our Ulsan site in South Korea is one such example. During the reporting period, this site received an impressive two awards: in 2013 from the Korean Gas Safety Corporation for twelve years without a gas-related accident, and in 2014 from the Korea Occupational Safety and Health Agency (KOSHA) for 13 years without any accident at all.
Transport Safety
WACKER ensures that its products are safely stored and transported. Before loading vehicles, we carry out stringent checks on them, especially if they are carrying hazardous goods. In 2014, we arranged for almost 7,800 trucks to be checked (2013: roughly 8,500). If a vehicle fails inspection, we continue sending it back until it passes. Failure rates have been low for years now. In 2014, the failure rate for shipments of hazardous goods in Germany dropped further to 0.3 percent (2013: 1.2 percent). WACKER normally audits hazardous-goods shippers every two years.
We rely on well-trained personnel for transport safety, too. In 2013 and 2014, our workforce in Germany alone completed around 2,500 classroom training courses and 2,750 online courses on the safe transportation of hazardous goods.
We regularly review aspects of transport safety with our logistics providers, e.g. during the annual Logistics Day. If deficiencies are found, we agree on improvements and then follow up on their implementation. WACKER uses in-house criteria and internationally recognized systems, such as the Safety and Quality Assessment System (SQAS) operated by the European Chemical Industry Council (CEFIC), to select logistics service providers and evaluate their performance. Our evaluation criteria include drivers’ qualifications and training, vehicle equipment and accident response. Through the use of standards and specifications, WACKER ensures that even the subcontractors working for logistics providers meet our stringent safety requirements.
For products that have a high hazard potential, we use packaging and tanks of the highest quality that often exceed statutory requirements. Wherever possible, we assess the road route to be taken by the transport.
We recorded a total of 16 transport incidents in 2013 and 2014. This number includes not only accidents and incidents involving the distribution of our intermediates and products where we commissioned the transport, but also incidents that do not involve hazardous goods, as well as those that do not adversely impact on people or the environment. These incidents, too, form part of our shipper assessments.
Download XLS |
|
|
|
|
|||
|
|
|
||||
Number of Accidents |
2014 |
2013 |
2012 |
|||
|
|
|
|
|||
Road |
5 |
4 |
8 |
|||
Rail |
2 |
1 |
2 |
|||
Sea |
1 |
2 |
– |
|||
Inland waterways |
– |
1 |
– |
|||
Air |
– |
– |
– |
|||
|
|
|