WACKER focuses its R&D efforts on finding solutions for customers and for serving such global megatrends as rising energy needs, urbanization, digitization and demographic change.
WACKER is a highly research-intensive, international chemical company. R&D expenditure in 2010 came in at €165.1 million (2009: €164.0 million). The
R&D rate – research and development spending as a percentage of Group sales – amounted to 3.5 percent, a decline against 2009 due to our robust sales growth.
New Products Account for Higher Share of Sales
The new-product rate (sales percentage of products launched in the last five years) grew again, at 23.6 percent (2009: 16.2 percent). 2010’s increase mainly stemmed from Siltronic, where new technologies for high-performance electronic components delivered higher sales. These technologies include wafers for chip generations with design rules of 32 nanometers. Siltronic also notched up its first sales of products with design rules of 22 nanometers. At WACKER POLYSILICON, we launched new products, too.
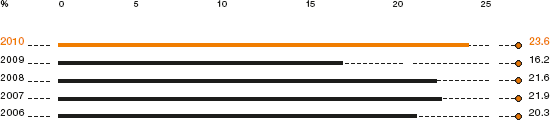
1 Sales percentage of products launched in the last five years
In 2010, WACKER invested €13.4 million in R&D facilities (2009: €10.2 million). In the “Consortium für elektrochemische Industrie,” our corporate research facility in Munich, we erected a new test facility and invested in new analytical instruments. Further investments included lab-capacity expansions worldwide, new lab equipment, and pilot plants.
We generated about €7.5 million from licensing agreements in 2010 (2009: €3.4 million), on account of greater production capacity at the Siltronic Samsung Wafer joint venture.
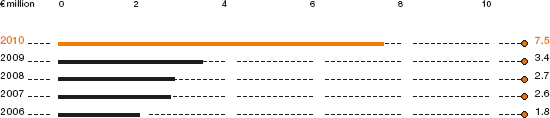
WACKER’s innovative strength is reflected in the number of patents held and patent applications submitted. In 2010, we filed 121 patent applications (2009: 150). Our patent portfolio contains 4,664 patents.
Most of the €165.1 million in R&D costs was spent on the development of new products and production processes.
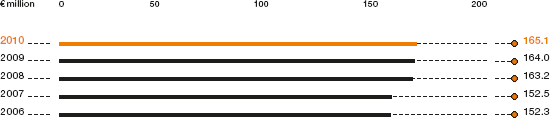
Research and Development at Two Levels
WACKER conducts R&D at two levels: centrally at our Corporate Research & Development department and decentrally at our business divisions. Corporate R&D coordinates activities across the company in consultation with the Executive Board.
We have a portfolio-management process to ensure that our R&D project portfolio is transparent throughout the Group. We thus evaluate existing projects and select new ones in line with market needs.
WACKER scientists are currently working on around 220 topics based on 40 technology platforms. More than a quarter of these topics are key strategic projects, which account for 45 percent of all project costs incurred in 2010.
Strategic Collaboration with Customers and Research Institutes
Our business divisions conduct application-driven R&D. They focus on product and process innovations relating to semiconductor technology, silicone and polymer chemistry, and biotechnology, as well as on new processes for producing polycrystalline silicon. To achieve successful research results more quickly and efficiently, we collaborate with customers, scientific institutes and universities. In 2010, WACKER worked with more than 30 European and American research institutes on around 50 research projects – covering topics such as white biotechnology, energy and 450 mm silicon wafers.
WACKER has also created a network of 20 technical competence centers worldwide. They liaise between sales offices and local production sites. At these centers, our specialists customize products to regional requirements, taking account of climatic conditions, national standards and local raw materials, for example.
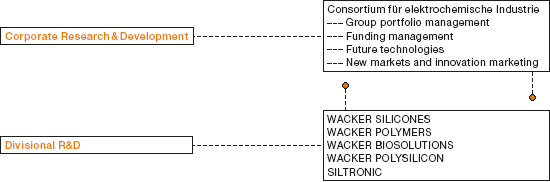
As the center of WACKER’s R&D activities, the Consortium has the task of researching scientific correlations to develop new products and processes efficiently. Another Consortium task is to harness and develop new business fields that complement the Group’s core competencies.
download table |
| ||||||||||||||
Employees in R&D as of December 31, 2010 |
|
|
|
|
| |||||||||
Number |
2010 |
2009 |
2008 |
2007 |
2006 | |||||||||
|
|
|
|
|
| |||||||||
Group R&D employees |
1,057 |
1,072 |
1,078 |
1,038 |
1,024 | |||||||||
R&D ratio1 in Group (%) |
6.5 |
6.9 |
6.8 |
6.9 |
7.0 | |||||||||
R&D employees, Germany |
855 |
860 |
836 |
835 |
819 | |||||||||
R&D employees, international |
202 |
212 |
242 |
203 |
205 | |||||||||
|
|
|
|
|
| |||||||||
Group R&D employees (Germany) |
855 |
860 |
836 |
835 |
819 | |||||||||
by qualification |
|
|
|
|
| |||||||||
Scientists and engineers |
337 |
332 |
311 |
302 |
288 | |||||||||
Lab staff and technicians |
344 |
349 |
345 |
344 |
349 | |||||||||
Other personnel |
174 |
179 |
180 |
189 |
182 | |||||||||
|
|
|
|
|
| |||||||||
Group R&D employees (international) |
95 |
90 |
113 |
66 |
63 | |||||||||
by qualification2 |
|
|
|
|
| |||||||||
Scientists and engineers |
31 |
30 |
34 |
29 |
25 | |||||||||
Lab staff and technicians |
32 |
29 |
34 |
36 |
34 | |||||||||
Other personnel |
32 |
31 |
45 |
1 |
4 |
WACKER operates in the highly promising fields of biotechnology, energy, construction and automotive engineering. In biotechnology, WACKER BIOSOLUTIONS focuses on the growth areas of food, pharmaceuticals and agriculture. We further improved our ESETEC® process for the bacterial production of pharmaceutical proteins. This has led to the production of several such proteins in high yields to cGMP (current Good Manufacturing Practice) standards. Some of these are already undergoing clinical tests.
Selected Divisional Research Projects
For the food industry, our researchers developed CAVAMAX® W8 CURCUMIN. This ring-shaped cyclodextrin sugar molecule renders the curcumin active ingredient more soluble in aqueous milieu, thereby increasing its bioavailability, i.e. the extent to which it can be absorbed in the human body. Curcumin has an antioxidant effect which stems from its ability to scavenge the free radicals that damage body cells. Studies have also revealed that curcumin possesses anti-inflammatory properties, which can support the prevention and treatment of cancer.
In the energy sector, we continued our activities in electricity conversion and storage. We are working on materials for use in lithium-ion batteries and fuel cells. These are used mainly in cars and to supply energy to houses. WACKER is a member of the National Platform for Electric Mobility, an initiative launched jointly by the German government and industry. By 2020, there are expected to be at least one million electric vehicles on German roads.
WACKER SILICONES added the GENIOSIL® product family to its range of construction sealants. These hybrid adhesives and sealants combine the typical properties of silicones and organic polymers. They crosslink particularly quickly and retain their functionality over the long term, even in highly stressed areas. They are free of tin and plasticizers. GENIOSIL® N70 achieves unprecedented levels of bond strength on all kinds of substrates. As a result, it is now possible to bond numerous items that previously had to be joined with nails and screws.
Our researchers also developed powder modifiers for engineering materials. Epoxy adhesives which have been modified with these high-impact products are able to withstand severe mechanical stress, such as that generated in the rotor blades of wind turbines.
In the medical sector, WACKER SILICONES launched a UV-activated silicone adhesive for wound care and scar treatment. Sold under the name of SILPURAN® 2149 UV, this product cures to a soft elastic material on brief exposure to ultraviolet light. The silicone helps to create a moist environment that supports wound healing. Adhesion is dependable and so gentle that wound dressings can be removed without sticking to the skin.
Research at WACKER POLYMERS is geared toward improving production processes for dispersions and dispersible polymer powders. We slashed emission levels for polymer production by lowering consumption of vinyl acetate monomer and enhancing its level of recovery. New products included vinyl acetate-ethylene dispersions for zero-emission indoor paints and for plasticizer-free adhesives, as well as new water-repellent polymer powders for plasters and exterior insulation and finish systems.
WACKER POLYMERS collaborated with customers on developing biodegradable polymer products composed of VINNEX® binders and flour or starch. The properties of such polymer blends are similar to those of petroleum-based plastics. However, they can be fully biodegraded by industrial composting techniques. This renders them suitable for use in packaging materials and products for the catering, gardening and landscaping sectors.
To improve the energy balance of solar cells and lower our costs, we further reduced energy consumption in polysilicon production. The energy payback time – the length of time required to regenerate the energy needed for production – has become even shorter. It now ranges from between 10 to 18 months, the exact duration depending on the geographical location of the installed solar panels.
Alexander Wacker Innovation Award for New Wafer-Grinding Method
WACKER honored two of its researchers with the Alexander Wacker Innovation Award 2010 for developing a method for grinding semiconductor wafers. Called Planetary Pad Grinding (PPG), this innovation allows ultra-flat silicon wafers to be manufactured for future generations of electronic components. It combines the advantages of lapping and grinding, two processing methods that were previously considered incompatible. We can now produce silicon wafers – in the required quality, in high yields and at competitive prices – for even more powerful electronic components.
Some semiconductor makers are considering the development of larger wafers, 450 mm in diameter, to enable further productivity gains and cost reductions. Siltronic is developing key processes for producing 450 mm wafers and is a member of EEMI450 (European Equipment and Materials Initiative for 450 mm), an EU-funded project.
Transferring Knowledge Locally
At our international training centers, we expanded our programs in 2010 and offered more interdisciplinary courses. The WACKER ACADEMY serves as a forum for industry-specific knowledge transfer between customers, distributors and WACKER experts. It concentrates on construction-chemical courses (which, since 2010, have included silicone applications in addition to polymer chemistry) and on training for other industries, such as cosmetics and paints. The program is rounded out with basic courses on business administration, intercultural cooperation and the efficient use of e-business tools.
The training centers’ proximity to our development and test laboratories promotes exchanges of views and enables participants to conduct practical on-site tests. We work with company research facilities, universities and institutes to ensure our seminars remain state of the art.
WACKER attaches considerable importance to fostering young scientific talent and close contacts with universities. In 2010, we enlisted students from over 30 universities to write final-year projects and theses. We additionally sponsored 29 students at the Institute of Silicon Chemistry, which was founded at the Technical University of Munich four years ago.
download table |
Key Product Launches in 2010 |
|
|
| |||
Product |
Description |
Application |
Sector | |||
|
|
|
| |||
CAVAMAX® W8 CURCUMIN |
Molecular encapsulation of the curcumin active ingredient in cyclodextrin |
Anti-inflammatory, prevention/ |
Dietary supplement | |||
|
|
|
| |||
DEHESIVE® 971 |
Platinum-catalyzed, addition-curing silicone polymer |
Production of labels and release papers |
Paper and label production | |||
|
|
|
| |||
ELASTOSIL® 76540 A/B |
Two-component liquid silicone rubber |
Assembly of plastic oil pans for engines |
Automotive | |||
|
|
|
| |||
ELASTOSIL® LR 3092/65 |
Silicone elastomers with low compression set |
Intercoolers, spark-plug boots |
Automotive | |||
|
|
|
| |||
ELASTOSIL® R 101 |
Highly elastic silicone elastomer |
Damping vibrations in engine bearings |
Automotive | |||
|
|
|
| |||
ELASTOSIL® R 770 |
Flame-retardant silicone elastomer |
Door and wall profiles, acoustic insulation mats |
Shipbuilding, transport, aircraft makers | |||
|
|
|
| |||
ELASTOSIL® R plus 4370 |
Self-adhesive silicone rubbers |
Manufacture of hard/soft combinations |
Plastics | |||
|
|
|
| |||
ELASTOSIL® LR 3040/40 |
Fast-curing silicone elastomer with high tear strength |
Membranes, valves, pacifiers, teething rings |
Automotive, household and leisure products, baby care | |||
|
|
|
| |||
ELASTOSIL® R plus 4366 and 4066 |
Solid silicone rubber with lubricious surface |
Catheters, drains, metering and connecting tubes |
Food and medical technology | |||
|
|
|
| |||
GENIOSIL® N70 |
Silane-curing, hybrid organic polymers |
Manufacture of elastic adhesives and sealants for plastics, tiles, plasterboard |
Construction | |||
|
|
|
| |||
POWERSIL® Fluid TR 20 |
Cold-start insulating fluid |
Cooling and insulating transformers |
Energy | |||
|
|
|
| |||
SilGel® 613 |
UV-activated silicone gel |
Encapsulating electronic components |
Automotive, solar cells, electrical and electronic engineering | |||
|
|
|
| |||
SILPURAN® 2149 UV |
UV-activated, ultra-pure silicone rubber |
Dressings for wounds and for treating scars |
Medicine | |||
|
|
|
| |||
SILPURAN® 8630/60 |
Solid silicone rubber |
Parts for medical devices, such as catheters and drains |
Medical technology | |||
|
|
|
| |||
VINNAPAS® XD 05 |
Polymeric binder (vinyl acetate-based copolymer dispersion) |
Adhesives, paper packaging for foodstuffs |
Paper and packaging industry, adhesives manufacturers | |||
|
|
|
| |||
VINNAPAS® EP 1400 and EP 441 |
Polymeric binder (vinyl acetate-based copolymer dispersion) |
Adhesives, packaging, cardboard boxes, envelopes, bags |
Paper and packaging industry, adhesives manufacturers | |||
|
|
|
| |||
VINNAPAS® EP 710 |
Polymeric binder (vinyl acetate-based copolymer dispersion) |
Adhesives, e.g. for cigarette paper |
Paper and packaging industry, adhesives manufacturers, tobacco industry | |||
|
|
|
| |||
VINNEX® |
Polymeric binder (vinyl acetate-based copolymer dispersion) |
Manufacture of polymer blends from renewable resources, e.g. flour and starch |
Food packaging, gardening and landscaping | |||
|
|
|
| |||
300 mm wafers with design rules of 32 nanometers |
Wafer format |
High-performance electronic components, e.g. microprocessors, data storage modules, signal processors |
Semiconductors |