Managing Sustainability
We are convinced that companies can only be profitable in the long term if they take their responsibility toward the environment and society seriously. Sustainability has thus been firmly rooted in both our production and business processes for many years.
Sustainability on a Global Basis
Our sustainability activities are underpinned by our membership in two global initiatives: Responsible Care® (the chemical-industry initiative) and the UN’s Global Compact. Through this voluntary commitment, WACKER undertakes to protect the environment, employees and society above and beyond legal requirements. Importantly, we expect our suppliers to respect the principles of the Global Compact, and we evaluate them on this point in our risk assessments.
In recent years, WACKER has grown worldwide. We have set up new production sites and expanded others. As globalization proceeds, we adapt our sustainability practices accordingly. The linchpin of our operational processes is our integrated management system (IMS).
WACKER has been pursuing several strategic projects in the field of sustainability management:
-
One focus has been on Group certification of our operational processes to ISO 9001 (quality) and ISO 14001 (environment) by 2011.
-
Every WACKER site is to be certified to OHSAS, (Occupational Health and Safety Advisory Series), an occupational health management system recognized all around the world.
-
Our Global EHS&PS Excellence project aims to standardize the management of environmental protection, health, safety and product stewardship worldwide, while taking account of regional requirements.
-
We are extending our compliance system across every region where WACKER operates.
Substantial progress was made on these projects in 2010:
-
Group certification: all sites in the USA and at WACKER Greater China are now covered by the Group certificate. It encompasses all production sites – except for those in Brazil and India, our Jena plant (Germany), and 2010’s new acquisitions. This has roughly halved the company’s previous annual expenditure on external audits.
-
Preparations for OHSAS certification of our occupational health and safety management system commenced. We compiled a checklist for sites to gauge their degree of compliance with OHSAS and to identify shortfalls.
-
The Global EHS&PS Excellence project was completed. Global responsibilities and reporting lines were simplified and rendered more transparent. We revised our policy on environmental protection, health, safety and product stewardship and adapted them to regional needs. We also created a new process that helps us set and track long-term sustainability goals.
In 2010, WACKER Greater China worked toward having its key, majority-owned production facilities certified as national environmentally-friendly enterprises by the Chinese Environmental Protection Bureau. Our Zhangjiagang site met all the requirements for the certificate, and is now awaiting an official audit. In 2010, Nanjing (a relatively new site) attained ISO 14001 certification for its environmental management system – a requirement for recognition as a national environmentally-friendly enterprise.
Compliance System Expanded
WACKER’s ethical and legal principles of corporate management exceed legal requirements. In 2010, the Group expanded its compliance system. For example, WACKER Greater China set up a compliance hotline. Our other subsidiaries each have a compliance officer who is contacted directly. We expanded our compliance team beyond Germany, the USA and China by appointing and training new compliance officers at other major production locations. As a result, employees in Japan, India, South Korea, Brazil and Singapore now have direct access to compliance officers. In 2010, the Compliance Management department held numerous classroom seminars to inform employees about WACKER’s ethical and legal management principles. We developed an online course that has been used to train people across the Group who have regular business contacts. Additionally, our workforce in Germany has been encouraged to undergo online training on data protection. If employees notice any violations, they have been instructed to inform their supervisors, the employee council, their designated HR contacts or the compliance officers.
Environmental Protection
All WACKER’s processes focus on the need to protect the environment and to manufacture safely. We attach particular importance to integrated environmental protection. This commences with product development and plant planning. In 2010, WACKER spent €11.8 million on environmental investments (2009: €9.1 million). Environmental operating costs amounted to €65.2 million.
In 2010, we began expanding Nünchritz’s wastewater treatment plants in readiness for the polysilicon production facility due to come on stream there in 2011. This expansion will double the capacity for treating inorganic wastewater.
In 2010, we continued working on our groundwater remediation strategy at Nünchritz. We conducted a field test to determine whether contaminants (solvent residues) in the groundwater there can be degraded by naturally occurring microorganisms. The test’s results are expected in 2011. The land for Nünchritz’s new polysilicon facility was remediated in 2010, as part of the construction work there. Some 75,000 metric tons of sludge contaminated with heavy metals and hydrocarbons were removed and disposed of properly. The remediation enabled us to avoid using virgin land for the new facility. The groundwater and soil contamination was a legacy of production activities prior to WACKER’s acquisition of the site.
Our environmental indicators revealed divergent trends in 2010. Water consumption fell thanks to a new recooling plant used in the cooling-water system at Burghausen, our largest site. The amount of non-methane volatile organic compounds (NMVOCs) rose, due to higher production-capacity utilization and plant start-ups in China. Overall, our environmental figures showed a positive trend. WACKER continuously strives to close its material loops and recycle byproducts from other areas into production – and, thus, to prevent or reduce waste.
download table |
| ||||||||||||||||
Environmental Indicators from 2008 to 20101 |
|
|
|
| ||||||||||||
|
|
2010 |
2009 |
2008 | ||||||||||||
|
|
|
|
| ||||||||||||
Air |
CO2 emissions |
986,000 t |
969,000 t |
976,041 t | ||||||||||||
|
Nitrogen oxides (NOX) |
926 t |
963 t |
997 t | ||||||||||||
|
Non-methane volatile organic |
415 t |
383 t |
501 t | ||||||||||||
Water |
Water consumption |
252,151,000 m3 |
264,532,000 m3 |
241,286,375 m3 | ||||||||||||
|
Chemical oxygen demand (COD) |
1,820 t |
2,730 t |
4,782 t | ||||||||||||
|
Halogenated organic |
6 t |
6 t |
7 t | ||||||||||||
Waste |
Disposed of |
48,520 t |
80,860 t |
87,293 t | ||||||||||||
|
Recycled |
77,030 t |
63,430 t |
74,327 t | ||||||||||||
|
Hazardous2 |
69,320 t |
100,860 t |
108,458 t | ||||||||||||
|
Non-hazardous |
56,230 t |
43,430 t |
53,161 t | ||||||||||||
Energy |
Electricity consumption |
3.8 TWh |
2.7 TWh |
2.4 TWh | ||||||||||||
|
Primary energy |
|
|
| ||||||||||||
|
Natural gas |
5.5 TWh |
5.4 TWh |
5.4 TWh | ||||||||||||
|
Solid fuels3 |
0.4 TWh |
– |
– | ||||||||||||
|
Heat (supplied by third parties)4 |
0.2 TWh |
0.2 TWh |
0.2 TWh | ||||||||||||
|
Heating oil |
0.01 TWh |
0.01 TWh |
0.01 TWh |
Energy Management
The chemical industry is an extremely energy-intensive sector. WACKER is constantly improving the energy efficiency of its processes. This enables us to remain globally competitive and to support climate protection. At Burghausen, for example, we generate hydroelectric power and our new Norwegian production site at Holla obtains its electricity mainly from hydroelectric power (as is usual in Norway). Our primary source of energy, though, is climate-friendly natural gas. At WACKER’s large Burghausen and Nünchritz sites, steam and electricity are produced in cogeneration systems. These combined heat and power (CHP) plants have more than 80 percent fuel efficiency, twice that of conventional power-generation plants.
In 2010, WACKER’s electricity consumption rose to 3.8 million MWh (2009: 2.7 million MWh), primarily due to expansion of polysilicon production at Burghausen and the acquisition of the silicon-metal plant at Holla, Norway. The Group’s captive power plants – the hydroelectric and CHP (gas and steam turbine) generating stations in Burghausen and the CHP in Nünchritz – produced 1.5 million MWh. This means that WACKER covered roughly 40 percent of its total electricity needs itself. Groupwide, CO 2 emissions totaled 986,000 metric tons, of which 83 percent resulted from captive power plants that are subject to emissions legislation.
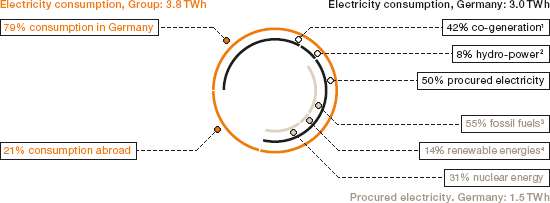
1 Burghausen and Nünchritz
2 Burghausen
3 Coal, lignite, oil, gas
4 Hydro, wind, solar power
WACKER’s German production sites account for 79 percent of its electricity needs. In Germany, we purchased enough electricity from utilities to cover 50 percent of our electricity requirements there. In line with the utilities’ primary energy sources, about half of this electricity was generated from fossil fuels (55 percent). 31 percent came from nuclear energy, and 14 percent from renewable energy sources.
2010 saw POWER PLUS, our energy-efficiency project, implementing further measures. Due to the purchase of the Holla site, heat consumption rose to 3.4 TWh (2009: 2.8 TWh) across the Group. The heat consumption figures reflect for the first time the use of solid fossil fuels (coal, charcoal, wood) at the newly acquired silicon-metal plant.
Workplace, Plant and Transport Safety
The primary goal of safety management at WACKER is not only to protect our employees, our neighbors and the environment, but also to safeguard our productivity. We analyze plant risk in two stages. First, we conduct a danger-scope analysis where we simulate a potential damaging event, such as a fire or product spill. We investigate possible causes and adopt preventive measures. Second, we examine critical plant components for potential error sources and then create a risk matrix. This matrix helps our experts to assess and classify risks and to take appropriate protective measures.
Production-Plant Safety Plans Reviewed
In 2010, as part of our ANSIKO 2010 project, we randomly reviewed the safety plans of all production plants that could prove especially hazardous. One focus was on facilities with a dust-explosion risk. That review was prompted by a dust explosion at Burghausen in 2009. While property had been damaged (costing some €0.5 million), no harm had been done to people or the environment.
WACKER attaches particular importance to providing ongoing training to its safety experts. We hold regular training sessions, for example, on plant safety and explosion protection. Experts from the Group organize safety training at international WACKER sites – in the year under review, they held safety courses at Ulsan (South Korea) and Zhangjiagang (China).
In 2010, there were 4.3 workplace accidents groupwide (2009: 4.0) per 1 million hours worked. Most accidents are not of a chemical nature. They are caused by tripping, slipping, falling, and manual activities. WACKER’s accident rate is higher than the global chemical-industry average. The ICCA (the global chemical association) cited an average of 3.65 accidents per 1 million hours worked in 2008. At WACKER, the accident rate is fueling our efforts to further enhance occupational safety. In 2010, we started rolling out a new safety program in Germany. Called WACKER Safety Plus, it adopts safety elements that Group companies and sites with particularly low accident rates have successfully employed. These include safety patrols, analysis of near-misses, and group discussions with the workforce.
download table |
| ||||||||||||
Reportable Accidents per 1 Million Hours Worked1 |
|
|
|
|
| |||||||
Accident Rate |
2010 |
2009 |
2008 |
2007 |
2006 | |||||||
|
|
|
|
|
| |||||||
Reportable accidents involving Group employees |
4.3 |
4.0 |
3.7 |
3.8 |
4.1 |
In addition to occupational and plant safety, we ensure that our products are safely stored and transported. Before loading dangerous goods vehicles, we carry out stringent checks on them. We reject any that are defective. The defect rate has been at a low level for years. In 2010, it was 3.0 percent in Germany. Every two years, WACKER audits hazardous goods shippers. We regularly review aspects of transport safety with our logistics providers, e.g. during the annual Shipping Day. If deficiencies are found, we agree on specific improvements and then follow up on their implementation. To evaluate shippers’ performance, we use in-house criteria and internationally recognized systems, such as the Safety and Quality Assessment System (SQAS) operated by the European chemical association (CEFIC), to evaluate shippers’ performance. Our evaluation criteria include driver qualifications and training, vehicle equipment and accident response.
In 2010, we recorded 5 transport accidents. This number includes not only accidents involving the delivery of our products where we commissioned the transport, but also incidents that do not adversely impact people or the environment.
download table |
| ||||||||
Transport Accidents |
|
|
| |||||
Number of Accidents |
2010 |
2009 |
20081 | |||||
|
|
|
| |||||
Road |
4 |
5 |
11 | |||||
Rail |
1 |
– |
4 | |||||
Sea |
– |
– |
2 | |||||
Inland waterways |
– |
– |
– | |||||
Air |
– |
– |
– |
Product Stewardship
WACKER ensures that all its products, if used properly, pose no risk to people or the environment. Product information is always up to date and any new findings are reflected in risk assessments. We compile material safety data sheets for all our sales products, regardless of legal provisions. WACKER publishes over 54,000 material safety data sheets in up to 33 languages.
We continuously strive to eliminate or minimize substances harmful to human health or the environment in our products and processes. We pursue this goal in different ways:
-
We seek to replace hazardous substances with alternatives
-
If no alternative substance is available, we supply (wherever possible) products containing hazardous substances only to commercial and industrial customers
-
We develop innovative alternatives to standard market products containing hazardous ingredients
LCAs for Dispersions and Dispersible Polymer Powders
In a pilot project carried out during 2010, WACKER POLYMERS prepared life cycle assessments (LCAs) for key intermediates and for dispersions and dispersible polymer powders belonging to our VINNAPAS® , VINNEX® and ETONIS® brands. This means that there are now life cycle assessments for all of WACKER POLYMERS’ major product families. Our LCAs look at the environmental impact caused by a specific product family throughout its life cycle – a “cradle-to-gate” assessment extending from manufacturing to the factory gate. The analyses allow us to assess the sustainability of our products and production processes, and improve them accordingly.
Social Commitment
Companies can only be successful if they have society’s trust. Consequently, we take our social responsibilities seriously, especially toward communities near our sites. We attach particular importance to young people’s scientific and technical education. We will need committed scientists and engineers in the future if we are to remain competitive. In 2010, we acted as sponsor and organizer of the state-wide “Young Scientist” competition in Bavaria for the seventh time. We also again sponsored the Dresden/East Saxony regional heat of “Young Scientist.”
In 2010, the Technical University of Munich (TUM) set up the TUM University Foundation. WACKER supported this sponsoring body with an initial donation of €250,000. In the future, the charitable foundation will aid research projects of outstanding merit, provide grants, and help cut through the red tape whenever leading academics are recruited from abroad.
Children’s Charity “Die Arche” Supported Again
A further social priority consists of projects to help children and young people. Since 2007, WACKER has supported a German religious charity, “Die Arche” (The Ark), which aids children and young people from socially disadvantaged families in several German cities. It provides the children with hot meals and extra tuition, organizes leisure activities and offers counseling. In 2010, WACKER again made a donation of €100,000 to the charity’s Munich branch.
WACKER’s relief fund, which helps the victims of disasters, supported three projects in 2010:
Haiti
In response to the Caribbean country’s dire situation, Wacker Chemie AG donated an initial €50,000 to the Group’s relief fund and pledged to match all employee donations. With more than €125,000 now raised, the relief fund will assist the “Don Bosco Dritte Welt” aid organization in rebuilding a destroyed elementary and high school in Gressier. The new school will offer around 350 places for boys and girls aged 6 to 18.
Pakistan
Torrential monsoon rains in northwest Pakistan in July 2010 caused flooding accompanied by mudslides and landslides. Many thousands were killed. Houses and crops were destroyed. Over 20 million people are believed to have been directly affected. WACKER’s relief fund has joined forces with Malteser International to rebuild an elementary school in the Swat district. The new school building is intended for around 250 girls. Wacker Chemie AG made an initial donation of €50,000 towards this project.
Sri Lanka
WACKER’s relief fund has been helping tsunami victims since 2005. Our employees’ donations have been used to rebuild schoolhouses in Kosgoda and to finance the teaching of four classes. The fund has pledged to extend its commitment beyond 2011. The aim is to support students through to their diplomas. To this end, the fund staged another donation campaign at its global sites in December 2010.