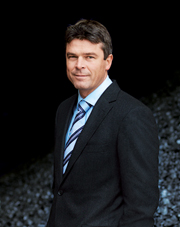
Torbjørn Halland is in charge of the Holla plant. A trained metallurgist, the 41-year-old was responsible for the site even before WACKER took it over. The enthusiastic skier likes to spend his free time with his family in the local mountains.
Raw Materials
Picture a white ship at a quayside, set against a backdrop of rolling hills and the deep-blue waters of Hemnefjord. The idyll is deceptive – because, here, eight hours’ drive north of Oslo, it’s all go. Workers are busily unloading tons of quartzite from cargo ships onto a conveyor belt that wends its way into vast storage depots. Faster! Faster! Don’t keep the production lines waiting at Holla Metall, they operate around the clock! Acquired by WACKER in July 2010, this Norwegian plant produces high-quality silicon metal in a complex process involving quartzite, coal and wood chips. Holla Metall’s output of 50,000 metric tons per year is enough to cover one-third of WACKER’s annual needs.
A Volatile Market
Some 2,000 kilometers further south, in Burghausen (Germany), Dr. Markus Kuhnlein points to a chart. “We need silicon as a raw material for 80 percent of our sales. Having our own production plant has greatly enhanced supply security,” says the procurement manager, who is responsible for silicon supplies groupwide. “We decided to opt for backward integration along the raw-material chain because the silicon market is so volatile. During the 2009 economic crisis, many manufacturers temporarily halted production and, now, they’re struggling to keep pace with rising demand,” says the 50-year-old. “Holla has made us more independent of market and price fluctuations.”
Securing Procurement Long Term
Holla Metall’s acquisition was one of the first major assignments facing Raw Materials Procurement (RMP). WACKER set up this corporate department back in 2008 to segregate raw materials and energy from other sourcing processes. “As a result, we’ve been able to optimize our purchasing terms, establish new supplier relationships and increase supply security – all vital achievements, since global competition for key raw materials is intensifying rapidly,” stresses Dr. Christian Hartel, who heads the new corporate department.
A 24-strong team of purchasing specialists handles vast sums of money. Hardly surprising, as raw materials and energy account for roughly half WACKER’s procurement volume of €2.8 billion. WACKER has defined three procurement categories for raw materials and energy. “We’ve developed and implemented long-term strategies for the first category, which covers our basic raw materials – silicon, ethylene, methanol, acetic acid and vinyl acetate – plus electricity and natural gas,” explains Hartel, showing us a presentation outlining WACKER’s procurement strategy. “We rely on a broad, global supplier portfolio with long-term contractual conditions. Additionally, we purchase precisely when prices are at their most favorable.”
The second category comprises 50 to 60 key strategic materials (such as catalysts). Although volumes are far lower here, the materials are of great strategic importance for WACKER. The company procures them primarily through multiyear framework contracts, but also adopts a flexible approach and sometimes makes purchases at short notice. “The third category contains a further 1,500 raw materials, which are often readily available. The great majority can be sourced in standardized processes under framework contracts,” says Hartel, who has a Ph.D. in chemistry.
Supply Security Is Paramount
How does WACKER achieve its procurement goals? Methanol is a case in point, especially as WACKER ranks among Europe’s top-ten consumers of this alcohol. Shipped by rail from Antwerp and Rotterdam to Burghausen, methanol is sourced from at least four suppliers, none delivering more than one-third of WACKER’s annual needs of 240,000 metric tons. “We stagger our contract durations (one to three years) so that two contracts expire each year,” adds Hartel. “This enables us to adapt contracts to reflect the market conditions affecting both parties. As a result, we can negotiate attractive prices and delivery conditions.”
Raw Materials from Neighbors
Raw-material procurement processes vary greatly and so are difficult to compare. Hartel illustrates this for ethylene, which WACKER converts into acetic acid. “The challenge here is that ethylene transportation is both complex and very expensive,” explains Hartel. Consequently, the Group sources this volatile, highly flammable gas primarily from a Burghausen neighbor – OMV – which produces the ethylene by cracking crude oil derivatives. WACKER has long-term contracts with OMV and, unlike for silicon, there would be no sense in the Group’s obtaining its own ethylene production facility. “You’d need to be using an awful lot of ethylene to justify building a cracker,” says Christian Hartel. Ethylene procurement is changing, too, though. “In fall 2011, we’ll be hooked up to the Northwest European ethylene pipeline. That will potentially broaden our supplier base and increase our supply security.”
Quality Makes All the Difference
Back up in Norway, Holla Metall employees have few concerns about being able to transport the silicon they produce. Since Hemnefjord never freezes over, transport routes are secure. Instead, the focus is on improving production processes because, with silicon, the devil is in the detail. “In 99.5 percent of cases, the product delivered is identical, whoever supplies it,” says Torbjørn Halland, site manager at Holla Metall. A handful of silver-gray chunks runs through his fingers. “But that half of one percent makes all the difference. Silicon contains roughly ten minor elements, such as aluminum, calcium and iron. Their quantity and distribution define the quality of the raw material.”
Since WACKER bought silicon from Holla even before the acquisition, the plant’s 140 employees are well aware of their new employer’s quality demands. “We need to maintain the same material quality from delivery to delivery,” explains Halland, “so that high-tech polysilicon production processes, for example, function smoothly, as well.” Halland is in no doubt that the whole Group stands to benefit from backward integration. And that goes for procurement, too: “Our expertise will support WACKER both in producing its own supplies and in sourcing silicon from third-party companies around the globe.”
Characteristics
On a grand scale: in 2010 WACKER purchased some €590 million worth of silicon, ethylene, VAM and methanol.
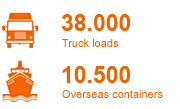
From Raw Material to Product
In Burghausen alone, the raw materials supplied produced about 700,000 metric tons of finished goods. That’s enough to fill 38,000 truck loads and 10,500 containers.
Securing Raw Materials
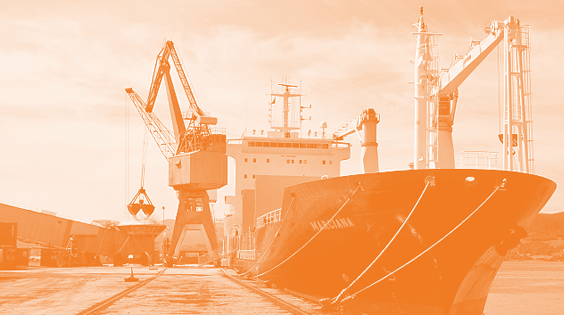
The acquisition of Holla in Norway has made WACKER more independent of market and price fluctuations, thus securing the long-term supply of silicon metal – the Group’s key raw material.
Holla’s production capacity of some 50,000 metric tons per year thus enables WACKER to cover about a third of its annual demand.
The Key Raw Materials
and Their Prices
Si Silicon |
C2H4 | CH3OH Ethylene/Methanol |
VAM Vinyl Acetate Monomer |