Energy
Energy Targets: Lowering Specific Energy Consumption by 2022
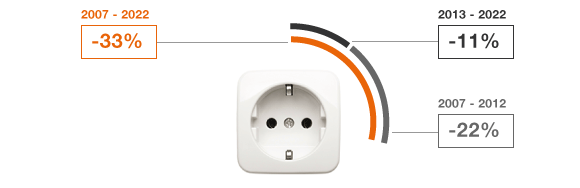
The chemical industry is an extremely energy-intensive sector. In Germany alone, it uses around 20 percent of all the power consumed by industry. WACKER, too, is therefore constantly improving the energy efficiency of its processes. This enables us to remain competitive in the world market, while contributing to climate protection. Many chemical reactions generate heat that can be put to use in other production processes. We have been using integrated heat-recovery systems in Burghausen and Nünchritz for years and are continually improving them. In this way, we can reduce the amount of primary energy (normally natural gas) that our power plants consume.
To further improve energy efficiency and lower specific energy consumption (amount of energy per net production volume), the Executive Board has defined energy targets for WACKER Germany. We already cut specific energy consumption by 22 percent between 2007 and 2012. A further reduction of 11 percent between 2013 and 2022 is now the target. Overall, by 2022, we will have brought our specific energy consumption down by one-third.
These energy goals also ensure we meet a requirement for ISO 50001 Group certification. We certified the energy management system for WACKER Germany to this standard in 2012.
Saving Energy with POWER PLUS
We have been pushing ahead measures to increase productivity and lower energy consumption since 2007 through our POWER PLUS energy efficiency program. In this program, our energy analysts scrutinize our production plants. At the same time, our employees are encouraged to make energy-saving suggestions.
The mandatory “Energy Management” training course (German-language only) gives employees tips on saving energy in production and in the office. In addition, employees learn the basics of energy management.
With regard to energy-saving ideas, Idea Management supports POWER PLUS: improvement suggestions submitted in the “Energy/Utilities” category, which was added in 2011, are not only sent to the reviewing experts via the intranet, but are also automatically forwarded to Energy Management. When this measure was first introduced in 2011, only 50 of the 8,220 submitted ideas were energy-related. The initiative bore fruit as early as 2012: of the 8,982 submitted ideas, 411 suggestions (5 percent) were entered in the “Energy/Utilities” category. Information provided by the “Energy Management” online training course contributed to this increase. The (German-language) training course can be accessed via the intranet and has been mandatory for employees in Germany since 2012.
One new tool used by our energy managers is the “energy cascade,” in which computer simulations are used to compare the current energy consumption of production plants with the theoretical optimum, and to identify the sources of energy losses. In 2012, it was used to determine potential electricity and heat savings for three plants at WACKER’s Burghausen site.
Energy Cascade
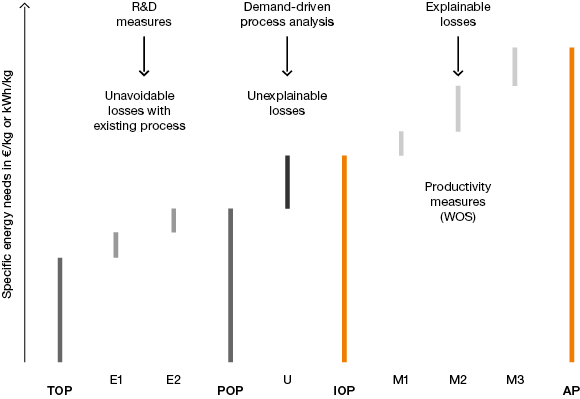
TOP = Theoretical Optimum Process
POP = Practical Optimum Process
IOP = Identified Optimum Process
AP = Actual Process
E = Explainable
U = Unknown
M = Measure
Generating Energy Efficiently
Burghausen uses hydroelectric power to generate electricity. Our Norwegian site, Holla, too, generates its electricity from water power. Our primary source of energy, though, is climate-friendly natural gas. At WACKER’s large Burghausen and Nünchritz sites, we produce steam and electricity in cogeneration systems. These combined heat and power (CHP) plants have more than 80-percent fuel efficiency, which is significantly higher than that of conventional plants, where electricity and heat are generated separately.
Hydroelectric Power
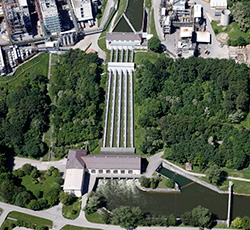
The Alzwerke power station has been supplying the Burghausen site with hydroelectric power since 1922.
The Burghausen site has been supplied with electricity from Wacker Chemie AG’s “Alzwerke” hydroelectric facility for over 90 years. From December 1922 to December 2012, this power station generated 22,132 GWh of electricity.
The Alz canal between Hirten on the Alz River and Burghausen on the Salzach River made it possible to harness the water – which plunges 63 meters into the turbines – for a hydroelectric power plant on the banks of the Salzach. The electricity generated by the Alzwerke plant was the key prerequisite for the chemical industry to settle in Burghausen. Over the past nine decades, the hydroelectric facility has continuously increased its energy yield and availability over 24 hours.
In 2012, our Nünchritz site required around 86 percent less process steam from its CHP plant to manufacture one metric ton of product than it did in 1999, when WACKER acquired the site. We converted our Nünchritz power plant from heavy fuel oil to more ecologically sound natural gas in 2006.
Saving Energy with WOS
In 2012, we improved the energy efficiency of our Burghausen power plant with the help of a project that forms part of our WOS (Wacker Operating System) program. Following a thermal study, we re-insulated a steam boiler. This saves around 540 MWh heating steam a year. We also insulated those external parts of the power plant which the study had identified as weak points for energy loss. This allows us to use hot water more efficiently, equivalent to 200 MWh of energy saved per year.
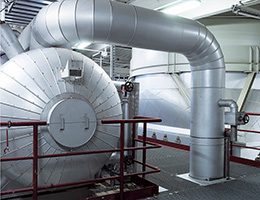
We have improved the energy efficiency of Burghausen’s CCGT (combined-cycle gas turbine) power plant with new thermal insulation.
The following are further examples of WOS projects with which we increased energy efficiency during the period under review:
- WACKER SILICONES hooked up a pair of distillation columns to form a heat-recovery system in Burghausen, which saves us around 80,000 metric tons steam per year.
- By raising the efficiency of WACKER POLYSILICON’s trichlorosilane production in Burghausen, we save over 20 MWh electricity per year.
- During the period under review, WACKER POLYSILICON enhanced its poly deposition process in Burghausen. This allows us to save almost 30 MWh electrical power per year.
Energy Consumption
In 2011, WACKER’s electricity consumption rose to 4.4 million MWh (2010: 3.8 million MWh). This was caused by the high capacity utilization of our production operations and the launch of polysilicon production at Nünchritz. In addition, a full year’s consumption of our silicon-metal production plant in Holla, Norway, which was acquired in June 2010, was included for the first time in 2011.
This rise in demand continued in 2012, when WACKER increased its electricity consumption further, to 4.6 million MWh. This was due to higher polysilicon production. The Group’s power plants – the hydroelectric and CHP (gas and steam turbine) generating stations in Burghausen and the CHP in Nünchritz – produced around 1.6 million MWh in 2012 (2011: 1.5 million MWh). This means that WACKER covered about a third of its total electricity needs itself. Groupwide, carbon dioxide emissions – of which around 60 percent in 2012 (2011: 64 percent) result from captive power plants that are subject to emissions trading rules – totaled about 1.3 million metric tons in the period under review.
In 2012, WACKER’s German production sites accounted for 76 percent of its electricity needs (2011: 73 percent). In Germany, we purchased enough electricity from utilities to cover 55 percent of our electricity requirements there (2011: 53 percent). In line with the utilities’ primary energy sources, 60 percent of this electricity was generated from fossil fuels (2011: 58 percent). 24 percent came from nuclear energy (2011: 20 percent) and 16 percent from renewable energy sources (2011: 22 percent). Heat consumption, which includes the use of solid fossil and biogenic fuels (coal, charcoal and wood) in silicon-metal production at Holla, Norway, fell slightly to 3.8 TWh (2011: 3.9 TWh).
Download XLS |
Energy Consumption | ||||||||||||
|
|
|
| |||||||||
TWh |
2012 |
2011 |
2010 | |||||||||
| ||||||||||||
|
|
|
| |||||||||
Electricity consumption |
4.6 |
4.4 |
3.8 | |||||||||
Heat consumption1 |
3.8 |
3.9 |
3.4 | |||||||||
Primary energy |
7.0 |
6.9 |
6.11 | |||||||||
Of which |
|
|
| |||||||||
Natural gas |
5.9 |
5.8 |
5.5 | |||||||||
Solid fuels2 (coal, charcoal and wood) |
0.9 |
0.9 |
0.4 | |||||||||
Heat (supplied by third parties)3 |
0.2 |
0.2 |
0.2 | |||||||||
Fuel oil |
0.02 |
0.02 |
0.01 |
Electricity Supply for the WACKER Group in 2012
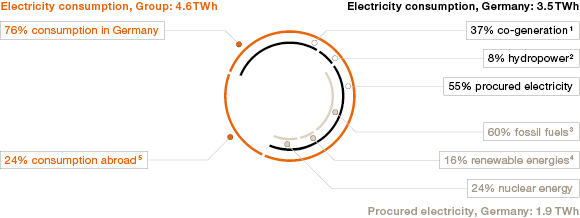
1 Burghausen and Nünchritz
2 Burghausen
3 Coal, lignite, oil and gas
4 Hydro, wind and solar power
5 Outside Germany, we purchase electricity from third parties based on the standard local energy mix