Idea Management
Ideas Submitted by WACKER Employees
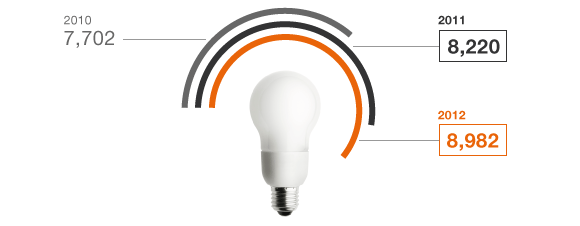
In order to do things better and stay competitive, WACKER relies on the ideas submitted by its employees. 2012 saw more employee suggestions than ever before. In total, we received 8,982 suggestions (2011: 8,220) – roughly 9.3 percent more than in the previous year. The participation rate (number of submitters per 100 employees) remained constant at 34 percent (2011: 34 percent). Our goal is still for every second employee to contribute ideas. Total benefits fell to €6.4 million (2011: €9.4 million). One of the reasons for the decline was that cost grounds prevented the measures from being implemented. In its annual idea management rankings for 2012, the German Institute of Business Administration (“dib”) put WACKER in ninth place among companies with more than 5,000 employees. That makes WACKER one of the most imaginative companies in Germany.
Since 1975, WACKER employees have submitted around 114,000 improvement suggestions. Over half of these – 62,000 suggestions – have been implemented, leading to company savings of €117 million. Submitters have received a total of €26 million in bonuses.
To maximize the benefits from ideas, WACKER has interlinked the Employee Suggestion Program, the Wacker Operating System (WOS) and Innovation Management.
Download XLS |
Idea Management | ||||||||
|
|
|
| |||||
|
2012 |
2011 |
2010 | |||||
| ||||||||
|
|
|
| |||||
Number of improvement suggestions |
8,982 |
8,220 |
7,702 | |||||
Total benefits (€ million) |
6.4 |
9.4 |
11.9 | |||||
Participation rate1 (%) |
34 |
34 |
33 |
Pleasant Climate for Saving Energy
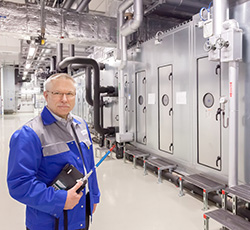
Savings potential can often be found where it is least expected. One example of a hidden energy guzzler is the supply of conditioned air. “To air-condition our rooms, we must first cool and dehumidify the air before regulating its temperature and moisture content as required,” says Georg Stemmer, energy coordinator at Siltronic. All this costs energy – and not too little, either. At Siltronic’s Burghausen site alone, there are more than 500 air-conditioning systems, which are responsible for over 25 percent of the site’s overall electricity consumption. Fortunately, there are employees who walk through their workplace with open eyes. One such employee noticed that a disused etching facility was still being supplied with fresh air and that the exhaust air was still being extracted. This much ventilation is not necessary for a facility that is no longer in service, which is why the air flow has now been restricted with flaps. Cost savings: a five-digit sum every year.
The air conditioning of work areas has savings potential, too. Instead of maintaining the exact same temperature and atmospheric humidity at Burghausen’s multi-wire sawing facility throughout the year, the employees had an idea: increase the temperature by one degree Celsius at higher humidity in the summer and decrease it by one degree at lower humidity in the winter. The difference is hardly noticeable for the employees, but clearly visible on Siltronic’s electricity bill. This reduced heating and cooling effort also leads to savings of a five-digit sum every year.