Product Stewardship
Research and Development
WACKER’s research and development follows three goals.
- Firstly, we search for solutions that meet our customers’ needs and contribute to their market success.
- Secondly, we optimize our processes in order to be the technology leader and to operate sustainably.
- Thirdly, we concentrate on creating innovative products and applications for new markets and on tapping into megatrends – such as higher energy requirements, urbanization, digitization and growing prosperity.
Research along the Supply Chain
WACKER takes environmental, and health and safety criteria into account at every stage of the product life cycle – every research and development project examines the sustainability aspects of our new products and processes, starting with the raw materials used. We try to minimize raw-material consumption, while selecting materials that offer maximum ecological benefit. Here are a few examples:
- In the period under review, WACKER POLYMERS launched projects to free its product portfolio of poorly biodegradable substances.
- Another key objective at this division was to continue enhancing the production processes for VINNAPAS® dispersions and dispersible polymer powders. That conserves raw materials and energy. We have made improvements in our production processes for vinyl acetate monomer (VAM) and for vinyl acetate-ethylene (VAE) dispersions.
WACKER continually strives to optimize its processes – their efficiency, environmental aspects, energy consumption and costs. For instance, our WACKER POLYSILICON division optimized the workflows in its closed production loop during the period under review. We increased the purity of polysilicon through improved production steps and continued to reduce energy consumption during deposition and conversion.
Environmental Assessments
Our products are generally supplied to business customers for further processing – not to end customers direct. Cradle-to-gate assessments, however, are partial LCAs which look at the environmental impact of products from the moment of manufacture to the time they reach the factory gate. They allow us to gage the sustainability of our products and production processes, and to improve them accordingly. Having launched life cycle assessments at WACKER POLYMERS in 2010, we extended these to further business divisions during 2011. Our goal is to establish this tool throughout the Group.
Our LCA data for VINNAPAS® brand VAE dispersible polymer powders (vinyl acetate-ethylene copolymer) have been incorporated into the Environmental Product Declaration project conducted by Deutsche Bauchemie (German Association of Construction-Chemical Manufacturers).
We compiled life cycle assessments on various dispersions, such as polyvinyl acetate and VAE dispersions for a project run by the European Polymer Dispersion and Latex Association (EPDLA). The EPDLA operates under the mantle of the European Chemical Industry Council (CEFIC).
WACKER took part in a 2012 study conducted by the European Silicones Centre (Centre Européen des Silicones; CES). This study looked at the entire product life cycle of silicones and related products, such as silanes. It addressed two aspects: the CO2 emissions generated during the production of silicones and the CO2 savings accruing from their use. It found that the use of silicones reduces the carbon footprint of many major products by a factor of 9. At 54 million metric tons of CO2 a year, this saving is equivalent to the emissions arising from heating 10 million homes.
We have introduced a tool to evaluate systematically the risks and opportunities of our product line from an environmental perspective. This WACKER® Eco Assessment Tool factors in the material, water and energy consumption of a product, as well as its ecotoxicity, over the entire life cycle. We have already used it to assess some product families and we will be widening its scope to include others.
Product Life Cycles
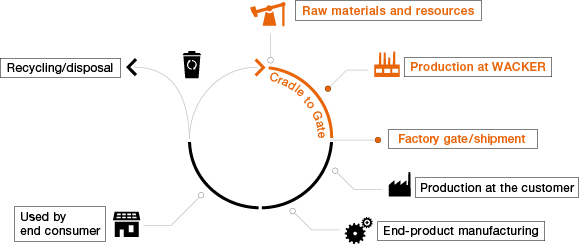
Research and Development at Two Levels
WACKER conducts R&D at two levels: centrally at our Corporate Research & Development department and locally at our business divisions. Corporate R&D coordinates activities on a company-wide basis and involves other departments, such as engineering (during process development). We also use a portfolio-management process to keep our R&D project portfolio transparent throughout the Group. In 2012, we enhanced the Project System Innovation (PSI) program we use to manage our innovation portfolio. The improvements include better risk recognition and a greater focus on sustainability. Now, when we do research on new products, we also systematically examine the use of materials, energy and water, and we assess ecotoxicity over the entire product life cycle.
WACKER Wins Best Innovator Award
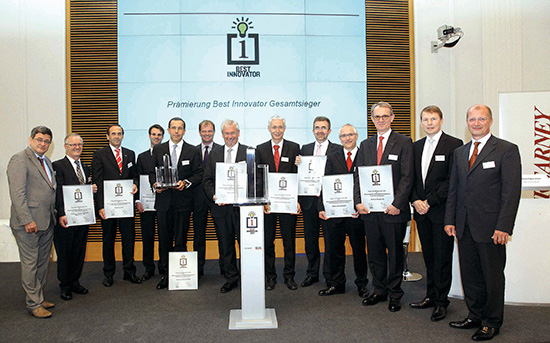
WACKER took first place in the Chemistry category of the 2011 Best Innovator Award for its sustainable innovation management. Management consultants A.T. Kearney and German business weekly “WirtschaftsWoche” organized the competition, which attracted more than 100 companies. The jury confirmed that WACKER had introduced systematic processes and operated innovation management as a core area of expertise. An important point in the jury’s assessment was that WACKER installed technology managers, who monitor the entire supply chain and manage the company’s innovation effort in the technology and customer segments.
WACKER scientists are currently working on around 260 topics based on more than 40 technology platforms. More than a quarter of the topics address strategic key projects in fields ranging from energy, construction, automotive engineering, to household and personal-care products, food and biotechnology. In 2012, they accounted for 45 percent of total incurred project costs of €77 million (2011: 45 percent of €78.9 million).
Strategic Collaboration with Customers and Research Institutes
Our business divisions conduct application-driven R&D. They focus on product and process innovations relating to semiconductor technology, silicone and polymer chemistry, and biotechnology, as well as on new processes for producing polycrystalline silicon. To achieve successful research results more quickly and efficiently, we collaborate with customers, scientific institutions and universities. In 2012, WACKER worked with more than 56 international research institutes on around 59 research projects (2011: 25 institutes and 64 projects). In a further 60 research projects – or one quarter of all our research projects – we are collaborating closely with customers, usually on the basis of collaboration agreements.
Our collaborative efforts cover topics such as electricity storage, biotechnology, process simulation and materials research for renewable energy production. Two sample projects are given below.
- In the field of lithium-ion batteries, Central R&D is working with various institutions, including the University of Münster. In 2011, we joined the German Network of Competence for Lithium Ion Batteries (KLib) (German-language link only).
- Siltronic AG and imec, a Belgian nanoelectronics research institute, signed an agreement in 2011 to collaborate on the development of silicon wafers with a gallium nitride layer (GaN-on-Si). This makes us an affiliate member of the imec Industrial Affiliation Program (IIAP). The aim of the project is to make possible the production of next-generation solid-state illuminants (e.g. LEDs) and power semiconductors on 200 mm silicon wafers.
Technical Competence Centers for our Customers
WACKER has also created a global network of 22 technical competence centers that liaise between sales offices and local production sites. Specialists in these centers customize products to regional requirements, taking account of climatic conditions, national standards and local raw materials, for example. They develop formulations for customers’ new products as well as optimize existing recipes.
Transferring Knowledge Locally
Our WACKER ACADEMY locations serve as a collection of forums for industry-specific knowledge transfer between customers, distributors and WACKER experts. The focus is on industry-specific courses, which now cover silicone applications in addition to polymer chemistry, such as for cosmetics and paints. The training centers’ proximity to our development and test laboratories promotes the sharing of ideas and enables participants to conduct practical on-site tests. We work with company research facilities, universities and institutes to ensure our seminars remain state of the art.
Research and Development Spending
WACKER ranks among the world’s most research-intensive chemical companies. In 2012, the Group spent €174.5 million on R&D (2011: €172.9 million). The R&D rate – research and development spending as a percentage of Group sales – was 3.8 percent, slightly above last year’s figure. The bulk of R&D costs were incurred in the development of new products and production processes.
Breakdown of R&D Spending
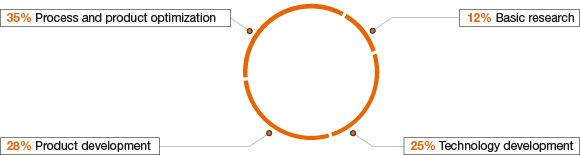
Publicly Funded Research Projects
Some of our research projects in 2011 and 2012 were subsidized by government grants. In 2012, these totaled €2.3 million (2011: €2.8 million). Sample projects are outlined below.
- Under the joint MAINPAGE project, the German Federal Ministry for the Environment, Nature Conservation and Nuclear Safety (BMU) funded a subproject of WACKER POLYSILICON and Siltronic. In MAINPAGE, we conduct research on innovative new materials for industrial photovoltaic applications with enhanced energy efficiency.
- Our participation in the National Platform for Electric Mobility (German-language link only) (NPE, a joint initiative run by the German government and industry) has resulted in a number of collaborative projects involving our Central R&D facility (Consortium). Some of these projects are publicly funded, one example being the SafeBatt project to develop lithium-ion batteries that are fireproof and protected from explosion (making them intrinsically safe), which is supported by the Federal Ministry of Education and Research (BMBF). Another example is the alpha-Laion project funded by the Federal Ministry of Economics and Technology (BMWi), in which we conduct research on high-energy lithium batteries for electric vehicles.
- In the EPoSil project, WACKER SILICONES is developing electrically-active silicone-based polymers for energy production. This is another project funded by the BMBF.
- In Germany’s joint SPINEL project (aimed at boosting the energy efficiency of photovoltaic and electronic applications through innovative electronics-grade base material), the Federal Ministry of Education and Research (BMBF) is subsidizing a Siltronic subproject.
- We are researching electrode materials for lithium-sulfur batteries for the LiSSi project sponsored by the BMBF. We are developing such fourth-generation high-capacity lithium-ion batteries jointly with project partners for electric mobility applications.
- WACKER is working on two subprojects within the integrated Carbon Capture, Conversion and Cycling (iC4) (German-language link only) project funded by the German Aerospace Center (DLR). The first is focused on the separation and cleaning of CO2 in order to prepare it for additional use. The second is researching catalysts for converting CO2 into hydrocarbons.
Our business divisions and Central R&D have also applied for government research grants totaling €2.5 million for further projects that are still in the approval phase. Our externally-funded research projects are coordinated through our Grant Management office, which evaluates candidate programs, submits our project proposals and manages contacts with funders.
Researchers and Developers at WACKER
In 2012, 1,008 employees were engaged in research and development in Corporate R&D and across the business divisions. That represents 6.2 percent of the Group’s workforce.
We recognize the dedication of our researchers by presenting them with awards. For their seminal work on silane synthesis, WACKER honored two of its Corporate R&D scientists with the 2011 Alexander Wacker Innovation Award. The two researchers developed a novel analytical method that, for the first time, permits observation of processes which occur during the fluidized-bed synthesis of silicone precursors by the Müller-Rochow method. With this knowledge, WACKER can further improve its production processes and thus save millions in costs. 2011’s €10,000 Innovation Award focused on basic research.
In recognition of a product innovation at WACKER POLYMERS, three of the division’s employees were presented with WACKER’s 2012 Alexander Wacker Innovation Award. These researchers developed novel dispersions based on vinyl acetate-ethylene copolymers that are used for coating various materials. A noteworthy feature of these coatings is that they make the print on cardboard packaging particularly durable and vivid. Compared with acrylate-based products, the two VINNAPAS® dispersions EF 101 and EF 575 offer customers an alternative technology with significant cost advantages.
A team of inventors from the Siltronic division topped the “Most Important Invention” category in the 2011 Inventor Award. This carries a cash prize of €10,000. The team found a way of improving processes that would boost the quality of epitaxial wafers. Defect-free wafers save material and energy and save Siltronic millions in costs every year.
The “Most Important Invention” category in the 2012 Inventor Award again went to a Siltronic employee, who modified the process chambers of epitaxy reactors to make deposition more efficient. This boosted throughput by 10 to 15 percent, and yielded annual savings in the tens of millions of euros.
Selected Research Topics
In the energy sector, we continued our activities in electricity storage and conversion. We are working on materials used in lithium-ion batteries to enhance this type of battery for automotive and consumer-product applications. We are also focusing on lightweight construction, as lighter materials can be used to conserve raw materials and energy, for instance in the automotive and aviation industries. In these fields, we are developing building blocks for composites. We have developed silicone products that lend themselves to hydroelectric power generation.
Today, technological innovation requires better and better materials – plastics that can be produced cost-efficiently and can withstand extreme temperatures without becoming brittle. In other words, components that offer higher performance yet are still lighter in weight. Often, there is a need for properties that cannot be realized in a single material. The solution here is VENTOTEC®. This powder-form additive is composed of spherical particles that have a low-modulus silicone core and a hard outer shell of organic polymer. Only small quantities of VENTOTEC® are needed to increase the toughness of the hardened resin significantly. Because the silicone particles retain their elasticity down to around -130 °C, this effect remains intact even at very low temperatures. VENTOTEC® is suitable for wind turbines and was launched on the market in the period under review.
WACKER BIOSOLUTIONS optimized its ESETEC® process for pharmaceutical proteins. We conducted a feasibility study of how to produce a PASylated human growth hormone in high yield. (PAS denotes the amino acids proline, alanine and serine collectively.) PASylation® technology enables the development of biopharmaceuticals that are more compatible, longer lasting and do not have to be administered as frequently. Using the ESETEC® secretion system, we developed a process for an antibody fragment for the FAB (Fragment Antigen Binding) product class for a customer project in 2011, which is now being clinically tested. The antibody fragments are used in therapeutic projects and for diagnostic research purposes.
We have identified new cyclodextrin applications in areas such as dairy products and reduced-fat foods, and received European Commission approval to use gamma-cyclodextrin as a food and beverage ingredient. The addition of cyclodextrin can mask a bitter taste in green-tea products, for example. Cyclodextrins enhance the bioavailability of ingredients such as curcumin and coenzyme Q10.
Sustainable Products
WACKER products are generally supplied to businesses for further processing, rather than to end customers. Our customers want us to produce these intermediates in a sustainable way. Plus, they expect their products to pose no risks to health or the environment. WACKER’s policy is to provide high-quality products that can be manufactured, transported, used and disposed of safely, with minimum environmental impact.
Over the last two years, WACKER has developed diverse products that promote sustainability. Examples are presented below for the megatrends of energy, urbanization, digitization and rising living standards.
Energy
Polysilicon: Energy-Generating Solar Installations
Polysilicon is a hyperpure material that has been purified by the distillation of trichlorosilane, deposited as rods and crushed into chunks for further processing. Our customers use it to produce crystalline solar wafers to make solar modules for installation on roofs, for example.
In 2012, WACKER sold over 38,000 metric tons of hyperpure polysilicon, making it one of the world’s largest producers. 2012 also saw the official start-up of polysilicon expansion stage 9 at Nünchritz (Germany). To improve the energy balance of solar cells and lower our costs, we make every effort to reduce energy consumption in polysilicon production.
The energy payback time – the time taken for a photovoltaic cell to generate the energy used in its production – has become even shorter. Depending on the geographical location of the solar cells, this payback time now ranges from 6 months (in the Sahara) to 18 months (in northern Europe). Each metric ton of polysilicon used in solar modules prevents the emission of 6,000 tons of CO2.
Silicone Elastomer Protects Photovoltaic Modules
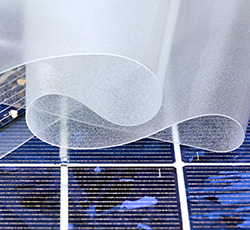
Our Corporate R&D department developed TECTOSIL® for encapsulating photovoltaic modules. Approved by Germany’s TÜV inspection authority, the film comprises a unique silicone elastomer that can be thermoformed, making it fast and easy to process. The film protects solar cells against mechanical and chemical stress and contains no corrosive components. The material absorbs hardly any water at all, presents an effective moisture barrier and stays permanently electrically insulating. TECTOSIL®, which showed early market promise in 2011, thus ensures that solar modules are of high quality and have a long lifetime.
Download XLS |
Selected Products – Energy | ||||||
|
|
|
| |||
Product |
Description |
Application |
Sector | |||
|
|
|
| |||
ELASTOSIL® Solar 2200 |
Transparent, pourable, non-corrosive silicone elastomer |
Encapsulant for flexible thin-film modules |
Solar industry | |||
TECTOSIL® 177 |
Thermoplastic silicone elastomer |
Encapsulant for photovoltaic modules |
Solar industry | |||
WACKER® SILICONE PASTE P 250 and P 300 |
Silicone lubricant pastes, free of boron-containing additives |
Fitting of cable accessories |
Transmission and distribution (T&D) industry | |||
POWERSIL® 570 PLUS |
Solvent-free silicone coating |
Coating of electrical insulators |
Transmission and distribution (T&D) industry | |||
ELASTOSIL® LR 3170/40 |
Self-adhesive, flame- resistant liquid silicone rubber |
LED sockets for flatscreen monitors, seals in solar installations, insulation in electric cars |
Automotive, electronic and solar industries | |||
VENTOTEC® |
Impact modifier |
Rotor blade bonding |
Wind turbines |
Dispersible Polymer Powder for Building Insulation: Energy-Efficient Construction
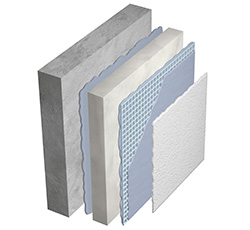
Modern ETICS/EIFS for building insulation consist of a multilayered material composite. But it takes the addition of a dispersible polymer powder to create a permanently stable insulation system.
VINNAPAS® dispersible polymer powder ensures adhesive mortar adheres to the walls and the insulation employed in ETICS/EIFS systems. The dispersible polymer powder boosts adhesion and impact resistance within the base coat. Hydrophobizing VINNAPAS® polymer powders, in particular, ensure that there is no moisture in the top coat.
There is enormous potential for using exterior insulation and finish systems (EIFS) / external thermal insulation composite systems (ETICS) to permanently reduce greenhouse-gas emissions. Heating and air-conditioning account for half of a building’s energy demand. Inadequately insulated houses lose a large part of their energy through exterior walls. An ETICS/EIFS system will cut a building's heating costs by as much as 50 percent.
The German Energy Agency (dena) has calculated the savings potential that can be achieved using insulation alone. While over 10,000 kilowatt hours of heating energy escape through the walls of an uninsulated detached house each year, this can be reduced to just 2,200 kilowatt hours if the external walls are insulated.
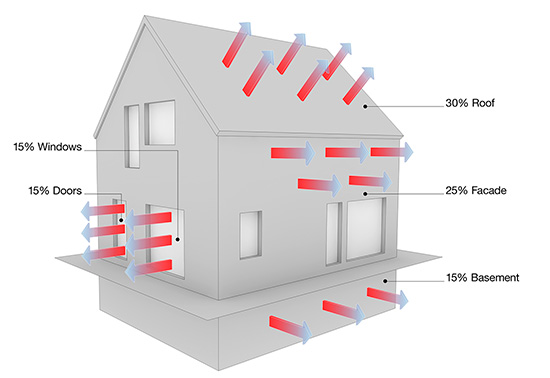
Indoor heat escapes through the roof, exterior walls and basement of uninsulated buildings. According to the German Energy Agency (dena), as much as 80 percent of this heat loss could be prevented by proper renovation of the building envelope and modern construction technology.
According to Germany’s EIFS/ETICS trade association (Fachverband WDVS) (German-language link only), some 840 million square meters of EIFS/ETICS were installed in Germany alone before 2009, which generated savings of almost 140 billion liters of heating oil or comparable fossil fuels, equivalent to a reduction of 700 million metric tons of CO2 emissions.
Block of Ice Defies the Summer Heat
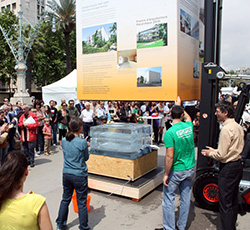
Unveiling the ice block in Barcelona: thanks to the ETICS/EIFS, 800 kilograms of the original 1,000 kilograms of ice withstood the heat of the Catalonian summer.
WACKER took part in an unusual bet in Barcelona in the summer of 2011. A solid block of ice weighing 1 metric ton was encased in an ETICS/EIFS system. This was then left outside in the summer heat for two weeks as part of an energy-efficiency exhibition. Visitors were encouraged to guess how much ice would be left when the exhibition closed its doors for the last time.
Summer temperatures in Barcelona can easily hit 35 °C. So, the question was: how much ice would be left when the exhibition was over? Guesses ranged from 50 to 1,000 kilograms. Thanks to ETICS/EIFS, the temperature inside the large packing crate remained at a constant 5 °C throughout the two weeks, with the result that barely 20 percent of the ice melted. Around 800 kg of ice survived the Catalonian summer heat for the two weeks of the exhibition, which ran from July 8 to 21, 2011.
Using a computer simulation, the Institute for Energy Efficiency (TBZ), an international charitable association for disseminating and promoting sustainable building practices, demonstrated that, without the ETICS/EIFS, three times as much ice would have melted during the course of the wager. The Spanish WACKER team thus provided a clear demonstration of the typical efficiency achieved with ETICS/EIFS in passive houses. These stay cool in summer and warm in winter, without the need for air-conditioning systems. That helps to save electricity and to lower CO2 emissions.
Download XLS |
Selected Products – Energy-Efficient Construction | ||||||
|
|
|
| |||
Product |
Description |
Application |
Sector | |||
|
|
|
| |||
VINNAPAS® 5044 N, VINNAPAS® 5048 H and VINNAPAS® 4042 H |
Dispersible copolymer powders based on vinyl acetate and ethylene, intended for neutral or water-repellent applications in the construction sector |
Ideal for use in ETICS/EIFS |
Construction industry | |||
SILRES® BS 5137 |
Aqueous, low-viscosity silicone fluid emulsion |
Impregnation of mineral wool |
Insulation and construction industries |
Urbanization and Construction
Dispersions for Environmentally Sound Paints
VINNAPAS® dispersions are used, among other things, as binders for interior-wall paints. Dispersions made without APEO-based surfactants (alkylphenol ethoxylates) and containing just minute amounts of volatile organic compounds (VOCs) prove to be particularly ecofriendly. Keeping the VOC level in interior wall paints below 1 gram per liter ensures a pleasant, healthy indoor climate.
Silicone Resin Emulsion Paints: Long-Lasting Facade Protection
SILRES® BS products based on quartz-like structures protect exterior paints and plasters. The facades stay attractive for longer and are better insulated, thereby boosting energy efficiency. Silicone resin emulsion paints (SREPs) are permeable to water vapor and so help to improve the climate indoors.
A coat of high-quality silicone resin emulsion paint reduces heat loss from external walls by as much as 40 percent. Heat is lost faster from wet walls – the role of the silicone resins is to help keep the walls dry. A coating of SREP decreases heat demand by an average of 4.6 percent. Silicone resin emulsion paints and silicone resin plasters lengthen the intervals between renovations of facades by up to 25 years. Some listed buildings cannot be insulated with ETICS/EIFS. In such cases, a silicone resin emulsion paint is one of the few materials that will improve a building’s energy balance.
Dispersible Polymer Powders for Tile Adhesives, Flooring and Insulation Systems
VINNAPAS® dispersible polymer powders permit the use of insulation boards comprising different materials, including renewable substances, such as cork and wood-wool. They reduce the amount of material needed in tile adhesives. These powders can also be used to make construction chemicals that meet valid environmental standards, such as the EMICODE® emissions standards set by Germany’s GEV (Association for the Control of Emissions in Products for Flooring Installation).
Download XLS |
Selected Products – Ecofriendly Construction | ||||||
|
|
|
| |||
Product |
Description |
Application |
Sector | |||
|
|
|
| |||
VINNAPAS® 5111 L |
Dispersible polymer powder with a very low VOC content (volatile organic compounds) |
Extremely smooth, self-leveling flooring compounds and grouts; certified to EMICODE® EC1+ and the Blue Angel eco-label |
Construction industry | |||
VINNAPAS® EF8300 |
Dispersion as a binder |
Binder for low-emission interior paints |
Coatings and construction industries | |||
GENIOSIL® W |
Hybrid polymer-based liquid membrane; is virtually odorless and has no labeling requirements under German hazardous substances legislation (“GefStoffV”) |
Waterproofing of surfaces in buildings, such as flat roofs, balconies, patios and basement walls |
Construction industry | |||
VINNAPAS® EAF 68 |
Binder for floor-covering adhesives without the addition of alkylphenol ethoxylates (APEOs) |
Universal binder for floor coverings, ranging from hard-to-bond floor coverings such as linoleum or polyvinyl chloride (PVC) to easy-to-handle carpeting |
Adhesives industry | |||
VINNOL® CEN 2752 |
Dispersion with a high vinyl chloride and reduced formaldehyde content |
Binder for coating textiles and nonwovens, particularly to obtain flame-resistant finishes, e.g. in upholstery, flooring coverings (such as PVC and needlefelt) and heat-sealable wadding materials |
Textiles and nonwovens industry | |||
GENIOSIL® XB |
Adhesive binder (hybrid polymer) with no content of plasticizer, solvent or tin catalysts |
Structural adhesives for wood, glass, metal and ceramics |
Adhesives and sealants industries, construction | |||
SILRES® IC 368 |
Liquid, solvent-free silicone resin intermediate |
Enhances properties of industrial coatings for wood, metal and sheet-metal strips |
Paint and coatings industry | |||
SILRES® BS POWDER S |
Highly efficient, water-soluble hydrophobic additive |
Greatly reduced water uptake in gypsum applications |
Building materials, construction industry | |||
ELASTOSIL® Catalyst NEO |
Tin-free catalyst for two-part, room-temperature-curing silicone rubber grades |
Moldmaking and encapsulation |
Artesanal manufacturing workshops, mold collections, restorers, institutes |
New Product Innovation Award for GENIOSIL®
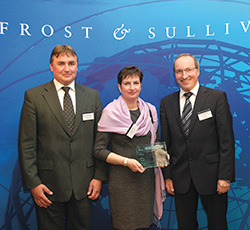
WACKER received Frost & Sullivan’s 2011 New Product Innovation Award in the Construction category for its GENIOSIL® product class. The alpha-silane technology in GENIOSIL® products allows the production of powerful adhesives and sealants free of plasticizers and solvents, such as joint and cabinet sealants and assembly adhesives. GENIOSIL® is also used in automotive and container construction, as well as to bond wood (parquet) flooring.
Composites from Recycled Material
WACKER offers novel composites for indoor use called natural fiber composites (NFCs). These enable the production of innovative floor and wall coverings made of natural fibers such as cork, leather, wood and slate. Not only that, but scrap can be used as well.
The floorings based on natural cork, Indian slate and VINNEX® binder feature a millimeter-thin, slate-sheet surface whose reverse side is a thin and warming cork layer to balance out unevenness in the stone. Moreover, the insulating cork fibers dampen the sound of footsteps. The stone surface is fireproof, very stable and hard-wearing, making it suitable for entrances, lobbies (e.g. hotels) and areas around hearths, stoves and open fireplaces.
Plus, VINNEX® powder binders can be used to treat leather-processing scraps and convert them into workable materials. The recycled leather can serve in the manufacture, for example, of durable floor tiles. To this end, the cutting waste from the leather industry is compressed to pellets and processed with VINNEX® to yield leather sheeting. Applications include furniture and wall coverings, flooring, as well as panels used in car interiors (for side trims or center consoles, for instance).
These new materials help to conserve resources and to use raw materials efficiently. This innovation earned WACKER, along with its partner BADER GmbH & Co. KG, the 2011 MATERIALICA Design + Technology Award in the CO2 Efficiency category.
Digitization
Wafers are cut from a silicon ingot. They are then used to produce chips for electronic devices. Sensors, power devices, microcontrollers and other electronic chips make sure that modern electric appliances and hybrid and electric vehicles are safe and economical.
The efficiency of semiconductor devices doubles about every two years. Among the key performance-boosting parameters are the design rules achieved on a silicon wafer. They determine how many transistors fit on a device per square centimeter.
Today, the semiconductor industry’s standard design rules are 32 and 22 nanometers (nm). In the coming years, they will decrease to 16 and eventually 11 nm. We are developing processes to produce 300 mm wafers that are used for 16 and 11 nanometer design rules. The first 16 nm products are in customer approval processes. We have evaluated the technology for 11 nm wafers and produced the first experimental products.
Rising Living Standards
When devising our strategic goals, we take our cue from global megatrends – including rising living standards, particularly in emerging markets. We intend to keep up with these trends by offering products which we make in energy- and resource-efficient processes. For example, with silicones for construction, for textiles, electronics and medical technology. With polymers for the paper and packaging industries, for example. And with cyclodextrins for the food and agricultural sectors. To this end, we launched new products made with sustainable ingredients in the period under review. A selection of these is given below.
Download XLS |
Selected Products – Silicones | ||||||
|
|
|
| |||
Product |
Description |
Application |
Sector | |||
|
|
|
| |||
ELASTOSIL® N 9111 |
Tin-free, general-purpose adhesive and sealant |
Bonding, sealing and coating of ceramic hobs, electric-cooker screens and control elements, and microwave-oven windows |
Household-appliance, automotive and electronics industries | |||
ELASTOSIL® LR 3011/50 FR |
Flame-retardant liquid silicone rubber |
LED sockets for flatscreen monitors, seals in solar installations, insulation in electric cars |
Automotive, electronic and solar industries | |||
ELASTOSIL® E 91 and ELASTOSIL® E 92 N |
Tin-free, condensation-curing silicone rubber grade |
Textile coatings, with good adhesive and non-slip properties; compatible with Öko-Tex® Standard 100 |
Textile industry | |||
ELASTOSIL® LR 3066 |
Food-grade liquid silicone rubber with low surface friction |
Dispensing valves for food technology |
Food and packaging industries | |||
SILPURAN® UR |
High-purity specialty silicones |
Long-term medical applications, such as port catheters, voice prostheses, gastric bands, pacemakers, and disk, joint and hearing implants |
Medical technology | |||
SILPURAN® 4200 |
Biocompatible silicone adhesive |
Adhesive and sealant for medical applications |
Medical technology | |||
SILPURAN® 6610/40 |
Biocompatible, radiation-resistant liquid silicone rubber |
Radiation-sterilizable silicone valves for medical devices |
Medical technology |
Download XLS |
Selected Products – Polymers | ||||||
|
|
|
| |||
Product |
Description |
Application |
Sector | |||
|
|
|
| |||
VINNAPAS® EP 8010 |
Vinyl acetate-ethylene (VAE) copolymer dispersion |
Water-based adhesives for paper products and packaging; enable plasticizer-free paper and packaging adhesives that comply with EU regulations on food-contact materials |
Packaging and adhesives industries | |||
VINNOL® H 30/48 M |
Surface-coating resin with excellent solubility in pure ester without the addition of ketones |
For packaging required by thermosensitive pharmaceuticals and foodstuffs, such as cheese and yoghurt |
Industrial coatings, packaging industry | |||
VINNOL® H 5/50 |
Polymer with elastic properties |
Binder for formulating without plasticizers; e.g. for printing inks in sterilizable food packaging |
Industrial coatings, |
Download XLS |
Selected Products – Cyclodextrins | ||||||
|
|
|
| |||
Product |
Description |
Application |
Sector | |||
|
|
|
| |||
CAVAMAX® W6 |
Alpha-Cyclodextrin as a purely plant-based, bioengineered emulsifier for stabilizing oil-in-water emulsions for the food industry |
Emulsifier for foods, such as salad dressings, mayonnaises, cream-based desserts, and margarine |
Food industry | |||
CAVAMAX® W6 |
Alpha-Cyclodextrin as water-soluble fiber |
Fiber for beverages and foods, such as dairy products, bakery products and cereals |
Food and beverage industries |