Prevention
Workplace Accidents1 Involving Permanent Staff and Temporary Workers
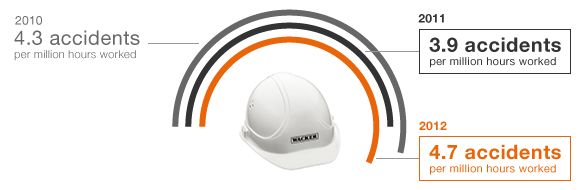
1 Accidents leading to at least one day off work
Managing plants and processes in a way that poses no risk to people or the environment is an important objective at WACKER. We therefore operate a groupwide safety management system that covers both workplace safety and plant safety. Our processes and workplace safety standards will be aligned with international standard OHSAS 18001 by 2015. Good workplace safety practice requires regular risk assessments and workplace monitoring.
Risk Management
The first step in ensuring plant safety is to identify the risks systematically and then assess them. This includes analyzing how well we control the energy (e.g. pressure, heat) existing in a process and determining what influence an individual fault might have on a chain of events leading up to a failure or accident. On completion of this comprehensive analysis, we specify safety measures that will prevent undesirable incidents.
Our “ANSIKO” plant safety project on dust-explosion protection was completed in 2011. In this project, we reviewed all the Group’s safety plans for facilities with a dust-explosion risk. The recommended improvements were then implemented. A follow-up “ANSIKO” project on machine safety was launched in the reporting period. Its goal is to identify machinery that poses a risk of injury, review safety plans for such machinery and, where needed, recommend additional measures to protect employees. The project was introduced to German plants in 2012 and has been extended to non-German production sites since mid-2013.
The expansion of polysilicon production at Nünchritz involved a corresponding upgrade of the site’s emergency-response procedures. Now, should an emergency occur, detectors will quickly recognize releases of hazardous gases, sirens and loudspeaker broadcasts will warn local residents, and signaling will divert traffic away from all roads in the vicinity. The plant fire department has been strengthened with new full-time firefighters and additional equipment (including a new, ultramodern turbo-extinguisher). The future WACKER site in Charleston, Tennessee, will be subject to the same safety standards that govern the Group’s other sites, including emergency-response procedures. For this reason, a new turbo-extinguisher has been acquired for this site, too.
Safety Training & Employee Motivation
WACKER is a firm believer in providing ongoing training for its safety experts, and holds regular training sessions, for example, on plant safety and explosion protection. Safety training at WACKER sites outside Germany is organized by specialists from the Group. In 2011, experts from all Asian production sites met in China to share information and attend training sessions. We also conducted safety audits at our sites in South Korea and China. A year later, the safety experts from all production sites met in Burghausen, Germany. We formed a committee (the “Expert Committee on Plant and Process Safety”) to organize advanced training in site and process safety issues. We conducted health and safety audits at production sites in Japan, Norway and the USA in 2012.
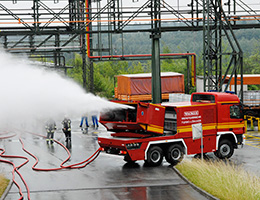
Once a year, the plant fire departments at our largest sites carry out emergency drills, during which state-of-the-art turbo-extinguishers are used.
But it is not only our safety experts who regularly go on courses. All our employees are given safety training specific to their individual workplace, e.g. in the form of e-learning courses. WACKER Germany, for example, offers 43 online training courses on workplace safety. Topics range from general safety guidelines for office and laboratory workers to instruction on working with respirators and hazardous materials. Each instruction module contains tests that enable participants to assess their progress. In China, WACKER held a safety day at all its sites, the first event of its kind there. During the event, three-fourths of the targeted employees participated in training sessions, presentations and plant inspections.
WACKER also has a great interest in ensuring that employees travel safely between their home and workplace. It organized a traffic-safety day for HQ employees in 2011 when they had an opportunity to expand their road-safety knowledge and try out their road-safety skills.
In 2012, the groupwide accident rate (number of workplace accidents with missed work days per 1 million hours worked) was 4.7. The corresponding figure in 2011 was 3.9. This result puts us behind those chemical companies that lead the way in occupational safety. In 2011 and 2012, for example, Bayer, BASF, Dow, Evonik and Henkel collectively had an average of 1.2 workplace accidents with missed workdays per 1 million hours worked. However, in terms of reportable accidents (accidents with more than three missed workdays), WACKER’s numbers are far better than the German chemical industry average. The reportable accident rate in 2012 was 2.1 per 1 million hours worked, while the chemical sector within Germany’s BG RCI (the statutory employer liability insurance carrier of the basic materials and chemical industries) registered 9.5 such accidents in chemical companies.
During the reporting period, there was not a single fatal workplace accident among WACKER employees. Unfortunately, however, one did occur at a partner company. At our Charleston site (Tennessee, USA), two construction workers in the process of laying concrete were caught by loose formwork and fell to their deaths. Construction at the site was temporarily suspended while a detailed investigation took place, as a result of which the partner company tightened up its safety precautions.
Very few of the accidents at our sites are chemical in nature. The most common causes are tripping, slipping, falling, and inattentiveness during manual activities. Not satisfied with our accident rate, we are redoubling our occupational-safety efforts. We are systematically implementing our new safety program – WACKER Safety Plus (WSP), which incorporates successful safety elements from sites that have particularly low accident rates. Such elements include safety patrols, discussions with the workforce and emergency drills. WACKER Safety Plus has the goal of recognizing and avoiding unsafe behavior – on the way to and from work, in the office, at the plant, in the operation of machinery, or in the handling of chemicals. We organized WSP seminars for executives at all of our German production sites in 2012. These were attended by 850 executives.
Download XLS |
Workplace Accidents Involving Permanent Staff and Temporary Workers | ||||||||||
|
|
|
| |||||||
|
2012 |
2011 |
2010 | |||||||
| ||||||||||
|
|
|
| |||||||
Accident rate across Group: accidents1 |
4.7 |
3.9 |
4.3 | |||||||
Accident rate in Europe |
5.3 |
4.9 |
5.1 | |||||||
Accident rate in the Americas |
4.3 |
1.7 |
2.8 | |||||||
Accident rate in Asia |
1.2 |
0.6 |
0.8 | |||||||
Accident rate across Group: reportable accidents2 |
2.1 |
1.4 |
1.2 | |||||||
Fatal workplace accidents |
− |
− |
– |
Practiced Safety
Low accident figures are a reflection of safety-conscious conduct. At WACKER, we give special recognition to facilities that operate for sustained periods of time without a reportable accident. Some of these have also been honored by institutions outside the company.
The WACKER POLYMERS site in Calvert City (US state of Kentucky) received an impressive two awards in 2011 for its high safety standards and many years of accident-free operations. The first was the Governor’s Safety and Health Award, which honors employers and employees who meet a required number of hours without workplace injuries serious enough to cause an employee to miss work. The second was the ACA Safety Award, won for the third year in a row, and presented by the American Coatings Association (ACA). The ACA Safety Award recognizes the commitment of those of its members who had no lost days to report due to workplace accidents.
20 Years without an Accident – Thanks to Cleanliness and Tidiness
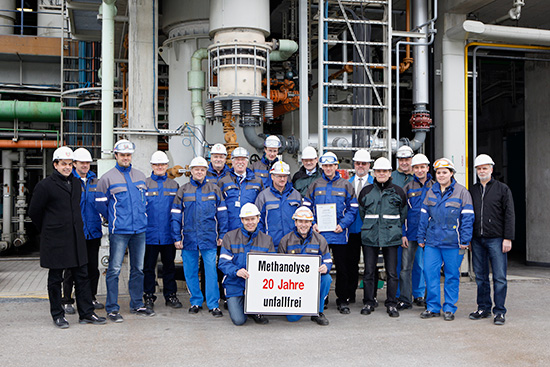
In 2011, the 34 employees at the Burghausen methanolysis plant celebrated 20 years without an accident. There have been no reportable accidents at the plant, which hosts some key processes in WACKER SILICONES’ base chemicals operations, since November 1991. The substances processed or arising in the plant, including methylchlorosilanes and hydrogen chloride, are potentially highly dangerous and corrosive. “Cleanliness and tidiness in the workplace are a matter of course for us,” explained facility head Stephan Beutlhauser. Regular training courses are also held to increase safety awareness and sharpen the employeesʼ vision, hearing and smell.
Download XLS |
Safety Awards 2011/2012 | ||||
|
|
| ||
Award |
Recipient |
Sponsor | ||
|
|
| ||
Recognition Award 2012 |
WACKER POLYMERS, |
Ulsan City Administration/Korea Gas Safety Corporation | ||
Safety Award 2011 |
WACKER POLYMERS, |
South Korean Ministry of Labor & Korea Occupational Safety and Health Agency (KOSHA) | ||
Governor’s Safety and Health Award 2012 |
WACKER POLYMERS, |
Governor of the US state of Kentucky | ||
Governor’s Safety and Health Award 2011 |
WACKER POLYMERS, |
Governor of the US state of Kentucky | ||
ACA Safety Award 2011 |
WACKER POLYMERS, |
American Coatings Association (ACA) | ||
Group Award 2011 |
SILMIX® Ohio |
Ohio Bureau of Workers’ Compensation | ||
100 % Award 2011 |
SILMIX® Ohio |
Ohio Bureau of Workers’ Compensation |
Transport Safety
WACKER ensures that its products are safely stored and transported. Before loading vehicles, we carry out stringent checks on them, especially if they are carrying hazardous goods. In 2012, we inspected more than 6,600 trucks at our German sites (2011: more than 6,000). If a vehicle fails inspection, we continue sending it back until it passes. The failure rate has been low for years now. In 2012, the figure for transporting hazardous goods in Germany was 2.2 percent (2011: 3.6 percent). WACKER audits hazardous goods shippers at least every two years.
We believe that well-trained personnel are an important element of transport safety. In each of 2011 and 2012, we instructed over 1,000 employees throughout the Group in classroom seminars on activities relating to the handling of hazardous goods. Some 1,500 completed at least one of the online training courses on offer.
Aside from the mandatory monitoring of hazardous-goods shipments, WACKER also tracks the transport of non-hazardous goods. WACKER safety standards are often higher than the minimum legal requirements on the shipping of hazardous materials. Whenever possible, these goods are preferentially shipped to customers by rail rather than by truck, using special safety rail tankers or shipping containers that meet the strictest safety standards.
We regularly review aspects of transport safety with our logistics providers, e.g. during the annual Logistics Day. If deficiencies are found, we agree on improvements and then monitor their implementation. WACKER uses in-house criteria and internationally recognized systems, such as the Safety and Quality Assessment System (SQAS) operated by the European Chemical Industry Council (CEFIC), to select logistics service providers and evaluate their performance. Our evaluation criteria include drivers’ qualifications and training, vehicle equipment and accident response. By stipulating observance of standards and specifications, WACKER ensures that even the subcontractors working for our logistics providers meet our high safety requirements.
We recorded a total of 18 transport incidents in 2011 and 2012. This number includes not only accidents and incidents involving the distribution of our intermediates and products where we commissioned the transport, but also incidents that do not involve hazardous goods, as well as those that do not adversely impact on people or the environment. These incidents, too, form part of our shipper assessments.
Download XLS |
Transport Accidents | ||||||
|
|
|
| |||
Number of Accidents |
2012 |
2011 |
2010 | |||
|
|
|
| |||
Road |
8 |
6 |
4 | |||
Rail |
2 |
1 |
1 | |||
Sea |
– |
1 |
– | |||
Inland waterways |
– |
– |
– | |||
Air |
– |
– |
– |