Sustainability
Managing Sustainability
Sustainability has been firmly rooted in our business processes for many years. Its importance to our company is shown by the fact that we have made sustainability one of our five strategic goals and have compiled our own Code of Sustainability. Sustainable development means balancing economic, ecological and social factors in everything we do.
Two voluntary global initiatives form the basis for sustainable corporate management at WACKER: the chemical industry’s Responsible Care® initiative and the UN’s Global Compact. These voluntary measures to protect the environment, employees and society go beyond what is legally required. We also expect our suppliers to observe the principles of the UN’s Global Compact and the Responsible Care® initiative, and have anchored this in our general terms of procurement.
WACKER made substantial progress on strategic sustainability-management projects in 2016.
Regional Emphasis
In 2016, the regional focus of WACKER’s sustainability management activities was on Europe, where we examined environmental, health and safety aspects of individual sites, including the Stetten and Halle sites in Germany, as well as our silicon-metal plant in Holla, Norway.
Group Certificate
Our Group certification program ensures that customer-driven specifications and our corporate standards are implemented at all WACKER sites. Almost all WACKER production sites are included in the ISO 9001 (quality) and ISO 14001 (environment) Group certificates. Exceptions are Wacker Química do Brasil, the Kolkata plant belonging to Wacker Metroark Chemicals Pvt. Ltd., India, and the Tsukuba site of Wacker Asahi Kasei Silicone Co., Ltd., Tokyo, Japan. All these sites have corresponding individual certificates. After commissioning, the new plant in Charleston, USA, was also incorporated into the ISO 9001 Group certificate.
As of 2012, all German sites belonging to Wacker Chemie AG, Siltronic AG and Alzwerke GmbH have been certified to ISO 50001 (energy management systems). Wacker Biotech GmbH and DRAWIN Vertriebs-GmbH were successfully certified to this standard in the reporting period. The silicone-producing sites in Burghausen and Nünchritz (both Germany), Jandira (Brazil), Zhangjiagang (China) and Amtala (India) are certified to the ISO 22716 standard for the cosmetics industry.
Our Sustainability Report: Best in the Industry
In 2016, the Institute for Ecological Economy Research (IÖW) and the business initiative “future e.V.” published their ranking of corporate sustainability reports. Conducted on behalf of the German Federal Ministry of Labour and Social Affairs, the initiative has now evaluated the sustainability reports of the 150 largest German companies for the ninth time. The 2013 / 2014 WACKER Sustainability Report was ranked 11th, which represents an improvement relative to our last ranking (2011: 14 th place). It took the top spot in the chemical / pharmaceutical sector.
Analysis of Fundamental Sustainability Issues
Following up on the regular stakeholder surveys conducted as part of our sustainability reporting, we also interviewed our top management on fundamental sustainability issues for the first time in 2016. The result was that compliance, product safety and plant safety are the top three issues as seen by the company and stakeholders.
Workplace and Plant Safety
Operating plants and processes in a manner that poses no risk to people or the environment is an important objective at WACKER. To this end, we have installed a groupwide safety management system that addresses both workplace and plant safety. Systematic workplace safety includes regular evaluation of hazards and work-area monitoring. The first step in ensuring plant safety is to systematically identify risks and assess them. This includes analyzing how well we control the energy present in a process (e. g. pressure, heat) and determining the effect that a single error might have on a chain of events that could lead to the escape of a substance or to an accident. On completion of this comprehensive analysis, we specify safety measures to prevent undesirable incidents.
WACKER attaches particular importance to providing its safety experts with ongoing training. We hold regular training sessions on topics such as plant safety.
Our goal for occupational safety is to reduce our groupwide accident rate (the number of workplace accidents per million hours worked) to at least 1.7 by 2020. Groupwide, we registered 3.0 workplace accidents with missed workdays per 1 million hours worked in the reporting period. In terms of reportable accidents (accidents with more than three days of absence), WACKER’s numbers are far better than the German chemical industry average. The reportable accident rate in 2016 was 1.6. per 1 million hours worked, whereas in 2015, Germany’s BG RCI (the statutory employer liability insurance carrier of the basic materials and chemical industries) registered 9.4 reportable accidents per 1 million hours worked in chemical companies.
Workplace Accidents Involving Permanent Staff and Temporary Workers – Group
Download XLS |
|
|
|
||||||||||||
Number |
2016 |
2015 |
2014 |
2013 |
2012 |
|||||||||
|
|
|
|
|
|
|||||||||
|
||||||||||||||
|
|
|
|
|
|
|||||||||
Accidents1 per 1 million hours worked |
3.0 |
2.6 |
2.8 |
3.8 |
4.7 |
|||||||||
Reportable accidents2 per 1 million hours worked |
1.6 |
1.0 |
1.2 |
1.4 |
2.1 |
|||||||||
|
|
|
|
|
|
Safe Transport of Hazardous Materials
WACKER ensures that its products are safely transported and stored, especially if hazardous goods are involved. In 2016, we had inspections carried out on over 9,500 trucks. Failure rates have been low for years now. In 2016, the rate was about 1.3 percent for hazardous goods shipments in Germany (2015: 1.5 percent). WACKER regularly audits its hazardous goods shippers. Through the use of standards and specifications, WACKER ensures that even the subcontractors working for our logistics providers meet our stringent safety requirements.
In 2016, we recorded seven transport incidents. They include incidents that did not involve hazardous goods, whether or not they adversely impacted people or the environment.
For high-risk products, we use packaging and tanks that meet the highest quality standards – in some cases exceeding statutory requirements.
Commitment to Refugees
WACKER takes seriously its social responsibilities, especially in communities around our sites. Training young people in the natural sciences is especially important to us because we need dedicated scientists and engineers in order to remain competitive.
2016 saw us take the helm as statewide sponsor and organizer of the Young Scientists competition in Bavaria for the tenth time.
Since 2007, we have been a supporter of “Die Arche” (The Ark), a Munich-based Christian charity working with some 400 children and young people from socially disadvantaged families, including refugee children. In the reporting period, WACKER presented its tenth annual donation of €100,000 to the charity’s Munich branch.
WACKER’s Burghausen Vocational Training Center (BBiW) and SchlaU, a Munich education initiative focusing on refugees, began working together in 2016. The collaboration aims to help young refugees living in Bavaria’s Altötting district (home to our Burghausen site) learn German, and to find them suitable training places. In this effort, WACKER is funding the SchlaU initiative with a sum of €200,000 over six years. The BBiW, supported by SchlaU, launched a career orientation week for young refugees, which was attended by 18 adolescents. The BBiW accepted two refugees as business trainees in the reporting period. Of the twelve unaccompanied refugee minors cared for in the BBiW youth guest house, six started apprenticeships with local craftsmen.
In recognition of its refugee-themed trainee project, the plant in Nünchritz, Germany, was honored with the Companies for Tolerance award, which the “Arbeit und Leben Sachsen” organization presents to companies that actively promote integration, diversity and tolerance and take a stand against discrimination and racism.
WACKER HILFSFONDS: Helping Flood Victims
Parts of the Lower Bavaria region in Germany were hit by a once-in-a-millennium flood in June 2016. Many individuals and social institutions were affected, including WACKER employees. WACKER HILFSFONDS, the Wacker Chemie AG foundation for disaster aid, is assisting those affected in the region. In a donation campaign organized by the relief fund, WACKER HILFSFONDS raised approximately €156,000. With a matching contribution from the company, a total of some €312,000 was provided to assist the rebuilding effort. WACKER also made a separate donation of €100,000 in emergency aid for flood victims.
Environmental Protection
WACKER attaches particular importance to integrated environmental protection, which commences with product development and plant planning. Our environmental protection measures often surpass statutory requirements – in the spirit of the central idea behind the Responsible Care® initiative. WACKER constantly works on improving its production processes, with the aim of conserving resources. One of our main tasks is to close material loops and recycle byproducts from other areas back into production, enabling us to reduce or prevent emissions and waste.
Our commitment to environmental protection is visible in the awards we have won. For example, WACKER Greater China was once again presented with Shanghai’s Magnolia Silver Award in recognition of its contribution to the city’s sustainable development. The Safety Committee of the Zhangjiagang Free Trade Zone recognized the safety and environmental-protection measures of the WACKER production site in this zone. The City of Portland presented its Gold Sustainability at Work Certification to Siltronic’s US production site in honor of its sustainability activities. It also presented its Gold Compliance Award for the safe, sustainable operation of the Portland wafer production facility’s wastewater treatment plant.
In 2016, WACKER invested €5.5 million in environmental protection (2015: €5.7 million). In the same period, environmental operating costs amounted to €81.0 million (2015: €83.8 million).
Environmental Indicators from 2012 to 2016
Download XLS |
|
|
|
||||||||||||
|
2016 |
2015 |
2014 |
2013 |
2012 |
|||||||||
|
|
|
|
|
|
|||||||||
|
||||||||||||||
|
|
|
|
|
|
|||||||||
Air |
|
|
|
|
|
|||||||||
CO2 emissions1 |
|
|
|
|
|
|||||||||
Direct (kt) |
1,287 |
1,234 |
1,251 |
1,253 |
1,311 |
|||||||||
Indirect (kt) |
1,856 |
1,544 |
1,420 |
1,241 |
1,133 |
|||||||||
NOX nitrogen oxides (t) |
2,035 |
1,910 |
1,990 |
2,010 |
2,225 |
|||||||||
Non-methane volatile organic compounds (NMVOCs) (t) |
920 |
910 |
870 |
830 |
800 |
|||||||||
Total dust2 (t) |
517 |
389 |
494 |
658 |
591 |
|||||||||
|
|
|
|
|
|
|||||||||
Water |
|
|
|
|
|
|||||||||
Water consumption (thousand m3) |
231,858 |
237,060 |
241,973 |
220,908 |
242,072 |
|||||||||
Chemical oxygen demand (COD) (t) |
1,310 |
1,150 |
1,230 |
1,320 |
1,460 |
|||||||||
Halogenated organic hydrocarbons (AOX) (t) |
3 |
2 |
2 |
2 |
3 |
|||||||||
|
|
|
|
|
|
|||||||||
Waste |
|
|
|
|
|
|||||||||
Disposed of (t) |
43,590 |
46,490 |
51,570 |
39,210 |
41,340 |
|||||||||
Recycled (t) |
123,550 |
121,420 |
121,540 |
124,040 |
114,330 |
|||||||||
Hazardous (t) |
81,110 |
75,520 |
78,330 |
78,910 |
70,910 |
|||||||||
Non-hazardous (t) |
86,030 |
92,390 |
94,780 |
84,340 |
84,760 |
|||||||||
|
|
|
|
|
|
Water Consumption Tested Using the Global Water Tool©
We use the Global Water Tool© (GWT) developed by the World Business Council for Sustainable Development (WBCSD) to analyze the annual relative water stress index of the countries in which our main global production sites are located. This assessment has been conducted since 2012, based on analyses using the water stress index developed by the Water Systems Analysis Group of the University of New Hampshire, USA. This index provides information on the relationship between water consumption and the availability of renewable fresh water. The outcome of the analysis is that our most important production sites are located in regions with a low relative water stress index. These regions account for more than 97 percent of our annual water use and over 90 percent of our production volume. Production sites in countries for which no GWT-based water stress index information is available account for less than 0.5 percent of our water consumption.
As part of the Bavarian Environmental Pact, we joined with seven other companies from ChemDelta Bavaria to establish Naturnahe Alz (Natural Alz), an association through which we support the state of Bavaria in renaturalizing the Alz river and enhancing its ecosystem long-term.
Environmentally Relevant Projects at the Production Sites
In 2016, we cleaned up and repaired the roughly 17-kilometer Alz canal at the Burghausen site. Its water is used to generate power as well as supply cooling and process water for the Burghausen site. To ensure that the waterway ecology would not be compromised during the clean-up phase, we used a monitoring program to control the alternative intake of cooling and process water and the altered disposal of cooling / process water and wastewater. We used the Salzach river as an alternative source of cooling and process water. As the temperature of this water is much lower than that of the Alz canal, much less water was required.
COD effluent burdens rose as a result of the new polysilicon production plant in Charleston (TN, USA).
The increase in AOX (adsorbable organic halogen compounds) was caused by discharge from a company based at the Burghausen site entering WACKER’s captive sewer system; the discharged substance did not adversely impact the environment.
Commissioning of the Charleston site led to a 4.3-percent rise in direct emissions of carbon dioxide (Scope 1) groupwide.
There were two reasons for increased nitrogen oxide emissions (NOx): first, the new Charleston site; second, the legally required recording of emissions data at the Holla site in Norway involved a new measurement method.
Emissions of non-methane volatile organic compounds (NMVOCs) at Burghausen fell; groupwide, they rose slightly as a result of higher production volumes at the sites in Nanjing (China) and Ulsan (South Korea).
One of our environmental targets is to halve specific dust emissions per metric ton of product groupwide between 2012 and 2022. This mainly affects silicon-metal production at the Holla site in Norway, where modifications were made to filtration systems during the reporting year in order to reduce dust. Owing to this modification work, dust emissions rose temporarily during the official, four-week period of non-standard operations. If specific emissions are calculated solely for normal operations in 2016, it is apparent that the measures already taken have brought about an improvement of some 40 percent relative to the base year of 2012.
Our indirect CO2 emissions from procured energy (as per Greenhouse Gas Protocol Scope 2) rose to 1,855 kilotons (kt) in the reporting period (2015: 1,544 kt). The reasons for the increase were the commissioning of the Charleston site, and the temporary shutdown of the Burghausen power plant for maintenance work. We used energy-efficiency measures to reduce weighted specific energy consumption and related specific CO2 emissions – while maintaining a comparable product portfolio.
Measuring the Group’s corporate CO2 footprint is an important tool for improving climate protection. That is why we have been measuring our Scope 3 emissions since 2012 – in addition to our indirect greenhouse gas emissions from procured energy (in accordance with Greenhouse Gas Protocol Scope 2), which we have been tracking since 2011. Scope 3 emissions comprise all those generated along the supply chain, e. g. by suppliers or through waste disposal and the transport of products. In 2016, we once again provided this emissions data to the Carbon Disclosure Project (CDP), which WACKER joined in 2007. Founded in London in 2000, CDP is a not-for-profit organization working to achieve greater transparency in greenhouse gas emissions. Wacker Chemie AG’s performance profile was rated B (on a scale from A to D) in CDP’s annual sustainability ratings.
Product Stewardship
WACKER takes environmental, health and safety aspects into consideration at every stage of the product lifecycle. In research and development projects, we examine the sustainability aspects of our new products and processes, starting with the raw materials used. We try to minimize raw-material consumption while selecting materials that offer maximum ecological benefit. Our products are generally supplied to business customers for further processing – not directly to end customers. Our lifecycle assessments (LCA s) look at the environmental impact caused by a specific product family throughout its lifecycle – a “cradle-to-gate” assessment extending from manufacturing to the factory gate. They allow us to gage the sustainability of our products and production processes, and to improve them accordingly. Our evaluations factor in the material, water and energy consumption of a product, as well as its ecotoxicity, over the entire lifecycle. With the help of the WACKER EcoWheel®, we identify key sustainability topics and, together with our customers, set priorities for research projects.
Product Lifecycles
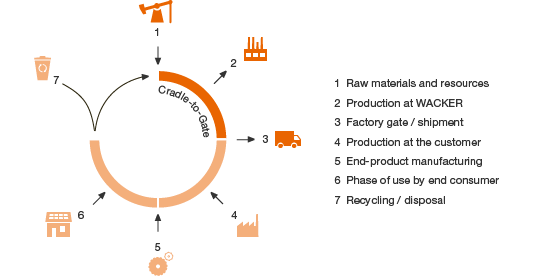
Energy Management
The chemical industry is one of the most energy-intensive sectors. In Germany alone, it uses around 20 percent of all the electricity consumed by industry. Wacker Chemie AG consumes 4,103 GWh of electricity in Germany, representing approximately 0.8 percent of the country’s electricity consumption. WACKER is continually improving the energy efficiency of its processes. This enables us to remain globally competitive while at the same time contributing to climate protection.
Many chemical reactions generate heat that can be put to use in other production processes. We have been using integrated heat-recovery systems in Burghausen and Nünchritz for years and are continually improving them. In this way, we can reduce the amount of primary energy (natural gas) consumed by our power plants.
To enhance energy efficiency and reduce specific energy consumption (amount of energy per unit of net production output), the Executive Board has defined energy targets for WACKER Germany. Our original goal was to reduce weighted specific energy consumption by one-third between 2007 and 2022, but we had already achieved that by 2014. We have now set a goal of reducing specific energy consumption to half of the 2007 level by the year 2022.
Generating Energy Efficiently
One way in which Burghausen generates electricity is by using hydroelectric power. Our Norwegian site, Holla, also generates its electricity mainly from water power.
Our primary source of energy, though, is climate-friendly natural gas. At Burghausen, our largest site, we produce steam and electricity using a cogeneration system. The highly efficient combined heat and power (CHP) plant operates at more than 80-percent fuel efficiency, which is significantly higher than that of conventional power plants generating electricity and heat separately.
WACKER’s German production sites accounted for 71 percent (2015: 78 percent) of its total electricity needs. We have taken energy-efficiency measures to reduce specific energy consumption even further in 2016. The Group’s power plants – the hydroelectric and CHP plants in Burghausen and the cogeneration plant in Nünchritz – produced around 1,416 GWh of electricity in 2016 (2015: 1,451 GWh). This means that WACKER uses environmentally friendly processes to cover roughly 25 percent of its total electricity needs itself. Groupwide, carbon dioxide emissions from captive power plants subject to emissions trading rules and from silicon-metal production in Holla (Norway) totaled about 1.0 million metric tons in the reporting period (2015: 1.1 million metric tons).
Electricity Supply
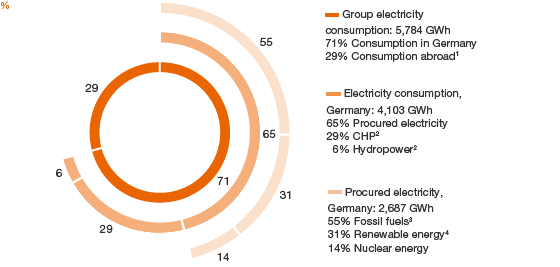
1Outside Germany, we purchase electricity from third parties based on the local standard energy mix
2Burghausen
3Coal, lignite, oil, gas; modified calculation method: since 2014, data has been in line with Germany’s energy mix; source: BDEW (German Association of Energy and Water Industries); status as of Nov. 2015, for the year 2014
4Hydro, wind, solar power; modified calculation method: since 2014, data in line with Germany’s energy mix; source: BDEW (German Association of Energy and Water Industries)
WACKER is subject to the regulations of the EU emissions trading system because of its CHP plants at the Burghausen and Nünchritz sites. We have covered shortfalls since 2014 by buying emission allowances for facilities subject to emissions trading.
Energy Consumption
Download XLS |
|
|
|
||||||||||||
GWh |
2016 |
2015 |
2014 |
2013 |
2012 |
|||||||||
|
|
|
|
|
|
|||||||||
|
||||||||||||||
|
|
|
|
|
|
|||||||||
Electricity consumption |
5,784 |
5,147 |
4,926 |
4,521 |
4,519 |
|||||||||
Heat consumption |
3,947 |
3,520 |
3,571 |
3,709 |
3,734 |
|||||||||
Primary energy use (total) |
6,464 |
6,062 |
6,081 |
6,176 |
7,030 |
|||||||||
Of which |
|
|
|
|
|
|||||||||
Natural gas |
5,420 |
5,029 |
4,975 |
5,051 |
5,927 |
|||||||||
Solid fuels1 |
769 |
768 |
839 |
872 |
862 |
|||||||||
Heat supplied by third parties2 |
258 |
245 |
242 |
236 |
223 |
|||||||||
Fuel oil |
17 |
20 |
20 |
17 |
18 |
|||||||||
|
|
|
|
|
|