Silicones – Our Business at a Glance
The age of silicones began at WACKER on August 2, 1947, making the chemical company Europe’s first silicone producer. Today, silicones account for over a third of WACKER’s total sales of €5.4 billion.
Raw Material from Holla
Silicone production requires one thing in particular: silicon metal. It is the most important raw material after methanol. WACKER’s production site in Holla, Norway, meets about a third of our total demand. The remainder is purchased on global markets. Captive production has key advantages, making WACKER slightly less dependent on price trends.

~ €10 Billion
Silicone Market
The silicone market is polarized. Accounting for 35 percent of the market, Dow Corning is currently the largest silicone manufacturer capable of producing its own raw materials. WACKER ranks second with 17 percent, just ahead of Momentive. WACKER is world No. 1 in a variety of application fields, such as building protection. The value chain operated by the largest silicone producers with backward integration amounts to around €10 billion.
Breakdown of Sales
WACKER SILICONES has been steadily increasing its sales for years. 2016 was the first time that its sales surpassed the two-billion-euro mark.
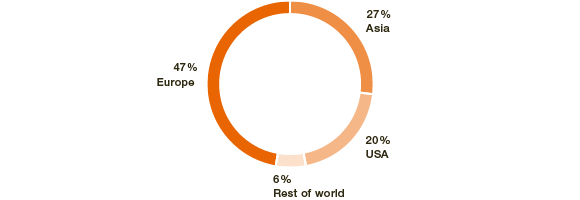
27%
Sales in Asia
WACKER SILICONES generates somewhat less than 30 percent of its sales in Asia, making it the second-largest market after Europe. Our silicone business in India and Southeast Asia grew at a particularly fast rate in 2016. Rising living standards in emerging Asian markets are fueling demand for high-quality products that contain silicone.
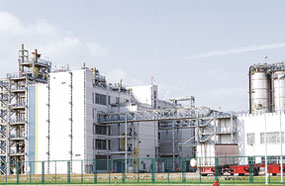
WACKER operates 26 production sites around the world, 12 of which belong to the integrated production network run by WACKER SILICONES. Located in Europe, Asia and the Americas, these sites supply global growth markets. The company’s Burghausen and Nünchritz sites in Germany and Zhangjiagang in China play a key role. They make sales products, as well as silanes and siloxanes, which are key upstream and intermediate products. The division’s fully integrated production system is unique, making it possible to treat byproducts and return them to the production cycle, where they are processed into value-added sales products.
22
Technical Competence Centers
Our technical centers are based locally to enable us to develop tailored market solutions – a service that benefits silicone customers as well. Every country has its own distinct raw materials, processing conditions, applications, legal regulations and standards, not to mention consumer expectations. WACKER’s silicone experts adapt products accordingly and show customers how to get the most out of silicones. WACKER ACADEMY regularly provides training at our technical centers, with courses designed for sales staff, customers, distributors and universities.
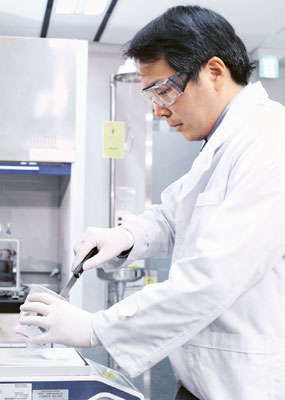
3,000
Products
Turn two into seven and then into 3,000: that’s silicone production at WACKER in a nutshell. WACKER uses two raw materials – silicon metal and methanol – to make 3,000 different silicone products in seven product lines: silanes, siloxanes, silicone fluids and emulsions, elastomers, resins, pyrogenic silica and, the most recent addition to the WACKER SILICONES family, organofunctional silanes.
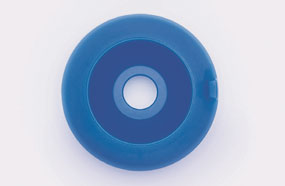
Nearly a third of WACKER employees work at the company’s largest business division, most of them in research, technical support and production. Almost 60 percent of them are based in Germany. Investments and expanding sales markets, especially in Asia, are causing the number of employees based outside Germany to rise at an above-average rate.
The Group’s largest silicones research laboratory facility is in Burghausen. In this facility, which occupies an area of 4,200 square meters, we develop silicone film, encapsulants, coatings, silicone gels and surfactants for the next generation of products. WACKER SILICONES’ technical support and quality control units are among the departments that use a number of laboratories there.