“Together, we have achieved pandemic readiness in Germany in record time.”
Germany is ready. In the event of another pandemic, vaccine production is guaranteed – thanks to the collaboration between CordenPharma and WACKER. The German government signed preparedness agreements with the two companies in 2022, showing that lessons had been learned from the COVID-19 pandemic.
Once the contracts had been awarded, the two companies embarked on a mammoth project with an ambitious deadline: they had just two years to achieve “pandemic readiness” and an annual production capacity of 80 million mRNA (messenger ribonucleic acid) vaccine doses. Should the need arise, the Center for Pandemic Vaccines and Therapeutics (ZEPAI) acting for the Federal Ministry of Health will contact the developer of the specific vaccine required. WACKER and CordenPharma will then jointly produce it. That is the plan.
“We want to continue to grow at WACKER. Our biotechnology business plays a crucial role here.”
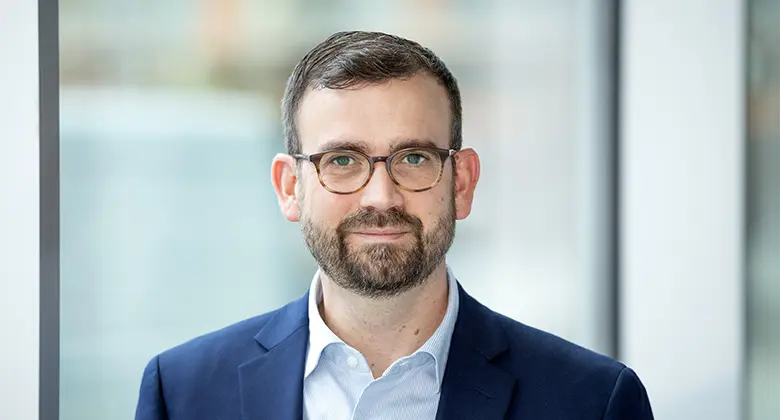
Working in tandem to cover the entire process chain
“It was a challenge that none of us had ever faced before,” recalls Andreas Anton, who heads the Pandemic Preparedness project at WACKER. “But we have a great team and we collaborated very well with each other. Everything aligned perfectly – in terms of our companies’ capabilities and also on a personal level.” Between them, WACKER and CordenPharma cover the entire process chain for mRNA vaccine production – from the manufacture of plasmid DNA starter material to the filling of the finished mRNA active. Alexander Radspieler, Anton’s counterpart at CordenPharma, explains the “rules of the game” of pandemic readiness:
“First, secure a supply of vaccines by ensuring all essential steps take place in Germany. Second, secure independence from external supply chains by ensuring the entire process occurs within the European Union.”
Against this background, WACKER chose to carry out production at its biotech site in Halle, Germany. There, it erected a new mRNA Competence Center, comprising four biopharmaceutical production lines. Groundbreaking took place on July 5, 2022. Less than two years later, the building was complete. This set a new world record for the fastest construction of a production facility for pharmaceutical actives. Meanwhile, CordenPharma decided that its production sites in Frankfurt am Main (Germany), Chenôve (France) and Caponago (Italy) would be brought into a state of pandemic readiness. It substantially expanded its lipid production capacity and simultaneously invested in supercritical liquid chromatography, an eco-friendly method of lipid purification. It also expanded its aseptic fill & finish capacity.
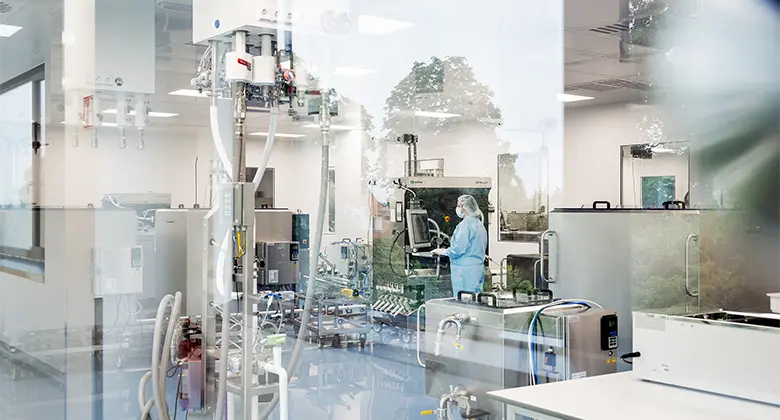
Successfully stocking up on staff
To ensure the project’s success, the WACKER team in Halle drew up comprehensive plans and schedules. After all, it was necessary to design and erect a new building, obtain the requisite equipment and hire and train considerably more staff. Anton recalls: “We went to great lengths to recruit talented individuals. For example, we ran a digital campaign using influencer videos to attract young people. That worked well.” In just one year, WACKER recruited more than 100 staff in Halle. They were trained straight away, even though the high-tech building was not yet finished. Special rooms were fitted out so that they could practise operating the machines. Where these were not yet available on site, they practised on virtual reality modules.
Protection for the active ingredient
Halle plays a key role in pandemic preparedness, because it is where all the central process steps take place. Says Anton, “The first thing we do there is produce the plasmid DNA, the starter material for manufacturing the mRNA vaccine.” Radspieler continues, “After that, we add our lipids to create the vaccine formulation. This crucial process step combines the mRNA with lipids to form liquid nanoparticles (LNPs). These are then packed inside a molecular envelope that protects the sensitive vaccine when it is being delivered to the muscle cells at the injection site. Before vaccination can happen, though, the vaccine is deep-frozen and sent to our aseptic fill & finish facility in Caponago in northern Italy, where it is packaged in pre-filled syringes and vials.”
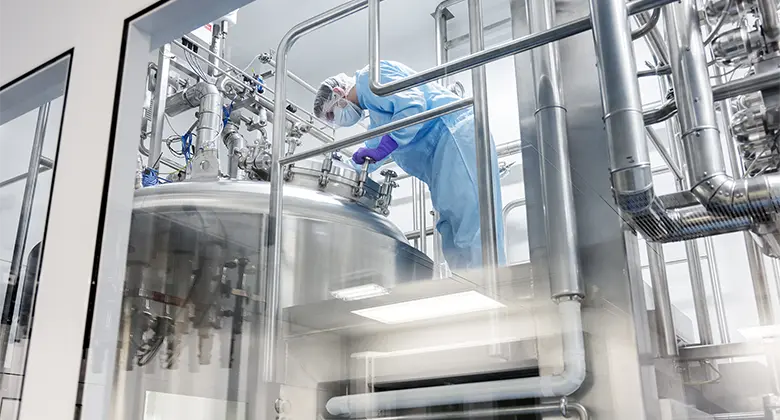
The experience gained by WACKER and CordenPharma from working on their own projects during the early days of mRNA vaccine development is standing them in good stead. During the COVID-19 pandemic, CordenPharma produced the lipids for the Moderna vaccine. WACKER successfully produced a candidate compound. The process technology needed for industrial-scale mRNA vaccine production was scaled up at WACKER’s Amsterdam site and laid the groundwork for setting up the mRNA competence center in Halle, where it ultimately invested over €100 million.
Flexible production lines
“As we don’t know which customer will be approaching us with a vaccine on Day X, we need to be prepared for everything,” explains Anton. “We designed the new facility around a modern process model that offers maximum flexibility.” As a result of this “ballroom concept”, there are no fixed pipe systems in the production rooms in Halle. Everything is designed to be as versatile and modular as possible, and the equipment is easy to move around. A “warm base” principle has also been adopted, whereby production equipment and staff are always on standby. The necessary raw materials and auxiliaries have also been stockpiled and are managed via a special storage and monitoring system. A logistics system connects all participating sites. “For the next five years, we are in a state of pandemic readiness. If the German government gives the order to manufacture mRNA vaccines, we can start the production process shortly after,” explains the WACKER expert.
This readiness also benefits our customers. In pandemic-free times, WACKER uses the facilities for pharmaceutical customers to produce active ingredients for clinical development. “But we can, and we do, make much more than mRNA vaccines – such as protein therapeutics, vaccines and plasmids,” Anton points out. “We operate globally across our four biotech sites in San Diego, Amsterdam, Jena and Halle to ensure we always offer the best production conditions for a given product.” Rapid switching between customer projects is a routine matter for WACKER and CordenPharma. As both are contract development manufacturing organizations or CDMOs, they are used to rapidly switching to other production processes. WACKER uses at least 50 percent of its capacity in Halle for customer projects, while the other half is reserved for vaccines production.
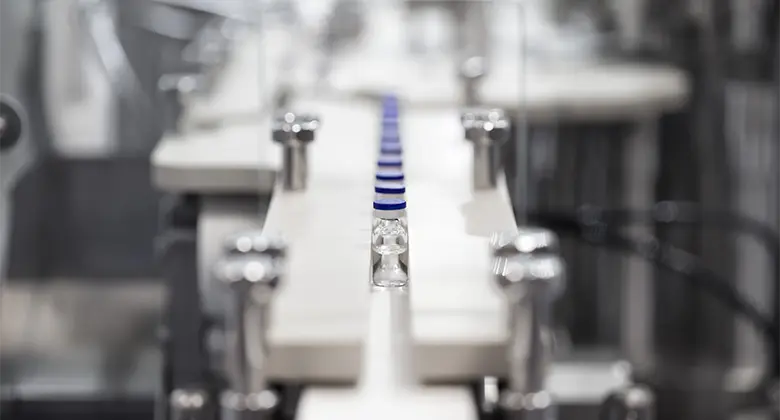
A top team with a sound plan
Overall, the pandemic readiness project involved several hundred staff members from WACKER and CordenPharma who spent many thousands of hours working on it. Without strong teamwork and mutual appreciation between WACKER and CordenPharma, this Herculean task would never have succeeded. Radspieler returns to this topic. “As we worked on the project, our trust in each other grew and that is what led to our joint success. We are now the only CDMO that can provide this service from start to finish. We have seen that we are a good match for each other and we can also win new projects in the future.” As the experts from WACKER and CordenPharma never tire of saying: Pandemic readiness depends on sound plans – and on staying in close contact with all partners. After all, you want to play safe in the event of a new pandemic.
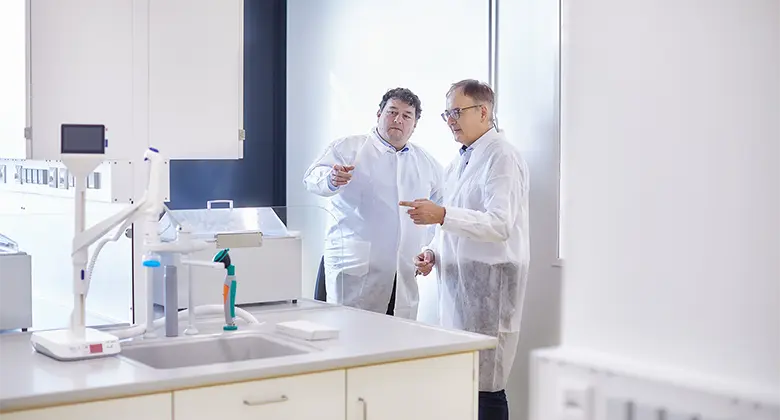
In Halle, Anton and his team have everything under control: time management, coordination of and collaboration with partners, service providers and ZEPAI. On March 27, 2024, he notified the authorities of pandemic readiness. Following intensive audits, the official confirmation came on June 1 that WACKER and CordenPharma are pandemic-ready. “That was the cherry on the top of the cake,” says Anton, “because our mRNA Competence Center officially opened just two days later. It’s amazing what you can achieve as a team.” •