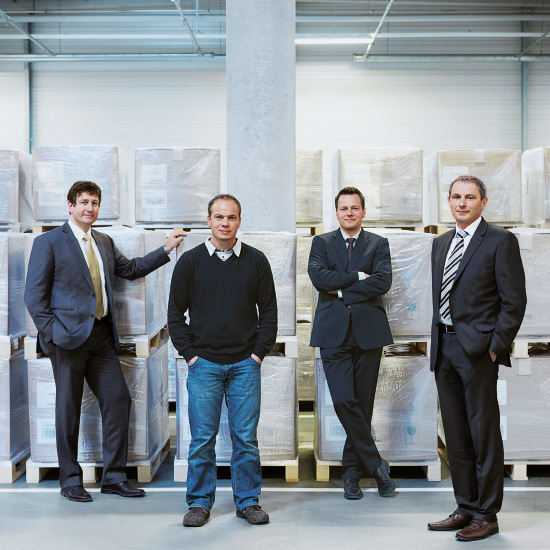
Clearly focused on fast and environmentally sound freight transport: (from left) Stefan Dartsch, Stefan Hrubesch,
Josef Oberlechner and Ludwig Hinterecker.
Modern locomotives, short routes for suppliers and environmentally friendly packaging – sustainability is as vital to WACKER’s logistics as the track is to the train. A visit to the heart of Burghausen’s logistics center.
Eight computer screens flicker in the container control center. Stefan Hrubesch always has an eye on one of them; he works here as head of Loading Control. “The red parts there,” he says, pointing to one of the computer screens, “are the container cars – and the small, rectangular blocks on top are the actual containers.” Hrubesch clicks on them to reveal what they contain – silicon, for example, or pyrogenic silica, or yet another WACKER product. Using the mouse, his co-workers are dragging one container after another onto the cars until the train is fully loaded. The whole system – called TESS (a German acronym standing for transport deployment control system) – is a vital logistics component at WACKER Burghausen.
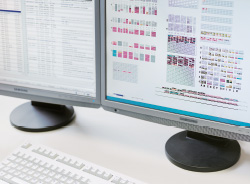
Initially, the trains are loaded on computer monitors
and, then, in real life.
Looking deceptively like some sort of game, the system calls for intuition and, above all, the ability to think logically. At their computer screens, Hrubesch and his four co-workers direct in-plant container transport and the train-loading process. Importantly, each train must be no longer than 560 meters and no heavier than 1,399 metric tons, otherwise it would not manage the steep, single-track section at Pirach. Despite this restriction, all the containers have to be on the train because they need to reach the North Sea ports of Hamburg and Bremerhaven at least two days before the loading window closes. “For us, Loading Control is the heart of a train,” says Stefan Hrubesch as he glances around the control center. “This is where all the information concerning the containers and the northbound shuttle train comes together.” For the last ten years, a shuttle train has left the plant daily – which helps reduce exhaust fumes on the roads.
Company-Operated Rail Track
Only a few meters from the control center, a white locomotive enters WACKER’s station at track 14. It is exactly 9:21 a.m. The locomotive is pulling a long line of fully laden container cars. Applying its brakes slowly, it comes to a halt. Once uncoupled, it heads to a side track. As it disappears, Stefan Dartsch (head of in-plant transport) points to a sign just behind the train station. That is where the jurisdiction of Germany’s national railroad operator ends. It is not the end of the tracks, though. Burghausen probably has Bavaria’s largest plant railroad, with 27 km of tracks leading to 19 loading bays – all the responsibility of Stefan Dartsch. As part of his preparation for the job, the engineer took a special examination to become a railroad operations manager.
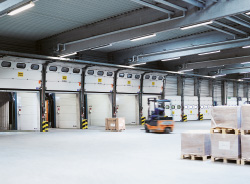
Center fill truck containers during the day and
train containers at night.
A yellow WACKER engine comes puffing up and hauls the first shuttle-train cars to a gantry crane, which relieves them of their loads. Each container is lifted onto a swap platform, ready to be taken to its in-plant destination by truck. The silicon containers are driven off first today. The unloading sequence reflects the day’s specific priorities.
Precision Work Up High
A gantry crane immediately loads new, full containers onto the cars. The crane operator, sitting in a cab some 10 meters above the ground, needs a really good eye for such precision work. The containers swinging through the air will go on their journey north the next day. Twenty-four kilometers from Hamburg, at the town of Maschen, the train divides. The containers in one section are headed for ships in Bremerhaven, with the rest destined for ships in Hamburg.
2010 saw 715,000 metric tons of products leaving the Burghausen plant – equivalent to the weight of 71 Eiffel Towers. Trains transported 230,000 tons of the total, with 154,000 carried by the shuttle train (which is exclusively for WACKER products) and 76,000 by regular freight trains.
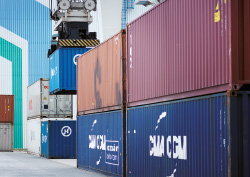
Precision work down to the last centimeter: the
crane operator lifts a container.
The Train Gets Top Priority
“Sustainability plays an important role in our logistics strategy,” stresses Ludwig Hinterecker (head of Logistic Services Procurement). First of all, sustainability means transporting as much freight as possible by rail. “In addition, we promote the use of state-of-the-art locomotives,” he continues, mentioning the 18 new engines deployed by the national operator in the region since late 2010. WACKER’s container cars are pulled, as of Landshut, by an environmentally friendly electric-powered locomotive. In the vicinity of Burghausen, though, a diesel locomotive is still used, since this route has yet to be electrified – and, moreover, is single track. For years, WACKER has championed the need to expand the railroad section running from Munich to Burghausen via Mühldorf and, in 2010, was pleased to see an initial success. In December, a 7.8-km double-track section opened near Mühldorf. In April 2011, an additional section between Tüßling and Burghausen was equipped with an electronic signaling system (replacing obsolete relay technology).
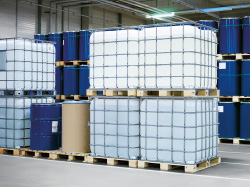
Intermediate bulk containers are increasingly
replacing conventional drums – saving packaging
material and storage space.
Avoiding Empty Shipments
Turning from trains to trucks, Ludwig Hinterecker explains the concept of regional freight carriers. “Each shipper serves a specific region, which is organized by zip code in Germany and by country in Europe.” This system avoids empty trucks and, therefore, lowers their mileage and fuel consumption. However, it requires multiple products to be loaded at a single location. One such location is Burghausen’s Logistics and Distribution Center. Here, 60 employees store, label and load around 30,000 pallets per month – seven days a week. Between 6 a.m. and 10 p.m., the forklifts load one pallet after the other into road containers. At night, it’s then the turn of the rail containers. To minimize the fire risk, the ambient oxygen in the fully-automated high-bay warehouse is lowered to 13 percent (about 7 percent less than normal) – equivalent to the oxygen available to hikers at an altitude of 3,500 to 4,000 meters. This area of the Logistics and Distribution Center is subject to strict safety regulations and can only be entered for checking purposes.
What is particularly striking about the whole Logistics setup is its efficiency. Everyone down to the switchman on the tracks knows exactly what they have to do and when. The forklift drivers glance briefly at a navigation device and immediately head off with their pallets to the correct lane. After one to two hours, the container is full.
Computer systems support most tasks, of course, whether labeling, loading or transport. “We not only have good computer systems, but also superb employees. That’s why we can load products so quickly and in such an environmentally friendly way,” explains Josef Oberlechner (head of Warehousing and Internal Traffic Control). In addition to the plant’s two central warehouses, there is an external warehouse three kilometers away. Altogether, they can hold 55,000 pallets, with none stored longer than absolutely necessary – which benefits both business and the environment.
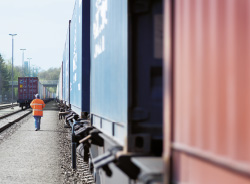
A WACKER freight train heads off to the North Sea
ports every day at 12:21 p.m.
Proximity to Suppliers
There are similar advantages when key suppliers locate near Burghausen. For instance, a supplier of plastic containers and other packaging materials opened a production facility in nearby Simbach. When ordering packaging, WACKER attaches great importance to material that is reusable and whose production was environmentally sound. For example, WACKER likes to use 1,000-liter containers, known as IBCs (intermediate bulk containers) – an approach which saves a lot of space compared to conventional drums. Consequently, less packaging material and fewer storage places are needed. In the case of steel containers, wall thicknesses have been reduced by around a tenth of a millimeter, which saves 149 metric tons of steel per year. What’s more, WACKER has been transporting all its gumbase output in recyclable paper bags for quite some time.
Let’s return to the train station. It is now about 11 a.m. The white locomotive changes tracks and connects to the outgoing train. From this point on, Germany’s national railroad operator assumes responsibility. In theory, the long train could leave immediately. But it has a timetable to follow. The train has to wait until 12:21 p.m. before it can depart.
Braking Quietly
Normally, freight trains make a loud screech when they brake. But not this container train. Stefan Dartsch is visibly proud: “This one has special brake blocks.” More and more WACKER cars (including 30 new rail tankers rented from the national railroad operator) have composite brake blocks (“K-blocks”), which function much more quietly, whatever the speed. WACKER strongly promoted the adoption of “K-blocks” in its discussions with the rail operator, since their adoption represents another small piece in the large picture of sustainability in logistics.