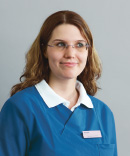
“I want our employees to live healthy lives and stay fit.”
Daniela Lechner
Medical Assistant, Health Services,
Burghausen Plant
The number of WACKER employees fell by 304 (down 1.9 percent) in 2009, whereas 696 new employees were hired (up 4.5 percent) in 2010 – the overall headcount thus reaching a record high. WACKER had 15,618 employees worldwide on December 31, 2009, and 16,314 a year later. The 2009 decline was chiefly due to the global economic downturn. Employment contracts with part-time employees were not extended, only some workers on short-term contracts received permanent contracts, and some jobs were eliminated at Siltronic and WACKER SILICONES. Reductions were achieved through natural fluctuation, as well as through transfers of employees to other parts of the Group such as the fast-growing WACKER POLYSILICON division. In addition, we offered phased-early-retirement plans. Germany’s short-time work option helped prevent layoffs of permanent staff.
The 2010 increase was due to the speedy economic recovery, which led to higher plant utilization. Plus, we continued to expand WACKER POLYSILICON. Our workforce also increased as a result of the acquisition of the Holla silicon-metal plant in Norway (129 employees) and the South Korean silicon facility at Jincheon (40 employees). In 2010, there was hardly any need for short-time work.
The majority of employees (about three quarters) are based in Germany, the remainder abroad.
download table |
Employees |
|
|
| |||
|
2010 |
2009 |
2008 | |||
|
|
|
| |||
WACKER Group |
16,314 |
15,618 |
15,922 | |||
Germany |
12,235 |
11,925 |
12,110 | |||
International (excluding Germany) |
4,079 |
3,693 |
3,812 | |||
Percentage outside Germany |
25.0 |
23.6 |
23.9 | |||
New hires, groupwide |
1,142 |
1,130 |
1,324 | |||
Percentage new hires, groupwide |
7.0 |
7.2 |
8.3 |
In the USA, we closed down the Duncan silicone-emulsions site in 2010. Almost all of the 50 employees affected by the closure were able to find other jobs. Some of them were offered employment at our US site in Adrian.
In 2010, WACKER announced that it would also close its Kempten (Germany) site in 2011. This closure is part of the structural measures announced in 2009. Among other things, these measures aim at consolidating the production of pyrogenic silica. WACKER will transfer production from Kempten to the existing high-volume facilities at Burghausen and Nünchritz, thus improving their utilization. For the 44 Kempten employees, we negotiated a comprehensive redundancy plan with the employee council that will not involve any involuntary layoffs. This plan took into account the employees’ age, as well as their marital status and seniority. Older employees who wish to stop working will receive termination agreements or be offered phased early retirement. Everyone else will be offered jobs at another WACKER site such as Burghausen or Nünchritz. WACKER will assist its employees in finding a place to live and subsidize the moving costs. For employees unable to relocate, there are plans to arrange reassignment contracts with other Kempten companies.
At Nünchritz, measures to open up new career prospects for 96 long-term unemployed were introduced in 2009. They started their training to qualify as skilled production workers and chemical technicians at the Nünchritz training facility run by ASG-Nordsachsen, which also provides training for WACKER. About 30 of these retrainees were living on unemployment benefits until they were taken on full time at the Nünchritz plant in 2010, where about 100 new jobs were created.
In 2010, the hiring of approximately 60 temporary workers at the polysilicon site in Burghausen led to a legal dispute between management and the employee council, which was ultimately settled out of court by mutual consent. The parties agreed on key items that take account of the temporary workers’ interests while also allowing job flexibility. A new wage model was thus agreed for temporary workers at the Burghausen site. It applies to Group companies who cover their cost of capital. Some of the temporary workers at WACKER POLYSILICON received short-term employment contracts. Management and the employee council also agreed to hold further discussions on this subject. These talks will concentrate on the question of how working time can be made even more flexible, enabling WACKER to better respond to fluctuating order levels.
download table |
Temporary Workers (as of December 31 Reporting Date) |
|
|
| |||
|
2010 |
2009 |
2008 | |||
|
|
|
| |||
Temporary workers, groupwide |
488 |
300 |
138 | |||
Thereof Germany |
374 |
247 |
80 | |||
Thereof international (excluding Germany) |
114 |
53 |
58 | |||
Percentage1 temporary workers, groupwide |
3.0 |
1.9 |
0.9 | |||
Percentage temporary workers, Germany |
3.1 |
2.1 |
0.7 | |||
Percentage temporary workers, outside Germany |
2.8 |
1.4 |
1.5 |
1 |
Ratio of temporary workers to employees groupwide |
WACKER regularly informs its staff on current internal and external developments. Employees receive timely and comprehensive information on major internal changes, taking into consideration the respective national and international information obligations.