Research and Development
Our researchers and developers focus on finding solutions to customer needs and responding to global concerns, such as rising energy consumption, depletion of raw materials, urbanization, digitization and demographic change. WACKER is a research-intensive chemical company. In 2010, our R&D rate – research and development spending as a percentage of Group sales – was 3.5 percent (2009: 4.4 percent). The decline can be explained by our strong sales growth in 2010.
As well as developing new products and processes, our R&D scientists continually strive to improve our production processes. They look for ways to reduce the use of raw materials and energy while at the same time increasing yields. They are also involved in testing the use of renewable raw materials, such as starch and straw. For every research project, we consider sustainability issues, document them via our groupwide project management system, and incorporate them into our project appraisals.
WACKER conducts R&D at two levels: centrally at our Corporate Research & Development department, and decentrally at our business divisions. Corporate R&D coordinates activities across the Group in consultation with the Executive Board. Our business divisions conduct application-driven R&D, focusing on:
-
Semiconductor technology (silicon wafers for semiconductor chips)
-
Silicone chemistry (silicone products, e.g. for the construction, automotive, electrical/electronic, textiles, cosmetics and medical sectors)
-
Polymer chemistry (dispersible polymer powders and polymeric binders used e.g. in the construction and automotive industries)
-
Biotechnology (fine chemicals and pharmaceutical intermediates)
-
New techniques for manufacturing hyperpure polysilicon (raw materials for the semiconductor and solar industries)
WACKER scientists are currently working on around 220 research themes based on 40 technology platforms. Our R&D activities are supported by a global network of 20 WACKER technical centers, which liaise between customers, sales offices and local production sites. At these centers, our specialists customize products to regional requirements, taking account of, for example, climate, national standards, and local raw materials.
We collaborate with customers, scientific institutes and universities to achieve rapid and effective research progress. 2010 saw WACKER cooperating with more than 30 research institutes in Europe and America on around 50 research projects. Areas of collaborative research that complement our own activities include white biotechnology, energy generation (photovoltaics and wind), energy storage
Research along the Supply Chain
WACKER takes environmental, health and safety criteria into account at every stage of the product life cycle – starting with the raw materials. We try to minimize
Indeed, WACKER continually strives to optimize its processes – their efficiency, environmental aspects, energy consumption and costs. During the reporting period, our WACKER SILICONES division significantly increased production-process efficiency thanks to new catalysts. This enabled us, for example, to simplify the silane manufacturing process, reduce process steps and save energy. What’s more, we cut waste generation by as much as 80 percent.
Life Cycle Assessments
In 2010, WACKER POLYMERS prepared life cycle assessments for VINNAPAS®, VINNEX® and ETONIS® dispersible polymer powders and dispersions as well as for other important intermediates, in order to analyze the environmental impact of all its key product groups. Our life cycle assessments consider the environmental factors associated with a product, from the initial stage of producing the starting materials to the factory gate
Research into Megatrends
Our R&D activities focus on energy, automotive, biotech and construction megatrends. On the energy front, for example, we are continuing to develop technologies for converting and storing energy. At present, we are investigating materials suitable for
In photovoltaics, we are strengthening our technological lead in polysilicon production. Our aim is to improve our silicon deposition process and to enhance our closed production loop, which ranges from silicon metal through hyperpure solar and electronics-grade silicon to silicones and pyrogenic silica.
In 2010, WACKER produced over 30,000 metric tons of hyperpure polysilicon, making us one of the world’s largest polysilicon manufacturers. 2010 also saw the official start-up of polysilicon expansion stage 8 at Burghausen. Currently, we are involved in two major projects: polysilicon expansion stage 9 at Nünchritz and the construction of a polysilicon facility in the US state of Tennessee.
We have further reduced the energy consumed by our polysilicon facilities. The energy payback time – the time taken for a photovoltaic cell to generate the energy used in its production – has become even shorter. Depending on the geographical location of the solar cells, this payback time now ranges from 6 months (in the Sahara) to 18 months (in Northern Europe). In many regions (including Germany), solar power now costs less than grid power, and its generation is increasingly independent of political incentives.
Some of our research projects are government funded:
-
2010 saw our semiconductor division – Siltronic – complete a basic research project (SIGMADT) on silicon-based starting materials for three-dimensional transistors. The project’s objective was to optimally adapt the properties of silicon wafers to three-dimensional transistors. As integration density continues to increase, it will become even more difficult to make electronic components for complex applications (such as navigation systems or computer tomography equipment) on just one plane. The transition to the third dimension opens the way to increased efficiency and reduced energy consumption. To meet this challenge, it is absolutely essential to improve wafer quality. Germany’s Federal Ministry of Education and Research (BMBF) provided a €3 million grant to fund this project for 30 months.
-
Semiconductor manufacturers are calling for the 450 mm diameter wafer, which is expected to increase productivity and curb costs. Siltronic is developing key processes for manufacturing 450 mm wafers and is involved in EEMI450 (European Equipment & Materials Initiative for 450 mm), a collaborative
EU-funded research project. Siltronic AG will receive funding of around €1 million for a period of 21 months, ending in February 2012.
-
Germany’s joint SPINEL project is devoted to boosting the energy efficiency of photovoltaic and electronic applications through innovative electronics-grade base material. As a result, the project also aims to make a substantial contribution to enhancing the energy yield of future energy systems. This objective is entirely in line with the German government’s energy policy on the conservation of fossil fuels and climate protection, and with the BMBF’s funding policy to increase the efficiency of renewable energy sources (based on its Basic Energy Research 2020+ strategy). SPINEL is researching a novel crystal-pulling method which operates without the use of a crucible. It uses granular silicon, which is much easier to process than rod-shaped polysilicon. Wacker Chemie AG and Siltronic AG have teamed up for this joint project. The BMBF has awarded Siltronic €1.8 million to fund its subproject – “Establishing a continuous, crucible-free single crystal-pulling method” – for a period of 27 months, until August 2011.
-
In the SuperPowerMOS joint project (energy efficient power-supply components for a voltage range of up to 400 V), the Fraunhofer Institute for Silicon Technology (ISIT), Danfoss Silicon Power GmbH, Siltronic AG and Vishay Siliconix Itzehoe GmbH have teamed up to develop innovative PowerMOS components for devices in the voltage range of up to 400 V. Heavily doped substrates are of particular interest as a starting material. The BMBF is providing funding of around €657,000 for Siltronic’s subproject – “Ultra-doped substrates for novel low-voltage PowerMOS components” – for a period of 39 months, until May 2011.
-
In a joint project called DECISIF (DEvice and CIrcuit performance boosted through SIlicon material Fabrication), partners from science and industry are researching the capabilities of “strained” silicon. The aim is to enable a faster and more energy-efficient manufacturing of electronic devices, such as notebooks, cellphones and MP3 players. The BMBF has awarded the project an €8.1 million grant. Of this, Siltronic will receive around €1.2 million to finance its part of the project from August 2008 until July 2011. Project partners Siltronic AG, GLOBALFOUNDRIES Dresden, AIXTRON AG, the Jülich Research Center and the Max Planck Institute of Microstructure Physics are contributing a further €6.4 million. Mechanical straining expands the crystal lattice of the silicon, which changes its electronic properties. This enables the charge carriers to flow more quickly through the transistor, as well as permitting switching frequency to increase and power consumption to decrease.
-
Our biotech specialists are developing new methods for producing ethylene and acetic acid from renewable raw materials. Acetic acid and ethylene are the precursors of vinyl acetate. This substance is processed by our WACKER POLYMERS division to make dispersible polymer powders and polymeric binders. In 2009, we succeeded for the first time in producing acetic acid to metric ton-scale from bioethanol. In another project, we are working to produce acetic acid and ethylene from biomass (e.g. straw). The BMBF is supporting this project as part of its BioIndustry 2021 funding initiative.
Sustainable Products
WACKER products are intended for the manufacturing industry (where they are further processed) rather than for end users. Our customers want us to produce their raw materials in a sustainable way. Plus, they expect their products to pose no risks to health or the environment. WACKER’s principle is to provide high-quality products that can be manufactured, transported, used and disposed of safely and with minimum environmental impact. Over the last two years, WACKER has developed diverse products that promote sustainability:
Automotive
A new silicone adhesive for plastic oil pans reduces the weight of a car and so cuts fuel consumption. ELASTOSIL® 76540 A/B is an extremely robust silicone elastomer: even when immersed in organic liquids (such as engine oil) at over
ELASTOSIL® R101 is a silicone elastomer that remains flexible even at temperatures as low as
Construction
WACKER SILICONES added the GENIOSIL® product family to its range of construction sealants. These hybrid adhesives and sealants combine the properties of silicones and organic polymers. They crosslink quickly and retain their functionality over the long term, even in highly stressed areas. They are free of tin and plasticizers. GENIOSIL® I70 ensures particularly high levels of bond strength on all kinds of substrates. As a result, it is now possible to bond numerous items that previously had to be joined with nails and screws (e.g. timber slats, plastic panels and metal components). The product also reliably bonds floor tiles and plasterboard.
WACKER manufactures binders which incorporate natural fibers from renewable raw materials, such as wood, cork and scrap leather. These natural fiber composites (NFCs) are recyclable, energy-efficient and can be thermoformed. VINNEX® is a brand of specialty binder powders based on vinyl acetate-ethylene (VAE) copolymers. When combined with slate and cork, for example, it creates a natural flooring that feels warm underfoot. NFCs based on recycled scrap leather can be used to manufacture coverings for furniture, floors and car interiors.
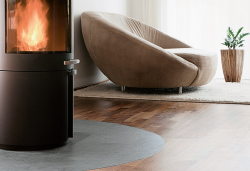
Renewable or recyclable raw materials (such as natural cork or slate) can be used in conjunction with VINNEX® powders to make flooring or wall coverings. Example: wafer-thin, flexible slate-cork tiles for flooring.
Our WACKER POLYMERS division is continuously developing its VAE copolymer dispersions for environmentally friendly, low-emission and low-odor interior paints. We have developed the VINNAPAS® EF718 dispersion specially for the Chinese market. The binder is free from alkylphenol ethoxylates (APEOs) and is low on volatile organic compounds (VOCs). The new product responds particularly well to thickeners, which reduces the amount needed – thereby lowering raw-material consumption further.
SILRES® BS provides silicone-based masonry protection by, for example, acting as the binder in silicone resin emulsion paints and plasters. SILRES® also makes brick manufacturing more environmentally friendly. The firing temperature is a key factor in determining the density and thus the quality of clay bricks. The higher this temperature is, the better the bricks are protected against moisture. When bricks were sprayed with a mixture of water and SILRES® BS16, they became water-repellent even at low firing temperatures. This saves energy and reduces CO2 emissions – a solution that is especially attractive to India (the world’s largest brick manufacturer), where most brickworks still do not have access to energy-efficient kilns.
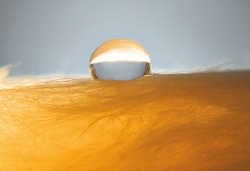
Insulation materials must be protected against moisture. Treatment with SILRES® silicone products provides effective protection. These water-repellent silicones prevent moisture from entering the insulation – as can be seen during the drip test on this piece of mineral wool.
Adhesives and Coatings
Concern about the environment has increasingly led to the replacement of solvent-based paint systems with water-based ones. WACKER has developed SILRES® MP50E for this purpose. The water-based silicone resin emulsion complies with the requirements of the US Food and Drug Administration (FDA) and Germany’s Federal Institute for Risk Assessment (BfR). The product provides a surface coating suitable for kitchen appliances, cooking utensils and grills.
Our researchers have developed a powder-based modifier for engineering materials. Epoxy adhesives modified with this high-impact product are able to withstand the severe mechanical stress generated in the rotor blades of wind turbines.
We have expanded our range of VAE copolymer dispersions to respond to the needs of the paper and packaging industry: VINNAPAS® XD05 allows the formulation of adhesives without the use of film-forming agents or plasticizers. The dispersion complies with the latest environmental and safety standards and is suitable for food packaging. What’s more, our VINNAPAS® EP1400 and EP441 copolymer dispersions allow adhesive manufacturers to dispense with film-forming agents and plasticizers. In addition, these new products are free from alkylphenol ethoxylates (APEOs) and contain only minute quantities of volatile organic compounds (VOCs).
Energy, Electrical & Electronic Sectors
Light-emitting diodes (LEDs) are the light source of the future. They produce high levels of luminosity whilst consuming just a fraction of the energy required by conventional light bulbs or energy-saving lights. However, as LED performance increases, new demands are placed on materials, particularly those used in lenses. Conventional materials are unable to withstand the light flux, and turn yellow. Now, manufacturers of high-power LEDs are focusing on silicones, which have the necessary heat resistance and light stability. WACKER’s new silicones sold under the LUMISIL® brand allow – for the very first time – optical lenses for LEDs to be applied directly to the light-emitting diode chip. In 2009, we presented the developer with the Alexander Wacker Innovation Award for his work in this field.
Transformers produce a lot of heat when in operation. As heat-transfer media, coolants are indispensable for dissipating this energy. WACKER offers silicone-based insulating fluids with high heat resistance for this purpose. POWERSIL® Fluid TR20 can be used to cool electrical machinery, where huge amounts of heat must be dissipated rapidly. The new product retains its functionality even at
The POWERSIL® UV range of silicone elastomers cure at room temperature by irradiation with UV light – which saves energy, since there is no need for oven curing. No fission products are released during vulcanization. This technology, with a proven track record in the electronics industry, can now be applied to insulating materials for high-voltage applications. Silicone elastomers are used, for instance, in combination with glass-fiber-reinforced epoxy resin, to manufacture long-rod and hollow insulators. Other important applications for POWERSIL ® UV include cable accessories, connecting parts for substations, and surge arresters.
SilGel ® 613 also cures in seconds at room temperature when exposed to UV light. This silicone gel is used for encapsulating electronic components, e.g. for automotive applications, solar cells and electrical appliances.
ELASTOSIL® Solar 2120 UV is a UV-activated silicone elastomer developed for the solar industry. It is ideal for encapsulating junction boxes. Since the product contains no photoinitiators, it leaves neither ions nor free-radical decomposition products in the material.
We developed TECTOSIL® especially for encapsulating photovoltaic modules. The plastic film comprises a silicone elastomer that can be thermoformed, making it fast and easy to process. It protects solar cells from mechanical and chemical stresses. The film contains neither catalysts nor corrosive substances. The material absorbs hardly any water at all, poses an effective moisture barrier and stays permanently electrically insulating. With the aid of TECTOSIL®, high-quality solar modules with a long service life can be produced.
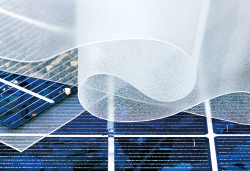
TECTOSIL® is a film for encapsulating photovoltaic modules. It is composed of a silicone thermoplastic. Transparent and non-yellowing, this material helps achieve high solar-module efficiency and affords the modules lasting protection.
High-concentration photovoltaic (HCPV) systems are an alternative to the conventional PV technology used in photovoltaic power plants. HCPV systems employ special lenses that concentrate sunlight and focus it onto high-performance cells. Much higher efficiencies are achieved in this way than with normal solar modules. WACKER has developed ELASTOSIL® Solar 3210 specifically for these high-performance modules. The two-part rubber is pourable and has very good light permeability, making it suitable for the production of optical lenses and moldings (for example Fresnel lenses).
Plastics and Composites
Our WACKER POLYMERS division has worked with customers to develop compostable products which combine flour or starch with VINNEX® polymeric binders. Although these polymer blends have similar properties to petroleum-based plastics, they are industrially compostable and biodegradable. This makes them ideal for the packaging, catering, gardening and landscaping sectors.
SILPURAN® 8630/60 can be used to manufacture molded parts and semi-finished products that have very low-friction surfaces. Unlike with traditional oil-exuding silicones, no oily silicone film forms at the surface. These high-purity solid silicone rubbers are therefore particularly suitable for medical applications, such as catheters and drains designed for greater patient comfort.
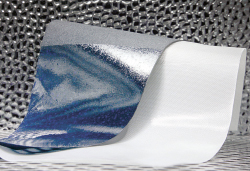
SILPURAN® 2149 UV is a silicone adhesive that we have developed for dressings to promote the healing of wounds and scars. This adhesive cures rapidly at room temperature after brief UV irradiation. Energy is saved by not having to oven-cure the silicone.
ELASTOSIL® R plus 4366 is another rubber grade that forms a low-friction surface with no oily film. This makes it easier to dispense food ingredients in metering tubes, for example. These solid silicone rubbers comply with the food standards of the Federal German Institute for Risk Assessment (BfR), the French Arrêté du 25 novembre 1992 and the US Food and Drug Administration (FDA).
ELASTOSIL® R plus 4370 bonds to plastics and metals, such as aluminum or steel, without the need for any special surface treatment or solvent primers. These self-adhesive solid silicone rubbers provide an environmentally sound way of producing hard-soft combinations for use in injection molding, for example.
Life Science – Pharma Industry
Our WACKER BIOSOLUTIONS division focuses on the growth areas of food, pharmaceuticals and agrochemicals. We have further improved our ESETEC® process for the bacterial production of pharmaceutical proteins (biologics), which has enabled us to increase our yields. Some of these biologics are currently undergoing clinical trials by our customers. Our pharmaceutical actives are used in the treatment of cancer, arthritis, and cataracts.
Our scientists have developed CAVAMAX® W8 CURCUMIN specifically for the food sector. The ring-shaped sugar molecule (cyclodextrin) improves the solubility of the active substance curcumin in an aqueous environment. This increases its bioavailability – in other words, the extent to which curcumin is absorbed by the human body. Curcumin mops up free radicals which damage body cells. Additionally, studies suggest that curcumin may have anti-inflammatory properties, which could play a role in the prevention and treatment of cancer.
Paper and Labels
DEHESIVE® 971 is a highly reactive silicone polymer which cures with the addition of a platinum catalyst. It is used for coating release liners and labels. Thanks to our product’s high reactivity, just trace amounts of the platinum catalyst are enough to ensure complete curing of the silicone layer. This enables paper manufacturers to cut platinum consumption by as much as 60 percent compared with conventional systems.
Energy-Efficient Construction
There is enormous potential for using exterior insulation and finish systems (EIFS) to sustainably reduce greenhouse-gas emissions. Heating and air-conditioning account for half of a building’s energy demand. Inadequately insulated, a house loses a large part of its energy through its exterior walls and roof. EIFS can reduce heat loss by 60 percent and cut the energy lost by air-conditioners by as much as 72 percent. The German Energy Agency (dena) has calculated the savings potential that can be achieved using insulation alone. While over 10,000 kilowatt hours of heating energy escape through the walls of an uninsulated single-family house each year, this can be reduced to just 2,900 kilowatt hours if the external walls are insulated.
According to dena, in Germany alone, only a third of all homes are adequately insulated. Giving a building effective insulation based on EIFS could save 80 million metric tons of CO2 emissions a year – that’s 10 percent of Germany’s total emissions. Surfaces where exterior insulation and finish systems have been used prevent 1.46 million metric tons of CO2 emissions annually, which so far amounts to over 300 million metric tons.
VINNAPAS® dispersible polymer powders added to the mortar ensure that the EIFS layers bond together firmly. The insulation systems are therefore much more stable, durable and weather-resistant. They permit the use of insulation boards comprising different materials, including renewable substances, such as cork and wood-wool. VINNAPAS® polymer powders can be used to make construction chemicals that meet the strict EMICODE® emissions standards set by Germany’s GEV (Association for the Control of Emissions in Products for Flooring Installation).
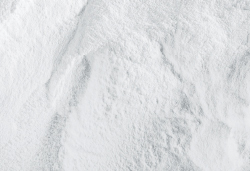
VINNAPAS® polymer powders are indispensable in modern construction-sector applications. They improve processing and optimize the properties of, for example, tile adhesives, plasters and self-leveling compounds. Plus, they enhance the efficiency of exterior insulation and finish systems, as well as sealing slurries.
Some listed buildings and historical monuments cannot be insulated with EIFS. In cases such as these, a coat of silicone resin emulsion paint (SREP) is one of the few materials that improve a building’s energy balance. WACKER SILICONES is a leading manufacturer of silicone resin emulsions for these paints. Damp walls lose heat relatively quickly, whereas silicone resins protect masonry against moisture ingress. A coat of high-quality silicone resin emulsion paint reduces heat loss from external walls by as much as 40 percent and lowers heat demand by an average of 4.6 percent. What’s more, this kind of paint improves the indoor climate by transmitting water vapor.
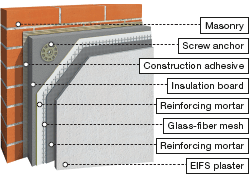
Exterior insulation and finish systems (EIFS) for building insulation consist of a multilayered material composite. Dispersible polymer powders bond masonry and insulating material firmly together to produce a stable insulation system.
Knowledge-Sharing
One way we promote knowledge sharing about energy-efficient construction techniques is by organizing seminars and technical workshops. In 2010, we expanded the program offered by our international training centers and held more interdisciplinary seminars. Our WACKER ACADEMY centers provide a forum for exchanging sector-specific expertise between customers, distributors and WACKER specialists. Construction chemicals are the main focus and, since 2010, we have complemented our polymer-chemistry seminars with courses on silicone construction applications – as well as with courses for other branches (including cosmetics and paints). The principles of intercultural cooperation and the efficient use of e-business systems round out our seminar program.
WACKER ACADEMY runs centers in Burghausen, Dubai, Moscow, Mumbai, Beijing, São Paulo and Singapore. Proximity to our development and test laboratories facilitates the exchange of expertise and gives participants the opportunity to perform practical tests on site. We collaborate with our own in-house research facilities, as well as with universities and institutes, to ensure that our seminar program is always at the cutting edge.
Although China’s construction boom shows no signs of letting up, many of its buildings still do not yet meet international energy-efficiency standards. Heating and cooling buildings consumes a third of all China’s energy. Such high energy consumption and the resulting air pollution have set alarm bells ringing in government quarters. At WACKER, we are committed to initiatives that make China’s municipal authorities and construction industry aware of the benefits of energy-efficient building techniques.
Since 2007, WACKER has been involved in an initiative run by the German Energy Agency (dena) and the Chinese Ministry of Construction – the goal being to promote energy-saving construction methods suited to the local climate. The project focuses on seminars held in major Chinese cities in different climate zones. On the one hand, cold regions need exterior insulation and finish systems to reduce heating costs (and cut greenhouse gas emissions). On the other hand, hot regions require insulation against heat to reduce the energy requirements of air-conditioning systems.
WACKER additionally partnered with other international companies in 2007 to establish the ETICS (External Thermal Insulation Composite System) Quality Alliance, spearheaded by the German Chamber of Commerce in Beijing. The purpose of the alliance is to draw attention to exterior insulation and finish systems and establish internationally recognized quality standards for energy-efficient construction. WACKER organizes informative events and user workshops in collaboration with the Chinese authorities, trade associations and inspectorates. In the reporting period, we promoted knowledge-sharing regarding energy-efficient construction techniques in Beijing, Shanghai and Tianjin with a program of seminars, technical training courses and conference presentations.
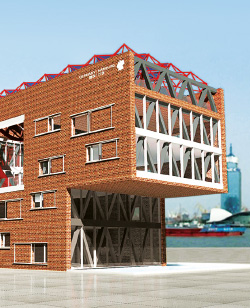
The Hamburg House at the EXPO 2010 in Shanghai is a perfect example of sustainable construction. Erected by the German city of Hamburg for the 2010 expo, the building is China’s first certified “passive house” to take local climatic conditions into account. Thanks to modern energy-efficient technologies and energy-saving building materials, the Hamburg House gets by with no external power supply, air conditioning or heating. WACKER’s contribution to the project was to provide silanes for concrete protection, silicone sealants, and dispersible polymer powders for high-performance dry mortars. For example, the interior walls and roof surfaces of the Hamburg House were protected with WACKER SILRES® BS Crème C. This active ingredient stops concrete and reinforced concrete from absorbing water or pollutants and so prevents rust damage. All mosaic tiles for the washrooms, bathrooms and kitchens were installed using tile adhesives and tile grout mortar containing WACKER’s VINNAPAS® polymer powders. This has the advantage of reducing raw-material consumption and dust pollution during cement manufacture. Grouts modified with VINNAPAS® are also water-repellent, which prolongs the lifetime of the materials.