The chemical industry is an extremely energy-intensive sector. In Germany alone, it uses around 20 percent of all the power consumed by industry. We believe it is our responsibility to continuously improve the energy efficiency of our processes. This enables us to contribute to climate protection while remaining competitive in the world market.
In 2010, the expansion of polysilicon production at Burghausen and the acquisition of the silicon-metal production facility at Holla in Norway increased WACKER’s electricity consumption to 3.8 million MWh (2009: 2.7 million MWh). The expansion of polysilicon production had also been the main reason for the rise in the amount of electricity consumed in 2009 (2008: 2.4 million MWh).
Accounting for 79 percent of the Group’s electricity needs, WACKER’s production sites in Germany purchased power from utilities to cover 50 percent of their electricity requirements in 2010. In line with the utilities’ primary energy sources, about half of this electricity was generated from fossil fuels (55 percent). 31 percent came from nuclear energy, and 14 percent from renewable energy sources. We are continuing to test the use of renewable energies and will include suitable offers as a permanent feature of our energy mix. The electricity used at our new production facility in Holla is generated almost entirely by hydropower, as is customary in Norway.
At WACKER’s large Burghausen and Nünchritz sites, steam and electricity are produced in cogeneration systems. These combined heat and power (CHP) plants have more than 80 percent fuel efficiency, which is twice that of conventional oil, gas or coal-fired power plants. Burghausen also uses hydropower to generate electricity. Our hydropower plant generates 270 gigawatt hours annually. This environmentally compatible energy source spares us 160,000 metric tons of carbon dioxide emissions every year. Together, the two CHP plants and the hydropower plant generated 1.5 MWh electricity in 2009 and 2010, respectively. This means that WACKER covered roughly 40 percent (2009: 55 percent) of its total electricity needs itself.
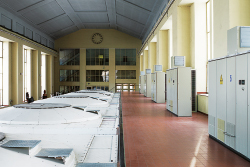
The Alzwerke hydroelectric power station has been supplying the Burghausen site with hydropower since 1922.
Many chemical reactions generate heat that can be put to use in other production processes. We have been using integrated heat-recovery systems in Burghausen and Nünchritz for years and are continually improving them. In this way, we can reduce the amount of primary energy (normally natural gas) that our power plants consume.
In 2010, our Nünchritz site required around 70 percent less electricity and 85 percent less process steam from its CHP plant to manufacture one metric ton of product than it did in 1999 when WACKER acquired the site. We have converted our Nünchritz power plant from heavy fuel oil to more ecologically sound natural gas.
Together, our large production facilities in Burghausen and Nünchritz consume around 75 percent of groupwide energy demand. Due to our acquisition of the Holla site in Norway, heat consumption rose to 3.4 TWh (2009: 2.8 TWh) across the Group. Heat consumption figures reflect for the first time the use of solid fossil fuels (coal, charcoal and wood) at the newly acquired silicon-metal plant.
In 2009, WACKER and Siltronic introduced an energy management system at their German sites in Burghausen, Nünchritz and Freiberg. This enables us to identify energy flows and consumers, as well as energy-saving opportunities. That same year, WACKER’s Burghausen and Nünchritz sites, as well as Siltronic’s Burghausen and Freiberg sites began having the new system certified to ISO 14001.
Many of our measures to improve the energy efficiency of our production facilities have come from the POWER PLUS project launched by WACKER in 2007 to increase energy efficiency at its Burghausen and Nünchritz plants. The project was extended to our Cologne plant in 2009. The success of POWER PLUS is based on two factors: our energy experts carefully scrutinized the production facilities and our employees put forward suggestions for improvements. All in all, we introduced more than 150 measures to improve energy efficiency, around 70 percent of which had been implemented by the end of 2010.
Here are two examples. Our WACKER SILICONES division has optimized distillation operations relating to siloxane production in Burghausen and installed an integrated heat-recovery system. This saves us around 100,000 metric tons of heating steam a year. In 2009, the Nünchritz plant saved more than 30 percent heating steam per metric ton of siloxane compared with 2006.
We have reduced energy consumption in a number of areas at POWER PLUS participant sites. Specific energy consumption (referenced to production output) has varied overall, as our production facilities were operating at fluctuating capacities and we have expanded polysilicon production, which is particularly energy intensive. Underutilization of many production facilities during the economic crisis of 2009, for example, had a negative impact.
We are also working on boosting energy efficiency at our sites outside Germany. A good example is our cyclodextrin facility at Eddyville (Iowa, USA), which was expanded in 2009. Cyclodextrins are biotech sugar molecules that serve as stabilizers and carrier substances in the life sciences, cosmetics, food and agricultural sectors. A substantial amount of the $21 million investment was channeled into a new by-product processing plant that reduces overall steam consumption by 35 percent.
Our Siltronic plant in Freiberg has come up with a way to adapt the supply temperature for crystal pullers so that the need for refrigeration machines has been largely eliminated. This saved 764 MWh of electricity at the Freiberg site in 2010.
We use energy-efficient electric motors for vehicles and equipment. We also save electricity by converting the direct electric drives of pumps in production facilities, for example, to speed-regulated drives, which automatically cut the speed when lower loads are involved.
download table |
Energy |
|
|
| |||
TWh |
2010 |
2009 |
2008 | |||
|
|
|
| |||
Electricity consumption |
3.8 |
2.7 |
2.4 | |||
Heat consumption1 |
3.4 |
2.8 |
2.8 | |||
|
|
|
| |||
Primary energy |
|
|
| |||
Natural gas |
5.5 |
5.4 |
5.4 | |||
Solid fuels2 (coal, charcoal, wood) |
0.4 |
– |
– | |||
Heat3 (supplied by third parties) |
0.2 |
0.2 |
0.2 | |||
Fuel oil |
0.01 |
0.01 |
0.01 |
1 |
In 2010, heat consumption figures reflect for the first time the use of solid fossil fuels (coal, charcoal and wood) at the newly acquired siliconmetal plant in Holla, Norway |
2 |
Used at the silicon-metal plant in Holla, Norway |
3 |
Steam, district heating |
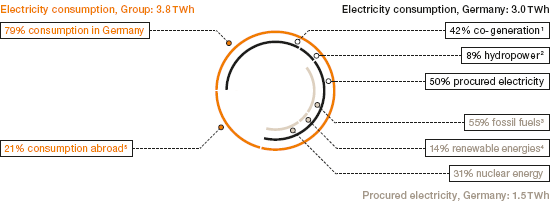
1 Burghausen and Nünchritz
2 Burghausen
3 Coal, lignite, oil, gas
4 Hydro, wind, solar power
5 Outside Germany, we purchase electricity from third parties based on the standard local energy mix