2009 and 2010 turned out to be two very different experiences for WACKER. The company remained stable in 2009, weathering the economic crisis, and then generated record sales and earnings in 2010. Amid all the economic ups and downs, WACKER continued its sustainability efforts. The following interview was held with Dr. Rudolf Staudigl (President & CEO), and Auguste Willems (Executive Board member responsible for sustainability issues).
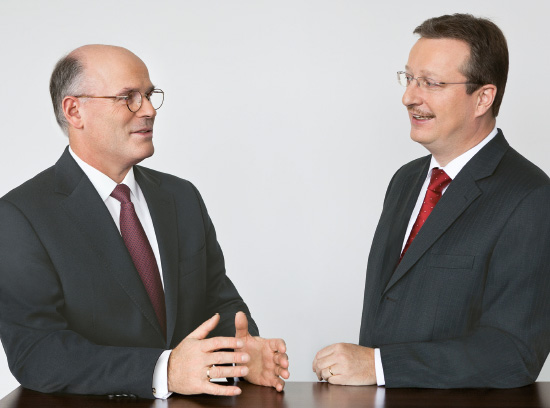
Operating a sustainable company is not only a duty – it also generates business opportunities. Dr. Rudolf Staudigl
(left) talking to Auguste Willems.
Dr. Staudigl, 2008 to 2010 was a turbulent period for WACKER. How did the recession impact sustainability management within the company?
Dr. Rudolf Staudigl Companies with sustainable practices, like WACKER, survived the crisis best. More than anything else, we were careful to keep our liquidity high and to avoid amassing any additional liabilities – by simply adhering to our solid business policies. We continued with our strategic investments, though perhaps at a slightly slower pace in some cases. Whenever necessary, we introduced short-time work, thereby retaining our highly qualified employees. This approach more than paid off when we needed to ramp up production capacity quickly. Furthermore, our employees sacrificed a portion of their salaries.
Auguste Willems Our business strategy is based on long-term, sustainable trends. That’s why we returned to growth quickly once things improved, because these trends remain valid.
Dr. Rudolf Staudigl Exactly. But fluctuations will always happen. In addition, sustainability in business means being able to navigate such fluctuations. That’s why it’s important to have solid foundations and a clear course. WACKER’s vision is to make an indispensable contribution to progress and sustainable development. We believe that we can only be enduringly profitable if we take our responsibility toward the environment and society seriously. That’s why sustainability has been so deeply rooted in both our production operations and business processes for years.
Mr. Willems, how did WACKER’s sustainability management develop in 2009 and 2010?
Auguste Willems First, I’d like to say that we adhered to our mission – in everything that we do, we strive for a balance of economic, environmental and social factors. Our company is becoming increasingly international. To harmonize standards across the Group, we developed our processes with an eye to globalization. The “Global EHS Excellence” project is a good case in point. We have now established uniform global standards for managing EHS and product safety. In doing so, incidentally, we also addressed the greatest challenge that stakeholders identified when surveyed in 2008: to maintain the same social and environmental standards at all our sites. Moreover, in 2011, we set up a Corporate Sustainability department, which now coordinates our sustainability efforts throughout the Group and along the entire value-added chain.
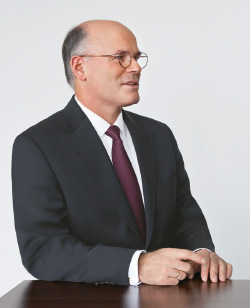
Critics often describe voluntary business commitments as mere lip service. What commitments has WACKER made and how important are they to the company?
Auguste Willems Above and beyond our involvement in official initiatives, we are deeply committed to sustainable corporate development at WACKER. This voluntary commitment is reflected in our participation in various initiatives. WACKER has been an active member of the chemical industry’s global Responsible Care® program from the start. The goal of Responsible Care® – to go above and beyond legal requirements – is firmly rooted in our company. A few years ago, we also joined the UN’s Global Compact and now comply with its ten principles: we safeguard human rights, maintain social and environmental standards and fight corruption. What’s more, this commitment extends to our suppliers, who must also abide by the Global Compact’s principles.
Dr. Rudolf Staudigl Speaking of corruption risks, we expanded our global network of compliance officers and intensively trained our employees in legally and ethically appropriate conduct.
Operating a sustainable company is not only a duty – it also generates business opportunities.
Dr. Rudolf Staudigl WACKER sees plenty of opportunities. As we’ve said, sustainability trends have a considerable impact on our business strategy. And the major issue here is energy. Whether we’re talking about generating, saving or storing energy – WACKER has a role to play. We lead the industry as a cost-effective, high-quality manufacturer of polycrystalline silicon – the key raw material for solar cells. Consequently, the growth of this alternative energy source benefits us as well. Other examples include products made from renewable raw materials, such as biopolymers and natural fiber composites. The list of examples is very extensive.
Products represent one half of a chemical company’s sustainability efforts, and manufacturing processes another. What successes did WACKER achieve on the manufacturing side during 2009 and 2010?
Auguste Willems I wouldn’t want to limit my response to just the past two years. Productivity is a central issue at WACKER, which is why we created our “Wacker Operating System” program a few years ago. It aims to generate greater output with less input. We are constantly on the lookout for ways of making more efficient use of raw materials and reducing our energy consumption. This is where our integrated production system gives us a tremendous advantage, as our plants use materials and energy within closed loops. In other words, we take the by-products of one production step and use them as the starting material for other chemical processes. We also do the same with waste heat, taking it from one process and using it for later production steps. That saves money and reduces our consumption of energy and resources. An integrated production system is a never-ending project – we’re always finding new ways of making it even better. But we don’t want to focus solely on in-plant production – we also need to look beyond the factory gates. To take just one example, we have been supplying dried silica sludge to the cement industry for the past year. The sludge is a waste product for us, but it contains a considerable amount of silicon dioxide, which is a terrific additive for cement.
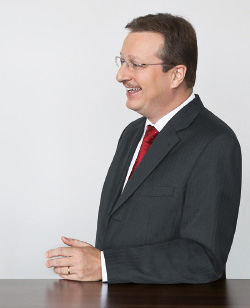
Dr. Staudigl, you were dissatisfied with the number of workplace accidents. What is WACKER doing to permanently reduce the accident rate?
Dr. Rudolf Staudigl Our overall accident figures weren’t good enough. Over the past year, we counted 4.3 workplace accidents per one million hours worked. Although that result is lower than the average for chemical companies in Germany, it is higher than the figures of the international manufacturers we benchmark ourselves against. Most accidents are not chemical in nature. Instead, they are caused by moments of inattention that result in people tripping up, slipping or falling down. Last year, we worked to prevent accidents by launching our WACKER Safety Plus program, which incorporates safety elements from sites with very low accident rates. We can learn quite a lot this way, especially from our non-German sites, where very few accidents occur.
The population is aging – and so are WACKER employees. How is the company addressing demographic change?
Dr. Rudolf Staudigl Fortunately, older people today are healthier and more productive than 30 or 40 years ago. While that takes the edge off demographic change, Germany, in particular, still faces the problem of fewer young people stepping into the older generation’s shoes. We have set ourselves ten strategic goals to remain innovative and competitive. I’ll give you two examples. First, we want to help our employees remain healthy and productive. Second, we want to intensify our efforts to hire talented individuals, especially scientists and engineers. WACKER is an attractive employer. This was confirmed last year, when a reputation analysis showed a high level of trust among our employees, with 6 out of 10 of them answering as true ambassadors for WACKER. That figure is extremely good compared to other companies in Germany.
WACKER is also involved in charitable activities. What projects did you support in 2009 and 2010?
Dr. Rudolf Staudigl Before looking at individual projects, I would like to point out that a company with a strong sense of social responsibility is a successful one. That’s because it can pay good salaries and offer stable jobs. We also know, however, that a company’s social responsibility does not stop with its own community – companies are global citizens, too. That is why our support extends to the poorest of the world’s poor.
Auguste Willems Our relief fund – the WACKER HILFSFONDS – is dedicated to rebuilding areas destroyed in natural disasters. Employee and company donations were used, for instance, to reconstruct an elementary school in the Sichuan province of China following the 2008 earthquake there. As part of a project run by the Don Bosco relief organization, we also helped rebuild a school destroyed in Haiti’s earthquake last year. And in Pakistan, we worked with Germany’s Malteser charity to build an elementary school after the 2010 floods. At our headquarters in Munich, Germany, we support a children’s charity known as “Die Arche” (The Ark).
In summary: How would you assess WACKER’s sustainability efforts during 2009 and 2010?
Dr. Rudolf Staudigl When a company practices sustainable development, it embarks on a continuous journey. I think we completed a major leg of this journey over the 2009-to-2010 period. The important point now is to continue anchoring and strengthening the topic in our corporate culture.
Dr. Rudolf Staudigl |
Auguste Willems |