Risk Management
In order to ensure safe production conditions, we analyze the risks posed by our plants – from the early design phase to start-up. We analyze plant risk in two stages. First, we conduct a danger-scope analysis where we simulate a potential damaging event, such as a fire or substance spill, investigating possible causes and adopting preventive measures. Second, we examine critical plant components for potential error sources and then create a risk matrix comprised of the following assessment criteria: impact, likelihood that individuals will be present in the risk area, likelihood that the event in question will occur, and options for eliminating the hazard in a timely manner. We use a matrix to classify risks and take appropriate precautions.
In 2010, as part of our ANSIKO 2010 project, we randomly reviewed the safety plans of all production plants that might be especially hazardous. One focus was on facilities with a dust-explosion risk. That review was prompted by a dust explosion at Burghausen in 2009. While property had been damaged (costing some €0.5 million), no harm was done to people or the environment.
WACKER also established the Loss Control Team during the period under review. Composed of internal fire-safety and hazardous-incident experts on the one hand and property insurance specialists on the other, the Loss Control Team studies potential fire and explosion hazards as well as any other risks that might jeopardize operations at our sites. The team’s efforts in 2010 included audits of the Burghausen, Freiberg, Jena and Cologne sites in Germany and the Eddyville, Allentown and Portland sites in the United States. Other audits included those of our sites in Jandira (Brazil), Kolkata (India), Plzeň (Czech Republic) and Ulsan (South Korea). We have implemented appropriate measures entailed by the audit.
Safety Training & Employee Motivation
WACKER attaches particular importance to the training of its safety experts, holding regular courses on topics such as plant safety and explosion protection. The program includes safety training at WACKER sites around the world by Group experts – in 2010, for instance, they provided training at Ulsan, South Korea, and Zhangjiagang, China.
But it’s not only our safety experts who regularly go on courses. All our employees are given safety training specific to their individual work areas. Thanks to e-learning sessions, employees can set their own ongoing training program. Topics range from general safety guidelines for office and laboratory workers to instruction on working with respirators and hazardous materials. Integrated into each instruction module are tests that participants can use to gauge their success.
WACKER’s responsibility for protecting its workers does not end with on-the-job safety, however. The Burghausen site, for instance, hosted traffic safety weeks in 2009 and 2010, giving employees the opportunity to learn about protective clothing for motorcyclists, vehicle noise testing, and braking and evasive maneuvers that drivers can perform at various speeds.
Avoiding accidents at the workplace is the goal of the “Fresh Impetus for Work Safety” initiative launched in 2007. Despite this awareness campaign, however, the number of accidents resulting in lost workdays rose during the period under review, with 4.3 workplace accidents reported throughout the Group in 2010 for every one million hours worked – up from 4.0 in 2009 and 3.7 in 2008. WACKER did not report any fatal workplace accidents during the reporting period. Few accidents are chemical in nature but are instead caused by tripping, slipping, falling and performing manual activities without due care.
While its accident rate is below that for the chemical industry in Germany, WACKER’s figures do lie above the global industry average. According to data provided by Germany’s BG RCI (the employers’ liability insurance association for raw materials and the chemical industry), 8.5 reportable accidents, i.e. those resulting in more than three lost workdays, were recorded at chemical companies in Germany in 2009. The International Council of Chemical Associations (ICCA) registered 3.65 accidents resulting in lost workdays for every one million hours worked in 2008. In view of this accident rate, we will continue to enhance our workplace safety efforts. In 2010, for instance, we developed a new safety program in Germany. Called WACKER Safety Plus, the program will adopt safety elements that have been successfully employed by sites and subsidiaries with particularly low accident rates. Examples include safety patrols, analysis of near misses, and group discussions with the workforce.
download table |
Workplace Accidents |
|
|
| |||
|
2010 |
2009 |
2008 | |||
|
|
|
| |||
Accident rate: reportable accidents per 1 million hours worked1 |
4.3 |
4.0 |
3.7 | |||
Fatal workplace accidents |
– |
– |
– | |||
|
|
|
| |||
Accidents among contract workers2 |
7 |
1 |
4 | |||
Number of contract workers2 |
371 |
199 |
66 | |||
Accident rate, contract workers2: reportable accidents per |
8.8 |
0.0 |
10.5 |
1 |
Accident rate reflects accidents leading to lost workdays |
2 |
Working at the Burghausen site |
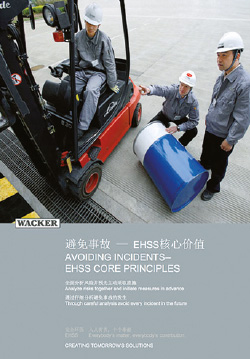
In 2009, the WACKER Greater China (WGC) subsidiary launched a safety and environmental-protection initiative at its sites. Management highlighted various aspects designed to raise employees’ awareness of their personal responsibilities. In this way, each employee’s job description was modified to include the topics targeted by the initiative. Patches bearing a motto were sewn onto work clothing, and online messages appeared automatically on computer screens after booting. These measures ensured that employees were constantly reminded of safety and environmental protection. “Our employees adopt a clean and safe approach to work,” said Guofa Zhu, in charge of the environmental protection and safety department. “And that’s how things should stay.” The initiative was a success: in 2009, WGC reported just 1.5 workplace accidents that involve days of absence, based on 1 million work hours; a year later, there were no notifiable accidents at all.
Practiced Safety
Safety-conscious conduct is reflected in low accident figures. Facilities without a reportable accident for sustained periods of time receive special recognition at WACKER. Some of these have also been honored by institutions outside the company.
In 2009, the NPCA/FCST, the American National Paint & Coatings Association, presented WACKER POLYMERS’ US operations with an award of honor for workplace safety. To be considered for the award, member companies had to meet certain criteria such as zero work days lost through work-related accidents over a five-year period.
In 2010, the South Korean government acknowledged WACKER POLYMERS’ excellent process safety management (PSM) at its site in Ulsan. The site earned the top grade P in the annual PSM inspection conducted by the Ministry of Labor and the Korea Occupational Safety and Health Agency (KOSHA). What’s more, the accident rate confirms Ulsan’s high safety awareness: not a single accident has occurred since 2000.
download table |
Safety Awards 2009/2010 |
|
| ||
Award |
Recipient |
Sponsor | ||
|
|
| ||
Annual Safety Award |
WACKER POLYMERS, |
NPCA/FCST | ||
Rated ‘P’ for process safety management |
WACKER POLYMERS, |
South Korean Ministry of Labor & Korea Occupational Safety and Health Agency |
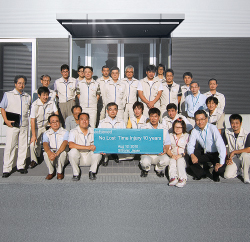
Employees at the Siltronic production site in Hikari, Japan, celebrated ten years without an accident in 2010. Located on the southwest coast of Japan’s main island of Honshu, Hikari produces silicon wafers for the semiconductor industry and monocrystals for other Siltronic sites and for the solar industry. According to the official Japanese definition, a company can only be recognized as accident-free for ten years if, during that time, not one of its employees has lost even a minute of work time due to injury. So what is the site’s secret? “We consistently apply the OHSAS international occupational safety standard,” reveals Dr. Atsuki Matsumura, the site president of Siltronic Japan. “And we learn from smaller incidents.” All WACKER sites – in addition to the company’s international Siltronic sites – are to be OHSAS-certified in the next few years.
The SAFE Storm Management System
The period under review also saw the WACKER Burghausen site participating in a storm research project known as SAFE (Sensor-Activated Severe Storm Early Warning System). As climate change results in more frequent and more intense storms, the SAFE project will make it possible to predict these storms earlier and to introduce action to avert the danger. The WACKER plant was the only industrial site to participate in the project, which was sponsored by the German Federal Ministry of Research. By networking new environmental sensors with existing weather stations and warning systems, the project created a sensor network whose data will be linked to cross-regional data (such as from satellites). The data can then be used in a new model for precise local forecasting that will give production sites fast, targeted weather warnings. Given the results of the research project, WACKER sees considerable benefit for its site from the storm warning system and will continue to run SAFE even after the trial studies have been completed.
Transport Safety
In order to make certain that its products are stored and transported safely, WACKER performs stringent vehicle inspections before loading materials for shipment – especially when those materials are hazardous. If a vehicle fails inspection, we continue sending it back until it passes. The failure rate, which has been low for many years, was 3.0 percent in 2010 for hazardous material shipments in Germany. WACKER audits hazardous goods shippers at least every two years.
In addition to monitoring hazardous materials shipments as prescribed by law, however, WACKER also makes sure that non-hazardous materials are transported safely. WACKER safety standards are often higher than the minimum requirements for shipping hazardous materials. Whenever possible, for instance, we do not ship chlorosilanes by truck – we prefer rail transport instead, using special safety rail tankers or shipping containers that meet the strictest safety standards.
We regularly review aspects of transport safety with our logistics providers, e.g. during our annual Shipping Day. If deficiencies are found, we agree on specific improvements and then follow up on their implementation. WACKER uses in-house criteria and internationally recognized systems, such as the Safety and Quality Assessment System (SQAS) operated by the European Chemical Industry Council (CEFIC), to select logistics service providers and evaluate their performance. Our evaluation criteria include driver qualifications and training, vehicle equipment and accident response. Through the use of standards and specifications, WACKER ensures that even the subcontractors working for our logistics providers meet the same requirements.
We recorded 10 transport accidents in 2009 and 2010. This number includes accidents involving the delivery of our products and intermediates where we commissioned the transport. What’s more, the shipping company’s evaluation includes incidents that do not involve hazardous goods, as well as those that do not adversely impact people or the environment.
download table |
Transport Accidents |
|
|
| |||
Number of Accidents |
2010 |
2009 |
2008 | |||
|
|
|
| |||
Road |
4 |
5 |
11 | |||
Rail |
1 |
– |
4 | |||
Sea |
– |
– |
2 | |||
Interior waterways |
– |
– |
– | |||
Air |
– |
– |
– |
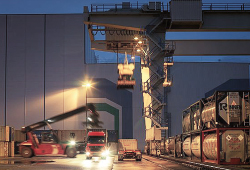
WACKER monitors the secure transport of both hazardous and non-hazardous goods.