To remain globally competitive, companies need to minimize their process costs. The Wacker Operating System (WOS) was launched in 2004 to boost WACKER productivity along the entire supply chain. The target figure is a 10-percent annual increase in productivity. WOS results are regularly reported to the Executive Board.
In 2009, our production facilities were running at very low capacity as a result of the financial crisis. WOS strategy was originally about cutting specific (volume-related) costs, but this was no longer sustainable in 2009. Instead, WOS was used to significantly lower overall costs. A year later, we reached our original goal, with specific production costs rising far less than production volumes. In 2010, WOS focused on the efficient use of raw materials and energy savings. In both years, WACKER carried out around 1,000 productivity projects worldwide.
Established by WACKER in 2009 to further cement WOS within the company, the WOS ACADEMY offers training in productivity topics. Participants are given hands-on training in specific projects at the various plants and are thus able to apply the methods immediately. The WOS ACADEMY instructors act as advisors during these projects. To foster sharing of experiences, a WOS Forum was set up.
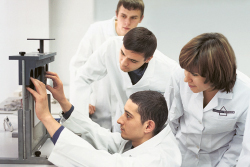
The WACKER ACADEMY in Moscow. This international facility offers the ideal platform for sector-specific networking between customers, sales partners and WACKER experts.
In 2007, WACKER launched its POWER PLUS energy-efficiency project for the Burghausen and Nünchritz sites, targeting a 10-percent reduction in specific energy consumption at both sites by late 2009 (base year: 2006). In 2009, we extended the program to our Cologne site. For further details of POWER PLUS, see Energy.
Siltronic also launched a productivity initiative, called Fab Improvement Program. In doing so, this business division is looking for ways to boost production capacity for 300 mm silicon wafers. Through standardized meetings and experience-sharing between the various shifts, Siltronic managed to raise its capacity by up to 10 percent. In late 2010, the program was extended to small-wafer production.