
“Product safety has to begin right here at the R&D stage.”
Christina Bauer
R&D Lab Technician,
Burghausen Plant
WACKER is continually working to prevent and reduce the use of substances which are harmful to human health or the environment in products and processes. We pursue this aim in a number of ways:
-
We try to replace harmful constituents with alternative substances.
-
In the absence of an alternative, we restrict the sale of products containing harmful substances to commercial and industrial customers wherever possible.
-
We develop innovative alternatives to conventional products containing harmful substances.
Product Information
We ensure that all our products, if used correctly, pose no risk to health or the environment. We continually update our product information and constantly revise our risk assessments to take account of new findings.
When advertising our products and services, we make sure that our brochures, for example, contain verifiable data, and precise, legally-compliant terminology and wording that reflect the current state of scientific knowledge. In 2010, WACKER POLYMERS issued “anti-greenwash” guidelines that stress the importance of publishing sound, factually correct information about products and services.
Only some 40 percent of WACKER products require safety data sheets by law. We compile these sheets for all chemical and biochemical sales products and issue over 54,000 data sheets in up to 33 languages.
WACKER publishes a wide range of information to ensure that substances and mixtures are handled correctly:
-
Designations of substances and mixtures
-
Potential risks
-
Composition and information about ingredients
-
First-aid measures
-
Fire-fighting measures
-
Response in the event of accidental release
-
Handling and storage
-
Restriction and monitoring of exposure / personal protective equipment
-
Physical and chemical properties
-
Stability and reactivity
-
Toxicological data
-
Environmental data
-
Notes on disposal
-
Transportation guidelines
-
Legislation and other information
Nanomaterials
We have recorded and assessed all the nanomaterials that we produce or use. Most of them are nanostructured – a classification that includes materials whose internal structures are nanoscale (between 1 and 100 nanometers), but whose dimensions are greater than the nano range. WACKER’s principal nanostructured products include HDK® pyrogenic silica, a powder used as a thickener, filler or flow enhancer. The physicochemical properties of the HDK® product group have been examined in detail, and extensive toxicological, eco-toxicological and epidemiological data exist.
In a joint project with the Technical University of Dresden, WACKER used new analytical techniques to measure workplace nanoparticle concentrations and sizes at our HDK® production facility in Nünchritz. The test results show that nanoparticle exposure does not increase during the bagging of nanostructured HDK®. It thus follows that employees engaged in this activity face no adverse health effects.
REACH
REACH legislation, which came into force in 2007, governs the registration, evaluation, authorization and restriction of chemicals within the European Union. Comprehensive data are gathered through REACH, which imposes new requirements on the manufacturers, importers and users of chemical products. On the European market, all substances used or imported in annual quantities exceeding one metric ton must be registered and evaluated. The scope of evaluation work is largely determined by the quantity of material produced or imported and the expected risks. Particularly high-risk substances are subject to regulatory approval.
For the chemical industry, the new legislation involves considerable effort and expense. WACKER estimates that REACH compliance will cost the company around €30 million. We have been preparing for REACH requirements since the EU Commission issued its white paper on chemicals policy in 2001. Our first step on the long journey toward REACH registration was to preregister phase-in substances produced in annual quantities exceeding one metric ton. We did this by the end of 2008, thus meeting the deadline. This step chiefly included substances listed in the European Inventory of Existing Commercial Chemical Substances (EINECS). We preregistered over 7,000 substances with the European Chemicals Agency (ECHA).
WACKER submitted its first registration dossier to the ECHA in 2009. In the following year, we successfully completed the first phase of substance registration in accordance with REACH requirements. The ECHA confirmed receipt of 85 dossiers and issued registration numbers for all the substances. WACKER is now entitled to produce these substances within the European Union without restriction and to supply them to EU member states.
In 2007, our Procurement department began asking our suppliers whether they have met the deadline for preregistering their substances and mixtures with the ECHA. We obtained information about our suppliers’ registration status in May and November 2010.
REACH demands extensive information about the properties of chemical products – which necessitates an increase in mandatory animal testing. WACKER makes every effort to avoid such testing and only performs ECHA-required tests. Whenever possible, we use recognized alternative methods, such as in-vitro tests. We classify substances with the same modes of action into groups for testing, and we work within REACH consortia to use scientific data from other companies on identical substances.
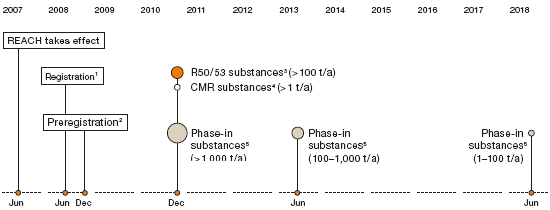
1 New substances > 1 metric ton/year
2 Phase-in substances > 1 metric ton/year
3 R50/53 substances: “highly toxic to aquatic organisms” and “may have long-term harmful effects in bodies of water”
4 CMR substances: carcinogenic, mutagenic or toxic to reproduction
5 Phase-in substances: predominantly old substances listed on the EINECS inventory (European Inventory of Existing Commercial Chemical Substances on the market before 1981)
GHS
GHS (Globally Harmonized System of Classification and Labeling of Chemicals) is a United Nations initiative for harmonizing the classification and labeling of hazardous substances. It is up to individual countries to decide whether to adopt the system, and, if so, when and how to go about it.
The EU Commission introduced GHS in Europe when the European Regulation on the Classification, Labeling and Packaging of Substances and Mixtures (the CLP Regulation) came into force in January 2009. On December 1, 2010, this new regulation replaced the existing directive on the classification and labeling of chemicals (Dangerous Substances Directive) and, from June 2015, it will also replace the Dangerous Preparations Directive.
WACKER met the year-end 2010 deadline for reclassifying all individual substances. Furthermore, we registered our substances in the EU Classification and Labeling Inventory by January 2011. We started adapting our safety data sheets to meet international GHS requirements back in 2007 and are continuing this process in line with the GHS implementation deadlines set for the countries to which we supply products. In 2010, we reclassified and labeled substances destined for Korea, Japan and Singapore according to GHS criteria.
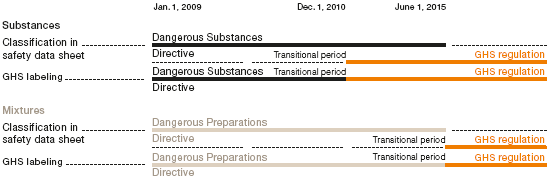
GHS implementation will cost WACKER around €3 million. For us, this system switchover means that every product must be checked, reclassified and relabeled. Within just a few years, we must reclassify tens of thousands of substances and mixtures, change all safety data sheets and redesign hazardous substance labels to take account of the new symbols.
download table |
Introduction of GHS |
|
|
| |||
Country/Economic Region |
Change of Safety Data Sheets |
Change of Labels |
Substances/Mixtures | |||
|
|
|
| |||
Brazil |
February 2011 |
February 2011 |
Substances | |||
China |
May 2011 |
May 2011 |
Substances and Mixtures | |||
European Union (EU) |
December 2010 |
December 2010 |
Substances | |||
European Economic Area |
June 2015 |
June 2015 |
Substances and Mixtures | |||
Indonesia |
September 2010 |
September 2010 |
Substances | |||
Japan |
January 2011 |
December 2006 |
100 Special Substances | |||
Malaysia |
June 2011 |
June 2011 |
Substances | |||
New Zealand |
July 2008 |
January 2011 |
Substances and Mixtures | |||
Switzerland |
December 2012 |
December 2012 |
Substances | |||
Serbia |
September 2011 |
September 2011 |
Substances | |||
Singapore |
December 2010 |
December 2010 |
Substances | |||
South Korea |
July 2010 |
July 2010 |
Substances | |||
Taiwan |
January 2009 |
January 2009 |
Substances and Mixtures | |||
Uruguay |
July 2010 |
July 2010 |
Substances and Mixtures |
GHS affects any employee involved with hazardous substances. It impacts not only production and laboratory workers (who handle GHS-labeled chemicals on a daily basis), but also safety officers (who prepare SOPs). Furthermore, employees who label vessels, piping and equipment have to know and be fully sensitized to the new hazard symbols. WACKER provides its employees with online training and a wide range of informative literature on GHS.
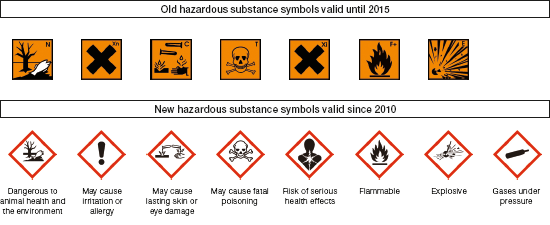
The GHS Regulation on the Classification and Labeling of Chemicals replaces the previous orange hazard symbols with new symbols consisting of a white diamond in a red frame.