Water is an extremely precious resource – not only as drinking water, but also as a raw material, solvent and coolant in many technical and chemical processes. At WACKER, we use water sparingly and always purify our wastewater as effectively as possible.
In 2009, water consumption rose by 10 percent groupwide compared with 2008. This increase was largely due to the fact that expansion stage 8 at Burghausen’s polysilicon production facility had gone on stream. The year-round operation of the new recooling plant at Burghausen meant that in 2010 the Group used around 5 percent less cooling water than it did in 2009. This reduction has consequences for water consumption.
Most of the water used at Nünchritz comes from an on-site well. Drinking water accounts for just 1 percent of our total water consumption at this site.
Compared with conventional fermentation methods, our new process for the bacterial production of pharmaceutical proteins (biologics) has cut emissions to air and water by half at our biotech facility in Jena. This success can be attributed to our DENSETEC® (high-cell density fermentation) and ESETEC® (expression and secretion system) technologies, which enable us to produce biologics in higher yields. The process utilizes ultrapure water obtained from drinking water.
By modifying production processes, our Siltronic division has reduced its use of chemicals, for example in wafer cleaning tanks. As a result, nitrate loads in the wastewater at Siltronic’s sites have fallen by 70 percent over the last ten years. We reuse water several times over, wherever the purity requirements for wafer manufacturing permit. This has allowed us to reduce consumption of demineralized (deionized) water by 20 percent in Burghausen and 30 percent in Portland over the last ten years without compromising on quality.
Our Ulsan site in South Korea uses process reactors in the production of dispersions, which are now mostly cleaned with the aid of polishing machines. As a result, we used 55 percent less water and 73 percent less detergent in 2010 than we did in 2003. The new cleaning process, which involves spraying atomized rinsing water from nozzles, has also improved production quality and increased throughput, thus increasing energy efficiency.
The chemical oxygen demand (COD) fell significantly in 2009 due to the closure of our site in South Brunswick (New Jersey, USA).
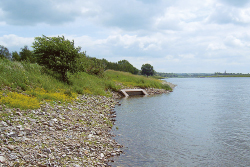
At our site in Nünchritz, we have investigated the biological quality of the water in the head and tailrace of the discharge from the wastewater treatment system into the Elbe river. We have not detected any adverse changes to water quality in this Elbe river habitat. Overall, the Elbe’s water quality has improved in recent years, and fish stocks are now flourishing. “Anglers like to fish around the outlet of our wastewater treatment plant as the water there is so clear”, explains Wolfgang Semmler, head of Environmental Protection and Safety at Nünchritz.
download table |
Water Consumption/Emissions to Water1 |
|
|
| |||
|
2010 |
2009 |
2008 | |||
|
|
|
| |||
Water consumption (m3) |
252,151,000 |
264,532,000 |
241,286,375 | |||
Cooling water volume (m3) |
233,153,000 |
248,061,000 |
218,310,0003 | |||
Wastewater volume2 (m3) |
21,031,000 |
20,002,000 |
22,074,455 | |||
COD (chemical oxygen demand)4 (t) |
1,820 |
2,730 |
4,782 | |||
AOX (adsorbable organic halides)4 (t) |
6 |
6 |
7 | |||
Heavy metals4 (t) |
1.3 |
1.6 |
1.7 | |||
Nitrogen4 (t) |
420 |
410 |
460 | |||
Phosphorus4 (t) |
7.0 |
5.4 |
9.1 |
1 |
Excluding the silicon-metal plant in Holla, Norway |
2 |
Excluding cooling water |
3 |
During the acquisition of current data, the original value (252,310,068 m3) was subsequently corrected to take account of new findings |
4 |
Taking into account internal and/or external wastewater treatment for all sites as of the 2010 reporting year |