Sustainability
Managing Sustainability
Companies can be profitable in the long term only if they assume responsibility for the environment and society. Sustainability has been firmly rooted in our business processes for many years. Its importance to our company is shown by the fact that we have made sustainability one of our five strategic goals and have compiled our own Code of Sustainability. Sustainable development means balancing economic, ecological and social factors in everything we do.
Two voluntary global initiatives form the basis for sustainable corporate management at WACKER: the chemical industry’s Responsible Care ® initiative and the UN’s Global Compact. These voluntary measures to protect the environment, employees and society go beyond what is legally required. We also expect our suppliers to observe the principles of the UN’s Global Compact and the Responsible Care ® initiative, and have anchored this in our general terms of procurement.
WACKER made substantial progress on strategic sustainability-management projects in 2015.
- Regional Emphasis
In 2015, the USA was the focal region of WACKER’s sustainability management, and we examined the environmental, health and safety aspects of individual sites, including the new plant in Charleston, Tennessee.
- Group Certificate
Our Group certification program ensures that customer-driven specifications and our corporate standards are implemented at all WACKER sites. Almost all WACKER production sites are included in the Group certification program. Exceptions to this are the sites in Brazil, the Kolkata plant belonging to Wacker Metroark Chemicals Pvt. Ltd., India, and the WACKER BIOSOLUTIONS site in Halle, Germany. All these sites, however, have corresponding individual certificates. As of 2012, all sites belonging to Wacker Chemie AG, Siltronic AG and Alzwerke GmbH have been certified to ISO 50001 (energy management systems). Wacker Biotech GmbH, DRAWIN Vertriebs-GmbH and Wacker-Chemie Versicherungsvermittlung GmbH began introducing this standard during the reporting year. The silicone-producing sites in Burghausen and Nünchritz (Germany), Jandira (Brazil), Zhangjiagang (China) and Amtala (India) have been certified to ISO 22716 for the cosmetics industry.
- Greenhouse Gas Emissions
The Group’s corporate CO2 footprint report is an important tool for improving climate protection. We have been calculating our indirect greenhouse-gas emissions in accordance with the Greenhouse Gas Protocol Scope 3 Accounting and Reporting Standard since 2012. These emissions include all those generated along the supply chain, e. g. by suppliers or through waste disposal and the transportation of products. In 2015, we also started calculating downstream transportation routes in accordance with Scope 3. In addition, calculations of our carbon footprint now include the effects of procured products and handling of our sales products right to the end of the product lifecycle.
- Sustainability Platform
In 2015, groupwide implementation of our new IT system for sustainability reporting (SPIRIT) was completed, thereby replacing various individual systems. We use this software to record environmental and safety-related events, for example, and to manage internal and external Integrated Management System (IMS) audits. Over 4,000 Group employees used SPIRIT during the year under review.
Sustainability Report Published
In 2015, WACKER published its Sustainability Report for 201 3/2014. The company again published the report exclusively as an online version – also in the interests of environmental protection. The report fully meets the G3 guidelines set by the Global Reporting Initiative (GRI). GRI accorded the report an A, its highest application level.
Compliance Management Reports Increase in Cybercrime Activities
WACKER’s ethical principles of corporate management go above and beyond the legal requirements. There are 24 compliance officers available worldwide to answer employee inquiries. They are based in Germany, the USA, China, Taiwan, Japan, India, South Korea, Brazil, Mexico, Singapore, Russia and the United Arab Emirates. Compliance issues arising in countries other than those listed are handled in Germany by the Chief Compliance Officer. When Siltronic AG went public in the reporting year, a Chief Compliance Officer was also named for this Group subsidiary. We named a compliance officer for the new polysilicon site in Tennessee, USA, as well.
Employees are instructed to inform their supervisors, the compliance officers, the employee council or their designated HR contacts if they notice any violations. In 2015, Compliance Management consulted with the international sites to ensure that globally applicable measures comply with local requirements. Another focus was the continued prevention of cybercrime.
Workplace and Plant Safety -1,600 Machines Inspected
Operating plants and processes in a manner that poses no risk to people or the environment is an important objective at WACKER. To this end, we have installed a groupwide safety management system that addresses both workplace and plant safety. In 2015, we completed alignment of our processes and workplace safety standards with the international OHSAS 18001 standard.
Systematic workplace safety includes regular evaluation of hazards and work-area monitoring. The first step in ensuring plant safety is to systematically identify risks and assess them. This includes analyzing how well we control the energy present in a process (e. g. pressure, heat) and determining the effect that a single error might have on a chain of events that could lead to the escape of a substance or to an accident. On completion of this comprehensive analysis, we specify safety measures to prevent undesirable incidents.
One area of focus since 2013 has been on machine safety as part of our ANSIKO project. By the end of 2015, experts had inspected around 1,600 machines at all sites all over the globe. We then used their recommendations to make these machines even safer for our employees.
WACKER attaches particular importance to providing its safety experts with ongoing training. We hold regular training sessions on topics such as plant safety. During the reporting year, we conducted training for our specialists in Adrian (USA), in particular in the area of explosion damage protection. We also carried out safety inspections at the US sites in Adrian, Calvert City and Eddyville. Safety experts from Germany assisted with commissioning of the new Charleston site.
Our goal for occupational safety in 2015 was to reduce our groupwide accident rate (the number of workplace accidents per million hours worked) to below 2.0. We did not reach this target, having 2.6 workplace accidents with missed workdays per 1 million hours worked groupwide in the reporting year. In terms of reportable accidents (accidents with more than three days of absence), WACKER’s numbers are far better than the German chemical industry average. The reportable accident rate in 2015 was 1.0 per 1 million hours worked (2014: 1.2), whereas in 2014, Germany’s BG RCI (the statutory employer liability insurance carrier of the basic materials and chemical industries) registered 9.3 reportable accidents per 1 million hours worked in chemical companies. Very few of the accidents at WACKER are chemical in nature. The most common causes are tripping, slipping, falling, and inattentiveness during manual activities. Not satisfied with our accident rate, we are stepping up our occupational-safety efforts. We are systematically implementing our new WACKER Safety Plus (WSP) program, which incorporates elements of successful safety strategies at sites with particularly low accident rates. Such elements include safety patrols, discussions with the workforce and emergency drills. The goal of WACKER Safety Plus is to recognize and avoid unsafe behavior – on the way to and from work, in the office, at the plant, when operating machinery, or when handling chemicals.
At its German sites, WACKER placed particular emphasis in 2015 on reviewing and updating hazard assessments. As a consequence, we have improved protection strategies and safety measures in many areas. The program will be continued at all German sites in 2016.
Workplace Accidents Involving Permanent Staff and Temporary Workers
Download XLS |
|
|
|
||||||||||||||||
Number |
2015 |
2014 |
2013 |
2012 |
2011 |
2010 |
2009 |
|||||||||||
|
|
|
|
|
|
|
|
|||||||||||
|
||||||||||||||||||
Accident rate for Group employees: accidents1 per 1 million hours worked |
2.6 |
2.8 |
3.8 |
4.7 |
3.9 |
4.3 |
4.0 |
|||||||||||
Accident rate for Group employees: reportable accidents2 per 1 million hours worked |
1.0 |
1.2 |
1.4 |
2.1 |
1.4 |
1.2 |
1.2 |
|||||||||||
|
|
|
|
|
|
|
|
Safe Transport of Hazardous Materials
WACKER ensures that its products are safely transported and stored. We carefully inspect vehicles before loading them, especially if hazardous goods are involved. In 2015, we had inspections carried out on over 7,000 trucks. If a vehicle fails an inspection, we refuse to deploy it until the defects have been remedied. Failure rates have been low for years now. In 2015, the rate was about 1.5 percent for hazardous goods shipments in Germany (2014: 0.3 percent). WACKER regularly audits its hazardous goods shippers.
We also review aspects of transport safety with our logistics providers. If deficiencies are found, we agree on improvements and then follow up on their implementation. When selecting logistics service providers and evaluating their performance, WACKER uses in-house criteria and internationally recognized systems, such as the Safety and Quality Assessment System (SQAS) operated by the European Chemical Industry Council (Cefic). Through the use of standards and specifications, WACKER ensures that even the subcontractors working for our logistics providers meet our stringent safety requirements.
In 2015, we recorded 13 transport incidents (2014: 8). This number includes accidents occurring during distribution of our intermediates and products in cases where we commissioned the transport. It also includes incidents not involving hazardous goods, whether or not they adversely impact people or the environment.
For high-risk products, we use packaging and tanks that meet the highest quality standards – in some cases exceeding statutory requirements.
Transport Accidents
Download XLS |
|
|
|
||||||||||||
Number of Accidents |
2015 |
2014 |
2013 |
2012 |
2011 |
2010 |
2009 |
|||||||
|
|
|
|
|
|
|
|
|||||||
Road |
10 |
5 |
4 |
8 |
6 |
4 |
5 |
|||||||
Rail |
2 |
2 |
1 |
2 |
1 |
1 |
– |
|||||||
Sea |
1 |
1 |
2 |
– |
1 |
– |
– |
|||||||
Inland waterways |
– |
– |
1 |
– |
– |
– |
– |
|||||||
Air |
– |
– |
– |
– |
– |
– |
– |
|||||||
|
|
|
|
|
|
|
|
Experiment Kit Wins Award and Commitment to Refugees
A company can be successful only if it enjoys the trust of the public, which is why we take our social responsibilities seriously, especially in communities around our sites. Training young people in the natural sciences is especially important to us because we need dedicated scientists and engineers in order to remain competitive.
WACKER continued work on its CHEM2DO experiment kit during the reporting year. After two years of seeing how the kit was used in practice, we adapted the 2012 edition to better reflect both the situation in the schools and the students’ prior knowledge. The new edition has been available since autumn of 2015. Germany’s federal SCHULEWIRTSCHAFT association presented Wacker Chemie AG with first place for the 2015 SCHULEWIRTSCHAFT “That has potential!” award in the Beginners – Large Companies category for its CHEM2DO Experiment Kit. This network awards its prize to active companies committed to improving job prospects for students. WACKER once again sponsored the Dresden / East Saxony regional heat of Young Scientists in 2015.
We attach particular importance to projects that help children and young people. In 2007, we began supporting Die Arche (The Ark), a Munich-based Christian charity for children and adolescents. The initiative, which works with around 400 children and young people from socially disadvantaged families, including refugee children, provides children with hot meals and extra tutoring, organizes leisure activities and offers counseling. In the reporting year, WACKER presented its ninth annual donation of € 100,000 to the charity’s Munich branch.
WACKER’s own Burghausen Vocational Training Center (BBiW) accommodated four unaccompanied adolescent refugees from Afghanistan in its youth guest house in 2015. Along with the eight African refugees taken in by WACKER in 2014, the company is now helping to integrate twelve displaced young people. The refugees are taking intensive German lessons to help them in their new life in Germany. They are also taking an integration class at the Mühldorf vocational school with the goal of obtaining the necessary educational qualification for vocational training.
New WACKER HILFSFONDS Project
Large areas of Nepal were devastated by two severe earthquakes in the spring of 2015, and the country still has not recovered from the disaster. According to UNICEF estimates, 400,000 people, one-fourth of them children, were ill-prepared for the onset of winter, more than half a year after the earthquake.
WACKER HILFSFONDS, our foundation for disaster aid, asked employees last year to make a donation to Namaste Nepal S-GmbH, a student charity based in Freiberg, Germany. The project was founded in 2015 by students at Geschwister-Scholl-Gymnasium secondary school, with the aim of cooperating with a Nepalese aid organization in building schools and preschools in the Sindhupalchok province. Wacker Chemie AG is taking part in the fundraising campaign by making an initial donation of € 50,000 and then matching employees’ donations.
Environmental Protection
WACKER attaches particular importance to integrated environmental protection, which commences with product development and plant planning. Our environmental protection measures often surpass statutory requirements – in the spirit of the central idea behind the Responsible Care ® initiative. WACKER constantly works on improving its production processes, with the aim of conserving resources. One of our main tasks is to close material loops and recycle byproducts from other areas back into production, enabling us to reduce or prevent emissions and waste.
Our commitment to environmental protection is visible in the awards we have won. For example, in 2015, the Association of International Chemical Manufacturers (AICM) in Beijing presented the Responsible Care® Chairman Award to WACKER Greater China for the second time. WACKER received the 2015 GreenFleet award for its sustainable fleet and passenger transport strategy. The award was conferred by FleetCompany GmbH, a subsidiary of TÜV Süd (the German association for technical inspection). The jury honored WACKER for using environmentally friendly vehicles, keeping passenger transports and business trips to a minimum, organizing shuttle services, and maintaining a fleet of on-site bicycles.
In 2015, WACKER invested € 5.7 million in environmental protection (2014: € 5.1 million). In the same period, environmental operating costs amounted to € 83.8 million (2014: € 88.2 million). Our silicon-metal plant in Holla (Norway), which we acquired in 2010, has been included in our environmental performance indicators since 2011. Metallurgical production at the site is quite different from WACKER’s typical chemical operations with respect to environmental impact. Airborne emissions, in particular, have risen as a result of the acquisition. Accounting for environmental performance indicators has included consolidated reporting on the new pharmaceutical site in Halle since 2015. The Charleston site reported environmental performance indicators for the commissioning phase in 2015.
Water Consumption Tested Using the Global Water Tool ©
In many parts of the world, clean water is particularly scarce, and obtaining and purifying water is very expensive. As a global player, we take such conditions into account in our production processes and during transport. We use the Global Water Tool © (GWT) developed by the World Business Council for Sustainable Development (WBCSD) to analyze the annual relative water stress index of the countries in which our main global production sites are located. This assessment has been conducted since 2012, based on analyses using the water stress index developed by the Water Systems Analysis Group of the University of New Hampshire, USA. This index provides information on the relationship between water consumption and the availability of renewable fresh water. The outcome of the analysis is that our most important production sites are located in regions with a low relative water stress index. These regions account for more than 97 percent of our annual water use and over 90 percent of our production volume. Production sites in countries for which no GWT-based water stress index information is available account for less than 0.5 percent of our water consumption.
One of our goals is to ensure even better protection of rivers and other surface water against the escape of harmful substances. In 2015, we identified potential groupwide risks to water and researched possible countermeasures. As part of our plant safety plans, we have developed additional measures for further enhancing protection. We have completed a project at the Burghausen site for improving protection of the Salzach river. We have further minimized the risk of water pollution caused by harmful substances leaking out from our direct-stream cooling system. To this end, we have, for example, shortened test equipment intervals and safeguarded our cooling water using secondary loops. In 2015, Wacker Chemie AG joined together with seven other companies from ChemDelta Bavaria to form the Naturnahe Alz association. The aim of this environmental initiative is to support the state of Bavaria in renaturalizing the Alz river and enhancing its ecosystem over the long term.
In 2015, we applied for a permit as required under German water law that will allow us to extract more groundwater at the Burghausen site in the future. We want to ensure the quality of our ultrapure water supply and, in particular, to bridge periods of poor-quality surface water. We will implement an extensive monitoring program when extracting groundwater. This will include measuring groundwater levels and discharge at three streams in the Haiming municipality and carrying out a functional check of the habitats in the riparian woodland, including evaluations of the status of conservation. Our aim is to ensure that groundwater extraction does not have a negative impact on the environment.
At the Burghausen site, WACKER SILICONES reduced the organic burden within the effluent feed to the biological wastewater treatment plant by means of Fentox® split-stream treatment. Over the last six years, we have gradually reduced the volume of harmful substances emitted into the Salzach river. We switched the biological wastewater treatment plant’s first bio-stage from double-tank to single-tank mode and started operation of an additional intermediate wastewater storage tank. We use it to collect peak pollutant loads so that they can be fed into the biological wastewater treatment system in a controlled manner during phases of low influent from production. The consistent feed-in supply leads to more stable operation of the biological wastewater treatment plant. Emissions of organic pollutants to the Salzach river have decreased by 42 percent since 2010. “Save Wastewater and Make a Profit” was the title of a special Employee Suggestion Program initiative that took place at the Nünchritz site from December 2014 to September 2015. The purpose of the initiative was to encourage employees to develop ideas for conserving and recycling water in production, thereby raising their general awareness for reducing wastewater. In the course of the initiative, wastewater in the central wastewater treatment plant at Nünchritz went down by some 5 percent.
Carbon dioxide emissions (Scope 1) were reduced groupwide by 1.4 percent, while NOx emissions fell by around 4 percent. At the Freiberg site, Siltronic took a third stage of the NOx scrubber into operation. We modernized a burner stage of the steam generator in Nünchritz. We reduced our NOx emissions in Nünchritz by cutting the amount of waste that is thermally processed. Extending the operating time of the gas turbine in our Burghausen power plant had a positive effect on NOx emissions.
At WACKER BIOSOLUTIONS’ Eddyville site in Iowa (USA), optimization of apparatus maintenance and solvent recovery has enabled us to continuously reduce NMVOC emissions since 2012 by 33 percent. NMVOC emissions rose groupwide due to increases in production.
At the Burghausen site, we commissioned a facility to recover 2,400 metric tons per annum of ethylene – previously disposed of in the waste-gas generator there – and utilize it for VAM production at WACKER POLYMERS.
In the reporting year, we also recorded waste at the Burghausen site that was not generated during production, but rather during construction and investment activities, e. g. rubble, scrap steel and paper. The amounts of waste produced in the period 2009 through 2014 were amended retroactively. The overall volume of waste generated decreased by around 3 percent groupwide in the reporting year.
Ever since WACKER acquired the Norwegian site in Holla in 2010, the main focus there has been on ongoing improvements to environmental protection efforts for the site’s energy-intensive silicon-metal production facilities. For example, maintenance was optimized for equipment that removes dust from silicon-metal production. These measures have significantly reduced emissions. While 3 kilograms of dust were emitted per metric ton of product in 2014, this figure was down to 2.5 kilograms in the reporting year, a specific reduction of 20 percent.
Environmental Indicators from 2009 to 2015
Download XLS |
|
|
|
||||||||||||||||||||||
|
2015 |
2014 |
2013 |
2012 |
2011 |
2010 |
2009 |
|||||||||||||||||
|
|
|
|
|
|
|
|
|||||||||||||||||
|
||||||||||||||||||||||||
Air |
|
|
|
|
|
|
|
|||||||||||||||||
CO2 emissions1 |
|
|
|
|
|
|
|
|||||||||||||||||
Direct (kt) |
1,234 |
1,251 |
1,253 |
1,311 |
1,341 |
986 |
969 |
|||||||||||||||||
Indirect (kt) |
1,544 |
1,420 |
1,241 |
1,133 |
1,075 |
– |
– |
|||||||||||||||||
NOX nitrogen oxides (t)2 |
1,910 |
1,990 |
2,010 |
2,225 |
2,221 |
926 |
963 |
|||||||||||||||||
Non-methane volatile organic compounds (NMVOCs) (t)3 |
910 |
870 |
830 |
800 |
750 |
700 |
610 |
|||||||||||||||||
|
|
|
|
|
|
|
|
|||||||||||||||||
Water |
|
|
|
|
|
|
|
|||||||||||||||||
Water consumption (thousand m3) |
237,060 |
241,973 |
220,908 |
242,072 |
268,657 |
252,151 |
264,532 |
|||||||||||||||||
Chemical oxygen demand (COD) (t) |
1,150 |
1,230 |
1,320 |
1,460 |
1,680 |
1,820 |
2,730 |
|||||||||||||||||
Halogenated organic hydrocarbons (AOX) (t) |
2 |
2 |
2 |
3 |
5 |
6 |
6 |
|||||||||||||||||
|
|
|
|
|
|
|
|
|||||||||||||||||
Waste4 |
|
|
|
|
|
|
|
|||||||||||||||||
Disposed of (t) |
46,490 |
51,570 |
39,210 |
41,340 |
46,640 |
48,620 |
84,310 |
|||||||||||||||||
Recycled (t) |
121,420 |
121,540 |
124,040 |
114,330 |
110,920 |
91,970 |
73,550 |
|||||||||||||||||
Hazardous (t) |
75,520 |
78,330 |
78,910 |
70,910 |
73,950 |
71,340 |
102,200 |
|||||||||||||||||
Non-hazardous (t) |
92,390 |
94,780 |
84,340 |
84,760 |
83,610 |
69,250 |
55,660 |
|||||||||||||||||
|
|
|
|
|
|
|
|
|||||||||||||||||
Energy5 |
|
|
|
|
|
|
|
|||||||||||||||||
Electricity consumption (GWh) |
5,147 |
4,926 |
4,521 |
4,519 |
4,277 |
3,623 |
2,568 |
|||||||||||||||||
Primary energy consumption |
|
|
|
|
|
|
|
|||||||||||||||||
Of which |
|
|
|
|
|
|
|
|||||||||||||||||
Natural gas (GWh) |
5,029 |
4,975 |
5,051 |
5,927 |
5,771 |
5,463 |
5,378 |
|||||||||||||||||
Solid fuels (coal, charcoal, wood) (GWh) |
768 |
839 |
872 |
862 |
886 |
432 |
– |
|||||||||||||||||
Heat supplied by third parties (steam and district heating) (GWh) |
245 |
242 |
236 |
223 |
218 |
228 |
209 |
|||||||||||||||||
Heating oil (GWh) |
20 |
20 |
17 |
18 |
16 |
13 |
8 |
|||||||||||||||||
|
|
|
|
|
|
|
|
Our indirect CO2 emissions from procured energy (as per Greenhouse Gas Protocol Scope 2) rose to 1,544 kt in 2015 (2014: 1,420 kt). The rise is due to the inclusion of emissions from electricity consumption for 300 mm wafer production in Singapore, increased production volumes at Burghausen and Nünchritz, and the higher emissions factor for electricity generation in Germany (data in accordance with “CO2 Emissions from Fuel Combustion, 2015 Edition” published by the International Energy Agency). We used energy-efficiency measures to reduce weighted specific energy consumption and related specific CO2 emissions – while maintaining a comparable product portfolio.
The Group’s corporate CO2 footprint report is an important tool for improving climate protection. Accordingly, in addition to starting in 2011 to track our indirect greenhouse gas emissions from procured energy (in accordance with Greenhouse Gas Protocol Scope 2), we have also been measuring our Scope 3 emissions since 2012. These include all emissions generated along the supply chain, e. g. by suppliers or through waste disposal and the transport of products. In 2015, we once again provided this emissions data to the Carbon Disclosure Project (CDP), which WACKER joined in 2007. Founded in London in 2000, CDP is a not-for-profit organization working to achieve greater transparency in greenhouse gas emissions.
Wacker Chemie AG once again improved its annual sustainability rating bestowed by CDP. Achieving a disclosure score of 97 out of a possible 100 points and a performance score of B on a scale of A to E, we are above average in the Energy & Materials category. WACKER is among the leading companies listed in the MDAX index.
Product Stewardship
WACKER takes environmental, health and safety aspects into consideration at every stage of the product lifecycle. In research and development projects, we examine the sustainability aspects of our new products and processes, starting with the raw materials used. We try to minimize raw-material consumption while selecting materials that offer maximum ecological benefit. Our products are generally supplied to business customers for further processing – not directly to end customers. Our lifecycle assessments (LCAs) look at the environmental impact caused by a specific product family throughout its lifecycle – a “cradle-to-gate” assessment extending from manufacturing to the factory gate. They allow us to gage the sustainability of our products and production processes, and to improve them accordingly. Our evaluations factor in the material, water and energy consumption of a product, as well as its ecotoxicity, over the entire lifecycle. With the help of the WACKER EcoWheel ®, we identify key sustainability topics and, together with our customers, set priorities for research projects.
Product Lifecycles
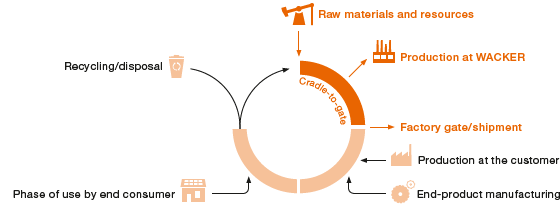
Energy Management
The chemical industry is one of the most energy-intensive sectors. In Germany alone, it uses around 20 percent of all the electricity consumed by industry. That is why WACKER, too, is continually improving the energy efficiency of its processes. This enables us to remain globally competitive while at the same time contributing to climate protection. Many chemical reactions generate heat that can be put to use in other production processes. We have been using integrated heat-recovery systems in Burghausen and Nünchritz for years and are continually improving them. In this way, we can reduce the amount of primary energy (as a rule, natural gas) consumed by our power plants.
To enhance energy efficiency and reduce specific energy consumption (amount of energy per unit of net production output), the Executive Board has defined energy targets for WACKER Germany. Our original goal was to reduce weighted specific energy consumption by one-third between 2007 and 2022, but we had already achieved that by 2014. We have now set a goal of reducing specific energy consumption by half of the 2007 level by the year 2022. Our energy goals ensure that we meet one of the requirements of the energy management system as per ISO 50001, a standard that we have introduced and certified at all sites of Wacker Chemie AG, Siltronic AG and Alzwerke GmbH in Germany. Accordingly, we introduced an energy management system three years before it even became mandatory to do so in 2015.
Generating Energy Efficiently
Burghausen uses hydroelectric power to generate electricity. Our Norwegian site, Holla, also generates its electricity mainly from water power. Our primary source of energy, though, is climate-friendly natural gas. At WACKER’s major sites in Burghausen and Nünchritz, we produce steam and electricity using cogeneration systems. These combined heat and power (CHP) plants are highly efficient, with more than 80-percent fuel efficiency, which is significantly higher than that of conventional plants generating electricity and heat separately.
Electricity Supply
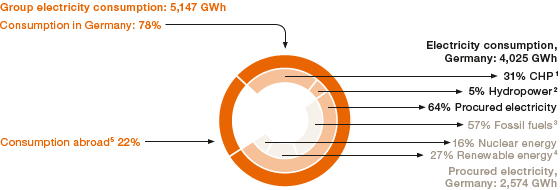
1 Burghausen
2 Burghausen
3 Coal, lignite, oil, gas; modified calculation method: since 2014, data has been in line with Germany’s energy mix; source: BDEW (German Association of Energy and Water Industries); status as of Nov. 2015, for the year 2014
4 Hydro, wind, solar power; modified calculation method: since 2014, data in line with Germany’s energy mix; source: BDEW (German Association of Energy and Water Industries)
5 Outside Germany, we purchase electricity from third parties based on the local standard energy mix
While absolute electricity consumption rose slightly to 5,147 GWh in 2015 (2014: 4,926 GWh), we were able to reduce specific energy consumption with energy-efficiency measures. The rise in absolute consumption stemmed from high polysilicon-plant utilization throughout the year and from including 300 mm wafer production in Singapore in the energy report. The Group’s power plants – the hydroelectric and CHP plants in Burghausen and the power plant in Nünchritz – produced around 1,451 GWh in 2015 (2014: 1,405 GWh). This means that WACKER covered almost 30 percent of its total energy requirements from its own production. Groupwide, carbon dioxide emissions from captive power plants subject to emissions trading rules and from silicon-metal production in Holla (Norway) totaled about 1.1 million metric tons in the reporting period (2014: 1.1 million metric tons).
WACKER is subject to the regulations of the EU emissions trading system because of its CHP plants at the Burghausen and Nünchritz sites. Procurement of emission allowances has been included in energy-procurement planning since 2013. Having achieved a surplus in the second trading period (2008 through 2012), we did not have to purchase additional emission allowances for 2013. We have covered shortfalls since 2014 by buying emission allowances for facilities subject to emissions trading.
WACKER’s German production sites accounted for 78 percent (2014: 79 percent) of its total electricity needs. In Germany, WACKER purchased 64 percent (2014: 64 percent) of the electricity it required. In line with the German energy mix, 57 percent of this electricity was generated from fossil fuels (2014: 56 percent), with 16 percent coming from nuclear energy (2014: 15 percent) and 27 percent from renewable energy sources (2014: 26 percent). Heat consumption, which includes the use of solid carbon-based and biogenic fuels (coal, charcoal, wood) for silicon-metal production at Holla (Norway), fell marginally across the Group to 3,520 GWh (2014: 3,571 GWh).
Energy Consumption1
Download XLS |
|
|
|
||||||||||||||||||
GWh |
2015 |
2014 |
2013 |
2012 |
2011 |
2010 |
2009 |
|||||||||||||
|
|
|
|
|
|
|
|
|||||||||||||
|
||||||||||||||||||||
Electricity consumption |
5,147 |
4,926 |
4,521 |
4,519 |
4,277 |
3,623 |
2,568 |
|||||||||||||
Heat consumption2 |
3,520 |
3,571 |
3,709 |
3,734 |
3,828 |
3,321 |
2,738 |
|||||||||||||
|
|
|
|
|
|
|
|
|||||||||||||
Primary energy use (total) |
6,062 |
6,081 |
6,176 |
7,030 |
6,891 |
6,136 |
5,595 |
|||||||||||||
Of which |
|
|
|
|
|
|
|
|||||||||||||
Natural gas |
5,029 |
4,975 |
5,051 |
5,927 |
5,771 |
5,463 |
5,378 |
|||||||||||||
Solid fuels3 (coal, charcoal, wood) |
768 |
839 |
872 |
862 |
886 |
432 |
– |
|||||||||||||
Heat supplied by third parties (steam and district heating) |
245 |
242 |
236 |
223 |
218 |
228 |
209 |
|||||||||||||
Fuel oil |
20 |
20 |
17 |
18 |
16 |
13 |
8 |
|||||||||||||
|
|
|
|
|
|
|
|