Calvert City – 4,000 Tank Trucks Full
One of the world’s largest dispersion reactors has just come on stream in Calvert City, Kentucky. WACKER has invested around € 50 million in the site, and the new facility is a clear indicator that the market for polymers in America still has plenty of potential.
The Americas

4,000 Tank Trucks Full
One of the world’s largest dispersion reactors has just come on stream in Calvert City, Kentucky. WACKER has invested around € 50 million in the site, and the new facility is a clear indicator that the market for polymers in America still has plenty of potential.
Products
VINNAPAS® dispersible polymer powders polymer dispersions
Employees
Approx. 110
LAND Area
60,000 m2
Mary Beth Hudson is doing one of her rounds of the premises. It is early morning, and the sun has barely warmed the clear Kentucky air. The metal pipes above the visitors’ heads point the way to the new reactor, already casting clearly defined shadows on the ground.
“I want to see how painting of the new building is coming along,” says Hudson, head of WACKER’s polymer plant in Calvert City. The facade of the new reactor, which the employees simply refer to as “CC6,” is being painted in the light gray color typical of WACKER. Inside the reactor building, everything has been running according to plan for many months.
High Product Quality
From a vantage point at the very top of the stairs in the new building, you can see a very thick stirring rod protruding from the gleaming silver reaction vessel. It rotates at 64 rpm, blending liquid vinyl acetate monomer with ethylene gas. The new reactor has an annual production capacity of 85,000 metric tons of vinyl acetate-ethylene copolymer dispersion – better known as VINNAPAS®. That is more than 4,000 tank trucks full. It is probably the biggest reactor for VAE dispersions in the world. Together with the other five reactors already in place at the Calvert City plant, the new reactor will help meet the growing demand for polymeric binders in North and South America.
In the new laboratory next door, two employees are analyzing the bright white dispersion produced in the reactor – and they are satisfied with the results. Since CC6 gradually began ramping up last summer, the facility has been manufacturing binders of the highest quality – no rejects and no second-rate product. “It’s all gone exceptionally smoothly,” says Hudson, smiling.
Her contentment is also evident back in her office, where she views the production figures on screen: in 2015, the two spray dryers, which turn the dispersions into dispersible polymer powders, had the highest utilization rates since 2007, a record Hudson expects will be broken again in 2016. Dispersions are performing well, too. In the region supplied by the Calvert City plant, WACKER already has a market share of 50 percent for VAE dispersions, and the new capacity expansion underscores that the American market promises WACKER huge growth potential.
Diverse Application Areas
Only a small portion of the dispersions produced in Calvert City are processed into dispersible polymer powders on site, something that sets the region apart from both Europe and Asia. The lion’s share of the dispersions made in Calvert City are shipped by road or rail to customers in North, Central and South America. The plant’s location close to America’s Midwest makes it an ideal hub. Whereas people from America’s East and West Coasts joke about Kentucky as a “flyover state” – viewed only from high above through an airplane window – WACKER appreciates its good transport infrastructure, which includes the Ohio River, rail lines and highways. “From here, we can reach three-quarters of our customers in just a few days,” says Hudson.
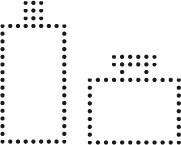
Product Portfolio
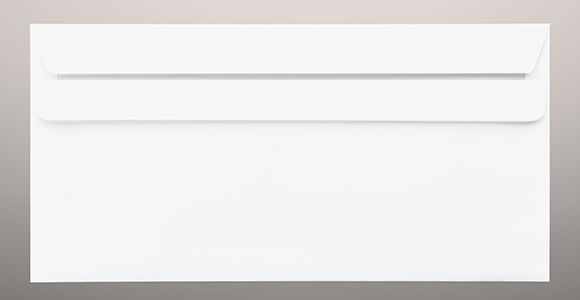
Excellent ability to adhere to difficult-to-bond substrates
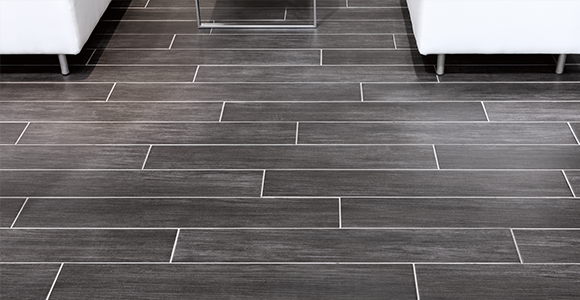
Higher-performing tile adhesives and low-emission interior paints
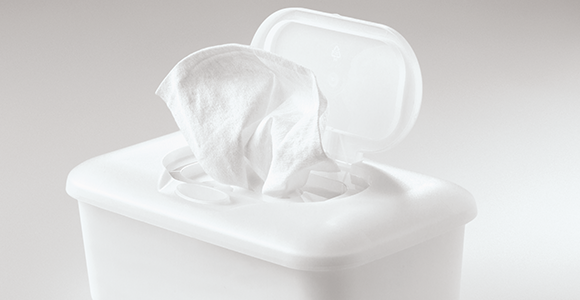
Good tensile strength, soft hand and controlled absorbency
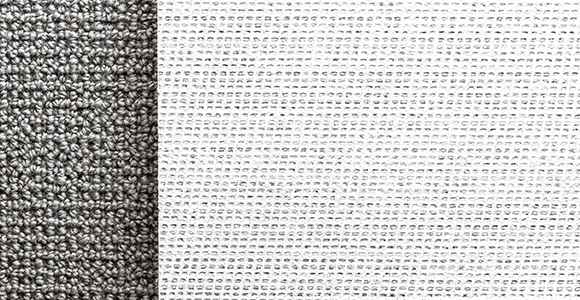
Good penetration and fiber adhesion
“People are optimistic about the future and are spending more money again.”
Mary Beth Hudson
Those customers use VINNAPAS® binder to make low-odor, highly compatible interior paints, water-based adhesives, tear-resistant nonwovens for wet wipes and paper towels, and robust exterior coatings. Carpet manufacturers, too, use the dispersion to bond fibers to the carpet backing. In the USA, business with paint manufacturers in particular has grown strongly in recent months – a reason for continuing optimism.
Low gasoline prices are currently fueling this trend in the USA. “People are optimistic about the future and are spending more money again,” says Hudson, adding that paint manufacturers such as industry leader Sherwin-Williams are expecting double-digit growth rates.
Hudson’s colleague John Tacca, who works at WACKER POLYMERS’ US headquarters in Allentown, Pennsylvania, has an even better overview of the market. He is responsible for the company’s polymer business in America. Tacca explains that, in 2015, sales of existing homes in the USA rose dramatically. “And if you buy an old home, the first thing you do is renovate and paint the walls,” he says with a smile.
“Our ambition is to have the industry leaders in our customer base.”
John Tacca
Tacca adds that the situation with new properties is positive as well. Statisticians in the USA estimate that more than a million private building projects were launched in 2015. Market researchers at The Freedonia Group expect to see strong growth in paints with low concentrations of volatile organic compounds. “Paints like these are increasingly becoming the standard in the USA – and VAE binders, in particular, can score points in this area,” he says.
For Tacca and his team, partnerships with suc-cessful, highly innovative customers are a key growth driver. His ambition is to have the industry leaders in his customer base. He talks, for in-stance, about one of America’s biggest paint manufacturers, who recently began offering a new paint collection, based on VINNAPAS®. “These paints are apparently selling like hotcakes,” says an enthusiastic Tacca, “and we are noticing it in our order books.” For every bucket of paint contains its fair share of VINNAPAS®.
In Central and South America as well, sales of polymers are on the rise, adds Tacca. In countries like Mexico, Brazil and Colombia, many manu-facturers of paints, plasters or tile adhesives are still not using polymeric binders, he says. But there is great interest in high-value products among the aspiring middle classes and manufacturers themselves. Only recently, says Tacca, he and his colleagues were able to convince some 100 potential customers in Mexico City of the effec-tiveness of VINNAPAS®. They were invited to kick a soccer ball at two walls with different plaster coatings – one with polymeric binders and one without. “Afterwards, the wall without VINNAPAS® had some sizable dents in it,” Tacca is pleased to note.
“After all, the market for binders is fourteen times larger than the VAE market.”
John Fotheringham
John Fotheringham and his team of dispersion strategists at WACKER headquarters in Munich want to use VAE binders to tap industries in which other binders – such as acrylate, acrylostyrene and styrene-butadiene – still reign supreme. “After all, the market for binders is fourteen times larger than the VAE market,” he explains. Fotheringham, who hails from Great Britain, is head of WACKER’s global dispersions business.
The engineers at WACKER’s lab in the USA are working, for instance, on new binders for use in paper manufacturing, on additives for asphalt and on sealants for the construction industry. “We don’t want to compete simply on price. We want to tailor our products to add real value for our customers,” says Tacca. He has been in the business for years and knows that customers are cautious. They need to have very good reasons before adapting their production to a new technology.
Biggest Plant for VAE Dispersions in the USA
Mary Beth Hudson has recently shown many new or potential clients around the Calvert City plant. The tours are hard work, says the head of 140 employees, before quickly adding: “But they’re worth it. When I show people around the plant here, they’re really impressed. Calvert City happens to be the biggest plant of its kind on the continent.”
But, sometimes, the innovations of her lab col-leagues make her a little bit nervous. When an entire industry suddenly switches from one binder to another, it can be really tough for the people in production. But then Hudson laughs at her own misgivings. Of all the employees at the Calvert City plant, she has been with WACKER the longest and has successfully tackled many challenges. “I’m an engineer,” she says. “I love solving problems.”