Auf Effizienz getrimmt
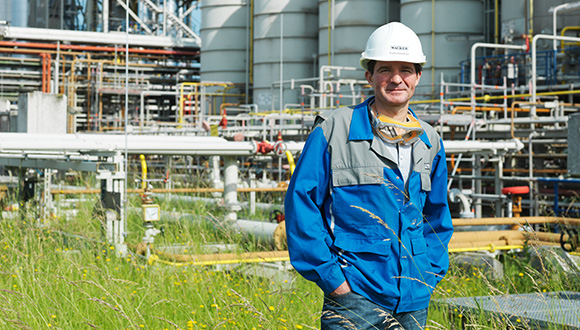
Christian Kaltenmarkner hat den Energieverbrauch seines Betriebs deutlich gesenkt. Und er hat noch viel vor.
Mit einem umfassenden Energiemanagement hat WACKER den spezifischen Energieverbrauch in Deutschland in den letzten fünf Jahren um 22 Prozent gesenkt. Für die kommenden Jahre hat der Konzern konkrete Energieziele festgelegt.
Christian Kaltenmarkner ist ein vorsichtiger Mensch. Darum hatte ihm die Sache auch lange Bauchschmerzen bereitet. Der Chemieingenieur wusste, dass in seiner Silan-Destillationsanlage einiges verbessert werden müsste. Die steigenden Energiekosten machten dem Betriebsleiter zu schaffen. Ein Umbau würde helfen, doch Kaltenmarkner zögerte. Technische Risiken waren durch zahlreiche Versuche nahezu ausgeschlossen worden. Denn unter keinen Umständen durfte das Chlorsilan mit Luftfeuchtigkeit in Berührung kommen, weil dabei ätzender Chlorwasserstoff entsteht. Aber ließen sich die zahlreichen Umbauten an den Kolonnen im vorgegebenen kurzen Zeitfenster von zwei Wochen realisieren? „Mir war klar: Das muss hundertprozentig funktionieren“, erinnert sich Kaltenmarkner. Sonst wäre auch die Rohstoffversorgung der gesamten Siliconproduktion in Burghausen in Gefahr gewesen.
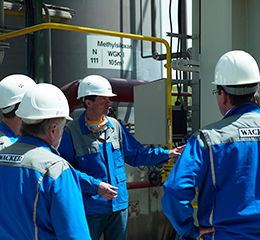
Um Energie zu sparen, arbeiten Betriebsleiter und Energiemanager eng zusammen.
Heute ist er heilfroh, dass er trotz aller Bedenken den Umbau gewagt hat. Durch einen Wärmeverbund kann er bisher ungenutzte Wärme aus der einen Anlage als Energiequelle in anderen Anlagen einsetzen. „Im Ergebnis hat es sogar viel mehr gebracht, als wir gehofft hatten“, sagt der 41-Jährige und schaut von seinem Büro zu den Destillationskolonnen, 60 Meter hohen Stahlzylindern, die wie glänzende Spargelstangen aus dem Boden wachsen.
In den 14 Kolonnen entstehen die Rohstoffe für die Siliconherstellung in reiner Form. Die Destillation holt aus einer flüssigen Silanmischung die einzelnen Komponenten heraus. Doch sie braucht viel Energie, und das treibt die Betriebskosten in die Höhe.
Durch den Umbau spart Betriebsleiter Kaltenmarkner nun jährlich über zwei Mio. Euro an Energiekosten.
Für WACKER sind solche Energiesparprojekte immens wichtig. Das Stammwerk Burghausen benötigt jeden Tag so viel Energie wie eine Stadt von der Größe Freiburgs. Der Anteil der Energie- an den Herstellungskosten wird mit steigenden Preisen für Öl und Gas immer größer und beträgt heute schon rund 12 Prozent.
Konkrete Energieziele
Energieeffizienz ist daher nicht nur wichtig für den Klimaschutz, sondern auch für eine wettbewerbsfähige Position auf dem Weltmarkt. „Natürlich wollen wir Energie und Rohstoffe sparen“, sagt Dr. Jutta Matreux, die im Konzern für Nachhaltigkeit verantwortlich ist. „Kaufmännisches Denken ist ein wichtiger Teil nachhaltigen Handelns.“
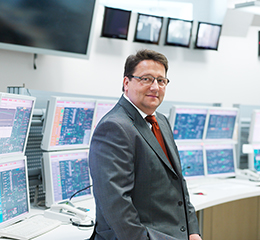
Jochen Lediger kümmert sich um die Umsetzung der Energieziele.
Deswegen hat WACKER in den letzten fünf Jahren den spezifischen Energieverbrauch in Deutschland um 22 Prozent gesenkt. Für die kommenden Jahre hat sich WACKER konkrete Energieziele gesetzt: In Deutschland sollen bis zum Jahr 2022 jährlich 1,5 Prozent spezifische Energie eingespart werden. Insgesamt soll der Energieeinsatz je Produktionsmenge um ein Drittel sinken. „Das ist sehr ehrgeizig“, sagt Jochen Lediger. „Aber wir wissen genau, wo wir ansetzen müssen.“
Jochen Lediger ist einer der Menschen bei WACKER, die sich um die Umsetzung dieser Energieziele kümmern. Der überbetriebliche Wärmeverbund am Standort Burghausen deckt bereits heute 44 Prozent des gesamten Wärmebedarfs. Der Energiemanager hat das gesamte System aus Energieverbrauchern und Energieströmen im Blick. Er sorgt auch dafür, dass am Standort Burghausen so energiesparend wie möglich produziert wird. In den letzten sieben Jahren hat er mit seinen Kollegen alle energieintensiven Anlagen unter die Lupe genommen. „Wir sind durch die Betriebe gezogen und haben mit den Leuten vor Ort Verbesserungen erarbeitet“, erzählt Lediger. 150 Energiesparprojekte konnten sie bisher umsetzen, die meisten haben sich bereits amortisiert.
Eines davon war der Umbau der Destillationskolonnen von Christian Kaltenmarkner. Neben dem Wärmeverbund sollte auch ein neues Innenleben die Anlage effizienter machen. 50 Mann waren rund um die Uhr im Einsatz, um kilometerweise alte Tragringe aus den Kolonnen herauszuschneiden. Der Zeitplan war so knapp kalkuliert, dass der TÜV nachts um vier Uhr die Schweißnähte abnahm. Und doch lief die Produktion nach zwei Wochen Umbauzeit wie geplant wieder an.
Um den Erfolg solcher Aktionen messen zu können, haben Jochen Lediger und seine Kollegen in den letzten Jahren viel Mühe darauf verwendet, Energiedaten zu sammeln. Sie haben neue Messungen eingerichtet, andere haben sie automatisiert. Wo früher einmal im Monat der Verbrauch abgelesen wurde, sind jetzt stündliche Messungen möglich. So kann Lediger genau nachverfolgen, wann, wo und wie viel Energie verbraucht wird.
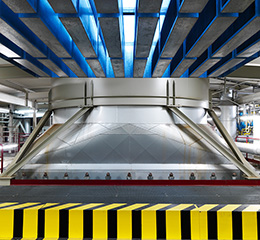
Abhitzekessel über der Turbine im Gas- und Dampfkraftwerk am Standort Burghausen.
2012 hat WACKER sein Energiemanagement an den deutschen Standorten erstmals nach ISO 50001 zertifizieren lassen. Die Audits haben Lediger und seinem Team gute Arbeit bescheinigt. Die Zertifizierung soll helfen, die effiziente Nutzung von Energie weiter voranzutreiben.
Eine neue Software unterstützt die Energiedatenerfassung, Abrechnung, Planung und Prognose. Mit ihr kann Jochen Lediger am PC ermitteln, wie viel Energie die Produktion am kommenden Tag braucht und wie viel Strom und Wärme WACKER produzieren wird. Das hängt zum Beispiel davon ab, ob im Kraftwerk alle Turbinen in Betrieb sind. Auch das Wetter spielt eine Rolle. So treibt an einem Regentag mehr Wasser als normal die Turbinen im Wasserkraftwerk an. Die genauen Prognosen machen die Kalkulation für den Energieeinkauf leichter. Zur Not kann auch nachts oder am Wochenende noch Strom für ein oder zwei Stunden zugekauft werden.
45 Prozent des Stroms für die deutschen Standorte produziert WACKER sowieso selbst. Der größte Teil entsteht in einem Gas- und Dampfkraftwerk, mitten auf dem Werkgelände in Burghausen. Eine unscheinbare Halle, die von außen nur durch ihre Größe beeindruckt. Drinnen wandeln riesige Turbinen und Dampfkessel Erdgas in Dampf und Strom um. Kraftwerkchef Stefan Seidel steht gerne in 52 Metern Höhe auf dem Dach des Kraftwerks und blickt herab auf das Werkareal, das von hier oben mit seinen unzähligen Produktionsanlagen, Leitungsnetzen und Büros an die Hauptplatine eines PCs erinnert. „Das ist schon beeindruckend“, sagt er, „für all die Produktionsbetriebe liefern wir die Energie.“
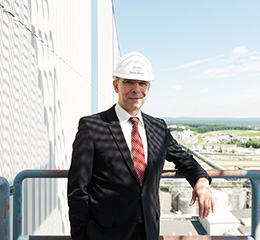
Kraftwerkchef Stefan Seidel liefert Energie für den größten WACKER-Standort.
Wasserkraft seit 1922
Stefan Seidel weiß, dass die Energieerzeugung unmittelbaren Einfluss auf die Herstellkosten und damit den Erfolg des Unternehmens hat. Dafür braucht man hochmoderne Anlagen. Das Kraftwerk arbeitet mit dem Prinzip der Kraft-Wärme-Kopplung. Es erzeugt gleichzeitig Strom und Prozessdampf für die Produktion. Der Grad der Brennstoffnutzung ist mit mehr als 80 Prozent doppelt so hoch wie bei herkömmlichen Kraftwerken.
Zusätzlich versorgt umweltfreundliche Wasserkraft das Werk mit Strom. Vom Dach des Kraftwerks zeigt Stefan Seidel auf den Alzkanal, der das Werkgelände als grün-braunes Band durchkreuzt. Er endet direkt oberhalb der Salzach am Wasserschloss der Alzwerke. Die WACKER-Tochter beliefert seit den Tagen von Unternehmensgründer Dr. Alexander Wacker die Produktion mit Strom. Als das Kraftwerk 1922 seinen Betrieb aufnahm, war es das größte Industrie-Wasserkraftwerk in Deutschland. Auch heute noch könnte es 90.000 Haushalte mit Strom versorgen, erzählt Stefan Seidel, und das ohne jeglichen Ausstoß von Kohlendioxid.
Darauf ausruhen kann Seidel sich nicht. Es ist Teil seiner Aufgabe, die Energieversorgung in Burghausen ständig zu optimieren. Eine Verbundproduktion wie bei WACKER lädt geradewegs dazu ein. Viele Innovationen kämen von den Mitarbeitern, erzählt Seidel. Zwei Ingenieure hatten zum Beispiel gerade vorgeschlagen, Prozesswasser, das entsalzt und dafür vorgewärmt werden muss, erst einmal als Kühlwasser über die Kraftwerkturbine laufen zu lassen. Eine kleine Änderung, die kaum etwas kostet, aber umso mehr bringt: Stefan Seidel rechnet mit einer jährlichen Einsparung von mehreren hunderttausend Euro.
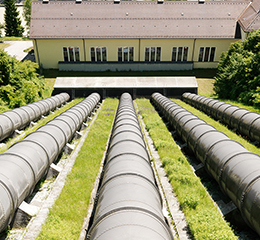
Alzwerke: umweltfreundliche Wasserkraft seit über 90 Jahren.
Auch Christian Kaltenmarkner ist mit seiner Silan-Destillation mittlerweile zum Effizienz-Experten geworden. Von seinem Büro im dritten Stock hat er seine Anlage gut im Blick. Er zeigt auf eine neue Kondensatleitung: „Die spart bis zu 200.000 Euro im Jahr.“ Neue, genauere Detektoren, die erlaubte Verunreinigungen im Siloxan messen, brächten bis zu 100.000 Euro im Jahr.
Noch nie waren seine Energiekennzahlen so gut, erzählt Kaltenmarkner stolz. Trotzdem haben er und auch Stefan Seidel für die Zukunft noch jede Menge Ideen im Kopf, wie sie ihre Anlagen effizienter machen könnten. „Das ist ja das Spannende an meinem Job, dass ich wie ein kleiner Unternehmer meine eigenen Energiesparhebel betätigen kann“, sagt Christian Kaltenmarkner. Auf Leute wie ihn können sich die Energiemanager verlassen.
Dem Energieverlust auf der Spur
Das neueste Werkzeug der Energiemanager ist die Energiekaskade. Mit Hilfe von Computermodellen stellen die Experten für die großen, energiefressenden Anlagen ein theoretisches Optimum und den aktuellen Energieeinsatz gegenüber. Das Modell zeigt, wo Energieverluste herkommen. Mit Hilfe dieser Simulationen können die Produktionsleiter noch genauer erkennen, wo die Einsparpotenziale bei Strom und Wärme stecken und wann sich die Optimierung lohnt. 2012 haben drei Betriebe in Burghausen die Energiekaskade umgesetzt, 2013 ist der Pulvertrockner im chinesischen Nanjing an der Reihe.