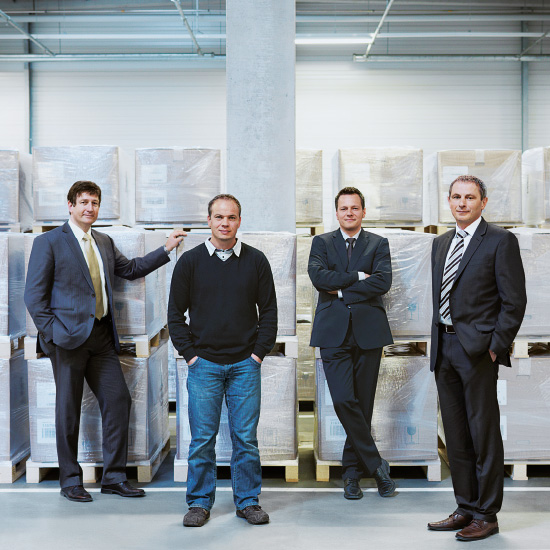
Haben den schnellen und umweltfreundlichen Warentransport im Blick: Stefan Dartsch, Stefan Hrubesch, Josef Oberlechner und Ludwig Hinterecker (v.l.n.r.)
Moderne Lokomotiven, kurze Wege für die Lieferanten, umweltfreundliche Verpackungen – Nachhaltigkeit gehört bei WACKER zur Logistik wie das Gleis zum Zug. Ein Besuch im Herzen des Logistikzentrums in Burghausen.
Acht Computerbildschirme flimmern im Containerleitstand. Einen davon hat Stefan Hrubesch immer im Blick, der hier als Leiter der Verladesteuerung arbeitet. „Das Rote hier“, sagt er und deutet auf einen der Bildschirme, „das sind Tragwagen für Container – und die kleinen rechteckigen Blöcke darauf sind in Wahrheit die Container.“ Hrubesch klickt sie an und kann sagen, was darin ist – Silicium zum Beispiel oder pyrogene Kieselsäure oder ein anderes WACKER-Produkt. Seine Mitarbeiter ziehen mit der Maus Container um Container auf die Tragwagen, so lange, bis der Zug voll beladen ist. Das Ganze nennt sich TESS und ist das Transport-Einsatz-Steuerungs-System – ein zentraler Bestandteil der Logistik bei WACKER in Burghausen.
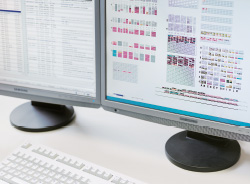
Zuerst werden die Züge am Computerbildschirm
virtuell beladen, danach in der Realität.
Was beinahe spielerisch aussieht, erfordert neben Intuition vor allem viel logisches Denkvermögen. Hrubesch und seine vier Mitarbeiter steuern an ihren Computern die Transporte der Container im Werk sowie die Beladung eines Zuges. Er darf nicht länger als 560 Meter sein und nicht schwerer als 1.399 Tonnen, weil er sonst nicht über den Piracher Berg kommt. Trotzdem müssen alle Container mit auf den Zug. Denn sie müssen spätestens zwei Tage vor Ladeschluss in den Nordseehäfen Hamburg oder Bremerhaven eintreffen. „Die Verladesteuerung hier ist das Herz des Zuges“, sagt Stefan Hrubesch und lässt seinen Blick durch den Leitstand schweifen. „Hier laufen alle Infos zusammen, die mit den Containern und dem Shuttle-Zug zu tun haben.“ Seit zehn Jahren verlässt dieser Zug jeden Tag das Werk und trägt dazu bei, die Schadstoffemissionen gering zu halten.
Hinter der Anschlussgrenze
Nur wenige Meter vom Leitstand entfernt fährt auf Gleis 14 um Punkt 9.21 Uhr eine weiße Lokomotive in den WACKER-Bahnhof ein. Sie zieht eine lange Reihe von Tragwagen hinter sich her, die alle mit Containern beladen sind. Langsam bremst der Zug und bleibt stehen. Die Lok wird abgekuppelt und fährt auf ein Nebengleis. Währenddessen zeigt Stefan Dartsch, der Leiter des Innerwerktransports, auf ein Schild gleich hinter dem Bahnhof. „Anschlussgrenze“ steht darauf und das bedeutet: An diesem Punkt endet das Hoheitsgebiet der Deutschen Bahn. Zwar laufen von hier aus 27 Kilometer Gleise durchs Werk, die zu 19 Ladestellen führen – aber verantwortlich für diese wohl größte Werkbahn in Bayern ist Stefan Dartsch. Der Ingenieur hat dafür eigens die Prüfung zum Eisenbahn-Betriebsleiter gemacht.
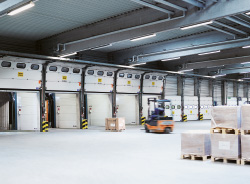
Die Mitarbeiter im Umschlag- und Logistikzentrum
befüllen mit Gabelstaplern tagsüber die
LKW-Container, nachts die Zug-Container.
Eine gelbe Lokomotive der WACKER-Werkbahn schnauft heran und schleppt die ersten Tragwagen des Shuttle-Zuges zum Portalkran, wo sie „abgekrant“ werden. Jeder Container kommt auf einen Wechselrahmen und wird anschließend von einem LKW zu seinem Bestimmungsort im Werk gebracht. Die Siliciumcontainer sind heute zuerst dran, abgeladen wird nach Wichtigkeit.
Maßarbeit in großer Höhe
Der Portalkran lädt sofort neue volle Container auf die Tragwagen. Dafür braucht der Kranführer ein richtig gutes Auge – er sitzt in rund zehn Metern Höhe in seiner Kanzel und muss von dort aus zentimetergenaue Maßarbeit leisten. Die Container, die er durch die Luft schwenkt, werden am nächsten Tag auf die Reise nach Norden gehen. In Maschen, 24 Kilometer vor Hamburg, wird der Zug dann geteilt – ein Teil der Container ist für Schiffe in Bremerhaven bestimmt, der andere für Schiffe in Hamburg.
Im Jahr 2010 haben Produkte mit einem Gesamtgewicht von 715.000 Tonnen das Werk in Burghausen verlassen – das entspricht rund 71 Eiffeltürmen. 230.000 Tonnen davon wurden mit der Bahn transportiert und davon wiederum 154.000 Tonnen mit dem Shuttle-Zug, der ausschließlich WACKER-Produkte transportiert. Weitere 76.000 Tonnen wurden mit Güterzügen im Regelverkehr transportiert.
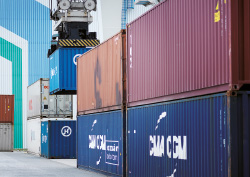
Beim Anheben und Aufsetzen der Container leistet
der Kranführer zentimetergenaue Maßarbeit.
Vorfahrt für die Bahn
„Nachhaltigkeit hat in unseren Logistikkonzepten eine hohe Bedeutung“, sagt Ludwig Hinterecker, Leiter Einkauf Logistikleistungen. Das fängt damit an, möglichst viele Güter mit der Bahn zu transportieren. „Dabei setzen wir uns für moderne Loks ein“, sagt Hinterecker und verweist auf 18 neue Lokomotiven, die seit Ende 2010 von der Bahn für den Transport in der Region eingesetzt werden. Der Containerzug von WACKER wird ab Landshut von einer umweltfreundlichen E-Lok gezogen. In der Umgebung von Burghausen fährt allerdings eine Diesellok, denn dieser Bereich ist noch nicht elektrifiziert und zudem eingleisig. WACKER setzt sich seit Jahren für einen Ausbau der Strecke von München über Mühldorf nach Burghausen ein und konnte sich 2010 über einen Anfangserfolg freuen: Im Dezember wurde bei Mühldorf ein 7,8 Kilometer langes, zweigleisiges Teilstück eröffnet. Im April 2011 wurde ein weiteres Teilstück zwischen Tüßling und Burghausen mit elektronischer Signaltechnik ausgerüstet und damit die veraltete Relaistechnik ersetzt.
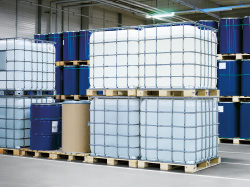
Die IBC ersetzen mehr und mehr herkömmliche
Fässer. Das spart Verpackungsmaterial,
Lagerfläche und Transportraum.
Leerfahrten vermeiden
Ludwig Hinterecker wechselt das Thema von der Bahn auf den LKW und erläutert das Gebietsspediteurkonzept: „Jeder Spediteur bedient eine bestimmte Region, die in Deutschland nach Postleitzahlen geordnet ist, in Europa nach Ländern.“ Das vermeidet Leerfahrten und spart daher Kilometer und Treibstoff, setzt aber voraus, dass verschiedene Produkte an einer Stelle geladen werden können. Eine solche Stelle ist das Umschlag- und Logistikzentrum, kurz: ULZ. 60 Mitarbeiter lagern, etikettieren und verladen hier rund 30.000 Paletten pro Monat – an sieben Tagen pro Woche. Von sechs bis 22 Uhr schieben die Gabelstapler eine Palette nach der anderen in LKW-Container, nachts sind dann die Zug-Container an der Reihe. Um die Gefahr eines Brandes so klein wie möglich zu halten, wird im vollständig automatisierten Hochregallager der Sauerstoff in der Luft auf 13 Prozent gesenkt, rund sieben Prozent weniger als normal. Das entspricht dem Sauerstoffgehalt bei einer Bergtour in 3.500 bis 4.000 Metern Höhe. Dieser Bereich des ULZ darf nur mit strengen Sicherheitsauflagen für Kontrollzwecke betreten werden.
Was im gesamten Logistikbereich besonders auffällt, ist die Effizienz: Bis hin zum Weichensteller auf den Gleisen weiß jeder genau, was er wann zu tun hat. Die Fahrer der Gabelstapler werfen nur einen kurzen Blick aufs Navigationsgerät und steuern sofort die richtige Gasse mit Paletten an – nach ein bis zwei Stunden ist der Container voll. Natürlich helfen bei den meisten Arbeiten Computersysteme, beim Etikettieren und Verladen ebenso wie beim Transport. Aber: „Wir können unsere Produkte nur deshalb so schnell und umweltfreundlich verladen, weil wir neben guten Computern auch hervorragende Mitarbeiter haben“, sagt Josef Oberlechner, Leiter Verkehrssteuerung und Lagerlogistik. Neben zwei zentralen Lagern im Werk gibt es drei Kilometer außerhalb noch ein Außenlager. Insgesamt bieten sie Platz für 55.000 Paletten, von denen keine länger als unbedingt nötig im Lager liegt. Das hat wirtschaftliche Vorteile und schont die Umwelt.

Jeden Tag um 12.21 Uhr macht sich ein WACKER-
Güterzug auf die Reise zu den Seehäfen.
Nähe zu den Lieferanten
Denselben Effekt hat die Ansiedelung wichtiger Lieferanten in der Nähe von Burghausen: So eröffnete ein Lieferant für Kunststofffässer und andere Verpackungsmaterialien eine Produktionsstätte im nahe gelegenen Simbach. Bei den Packmitteln achtet WACKER sehr darauf, solche zu ordern, die umweltschonend hergestellt und wiederverwendet werden. Zum Beispiel werden 1.000-Liter-Container, sogenannte IBC (Intermediate Bulk Container), eingesetzt, die im Vergleich zu herkömmlichen Fässern viel Platz sparen – was weniger Verpackungsmaterial und weniger Stellfläche zur Folge hat. Bei Stahlfässern wurde die Wanddicke um einen Zehntel Millimeter reduziert. Dadurch können 149 Tonnen Stahl pro Jahr eingespart werden. Und der Kaugummigrundstoff, den WACKER herstellt, wird seit einiger Zeit ausschließlich in recyclefähigen Papiersäcken transportiert.
Zurück zum Bahnhof. Gegen 11 Uhr wechselt die weiße Lokomotive das Gleis und kuppelt an den Ausgangszug an. Von jetzt an ist wieder das Tochterunternehmen der Bahn zuständig. Theoretisch könnte der Zug sofort losfahren. Aber er muss sich an den Fahrplan halten und deshalb setzt er sich mit den vielen Wagen erst um 12.21 Uhr in Bewegung.
Auf leisen Sohlen
Normalerweise machen Güterzüge beim Bremsen sehr laute, schrille Geräusche – nicht aber der Containerzug. Stefan Dartsch ist darauf sichtlich stolz, er lächelt und sagt: „Dieser Zug kommt auf ganz leisen Sohlen daher.“
Er meint das wörtlich. Immer mehr WACKER-Waggons, darunter auch 30 neue, von der Bahn gemietete Kesselwagen, verfügen über eine sogenannte K-Sohle – eine Kompositbremse, die bei jedem Tempo deutlich leiser bremst. WACKER hat sich bei der Bahn für diese Sohlen starkgemacht. Denn auch sie sind ein kleiner Mosaikstein beim großen Thema Nachhaltigkeit in der Logistik.