Die chemische Industrie ist eine der energieintensivsten Branchen. Allein in Deutschland nutzt sie rund 20 Prozent des Stroms, der von Industriebetrieben verbraucht wird. Für uns ist es wichtig, kontinuierlich die Energieeffizienz unserer Prozesse zu verbessern. Damit leisten wir einen Beitrag zum Klimaschutz und bleiben zugleich auf dem Weltmarkt wettbewerbsfähig.
WACKER hat im Jahr 2010 durch den Ausbau der Polysiliciumproduktion am Standort Burghausen und den Zukauf der Siliciummetallproduktion in Holla, Norwegen, seinen Stromverbrauch auf 3,8 Mio. MWh erhöht (2009: 2,7 Mio. MWh). Auch im Jahr 2009 stieg der Stromverbrauch vor allem durch den Ausbau der Polysiliciumproduktion (2008: 2,4 Mio. MWh).
Vom konzernweiten Strombedarf entfallen 79 Prozent auf die deutschen Produktionsstandorte. WACKER hat im Jahr 2010 in Deutschland 50 Prozent seines benötigten Stroms zugekauft. Entsprechend den Primärenergiequellen der Versorgungsunternehmen wurde etwa die Hälfte dieses Stroms aus fossilen Energieträgern erzeugt (55 Prozent). 31 Prozent stammen aus Kernenergie, 14 Prozent aus erneuerbaren Energiequellen. Wir prüfen weiter den Einsatz erneuerbarer Energien und nehmen passende Angebote dauerhaft in unseren Energiemix auf. Unser neuer Produktionsstandort in Holla bezieht seinen Strom, wie in Norwegen üblich, überwiegend aus Wasserkraft.
An unseren großen Standorten Burghausen und Nünchritz erzeugen wir Dampf und Strom in gekoppelter Produktion. Diese Kraft-Wärme-Kopplungsanlagen haben mit über 80 Prozent einen doppelt so hohen Brennstoffnutzungsgrad wie konventionelle Energieerzeugungsanlagen, die Öl, Gas oder Kohle umsetzen. Am Standort Burghausen nutzen wir auch Wasserkraft, um Strom zu erzeugen. Unser Wasserkraftwerk erzeugt jährlich 270 Gigawattstunden. Durch diese umweltfreundliche Energiequelle vermeiden wir jährlich den Ausstoß von 160.000 Tonnen Kohlendioxid. Die beiden Kraft-Wärme-Kopplungsanlagen und das Wasserkraftwerk erzeugten in den Jahren 2009 und 2010 jeweils 1,5 Mio. MWh Strom. Damit produzierte WACKER knapp 40 Prozent (2009: 55 Prozent) seines Strombedarfs selbst.
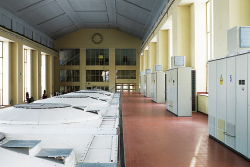
Die Alzwerke versorgen den Standort Burghausen seit 1922 mit elektrischer Energie aus Wasserkraft.
Bei vielen chemischen Reaktionen wird Wärme frei, die wir für weitere Produktionsprozesse nutzen. An den Standorten Burghausen und Nünchritz praktizieren wir seit Jahren Wärmeverbünde und verbessern diese stetig. So reduzieren wir den Einsatz von Primärenergie (in der Regel Erdgas) in unseren Kraftwerken.
Unser Werk Nünchritz brauchte im Jahr 2010, um eine Tonne Produkt zu produzieren, rund 70 Prozent weniger Strom und 85 Prozent weniger Prozessdampf aus dem Heizkraftwerk als 1999 – damals hatte WACKER den Standort übernommen. Das Nünchritzer Kraftwerk haben wir von schwerem Heizöl auf klimafreundlicheres Erdgas umgestellt.
Unsere großen Produktionsstandorte Burghausen und Nünchritz verbrauchen zusammen rund 75 Prozent der konzernweit benötigten Energie. Konzernweit stieg der Wärmeverbrauch wegen des Zukaufs des norwegischen Standorts Holla auf 3,4 TWh (2009: 2,8 TWh). Im Wärmeverbrauch ist erstmals der Einsatz fester fossiler Energieträger (Kohle, Holzkohle, Holz) in der neu erworbenen Siliciummetallproduktion berücksichtigt.
WACKER und Siltronic führten im Jahr 2009 an ihren deutschen Standorten Burghausen, Nünchritz und Freiberg ein Energiemanagementsystem ein. Mit diesem System ermitteln wir Energieströme, -verbraucher und -sparmöglichkeiten. An den WACKER-Standorten Burghausen und Nünchritz sowie den Siltronic-Standorten Burghausen und Freiberg lassen wir die Energiemanagementsysteme seit 2009 nach ISO 14001 zertifizieren.
Ein Großteil unserer Maßnahmen, mit denen wir die Energieeffizienz unserer Produktionsanlagen verbessern, geht auf das Projekt POWER PLUS zurück. Dieses Projekt wurde im Jahr 2007 gestartet, um die Energieeffizienz an den Standorten Burghausen und Nünchritz zu erhöhen. Seit 2009 ist auch unser Werk Köln dabei. Der Erfolg von POWER PLUS beruht auf zwei Faktoren: Unsere Energieexperten haben die Produktionsanlagen unter die Lupe genommen, und unsere Mitarbeiter haben Verbesserungsvorschläge entwickelt. In Summe konnten so mehr als 150 Maßnahmen eingeleitet werden, um die Energieeffizienz zu verbessern. Bis Ende 2010 haben wir rund 70 Prozent dieser Maßnahmen umgesetzt.
Zwei Beispiele dazu: Unser Geschäftsbereich WACKER SILICONES hat am Standort Burghausen die Destillation der Siloxanproduktion verbessert und einen Wärmeverbund aufgebaut. Dadurch sparen wir jährlich über 100.000 Tonnen Heizdampf. Das Werk Nünchritz hat 2009 im Vergleich zu 2006 pro Tonne Siloxan mehr als 30 Prozent Heizdampf eingespart.
An unseren Standorten, die sich an POWER PLUS beteiligen, haben wir in vielen Bereichen den Energieverbrauch reduziert. Insgesamt hat sich der spezifische (auf die Produktionsmenge bezogene) Energieverbrauch differenziert entwickelt, da unsere Produktionsanlagen unterschiedlich ausgelastet waren und wir die energieintensive Polysiliciumproduktion ausgebaut haben. Negativ wirkte sich zum Beispiel die schwächere Auslastung vieler Anlagen während der Wirtschaftskrise des Jahres 2009 aus.
Auch an unseren internationalen Standorten arbeiten wir daran, unsere Energieeffizienz zu steigern. Ein Beispiel ist die im Jahr 2009 erweiterte Anlage für Cyclodextrine am Standort Eddyville/Iowa, USA. Diese biotechnologisch hergestellten Zuckermoleküle werden als Stabilisatoren und Trägermaterial in der Life-Science- und Kosmetikindustrie sowie im Lebensmittel- und Agrobereich eingesetzt. Ein wesentlicher Teil der 21-Mio.-US-$-Investition floss in eine neue Nebenprodukt-Aufarbeitungsanlage. Sie verringert den Dampfbedarf der gesamten Anlage um 35 Prozent.
Unser Siltronic-Standort Freiberg hat die Vorlauftemperatur für Kristallziehanlagen so angepasst, dass wir auf den Einsatz von Kältemaschinen zum großen Teil verzichten können. Dadurch haben wir im Jahr 2010 am Standort Freiberg 764 MWh eingespart.
Wir nutzen energiesparende Elektromotoren für Fahrzeuge und Geräte. Wir sparen zudem Strom, indem wir den direktversorgten auf geregelten Elektroantrieb umstellen, zum Beispiel bei Pumpen in Produktionsanlagen, deren Drehzahl bei geringerer Transportlast automatisch gedrosselt wird.
Tabelle herunterladen |
Energie |
|
|
| |||
TWh |
2010 |
2009 |
2008 | |||
|
|
|
| |||
Stromverbrauch |
3,8 |
2,7 |
2,4 | |||
Wärmeverbrauch1 |
3,4 |
2,8 |
2,8 | |||
|
|
|
| |||
Primärenergieeinsatz |
|
|
| |||
Erdgas |
5,5 |
5,4 |
5,4 | |||
Feste Energieträger2 (Kohle, Holzkohle, Holz) |
0,4 |
– |
– | |||
Wärme Fremdbezug3 |
0,2 |
0,2 |
0,2 | |||
Heizöl |
0,01 |
0,01 |
0,01 |
1 |
Im Wärmeverbrauch ist 2010 erstmals der Einsatz fester fossiler Energieträger (Kohle, Holzkohle, Holz) in der neu erworbenen Siliciummetallproduktion in Holla, Norwegen, berücksichtigt. |
2 |
Eingesetzt in der Siliciummetallproduktion in Holla, Norwegen |
3 |
Dampf, Fernwärme |

1 Burghausen/Nünchritz
2 Burghausen
3 Steinkohle, Braunkohle, Öl, Gas
4 Wasserkraft, Wind, Solar
5 Im Ausland beziehen wir den Strom fremd auf Basis des örtlichen Standard-Energiemix.